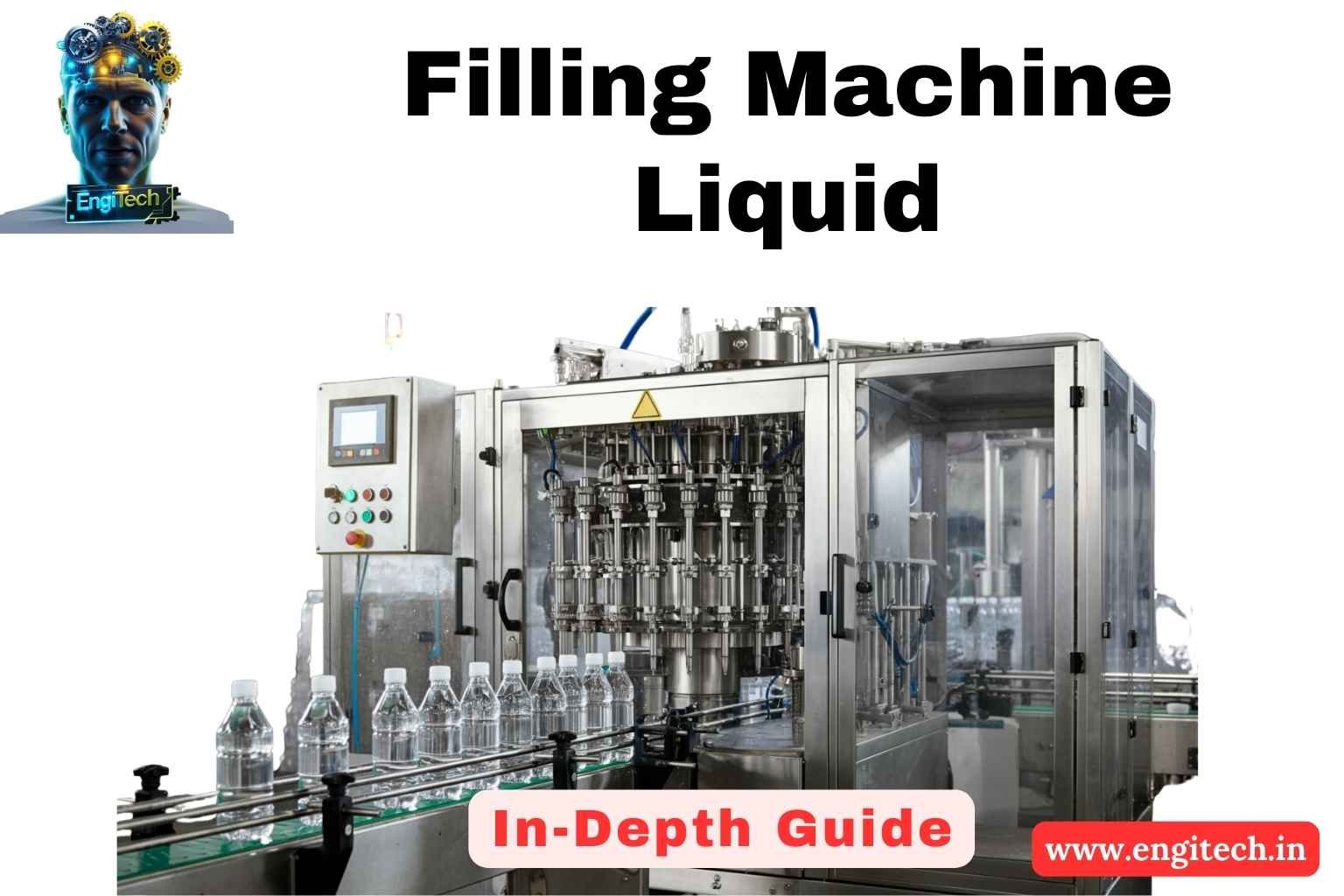
Are you trying to streamline your production line, reduce product waste, and ensure the highest safety standards when it comes to packaging liquids? If so, you are in the right place. In today’s fast-paced industrial environment, filling machine liquid solutions have become essential for businesses looking to elevate their operations. This comprehensive guide will walk you through everything you need to know, from the basics of liquid fillers to advanced optimization techniques. If you’re new to liquid filling machines or you’re a seasoned professional looking to refine your processes, read on for insights that could revolutionize your packaging line.
Imagine running a small beverage company without a reliable way to fill bottles. Your workers stand in line manually pouring liquids into containers, double-checking measurements by sight. Not only does this slow you down, but you risk inconsistency in fill volumes, potential contamination, and, ultimately, a blow to your brand’s reputation. In a global marketplace, consistent quality is paramount—whether you’re packaging water, syrup, paint, or pharmaceutical solutions.
That’s precisely why filling machine liquid systems are a game-changer. They automate the process of measuring and dispensing fluid into containers with speed and precision. When optimized correctly, these machines minimize waste, reduce labor costs, and adhere to strict industry standards. For many businesses, the question is not whether to use a liquid filling machine, but which one to use, how to maximize its potential, and how to integrate it seamlessly with existing operations.
From the outset, it’s clear that liquid filling technology is not just about mechanics or automation; it’s about ensuring each product that goes out the door is safe, accurately measured, and delivered on time. In this guide, you’ll learn how to choose, install, operate, and maintain a liquid filling machine that aligns with your business goals—while also satisfying your customers’ needs and regulatory requirements.
Table of Contents
Types of Liquid Filling Machines
Liquid filling machines come in various forms. Each is designed to handle specific viscosity levels, container types, and production volumes. Below is an in-depth look at some of the most common types:
Gravity Fillers
How They Work: Gravity fillers rely on the simple principle of gravity to pull liquid from a holding tank into a container. The flow is controlled by valves that open and close based on fill level settings.
Pros and Cons:
- Pros: Simple design, cost-effective, and easy to maintain.
- Cons: Limited to lower viscosity fluids and may lack the precision required for certain high-end products.
Ideal Use Cases: Water, juices, and other thin liquids that flow easily under the force of gravity.
Piston Fillers
How They Work: Piston fillers use a piston to draw a specific volume of liquid from the product supply and then push it into the container. Volume accuracy is determined by the stroke length of the piston.
Pros and Cons:
- Pros: High accuracy, suitable for thicker or more viscous products (e.g., sauces, lotions).
- Cons: Requires more complex maintenance and has more moving parts, which can lead to downtime if not properly cared for.
Ideal Use Cases: Personal care items like creams, dense food products like peanut butter, and some semi-solid pharmaceutical products.
Overflow Fillers
How They Work: Overflow fillers fill containers to a certain level, allowing excess product to circulate back into the supply tank. This ensures that each container has the exact same fill line, which is ideal for transparent containers.
Pros and Cons:
- Pros: Aesthetically pleasing fill levels, great for thin to medium viscosity liquids.
- Cons: Not suitable for highly viscous products and might generate extra foam in some liquids like carbonated beverages.
Ideal Use Cases: Shampoos, lower viscosity soaps, beverages in clear bottles, and products where uniform fill appearance is crucial.
Pump Fillers
How They Work: Pump fillers employ various types of pumps—gear pumps, peristaltic pumps, or lobe pumps—to move liquid into containers. Flow rate and volume are precisely controlled by adjusting pump speed and time.
Pros and Cons:
- Pros: Highly versatile for a wide range of viscosities. Pumps can handle chunky liquids with particulates.
- Cons: Pump complexity can increase costs, and cleaning can be more involved due to multiple pump components.
Ideal Use Cases: Marinades with bits of herbs, beverages with small fruit pieces, cosmetic lotions with microbeads, and other specialized products.
Aseptic Fillers
How They Work: Aseptic fillers operate in a sterile environment to prevent any microbial contamination. They use advanced filtration, often combined with sterilization techniques for containers and packaging materials.
Pros and Cons:
- Pros: Essential for products with stringent sterility requirements, like pharmaceuticals or certain dairy items.
- Cons: High initial investment, requires specialized knowledge for operation and maintenance.
Ideal Use Cases: UHT milk, injectable pharmaceuticals, long-shelf-life products that cannot tolerate microbial presence.
Key Industries Benefiting from Liquid Filling Machines
- Food and Beverage: Bottled water, juices, carbonated soft drinks, sauces, dressings, oils, and more.
- Pharmaceutical and Biotech: Syrups, vaccines, intravenous fluids, injectable drugs.
- Cosmetics and Personal Care: Shampoos, conditioners, lotions, perfumes.
- Chemicals and Paints: Detergents, solvents, paints, industrial chemicals.
- Household Goods: Cleaning agents, dishwashing liquids, fabric softeners.
Each industry has unique regulatory requirements, viscosity challenges, and volume demands. However, they all share one goal: achieving consistent, safe, and efficient filling.
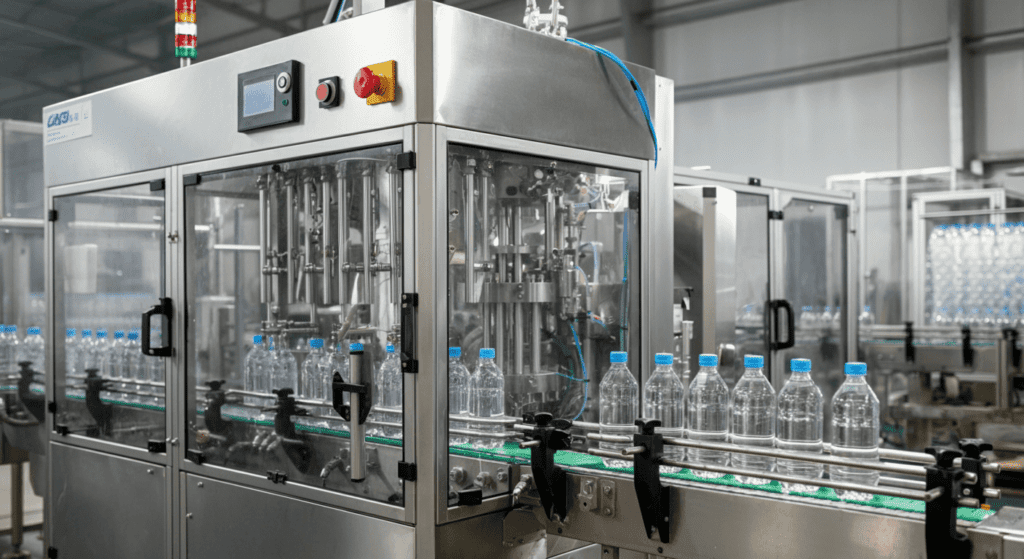
Core Components of a Liquid Filling Machine
While the design may vary across different types of liquid filling machines, you can generally expect the following core components:
- Product Tank or Hopper: Holds the liquid product before dispensing.
- Valves or Pumps: Control the flow of liquid to the container.
- Filling Nozzles: Dispense the liquid, often equipped with drip-free or anti-foaming features.
- Control Panel: Houses the electronic controls for speed, volume, and other operational parameters.
- Conveyor System: Transports containers to and from the filling station.
- Sensors and Actuators: Ensure precise fill levels and synchronize container movement.
- Frame and Housing: Provides structural support and can be made of stainless steel or other materials suitable for sanitary operations.
Understanding these components is crucial when you’re troubleshooting or deciding on the right machine for your application. Each part must be calibrated and maintained to ensure smooth operation and maximum product integrity.
How to Choose the Right Liquid Filling Machine
Selecting a filling machine is not merely about picking the fanciest model on the market. It’s about aligning a machine’s capabilities with your specific operational needs.
Viscosity Requirements
A watery liquid like bottled water or cold brew coffee flows at a much lower viscosity than a thick shampoo or peanut butter. Matching your machine type to the viscosity ensures consistent throughput and avoids clogs or inefficient fills.
Container Variety and Size
If you’re filling multiple container types—ranging from small vials to large jugs—you’ll need a machine that can handle different sizes without requiring lengthy changeover times. Some machines come with quick-change features or adjustable guides for different container shapes.
Production Throughput
Are you producing 1,000 bottles per hour or 100,000 bottles per hour? Your required speed will directly influence the type and scale of filling machine you invest in. Higher throughput usually means more advanced (and more expensive) machinery.
Accuracy Demands
Certain products, like pharmaceutical solutions, require near-zero deviation in fill volumes. Even in food and beverage industries, regulations might allow only minimal variance. Overfilling leads to product loss and increased costs, while underfilling can result in compliance issues.
Budget and ROI
While the initial cost of a high-end filling machine may seem daunting, consider long-term benefits. A more efficient machine can reduce labor and product waste, quickly paying for itself by improving overall operational efficiency.
Installation and Setup: Best Practices
A well-planned installation ensures your liquid filling machine operates smoothly from day one. Here are some best practices:
- Site Preparation: Make sure the installation area is clean, well-lit, and has adequate floor space to accommodate the machine and related equipment such as conveyors.
- Utility Requirements: Check for electrical voltage compatibility, compressed air supply (if needed), and proper drainage.
- Sanitation Compliance: Particularly in food, beverage, and pharmaceutical industries, ensure that floors, walls, and surrounding areas can be easily sanitized.
- Operator Training: Provide thorough training for machine operators. This includes safety protocols, basic troubleshooting, and routine cleaning procedures.
- Initial Calibration: Run several test fills using water or a standard solution to calibrate fill volumes, adjust nozzle heights, and confirm conveyor speeds.
By taking these preliminary steps seriously, you prevent costly downtime and ensure that your filling machine performs at its highest potential right from the start.
Operational Workflow: Step-by-Step Breakdown
While specifics may vary by machine type and industry, the general workflow typically follows these steps:
- Container Loading: Empty containers are placed on a conveyor system either manually or via an automated unscrambler.
- Indexing: Sensors detect the presence of containers, stopping them precisely under the filling heads.
- Filling Cycle: The machine dispenses liquid into the containers. Volume or level is typically controlled by timers, pumps, pistons, or overflow nozzles.
- Excess Removal or Sealing (Optional): In some systems, any excess liquid is removed, or the container might be sealed immediately (e.g., capping in a continuous process).
- Discharge: Filled containers move on to the next station—often a capping or sealing machine.
- Quality Check: Operators or automated systems inspect fill levels, ensuring they meet specified tolerances.
- Labeling and Packaging: After filling and sealing, containers usually go to labeling, coding, and final packaging before leaving the production floor.
Maintaining a clean, methodical workflow reduces cross-contamination and ensures each container is consistently filled, labeled, and sealed.
Maintenance and Cleaning Protocols
Routine maintenance and cleaning are paramount for efficiency and product safety. Without a solid schedule, you risk malfunctioning parts, contamination, or unplanned downtime.
- Daily Wipe-Down: Use a food-grade sanitizer or an industry-approved cleaning agent to wipe all contact surfaces.
- Weekly Inspection: Check valves, pistons, and seals for wear and tear. Tighten loose parts, and replace worn gaskets.
- Monthly Deep Clean: Drain the machine of any product, disassemble nozzles, hoses, and pumps (if applicable), and sanitize thoroughly.
- Lubrication: Follow the manufacturer’s guidelines on lubricating moving parts. Over-lubrication can attract dust or contaminate product, so always use food-safe lubricants where required.
- Professional Servicing: Schedule annual or bi-annual maintenance with certified technicians who can replace parts before they fail, calibrate sensors, and upgrade software if needed.
A well-maintained machine will not only last longer but will also produce more consistent fill volumes and reduce the risk of contamination or product loss.
Regulatory Compliance and Safety
No discussion about filling machine liquid systems is complete without addressing regulatory compliance. Different regions have agencies like the U.S. Food and Drug Administration (FDA) or the European Food Safety Authority (EFSA) overseeing standards, especially in food, beverage, and pharmaceutical industries.
- Material Standards: Stainless steel is often required for contact parts due to its corrosion resistance and ease of cleaning.
- Cleaning and Sanitation Protocols: Machines must be designed for rapid cleaning, especially in industries like dairy or pharmaceuticals where bacterial growth can be a serious concern.
- Labeling Requirements: Fill volumes must match what is declared on the label, and traceability standards might require batch coding.
- Operator Safety: Guardrails, emergency stop buttons, and clear safety signage must be present around mechanical and electrical components.
Fines, product recalls, and reputational damage can all stem from non-compliance. It’s essential to stay up-to-date with current regulations and invest in machinery that meets or exceeds those standards.
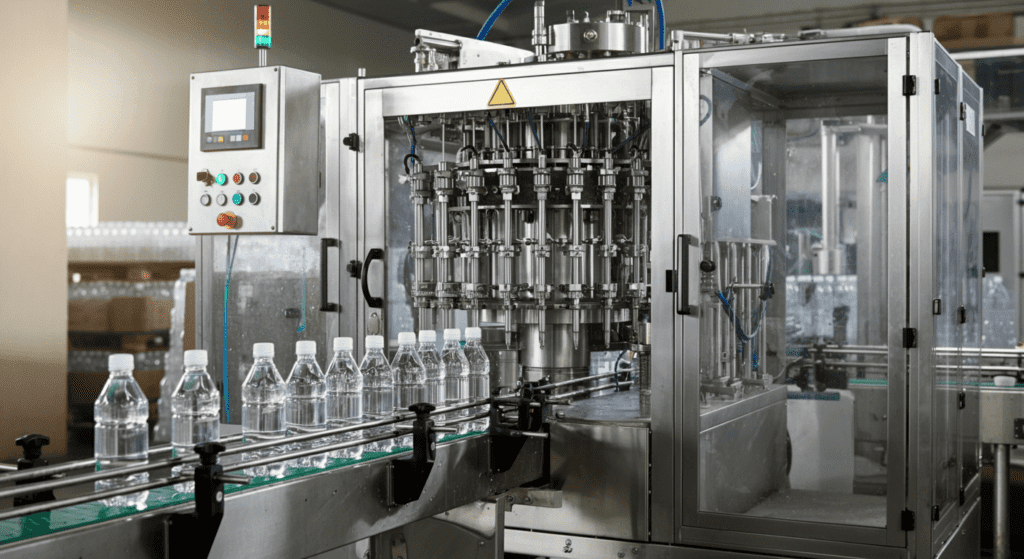
Optimizing Efficiency and Reducing Downtime
While investing in a reliable machine is important, how you operate and maintain that machine ultimately determines overall efficiency. Here are some strategies:
- Production Scheduling: Run machines during off-peak utility hours to reduce energy costs.
- Buffer Zones: Create buffer stock or intermediate storage so that a downstream disruption doesn’t stall the entire line.
- Real-Time Monitoring: Implement sensors and software that track fill rates, detect leaks, and monitor machine health.
- Training Programs: Consistent operator training reduces human error, speeds up troubleshooting, and leads to fewer accidents.
- Continuous Improvement: Conduct regular performance reviews, tracking metrics like Overall Equipment Effectiveness (OEE). Use this data to identify inefficiencies, whether in manning levels, fill rates, or machine maintenance.
By paying close attention to metrics and encouraging a culture of continuous improvement, your operation stays agile and productive.
Common Challenges and Troubleshooting
Even the best machines experience occasional hiccups. Below are a few common problems and how to address them:
- Inconsistent Fill Levels: Could be caused by inaccurate pump calibration, clogged nozzles, or variations in product viscosity due to temperature changes.
- Excess Foaming: Adjust nozzle design or fill speed, especially in overflow fillers. For carbonated beverages, specialized filling methods are often necessary.
- Leaks and Drips: Check seals, gaskets, and O-rings in pistons or pumps. Also, ensure your nozzle valves close properly.
- Machine Jams: Debris or an irregular container shape might jam conveyors or guide rails. Conduct daily inspections to spot and remove any obstructions.
- Electrical or Sensor Failures: Regularly check wiring and sensor alignment. Keep spare parts on-hand for quick replacement.
When troubleshooting, always follow your machine’s user manual and consult with the manufacturer’s support team if the issue persists. Investing in operator training will also help your team detect and address problems before they escalate.
Advanced Technologies and Future Trends
The world of filling machine liquid systems is not static. Constant advances are occurring in automation, robotics, and data analytics. A few emerging trends:
- Industry 4.0 and IoT Integration: Smart sensors send real-time data to a central control system, enabling predictive maintenance and remote troubleshooting.
- Robotic Arms: Some high-end systems use robotic arms for container handling, reducing manual labor and boosting precision.
- Adaptive Fill Algorithms: Machine learning algorithms dynamically adjust fill parameters based on changes in viscosity or temperature.
- Ultrasonic and Laser Scanning: Ensures more accurate fill-level detection without direct contact, minimizing contamination risks.
- Eco-Friendly Packaging: As sustainability demands rise, expect more innovations in biodegradable containers and optimized filling techniques to reduce waste.
Staying updated on these technological trends can provide a competitive edge, allowing you to produce high-quality products faster and with fewer resources.
Frequently Asked Questions (FAQs)
1. What’s the best filling machine for highly viscous liquids?
Piston fillers are often preferred for thick substances, though pump fillers with lobe or gear pumps can also handle viscous products effectively.
2. How do I minimize product waste during filling?
Regularly calibrate the machine, use anti-drip nozzles, and maintain a stable temperature for your product to reduce viscosity fluctuations.
3. Is an aseptic filling machine necessary for beverages like milk?
Yes, for products susceptible to bacterial contamination, aseptic filling is critical. This ensures long shelf life without preservatives.
4. Can one machine handle multiple product types?
Some versatile machines can be adapted for different viscosities and container sizes, but frequent changeovers and thorough cleaning will be required.
5. How frequently should I conduct a deep clean?
It varies by industry. Food and pharmaceutical lines often conduct weekly or monthly deep cleans, depending on the risk of contamination and product residue.
6. Is it possible to integrate a capping and labeling system with a single filling machine?
Absolutely. Many modern filling machines can integrate seamlessly with cappers, labelers, and case packers, forming a fully automated production line.
7. How do I ensure compliance with FDA or EFSA standards?
Invest in machines with sanitary designs, use approved materials (e.g., stainless steel for contact parts), maintain rigorous documentation, and follow good manufacturing practices.
Conclusion: Your Next Steps for Success
Liquid filling machines lie at the heart of countless industries—from beverages and cosmetics to pharmaceuticals and paints. Making the right choice isn’t just about buying a machine; it’s about optimizing your entire operation. By selecting the right type of filler (gravity, piston, pump, overflow, or aseptic), ensuring proper installation, and committing to ongoing maintenance, you can produce consistent, high-quality products that meet both consumer expectations and regulatory standards.
Remember the keywords: filling machine liquid is your gateway to faster, cleaner, and more precise packaging. Take a moment to evaluate your current setup. Are you constantly dealing with inconsistent fill volumes, frequent machine downtime, or excessive product waste? A well-chosen and well-maintained filling machine can solve these issues, boost your brand’s reputation, and enhance your bottom line.
If you found this guide helpful, feel free to share it with your network or comment below with your questions and experiences. Together, we can foster a community of best practices around liquid filling machines. For deeper insights, consider subscribing to our newsletter or reaching out for a customized consultation.
Stay Connected with EngiTech
EngiTech is your trusted source for in-depth knowledge on industrial mechanical engineering machines and technologies. Stay ahead with the latest innovations, expert insights, and practical guides designed to help you make informed decisions for your business and engineering needs. Join our growing community of professionals and industry leaders to stay updated and competitive in the ever-evolving world of industrial technology.