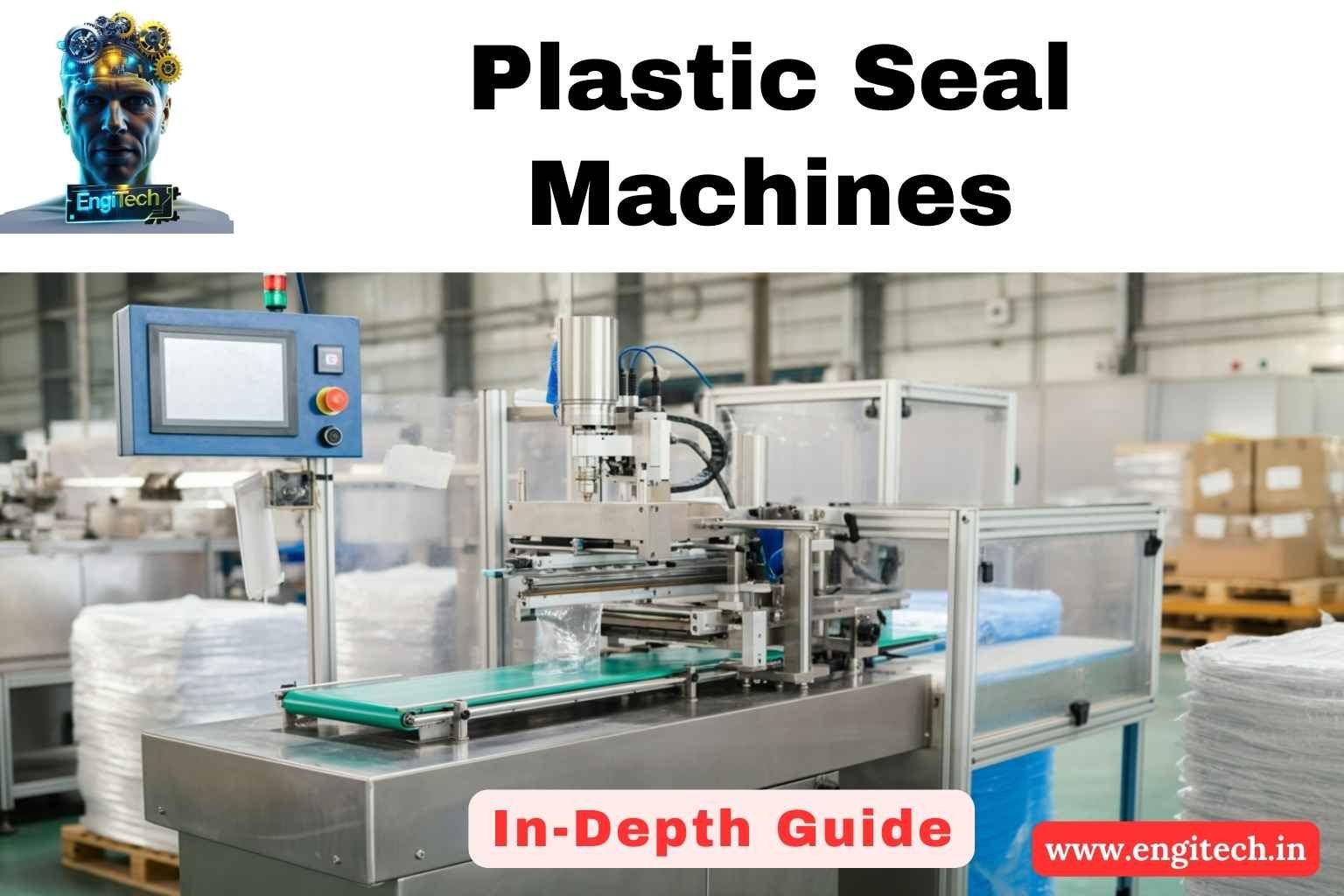
In the fast-paced world of manufacturing and distribution, efficient packaging is a critical component of success. Whether you’re an e-commerce entrepreneur, a food manufacturer, or part of a global logistics chain, choosing the right plastic seal machine can make or break your production line’s profitability.
In this comprehensive guide, you’ll discover the benefits, varieties, maintenance tips, and expert strategies for optimising your plastic seal machine operations. By the end, you’ll be well-equipped to make informed decisions that save you time, reduce product damage, and boost overall business profitability.
Table of Contents
Introduction: The Growing Importance of Plastic Seal Machines
In today’s global marketplace, packaging isn’t merely an afterthought; it’s a pivotal aspect of brand identity, product protection, and consumer satisfaction. According to research by the World Packaging Organisation, the packaging industry is growing at an unprecedented rate, with plastic packaging solutions taking center stage due to their versatility and cost-effectiveness. At the heart of this booming segment lies a key piece of equipment: the plastic seal machine.
Why Packaging Matters More Than Ever
- Brand Perception: Consumers often judge a product’s quality by its packaging. If the seal is improperly done or the plastic is compromised, it casts doubt on the brand’s reliability.
- Product Protection: A secure seal safeguards against contamination, spoilage, or tampering—especially vital for food, pharmaceutical, and cosmetic products.
- Legal and Regulatory Requirements: Certain industries, like medical and food service, must adhere to strict packaging standards. Improper sealing could lead to regulatory fines or product recalls.
User Intent and the Drive for Efficiency
Whether you operate in a small workshop or a sprawling factory, time and cost-efficiency are top priorities. A plastic seal machine can significantly speed up the packaging process while maintaining high-quality seals. This comprehensive guide aims to address every aspect of plastic seal machines—from selecting the right type to preventive maintenance—so you can navigate the market with confidence and get the most out of your investment.
2. How Plastic Seal Machines Work: Core Components and Processes
To fully appreciate the value of a plastic seal machine, let’s break down the basic science behind it. While various models exist—from simple handheld sealers to fully automated systems—the core operating principle remains similar.
- Heating Element: At the heart of most plastic seal machines lies a heating wire or bar. When the machine is activated, an electric current passes through the heating element, raising it to the required temperature.
- Sealing Jaw or Bar: This is where the plastic material is clamped for sealing. Pressure is applied by either a manual lever or an automated mechanism, ensuring the two plastic layers fuse together.
- Cooling Mechanism: After heat fuses the plastic layers, a cooling phase locks in the seal’s integrity. Some advanced machines use water or air-cooling systems to accelerate this phase.
- Control Panel: Modern machines often come with digital controls that let you adjust temperature, sealing time, and pressure. Achieving the right balance prevents under-sealing (leading to leaks) or over-sealing (causing plastic damage).
Why Does This Process Matter?
Knowing how a plastic seal machine works helps you troubleshoot common issues (like uneven seals or melted plastic) and optimize settings for different plastic thicknesses and compositions. Mastery of this fundamental process separates efficient packaging operations from costly, error-ridden ones.
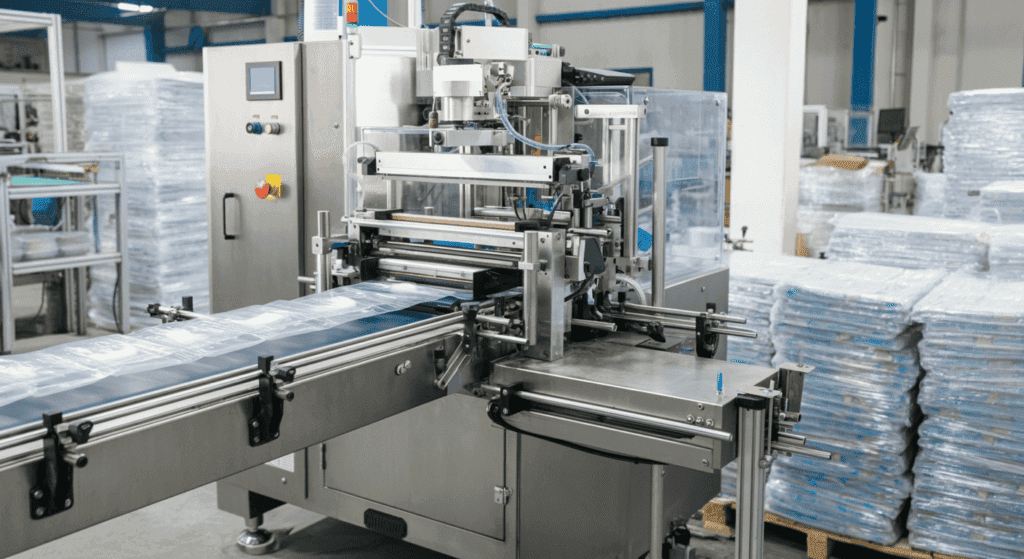
3. Types of Plastic Seal Machines and Their Best Uses
Not all plastic seal machines are created equal. The right model depends on factors like production volume, packaging material, budget constraints, and industry regulations. Below are the most common types you’ll encounter.
3.1 Handheld Heat Sealers
- Description: Small, portable devices that use a heated jaw to seal plastic bags or pouches.
- Ideal For: Low-volume operations, home-based businesses, or occasional packaging needs.
- Advantages: Affordable, minimal maintenance, and easy to store.
- Drawbacks: Not suitable for large-scale, continuous sealing due to manual operation.
3.2 Impulse Sealers
- Description: These sealers deliver short bursts of heat, ideal for materials like polyethylene (PE) or polypropylene (PP).
- Ideal For: Moderate-volume packaging in retail stores, laboratories, or small manufacturing units.
- Advantages: Energy-efficient (heating element is active only when sealing), versatile, and user-friendly.
- Drawbacks: May not handle thicker plastic films efficiently.
3.3 Continuous Band Sealers
- Description: These machines seal pouches and bags as they move along a conveyor belt, offering high-speed sealing.
- Ideal For: Medium to high-volume operations in food packaging, chemical industries, and pharmaceuticals.
- Advantages: Automated sealing, adjustable speed, and temperature control for consistent seals.
- Drawbacks: Higher initial cost and more complex maintenance.
3.4 Automatic Rotary Sealers
- Description: Utilize rotating belts or rollers to apply heat and pressure continuously.
- Ideal For: Industrial packaging lines where speed and consistency are paramount.
- Advantages: Automated, high throughput, often includes cutting and trimming functions.
- Drawbacks: Requires significant floor space, potentially higher energy consumption.
3.5 Vacuum Sealers
- Description: Remove air from the package before sealing, ideal for products sensitive to oxidation or moisture.
- Ideal For: Food packaging (especially meat, cheese, and coffee), electronics, and medical supplies.
- Advantages: Extended shelf life, reduced product spoilage, professional appearance.
- Drawbacks: Higher cost, might require specialized bags or pouches.
3.6 Ultrasonic Sealers
- Description: Use ultrasonic vibrations instead of heat to fuse plastic materials, often employed in specialized industries like medical device packaging.
- Ideal For: Heat-sensitive materials or high-precision seals.
- Advantages: Minimal thermal stress on the packaging material, consistent sealing even through contaminants.
- Drawbacks: Higher initial cost, specialized maintenance required.
4. Key Features to Look For Before Buying
Choosing the wrong plastic seal machine can lead to production bottlenecks, wasted materials, and even safety hazards. Here are the crucial factors to evaluate before making a purchase:
- Sealing Width and Length
- Ensure the machine can accommodate the width of bags or pouches you intend to seal.
- Industrial packaging often requires wider seals for added strength.
- Adjustable Temperature Settings
- Different plastic materials have unique melting points. Look for a machine that offers precise temperature control to avoid under- or over-sealing.
- Sealing Speed
- High-volume operations need faster machines with automated feeding systems.
- If your volume is moderate, a simpler model with manual feeding might suffice.
- Build Quality and Materials
- Stainless steel frames resist corrosion and endure continuous operation.
- Check the quality of components such as belts, heating elements, and control panels.
- Ease of Maintenance
- Look for modular designs where parts can be quickly swapped out.
- Read user reviews to gauge how frequently typical wear-and-tear components need replacement.
- Safety Features
- Machines with built-in alarms or auto-shutoff can prevent overheating.
- Safety guards or shields around the sealing area reduce the risk of workplace accidents.
- Warranty and After-Sales Support
- Reliable manufacturers often provide extended warranties and easily accessible service centers.
- Factor in the availability of spare parts when calculating long-term ownership costs.
By focusing on these key features, you’re more likely to invest in a plastic seal machine that meets your operational demands and budgetary constraints.
5. Sealing Technology Innovations for Modern Packaging
The packaging industry is constantly evolving. Whether it’s the push for sustainability or the drive for faster production, new sealing technologies are making their mark.
5.1 Automated Sensor Controls
Modern plastic seal machines often incorporate sensors that measure temperature, pressure, and even bag placement. This reduces the margin for human error and ensures each seal is identical, enhancing consistency across product lines.
5.2 Smart Connectivity
Imagine receiving a notification on your phone if a seal fails or if the machine requires maintenance. Thanks to the Internet of Things (IoT), this is becoming a reality. Wi-Fi-enabled sealers can transmit performance metrics in real time, helping managers optimize production schedules and quickly address faults.
5.3 Sustainable Sealing Materials
As businesses seek eco-friendly packaging solutions, biodegradable or compostable films are on the rise. Sealing these specialized materials may require lower temperatures or different sealing times—making a machine with precise control essential.
5.4 Robotics and AI Integration
Automated robotic arms paired with AI-driven vision systems can position items for sealing without manual intervention. While this might be overkill for small and mid-sized operations, it’s an increasingly popular solution for large-scale factories focusing on high throughput with minimal labor costs.
Pro Tip: If you’re unsure whether a cutting-edge technology is worthwhile for your operation, run a cost-benefit analysis. Compare potential gains in productivity or brand image (like sustainability credentials) against the machine’s total cost of ownership.
6. Common User Challenges and Practical Solutions
Even the most advanced plastic seal machine can encounter problems. Below are common challenges users face, along with actionable ways to overcome them.
Challenge 1: Inconsistent Seal Quality
- Possible Causes: Temperature fluctuations, uneven pressure, or dirty sealing surfaces.
- Solution: Calibrate your machine regularly. Clean the sealing jaws after every shift to remove melted plastic residues.
Challenge 2: Slow Throughput
- Possible Causes: Manual feeding, frequent downtime for maintenance, or inadequate heat recovery between seals.
- Solution: Upgrade to a continuous band sealer or add a conveyor system. Ensure your machine’s heating elements and cooling systems match your production speed requirements.
Challenge 3: Excessive Material Waste
- Possible Causes: Overlapping bags, incorrect bag sizes, or poorly aligned sealing jaws.
- Solution: Train operators on proper bag placement and machine setup. Consider machines with alignment guides or sensors that detect misfeeds.
Challenge 4: Operator Safety
- Possible Causes: High temperatures, unprotected moving parts, or lack of safety training.
- Solution: Invest in machines with safety covers and emergency stop buttons. Provide comprehensive training and clear signage. Perform routine risk assessments.
Challenge 5: Seal Failure in Extreme Environments
- Possible Causes: Machines operating in humid or dusty settings without adequate protection.
- Solution: Opt for IP-rated (Ingress Protection) machines designed to withstand specific environmental conditions. Regularly inspect and clean internal components to prevent buildup or corrosion.
7. Maintenance and Safety Tips to Maximize Machine Lifespan
A well-maintained plastic seal machine can run for many years, delivering consistent performance. Here’s how to keep your machine in top shape:
7.1 Routine Cleaning
- Daily: Wipe down external surfaces with a soft cloth to remove dust and grime.
- Weekly: Clean sealing jaws with isopropyl alcohol to remove plastic residue.
- Monthly: Check the conveyor belt (if applicable) for wear or fraying edges.
7.2 Periodic Part Replacement
- Heating Elements: Over time, the wire or bar can degrade. Replace according to the manufacturer’s timeline or if you notice inconsistent sealing temperatures.
- Belts and Rollers: In continuous sealers, belts can wear out, leading to compromised seal quality.
- Gaskets and O-Rings: Vacuum sealers often rely on a tight seal for air extraction. Defective gaskets will result in partial seals or air leaks.
7.3 Lubrication and Calibration
- Lubricate: Some machines require periodic lubrication of moving parts. Consult your manual for recommended lubricants and schedules.
- Calibrate: Machines with digital controls may need software updates or hardware calibrations to maintain temperature accuracy.
7.4 Safety Drills
- Emergency Stop Practice: Ensure operators know how to activate emergency stop procedures and can recognize the signs of a machine malfunction.
- Clear Workspace: Keep the floor around the machine free of debris or spills to reduce slip hazards.
- Proper Gear: Encourage or mandate protective gloves, heat-resistant clothing, and eye protection where necessary.
Safety Reminder: Never operate a plastic seal machine with damaged electrical cords or missing safety guards. If you suspect any issue with the machine’s structural integrity, shut it down immediately and consult a qualified technician.
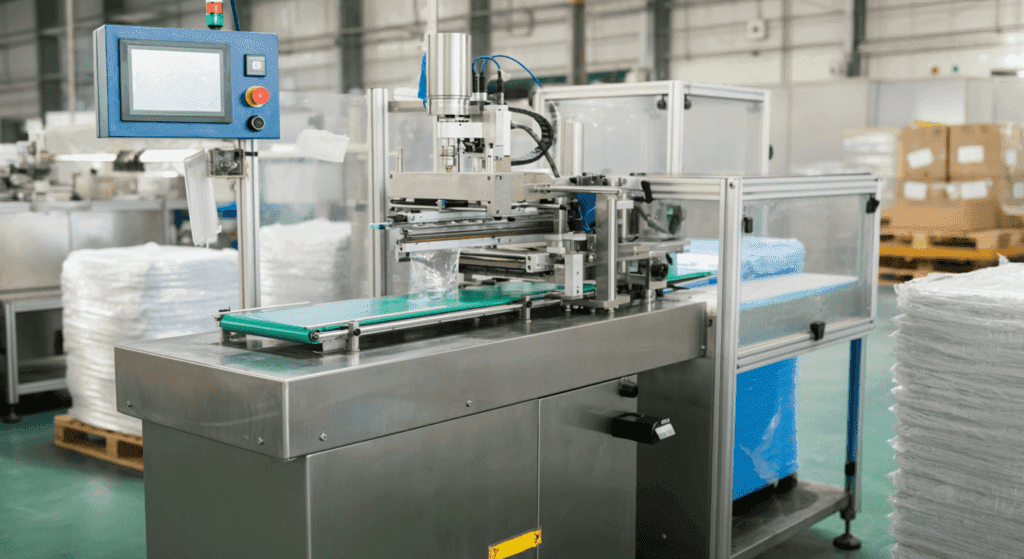
8. Industry Insights and Real-World Applications
The demand for robust packaging solutions spans a broad spectrum of sectors, each with unique requirements. Below are some industry-specific applications where a plastic seal machine plays a critical role.
8.1 Food and Beverage Industry
- High Sanitation Standards: Machines must be easy to clean and built from non-corrosive materials.
- Modified Atmosphere Packaging (MAP): Uses vacuum or gas flushing to extend shelf life, requiring specialized sealers with advanced sensors.
8.2 Pharmaceuticals and Healthcare
- Tamper-Evident Seals: Maintaining sterility is paramount, and any seal breach could be life-threatening.
- Precision: Ultrasonic sealers are often favored for medical pouches, as they minimize thermal stress and maintain package integrity.
8.3 E-Commerce and Retail
- Branding Opportunities: Clear plastic packaging with a well-executed seal offers an appealing product presentation.
- High Throughput: Continuous band sealers help handle large order volumes, especially during peak seasons or flash sales.
8.4 Chemicals and Industrial Goods
- Chemical Resistance: Packaging materials must withstand corrosive substances; the seal must remain intact under harsh conditions.
- Bulk Packaging: Large pouches or drums might necessitate specialized or custom-built sealers.
8.5 Electronics and High-Value Goods
- Anti-Static Packaging: Some products require special static-resistant bags, which must be sealed at precise temperatures.
- ESD Safety: Operators often need to use grounding devices to prevent damaging electrostatic discharge during packaging.
9. FAQ: Your Plastic Seal Machine Questions Answered
Below are some frequently asked questions about plastic seal machines, optimized in a Q&A format to help you quickly find solutions and insights.
Q1: How often should I replace the heating element on my plastic seal machine?
A1: It depends on usage and the quality of the element. Many manufacturers recommend changing it every 6 to 12 months for continuous operation. However, always monitor for signs of wear or uneven heating.
Q2: Can a plastic seal machine handle different types of plastic films (e.g., polyethylene, polypropylene, mylar)?
A2: Most machines can handle a range of materials as long as you adjust temperature and sealing time. Check the manufacturer’s specifications to ensure compatibility with less common or multi-layer films.
Q3: What if my seals keep failing in a humid environment?
A3: High humidity can affect the machine’s electronics and the sealing process itself. Make sure your equipment is rated for the environment. You may also need a dehumidifier or moisture barriers around the production area.
Q4: Are vacuum sealers worth the extra cost?
A4: Vacuum sealers can significantly extend the shelf life of perishable items by removing oxygen. If you deal with food, electronics, or medical products that require long-term preservation, the upfront investment often pays off in reduced spoilage.
Q5: How do I ensure my machine meets local safety regulations?
A5: Check for UL (Underwriters Laboratories) or CE (Conformité Européenne) certifications. Also, review Occupational Safety and Health Administration (OSHA) guidelines or local equivalents to confirm compliance.
Q6: Can I use a plastic seal machine for liquid products?
A6: Yes, but you need to be extra cautious. Ensure the plastic pouch or container is upright and that the machine is equipped to handle potential spills. Some machines come with specialized clamps or compartments for liquid packaging.
Conclusion and Next Steps
A plastic seal machine is more than just a piece of equipment; it’s a cornerstone of efficient and effective packaging. From the nuanced science of heat application to the cutting-edge possibilities of IoT connectivity, the world of plastic seal machines is rich with opportunities to enhance product presentation, extend shelf life, and increase customer satisfaction. By understanding the different types of sealers, you can select a model tailored to your production scale and budget. Knowing how to maintain and troubleshoot your equipment ensures you stay ahead of costly downtime.
Key Takeaways
- End-to-End Knowledge: Familiarize yourself with machine components, from heating elements to conveyor belts, to effectively diagnose common issues.
- Customization: Different industries have unique needs—choose a machine that aligns with your operational goals, environmental conditions, and regulatory requirements.
- Maintenance Saves Money: Regular cleaning, part replacement, and calibration are essential for maximizing the lifespan and performance of your plastic seal machine.
- Stay Future-Ready: Keep an eye on emerging technologies like smart sensors, IoT integrations, and biodegradable materials to remain competitive and eco-friendly.
Ready to Elevate Your Packaging Process?
- Comment: Have questions or unique packaging challenges? Share them below.
- Share: If you found this guide helpful, pass it along to colleagues or friends.
- Subscribe: Sign up for our newsletter to stay updated on the latest packaging technologies, industry insights, and exclusive tips for optimizing your plastic seal machine operations.
By adopting the insights and best practices outlined in this guide, you’re well on your way to achieving a streamlined, cost-effective, and high-quality packaging system that resonates with both end-users and industry professionals. Embrace the power of the right plastic seal machine, and watch your efficiency—and brand reputation—soar.
Stay Connected with EngiTech
EngiTech is your trusted source for in-depth knowledge on industrial mechanical engineering machines and technologies. Stay ahead with the latest innovations, expert insights, and practical guides designed to help you make informed decisions for your business and engineering needs. Join our growing community of professionals and industry leaders to stay updated and competitive in the ever-evolving world of industrial technology.