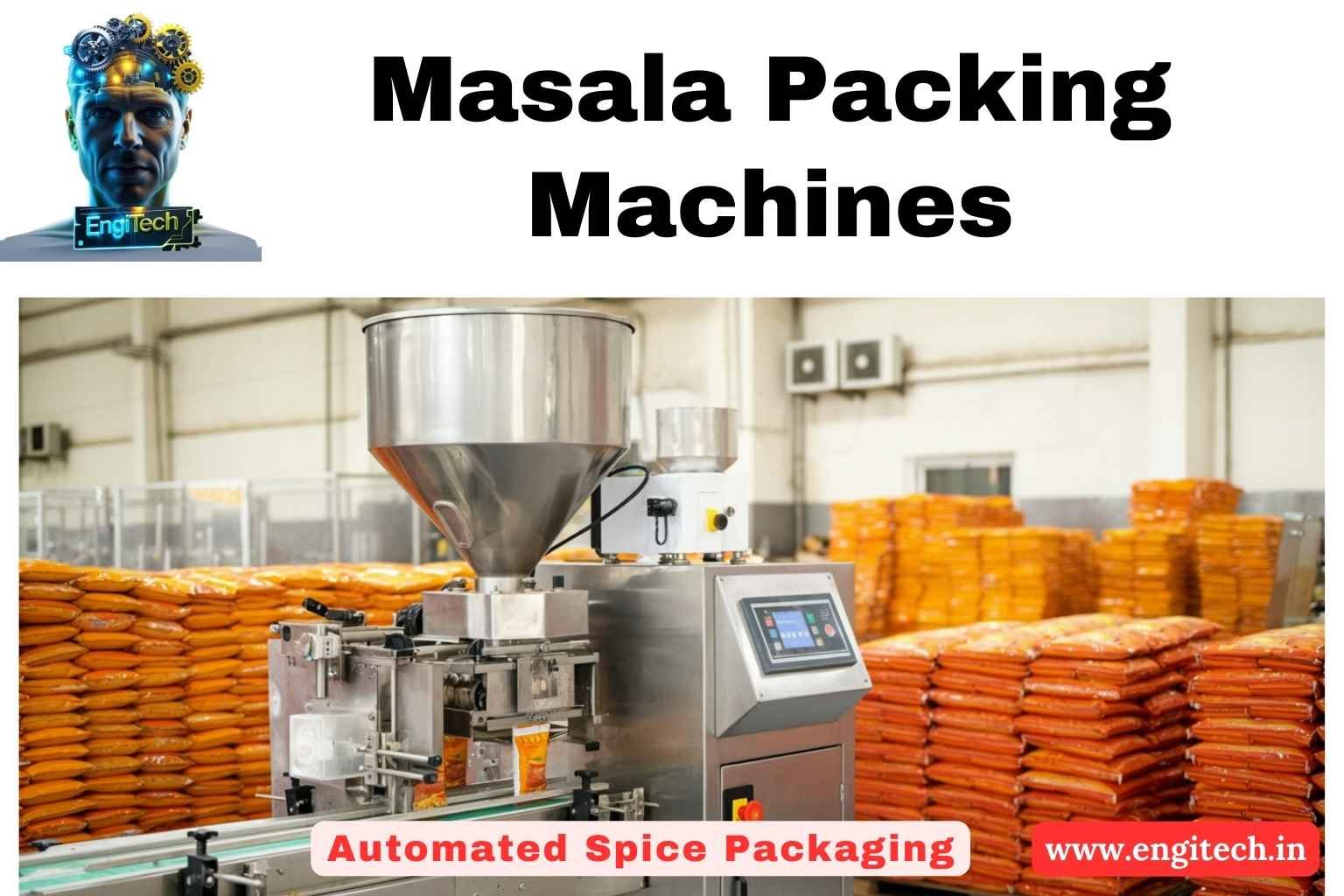
Introduction: Why Masala Packing Machines Matter
Imagine walking down the spice aisle in a bustling market: vibrant aromas of turmeric, cumin, coriander, and chili powder swirl together, promising bold flavors and mouthwatering dishes. Each packet of masala you see has likely gone through a meticulously designed packaging process to preserve freshness and maintain quality. For businesses, getting that process right can be the key to customer satisfaction and brand loyalty. And that’s precisely where a Masala packing machine comes into the picture.
In today’s competitive market, preserving the authenticity of masala is crucial for both large-scale spice producers and small businesses looking to thrive. One of the biggest challenges is ensuring that the packaged spices remain aromatic, uncontaminated, and in perfect condition until they reach the end consumer. The right masala packing machine not only automates the process but also minimizes product loss, enhances hygiene, and reduces labor costs. This guide explores everything you need to know about masala packing machines, including the latest technologies, best operational practices, and tips for selecting the perfect model for your business.
Whether you’re a seasoned spice manufacturer or a budding entrepreneur, you’ll find actionable strategies in this article to enhance efficiency, improve packaging quality, and boost overall customer satisfaction. By the end, you’ll be well-prepared to make an informed decision about investing in a masala packing machine—or optimizing the one you already own.
Table of Contents
Understanding the Masala Packing Machine Market
The global market for spice and masala packaging has evolved exponentially in the last decade. According to recent industry reports, consumers worldwide are increasingly exploring international cuisines, boosting the demand for packaged spices. An efficient Masala packing machine responds to this surge by offering both quality and quantity packaging in less time.
Global Demand for Spices
- Rising Culinary Exploration: People are experimenting with dishes from different cultures, driving the popularity of ready-to-use spice packets.
- Convenience Factor: Modern lifestyles demand quick and convenient cooking solutions. Pre-measured masala packs reduce preparation time.
- Stringent Quality Standards: Regulatory bodies and consumers emphasize hygienic packaging, influencing companies to invest in high-end machinery.
Importance of Packaging for Customer Satisfaction
Packaging is no longer just a protective layer; it is an extension of your brand. Customers often associate the packaging’s appearance and convenience with product quality. When spices are vacuum-sealed, nitrogen-flushed, or properly sealed in laminated pouches, consumers sense the commitment to freshness. This perception directly impacts brand loyalty and repeat purchases.

Key Components and Functionality
A Masala packing machine is designed with several integrated components working in harmony to ensure efficient and precise packaging. Understanding these parts is crucial for proper operation and maintenance.
Main Components
- Feeding System: Transfers masala powder from a hopper or feeder into the packaging machine.
- Weighing Mechanism: Ensures that the correct quantity of masala is dispensed into each packet, maintaining consistent weight and reducing wastage.
- Form-Fill-Seal Unit: Creates the pouch from a roll of packaging film, fills it with masala, and seals it securely to prevent leakage.
- Control Panel: Features user-friendly touchscreens or digital controls for setting parameters like filling speed, packet weight, and sealing temperature.
- Sealing Jaws: Apply controlled pressure and heat to seal pouches, ensuring they’re airtight.
- Discharge Conveyor: Transports the finished packets for secondary packaging or final storage.
Automation and Sensors
Modern masala packing machines incorporate advanced sensors that detect whether a pouch is in place, monitor fill levels, and regulate temperature. Automation ensures consistency, with minimal human intervention needed once the machine is set up. This level of precision is essential in preventing downtime, preserving product freshness, and meeting strict regulatory standards.
Types of Masala Packing Machines
Selecting the right type of Masala packing machine depends on your production capacity, budget, and specific packaging requirements. Below are the common variants:
1) Automatic Masala Packing Machines
Key Features
- High-speed operation, often packing 40-100 pouches per minute.
- Advanced weighing and filling technology for minimal error.
- Ideal for large-scale spice manufacturers handling huge volumes.
- Equipped with digital sensors to reduce human labor.
Advantages
- Consistent output and accurate fill weights.
- Lower labor requirements.
- Reduced downtime due to automated features.
Disadvantages
- Higher initial investment.
- Requires skilled technicians for maintenance.
2) Semi-Automatic Masala Packing Machines
Key Features
- Partially automated but still requires manual labor for certain tasks like pouch loading or sealing alignment.
- Usually packs 20-50 pouches per minute.
- Suitable for small to medium enterprises.
Advantages
- More affordable than fully automatic units.
- Easier to operate with minimal training.
Disadvantages
- Slightly slower packaging rate.
- Greater reliance on operator precision.
3) Manual Filling and Sealing Machines
Key Features
- Requires an operator to hand-fill and then seal each pouch.
- Typically used by small-scale businesses, home-based spice suppliers, or niche market producers.
Advantages
- Very low initial cost.
- Best for extremely small production runs or specialty products.
Disadvantages
- Labor-intensive, which can increase overhead costs.
- Prone to human error, resulting in inconsistent packet weights.
Choosing the Right Machine for Your Business
Your perfect masala packing machine isn’t necessarily the most expensive or the fastest one. It’s the unit that balances your unique business needs, budget, and product quality requirements. Below are some factors to consider:
- Production Volume: Assess how many kilograms or pouches of masala you need to package daily.
- Budget Constraints: Factor in not just the purchase price but also the long-term costs like maintenance and electricity usage.
- Automation Level: If you have a fast-growing business or plan to scale, an automatic machine may offer the best long-term ROI.
- Space Availability: Measure your production floor space to ensure the machine fits seamlessly into your facility.
- Integration Needs: Some machines can integrate with labeling systems or barcoding units. If branding and traceability are crucial, look for integrated solutions.
- Service and Support: Check the availability of local service centers or supplier support to minimize downtime.
Actionable Tip: Visit trade shows or talk to existing machine owners to get firsthand insights. Real-world testimonials often reveal details that brochures and spec sheets might overlook.
Step-by-Step Packing Process Explained
Let’s break down the masala packing process to see how a typical automated system handles spice packaging:
- Loading the Hopper
- Operators load masala powder into a central hopper.
- The hopper often has a stirrer to prevent clumping, especially important if the spice has high moisture content.
- Weighing and Dispensing
- Automated scales measure the exact amount of masala required per pouch.
- Load cells or weigh sensors monitor and maintain precise weight.
- Pouch Formation
- A roll of printed film or packaging material unwinds into the machine.
- The machine forms it into a tube, and a vertical seal is applied.
- Filling
- The machine dispenses the measured quantity of masala into the newly formed pouch.
- Proper timing and synchronization ensure no spillage or wastage.
- Sealing and Cutting
- Horizontal sealing jaws seal the top of the pouch.
- The finished packet is cut off, completing the cycle.
- Batch Coding and Labeling (Optional)
- The machine can print batch numbers, manufacturing dates, or barcodes.
- Some setups integrate labeling systems for branding.
- Inspection and Discharge
- Finished packets move along a conveyor to a collection tray.
- Operators may perform random quality checks.
- Secondary Packaging
- Pouches are packed in cartons or shrink-wrapped for transportation.
Common Challenges and Troubleshooting Tips
Even the most advanced masala packing machine can face issues. Recognizing early warning signs helps prevent downtime and ensures your product quality remains consistent.
Frequent Issues
- Inconsistent Weight: Could be due to a faulty weigh sensor or changes in the product’s moisture content.
- Poor Sealing Quality: Might stem from incorrect temperature settings or damaged sealing jaws.
- Product Spillage: Often happens if the timing between the filler and the sealer is off.
- Clogging: Sticky or oily masala powders can block hopper outlets or dispensing nozzles.
Troubleshooting Tips
- Calibrate Regularly: Make it a routine to check and calibrate weight sensors.
- Monitor Temperature: Use a digital thermometer to ensure the sealing jaws are neither too hot nor too cold.
- Use Appropriate Packaging Films: If your spice has high oil content, opt for moisture-resistant and oil-resistant films.
- Clean Thoroughly: Residue build-up can cause machine jams, leading to increased downtime.
Expert Insight: According to seasoned technicians, up to 80% of machine-related problems can be prevented with routine maintenance and timely equipment upgrades. Maintaining a log of issues, solutions, and outcomes can help diagnose recurring problems faster.
Maintenance and Safety Guidelines
Efficient operation and a long machine lifespan go hand-in-hand with a robust maintenance schedule. Safety measures also protect both workers and equipment. Below are some comprehensive guidelines:
- Daily Cleaning: Clear out any spice residues. Spices left overnight can attract moisture, potentially causing rust or bacterial growth.
- Lubrication: Use manufacturer-recommended lubricants on moving parts like gears, chains, and sealing jaws.
- Inspection of Critical Parts: Regularly examine the sealing jaws, belts, sensors, and PLC (Programmable Logic Controller) systems for wear and tear.
- Electrical Safety: Turn off the main power and follow lockout/tagout procedures before conducting any electrical work.
- Personnel Training: Only trained and authorized personnel should operate or service the machine. Regular training reduces the likelihood of accidents.
- Emergency Preparedness: Keep fire extinguishers and first-aid kits nearby. Ensure all safety guards are in place during operation.
By incorporating these safety and maintenance best practices, manufacturers can maintain consistent product quality, minimize downtime, and protect employee well-being.
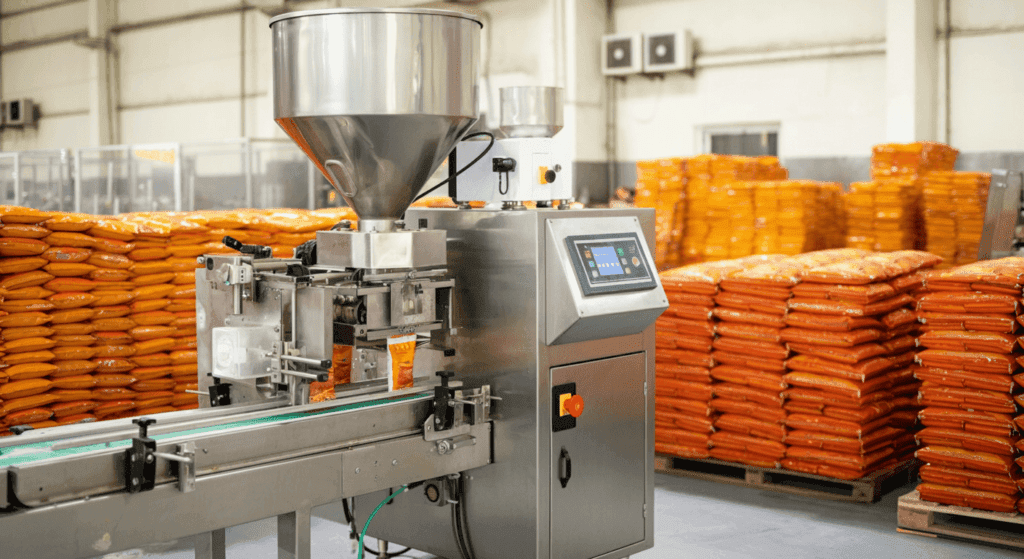
Cost Factors and ROI Considerations
When purchasing a Masala packing machine, you’re making a significant capital investment. Evaluating both the initial and long-term costs is essential to determine potential returns.
Initial Costs
- Machine Purchase: Varies depending on capacity, automation level, and brand reputation.
- Installation and Setup: Includes costs for freight, initial calibration, and possible retrofitting of your facility.
- Training: Some suppliers offer free training, while others charge for on-site or remote instructional sessions.
Ongoing Expenses
- Maintenance: Spare parts, regular servicing, and lubrication add to the ownership cost.
- Energy Consumption: High-capacity machines may require substantial electrical power.
- Labor: Even automated lines need oversight, especially for quality control and supervision.
Calculating ROI
To estimate ROI, factor in productivity gains, labor cost savings, and the potential for scaling production. For instance, a machine that can handle double your current output may pay for itself faster if your market demand is steadily growing. Alternatively, a smaller semi-automatic machine might be more prudent for a family-run spice business that prioritizes minimal overhead.
Industry Insights and Future Trends
The packaging sector is witnessing rapid innovations, many of which apply directly to masala packing machines. Staying updated can give your business a competitive edge.
Eco-Friendly Packaging
Consumers are more eco-conscious than ever, and many spice manufacturers are shifting to biodegradable or recyclable packaging materials. Machines capable of handling sustainable films or compostable pouches are gaining popularity.
Smart Technology and IoT
Advanced sensors, real-time monitoring, and machine-to-machine communication (M2M) can help manufacturers track efficiency, identify issues proactively, and perform predictive maintenance. Cloud-based dashboards provide remote access to machine metrics, boosting operational agility.
High-Speed, High-Precision Machines
With the spice sector’s global expansion, manufacturers seek machines capable of consistently packaging large volumes without sacrificing accuracy. Innovations in weigh scales and servo-driven mechanisms make this a reality.
Integration with Automated Warehouse Systems
Next-generation machines often integrate directly with automated warehouse solutions for seamless inventory management. Such integrations help reduce errors in storage, retrieval, and shipping processes.
FAQs About Masala Packing Machines
Q1: Which masala packing machine is best for a startup business?
For most startups, a semi-automatic masala packing machine balances cost and efficiency. It allows you to manage moderately high volumes without the steep price of fully automatic machinery.
Q2: How do I prevent spice clumping inside the hopper?
Consider using a hopper with a built-in agitator or stirrer. Adjust the speed of the stirrer based on how moisture-prone the spice mix is, and store raw materials in a low-humidity environment.
Q3: What type of packaging material is ideal for masala?
Often, laminated plastic or foil pouches are used because they offer good barrier properties against moisture and oxygen. If eco-friendliness is a priority, look into biodegradable plastic-alternatives suited for spices.
Q4: How often should the machine be serviced?
Basic daily cleaning is crucial. In terms of comprehensive servicing, manufacturers recommend a thorough check-up every 3 to 6 months. This includes calibrating sensors, lubricating moving parts, and replacing worn seals.
Q5: Is nitrogen flushing necessary for masala packaging?
Nitrogen flushing can extend shelf life by replacing oxygen inside the pouch, slowing down oxidation. It’s especially beneficial for spices prone to rancidity due to their oil content, like chili or turmeric.
Q6: Can I package multiple spice blends with one machine?
Yes, as long as you adjust the machine settings (weighing calibration, pouch size, sealing temperature) for each blend. However, thorough cleaning between batches is essential to prevent cross-contamination.
Conclusion
Masala packing machines are at the heart of modern spice manufacturing, ensuring that the final product remains fresh, aromatic, and accurately measured. By adopting advanced technologies, understanding the various types of machines available, and following rigorous maintenance guidelines, you position your business to excel in a highly competitive market.
Key Takeaways
- A Masala packing machine elevates both the efficiency and the quality of spice packaging.
- Choosing between automatic, semi-automatic, and manual options depends on your budget, production needs, and future growth plans.
- Regular maintenance and adherence to safety guidelines can significantly reduce downtime and prolong machine life.
- ROI depends not just on machine cost but also on how effectively you can scale and market your products.
- Staying updated on trends like IoT integration and eco-friendly packaging gives you an edge.
Ready to invest in a Masala packing machine or optimize your existing setup?
- Share your experiences or ask questions below—we’d love to hear about your journey in spice manufacturing.
- Explore our in-depth resources on Powder Packaging Solutions for further insights.
- Subscribe to our newsletter to stay updated on the latest in food packaging technology and industry best practices.
Your success in packaging aromatic spices can hinge on the right equipment, knowledge, and continual adaptation to evolving market trends. By leveraging expert insights, robust machinery, and a commitment to quality, you can position your brand as a go-to name in the masala world.
Stay Connected with EngiTech
EngiTech is your trusted source for in-depth knowledge on industrial mechanical engineering machines and technologies. Stay ahead with the latest innovations, expert insights, and practical guides designed to help you make informed decisions for your business and engineering needs. Join our growing community of professionals and industry leaders to stay updated and competitive in the ever-evolving world of industrial technology.