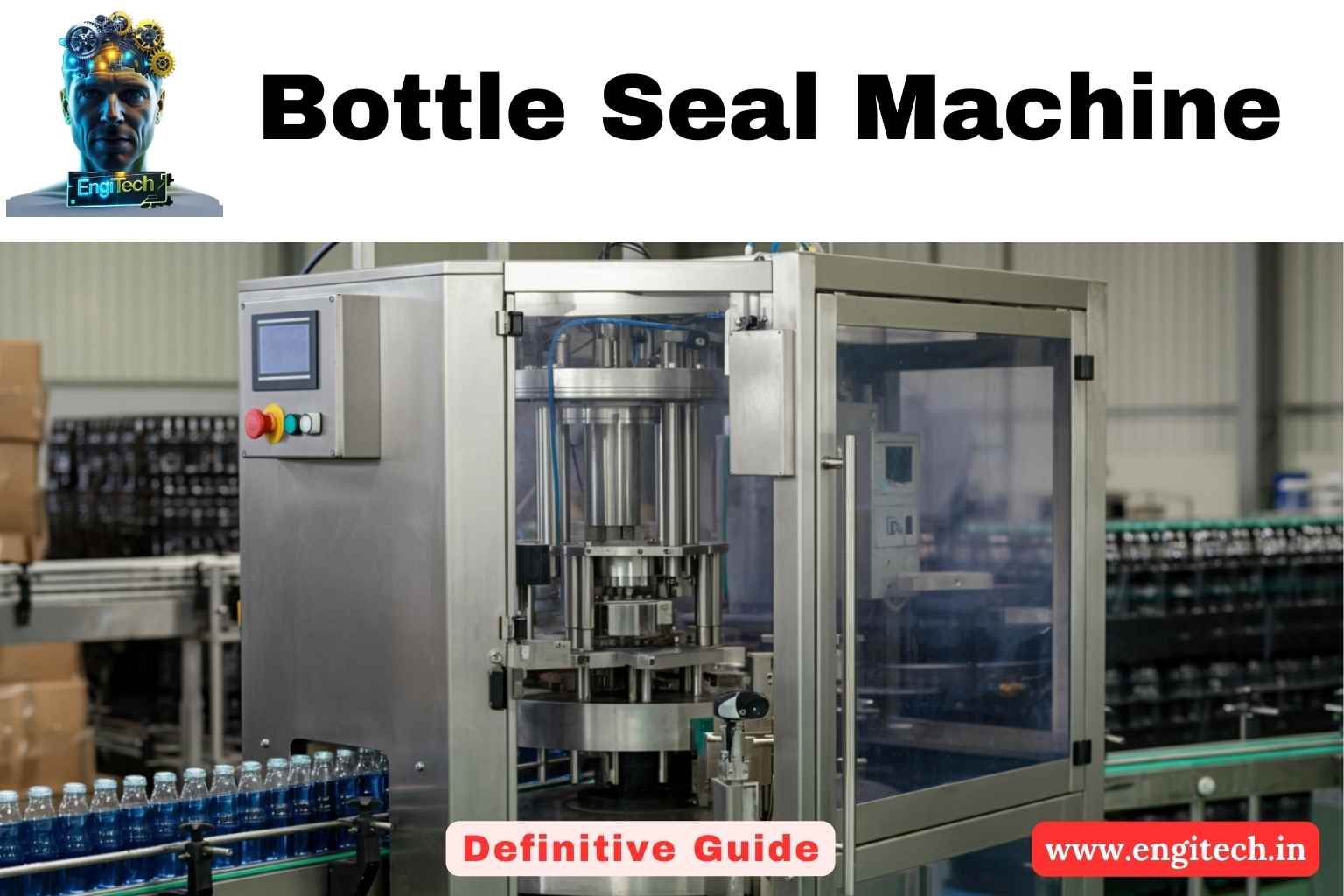
Picture this: You’ve meticulously filled hundreds—maybe thousands—of bottles with your product. It could be a newly launched sports drink, a popular hot sauce, or a freshly formulated cosmetic serum. But despite your best efforts to create something remarkable, one overlooked detail can unravel the entire process: a faulty seal.
Consumers these days demand more than a decent product; they also expect impeccable hygiene, safety, and ease of use. One leaking bottle in a shipment can erode trust, trigger product recalls, or even damage your brand’s reputation. If you want to be absolutely certain each bottle meets the highest standards of consumer satisfaction, you need the right equipment—this is where a bottle seal machine shines.
Over the next several sections, we’ll take a deep dive into everything related to bottle seal machines. We’ll explore how they help maintain product quality, discuss the different types available on the market, explain how to choose and operate them effectively, and detail what it takes to keep them running smoothly. By the end of this guide, you’ll not only understand which machine suits you best but also how to leverage it for maximum efficiency and profitability.
Table of Contents
What Is a Bottle Seal Machine?
A bottle seal machine is specialized packaging equipment designed to create an airtight or tamper-proof seal on a variety of bottle types. Ranging from small benchtop models to fully automated systems, these machines apply seals through mechanisms like heat induction, pressure application, or ultrasonic sealing. In many industries—beverage, pharmaceutical, cosmetic, and more—proper sealing is a fundamental requirement for regulatory compliance, safety, and brand reputation.
Key Takeaways
- Primary Function: To ensure each bottle is thoroughly sealed for optimal freshness, safety, and shelf life.
- Industries: Commonly used in food and beverages, personal care products, cosmetics, pharmaceuticals, and more.
- Compliance: Most health authorities, such as the FDA (in the U.S.), consider sealing an essential component of consumer safety.
Why Proper Sealing Matters
Imagine buying a bottle of juice only to notice the cap isn’t secure. That one poorly sealed container raises doubts about the entire batch’s quality and safety. Trust is fragile in the marketplace, and a faulty seal can compromise not only customer satisfaction but also regulatory compliance.
- Product Integrity: A tight seal protects against contamination, spoilage, and tampering.
- Extended Shelf Life: Its shelf life is naturally prolonged when the product is kept safe from microbial and environmental factors.
- Regulatory Compliance: Agencies like the FDA, EMA, or local health departments often require airtight seals for specific products—especially those intended for human consumption or topical use.
- Consumer Confidence: A well-sealed bottle assures customers that the product they’re about to use has not been compromised.
Pro Tip: Beyond legal requirements, brand reputation is everything. A strong, reliable seal can safeguard your brand from negative reviews or potential lawsuits.
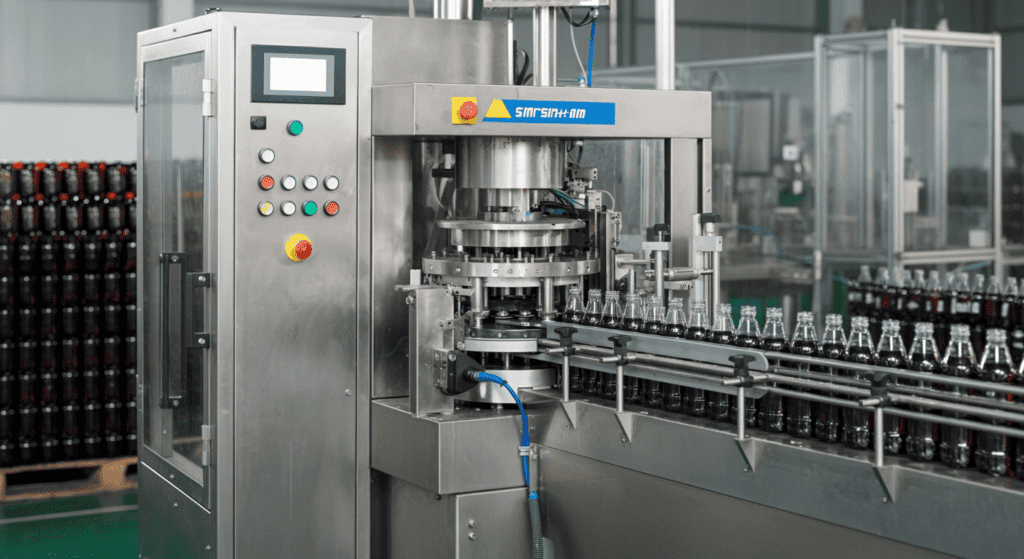
Key Components and How They Work
Although bottle seal machines come in various designs and sizes, several core components are typically found across different models:
- Sealing Head or Sealing Element: This is where the heat or pressure is applied to the bottle cap or foil seal.
- Conveyor (in Automated Systems): Moves bottles to and from the sealing area at a consistent rate, ensuring uniform output.
- Control Panel or Interface: Allows the operator to adjust temperature, speed, pressure, and other machine settings.
- Sensors and Safety Mechanisms: Modern bottle seal machines often include safety features like emergency stop buttons and sensors that detect misaligned bottles or missing caps.
- Chiller or Cooling System (Optional): In some high-heat processes, a cooling system ensures the machine and the sealed products don’t overheat.
By understanding these components, you can better appreciate the technology ensuring each bottle is sealed to perfection.
Types of Bottle Seal Machines
Whether you’re a budding entrepreneur or a large-scale producer, you’ll find a variety of bottle seal machines tailored to your industry. Below are the most common types:
1) Induction Sealers
Induction sealers use electromagnetic induction to heat an aluminum foil liner beneath the bottle cap. This heat melts the liner’s sealant material, bonding it to the bottle’s rim. Induction sealers are particularly popular in the food, beverage, and pharmaceutical industries due to their speed and reliability.
- Pros:
- Tamper-evident seal
- No direct contact or open flames
- Fast sealing speeds for high-volume production
- Cons:
- Requires specialized foil liners
- Higher initial cost compared to simpler sealing methods
2) Heat Shrink Sealing Machines
Heat-shrinking systems apply a shrink band or sleeve around the bottle’s cap. Heat causes the band to contract around the neck of the bottle or jar, creating a tamper-evident seal.
- Pros:
- Highly visible security (shrink bands show obvious tampering)
- Works well for a wide range of bottle shapes
- Cons:
- Requires additional consumables (shrink bands)
- May add time to production if done manually
3) Ultrasonic Sealers
Ultrasonic sealing technology uses high-frequency vibrations to generate heat at the interface between two materials, sealing them together without any external heat source. This method is less common for standard beverage packaging but is frequently used in niche or high-end applications.
- Pros:
- Ideal for heat-sensitive products
- Energy-efficient
- Strong, clean seals
- Cons:
- Specialized, expensive equipment
- Requires precise alignment and expertise
4) Pressure or Crimp Sealers
These machines apply mechanical force or crimping to attach lids or caps—often used in lab settings or for small-scale operations. Think of the crimp top you’d find on a bottle of carbonated water or specialized pharma products.
- Pros:
- Budget-friendly for small runs
- Straightforward operation
- Cons:
- Slower compared to automated machines
- May not provide a tamper-evident seal (unless designed with additional features)
5) Vacuum and Modified Atmosphere Packaging (MAP) Systems
Vacuum sealing removes air from the container before sealing, while MAP replaces the air with specific gases like nitrogen or carbon dioxide. These methods are mostly used in the food industry for products requiring extended shelf life.
- Pros:
- Extends freshness and preserves flavor
- Highly effective for perishable goods
- Cons:
- Can be expensive and complex
- Requires specialized packaging materials
How to Choose the Right Bottle Seal Machine
Selecting the best bottle seal machine for your operation is not just about finding a device that seals bottles. You must also consider efficiency, scalability, and compliance with industry standards. Below are the primary factors to evaluate:
- Production Volume:
- Small or Medium Scale: A semi-automatic induction sealer or a bench-mounted heat sealer might suffice if your output is moderate.
- Large Scale: Fully automated systems with conveyors and high-speed sealing heads are more appropriate if you’re producing thousands of bottles per hour.
- Container Material and Shape:
- Glass, plastic, or metal: Different materials react differently to heat and pressure.
- Unique shapes: Machines with adjustable guides or specialized sealing heads can handle irregular or custom-shaped bottles.
- Sealing Method and Temperature:
- Heat-sensitive products (like certain pharmaceuticals or cosmetics) may do better with ultrasonic sealing.
- For more robust and mass-produced items (like beverages), high-speed induction sealers are often best.
- Regulatory Requirements:
- Check local safety and food packaging regulations to ensure the machine meets all compliance standards.
- In certain industries, tamper-evident seals are mandatory.
- Budget and Scalability:
- Besides the initial purchase, consider the cost of consumables (foil liners, shrink bands) and long-term maintenance.
- Think ahead: will you need to scale production significantly in the future?
- Machine Footprint and Integration:
- If you’re short on space, you might consider a smaller benchtop model or a system that integrates easily with your existing production line.
Expert Insight: Before finalizing a purchase, request product trials or demos. Observing how the machine handles your specific bottle size and material can save headaches down the line.
Step-by-Step Guide: Using a Bottle Seal Machine
While each model varies, here’s a general overview of how most automated or semi-automated machines operate:
- Preparation
- Check the Seals: Whether you’re using induction foil liners or shrink bands, ensure you have the correct size and type for your bottle.
- Machine Setup: Adjust the settings for temperature, speed, or pressure based on your bottle material and size. Always consult the manufacturer’s manual.
- Positioning the Bottles
- If you have a conveyor system, place bottles upright on the belt. Ensure bottles are spaced evenly to prevent misalignment.
- For semi-automatic models, manually position each bottle under the sealing head.
- Applying the Seal
- Heat or Pressure Application: The machine applies heat (induction, steam, or infrared) or pressure to bond the seal.
- Cooling (if required): Some systems have a cooling zone to help set the seal quickly.
- Inspection and Quality Control
- Randomly inspect sealed bottles to confirm a secure seal with no wrinkles or gaps.
- Check for any signs of leakage or misapplied seals.
- Post-Sealing Procedures
- Labeling or packaging can follow once bottles have cooled (if heat was applied).
- Store sealed bottles under recommended conditions.
Pro Tip: A standardized workflow, including calibration and final inspection, reduces errors and ensures product consistency.
Maintenance Best Practices
Proper maintenance of your bottle seal machine enhances safety, reduces downtime, and extends equipment lifespan. Here are the most crucial steps:
- Daily Cleaning:
- Wipe down sealing heads, conveyors, and other surfaces to remove residue.
- Avoid harsh chemicals that could damage seals or corrode components.
- Regular Inspection:
- Check mechanical parts (belts, gears, sealing heads) for wear and tear.
- Listen for unusual noises—vibrations or screeching often signal a part nearing failure.
- Scheduled Servicing:
- Follow the manufacturer’s recommended service intervals, including lubrication and part replacements.
- Keep a maintenance log to track repairs, part replacements, and any issues.
- Calibration and Testing:
- For induction or ultrasonic machines, periodically test the temperature and alignment settings.
- If your seals start failing unexpectedly, recalibrate according to the manual or consult a technician.
- Staff Training:
- Ensure all operators know how to handle routine cleaning, minor troubleshooting, and safe shutdown procedures.
- Misuse by untrained staff is one of the most common causes of machine breakdown.
Common Challenges and Troubleshooting
No machine is foolproof. Here are some frequent hiccups you might encounter and ways to address them:
- Incomplete Seals
- Cause: Insufficient heat, poor alignment, or incorrect liner size.
- Solution: Check temperature settings, ensure the bottle is centered, and verify the correct liner dimensions.
- Overheating
- Cause: Excessively high sealing temperatures, continuous operation without breaks, or malfunctioning cooling systems.
- Solution: Allow the machine to cool, reduce the temperature setting, or inspect the cooling fans and vents.
- Wrinkled or Damaged Seals
- Cause: Overly high pressure, poorly sized shrink bands, or foreign particles on the sealing surface.
- Solution: Adjust the machine’s pressure and temperature settings, and clean the sealing head.
- Bottleneck or Production Delays
- Cause: Mismatch between conveyor speed and sealing head speed, or frequent jams in the machine.
- Solution: Reconfigure line speed, remove any obstructions, or upgrade to a system better suited for your throughput.
- Electrical or Mechanical Failure
- Cause: Aging parts, poor maintenance, or power surges.
- Solution: Regularly replace worn components, use surge protectors, and keep backup parts on hand.
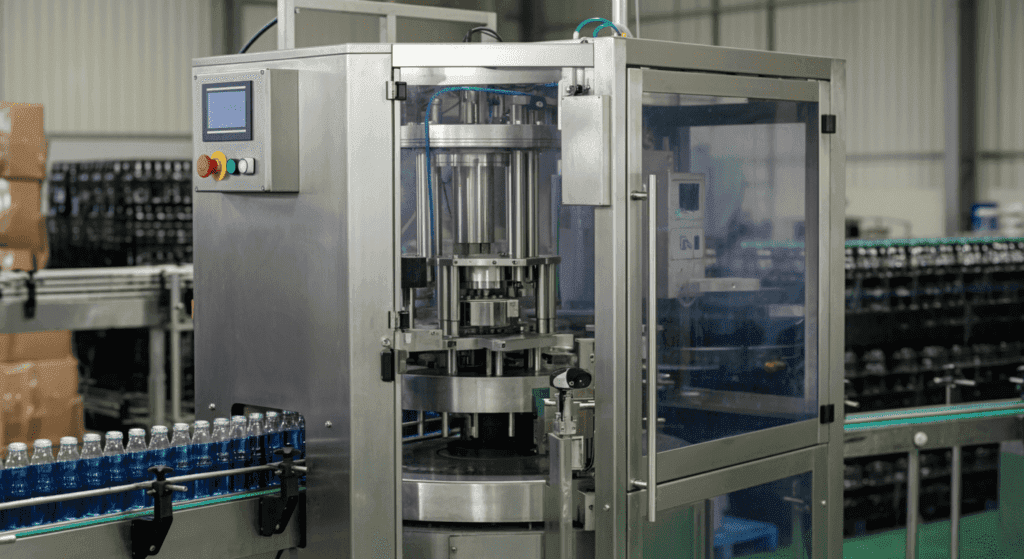
Industry Applications and Benefits
A bottle seal machine isn’t a one-size-fits-all piece of equipment; however, it plays an indispensable role in multiple sectors. Below is a brief look at the industries that heavily depend on dependable sealing processes:
- Food and Beverage
- Carbonated drinks, water bottles, juices, sauces, and edible oils.
- Benefits: Prevents spoilage, ensures tamper evidence, meets regulatory guidelines.
- Pharmaceutical and Healthcare
- Over-the-counter syrups, prescription medication bottles, and nutritional supplements.
- Benefits: Maintains product integrity, meets rigorous safety standards, provides tamper evidence.
- Cosmetics and Personal Care
- Creams, lotions, serums, and essential oils.
- Benefits: Preserves product efficacy, avoids contamination, offers a professional appearance.
- Chemical and Industrial
- Cleaning supplies, motor oils, or specialized chemicals.
- Benefits: Prevents leaks, maintains safety, and complies with shipping regulations.
- Dairy and Agriculture
- Dairy products, fertilizers, and various agri-based liquids often need specialized sealing to prevent leaks and ensure freshness.
Competitive Edge: Businesses that invest in modern, efficient seal machines can handle large order volumes, reduce returns due to leaks, and enhance brand reliability. The machine practically pays for itself in the long run by boosting productivity and protecting the brand’s reputation.
Frequently Asked Questions (FAQ)
Below are some of the most common questions people have about bottle seal machines—organized in a way that can boost your Featured Snippet potential.
Q1: How do I know if I need an induction sealer or a heat shrink sealer?
Answer: It depends on your product and sealing requirements. Induction sealers offer a highly secure seal beneath the cap, making them ideal for liquids and tamper-evident needs. Heat shrink sealers, on the other hand, place a visible shrink band around the cap—often used where a clear, tamper-evident band is desired. If you need a strong internal seal for fresh beverages or pharmaceuticals, induction sealing is likely better. For quick tamper evidence on cosmetic or food jars, heat shrink is a simple solution.
Q2: Is a bottle seal machine compatible with all bottle materials?
Answer: Most modern machines can handle plastic, glass, and even metal containers, but their optimal operation depends on proper settings and the right sealing materials. Always check the manufacturer’s guidelines before purchasing.
Q3: How does induction sealing work without direct heat or flames?
Answer: Induction sealing uses electromagnetic fields to generate heat in the aluminum foil liner under the cap. This localized heat melts the foil’s adhesive layer, bonding it to the bottle’s rim. It’s efficient, safe, and doesn’t expose your product to open flames.
Q4: Can I scale up an existing semi-automatic machine to meet higher production volumes?
Answer: Some semi-automatic models can be retrofitted with conveyors or upgraded to faster speeds. However, for significant volume increases, you may need to invest in a fully automated system designed to handle higher throughput.
Q5: How often should I replace liners or sealing components?
Answer: Induction liners are typically single-use items. Replace them with every bottle to ensure a fresh, tamper-evident seal. For machine components, follow the recommended maintenance schedule. Parts like sealing heads may last a long time but should be regularly inspected for wear.
Conclusion
Achieving a perfect seal every time is a cornerstone of product quality, safety, and branding. A bottle seal machine can take the guesswork out of this critical step, ensuring that each container not only looks professional but also meets the highest safety standards. From induction sealers that create a robust, tamper-proof bond beneath the cap to heat shrink systems that add a visible layer of security, there’s a machine to suit nearly any packaging need.
Key Takeaways:
- Identifying your production volume, container type, and industry regulations will narrow your search for the ideal sealing machine.
- Proper maintenance—from simple daily cleaning to scheduled servicing—helps you avoid costly downtime.
- Mastering the art of sealing not only instills consumer confidence but also streamlines your production line, cutting down on waste and returns.
Ready to Take the Next Step?
- Share Your Thoughts: Have you encountered any specific sealing challenges? Let us know in the comments below—we might feature your question in future updates.
- Explore More Guides: Check out our related articles on packaging automation and quality control tips to optimize your entire production process.
- Contact Our Team: If you need personalized advice on choosing the right bottle seal machine for your business, reach out to our technical experts. We’re here to help you find a tailored, cost-effective solution.
Your packaging line is an extension of your brand’s promise. By selecting and maintaining the right bottle seal machine, you safeguard not just the product but also your hard-earned reputation. Don’t settle for anything less than the best—invest in a sealing solution that meets today’s consumer demands and positions your business for long-term growth.
Stay Connected with EngiTech
EngiTech is your trusted source for in-depth knowledge on industrial mechanical engineering machines and technologies. Stay ahead with the latest innovations, expert insights, and practical guides designed to help you make informed decisions for your business and engineering needs. Join our growing community of professionals and industry leaders to stay updated and competitive in the ever-evolving world of industrial technology.