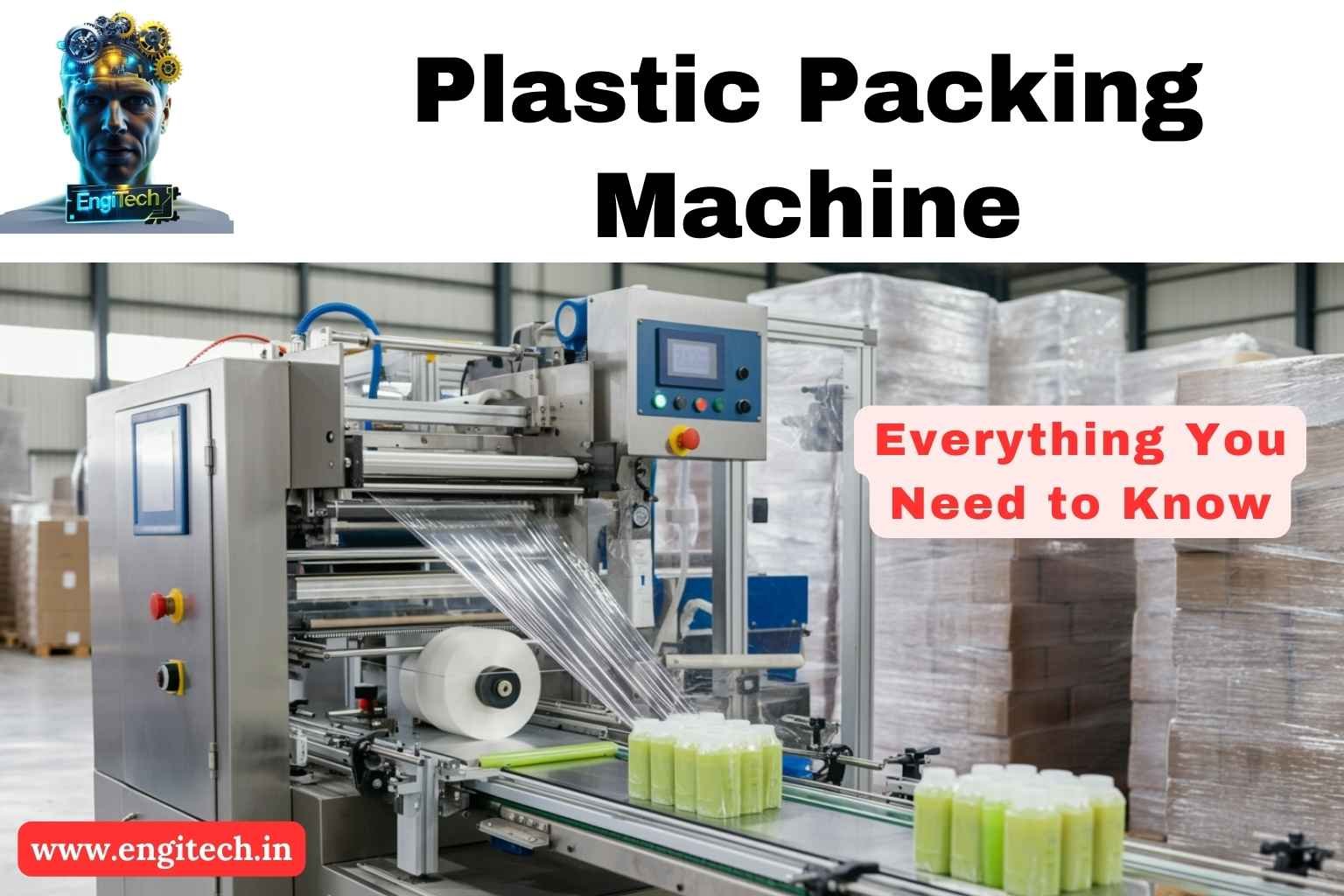
In today’s fast-paced manufacturing environment, plastic packing machines have become indispensable for businesses seeking efficiency, consistency, and durability in their packaging process. Whether you’re a startup exploring your first packaging line or an established company looking to upgrade existing equipment, this guide will walk you through the essentials of choosing and maintaining a plastic packing machine. By the end, you’ll understand not only how these systems improve your bottom line but also how they can enhance product safety, brand image, and sustainability.
In this in-depth post, we’ll cover real-world examples, expert insights, and step-by-step recommendations—all with the aim of helping you make informed decisions. Let’s dive right in.
Table of Contents
1. Understanding the Importance of Plastic Packing Machines
Plastic packaging is ubiquitous in modern commerce, playing a vital role in preserving product quality and facilitating safe transport. Here’s why plastic packing machines are so crucial:
- Product Protection: Plastic creates a barrier against moisture, contamination, and external impacts, ensuring products reach customers in pristine condition.
- Brand Consistency: Uniform packaging reflects professionalism and helps in brand recognition.
- Regulatory Compliance: Many industries—like pharmaceuticals and food—are bound by strict packaging standards. Automated equipment helps maintain compliance.
- Operational Efficiency: By automating repetitive tasks, companies save on labor costs and reduce human error.
Beyond these factors, plastic packing machines can significantly speed up production times, increasing output and boosting overall profitability. If your goal is to stay competitive in a crowded marketplace, upgrading or adopting a plastic packing machine is often a strategic move.
2. How Plastic Packing Machines Work
At their core, plastic packing machines function by automating the process of sealing products in plastic film or pouches. While the specifics vary depending on the model and application, the general workflow usually includes:
- Feeding Mechanism: Machines use either roll-fed plastic film or pre-formed pouches.
- Product Insertion: The item is placed—often via conveyor—into the plastic film or bag.
- Sealing & Cutting: High-temperature sealing bars fuse the plastic layers, creating airtight closures. After sealing, the film is cut to separate individual packages.
- Quality Check & Ejection: Advanced systems have sensors that detect sealing errors, label misalignments, and other defects, removing faulty packages automatically.
Some machines also integrate labeling and coding functionalities, which streamline the labeling process for traceability and brand identity. Advanced models include inline quality checks like weight measurement or X-ray inspection to ensure each packaged product meets safety and quality standards.
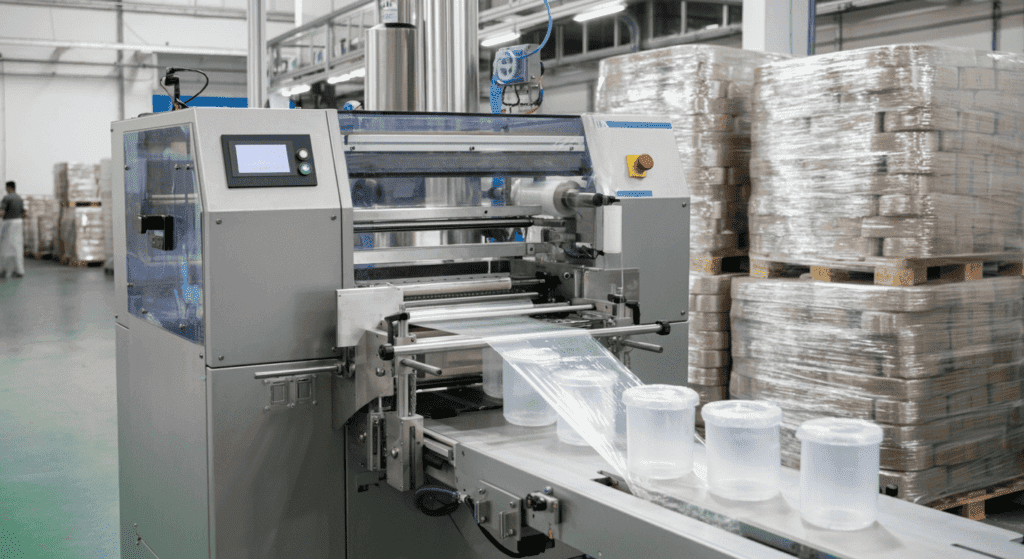
3. Key Components and Features to Consider
When you’re evaluating plastic packing machines, pay close attention to the following components and features, as they can heavily influence both cost and performance:
- Conveyor System:
- Belt Material: Needs to be resistant to chemicals and abrasion.
- Speed Control: Varying speeds can optimize production rates.
- Sealing Mechanism:
- Heat Seal Bars: Consistent temperature control ensures strong, uniform seals.
- Impulse Seal: An alternative sealing method that pulses heat, beneficial for certain plastic films.
- Control Panel & Automation:
- User Interface (UI): An intuitive touchscreen makes the system easy to program.
- Programmable Logic Controller (PLC): Offers customization for speed, seal temperature, and package length.
- Sensors & Safety Guards:
- Photoelectric Sensors: Detect product alignment.
- Safety Guards: Prevent accidents and shut down the machine if doors or panels are opened mid-operation.
- Additional Options:
- Vacuum & Gas Flush: Ideal for food packaging to prolong shelf life.
- Label Applicators & Printers: Integrate branding and compliance labels in one pass.
By scrutinizing these aspects, you can choose a machine that aligns with your production goals, budget, and quality control standards.
4. Types of Plastic Packing Machines
4.1 Vertical Form-Fill-Seal (VFFS) Machines
- Overview: These machines take a roll of plastic film, form a vertical pouch, fill it with the product (e.g., snacks, grains, powder), and then seal it.
- Best For: Industries where products are free-flowing or granular, such as snacks, cereals, and coffee beans.
- Key Benefit: High-speed operation with efficient material usage.
4.2 Horizontal Form-Fill-Seal (HFFS) Machines
- Overview: Plastic film is fed horizontally. The product is placed either manually or automatically onto the film, after which the machine seals it into individual packets.
- Best For: Biscuits, confectionery, and other products that lie flat or require specific orientation.
- Key Benefit: Ideal for delicate products, reducing the risk of damage during packaging.
4.3 Shrink Wrappers
- Overview: Used to wrap products in heat-sensitive film that tightens around the product when exposed to heat.
- Best For: Multipacks, bottled items, and irregularly shaped products.
- Key Benefit: Offers a tamper-evident seal and displays products attractively.
4.4 Vacuum Sealers
- Overview: These remove air from the package before sealing, extending product shelf life.
- Best For: Perishable goods such as meats, cheeses, and produce.
- Key Benefit: Prolongs freshness and reduces spoilage.
4.5 Blister & Skin Packaging Machines
- Overview: Products are placed on a rigid backing and sealed with transparent plastic, forming a protective shell.
- Best For: Electronics, hardware, and consumer goods that benefit from a see-through package.
- Key Benefit: High product visibility and strong protection against handling damage.
4.6 Stand-Up Pouch Machines
- Overview: The machine creates or fills stand-up pouches (often gusseted) with products, then seals them.
- Best For: Liquid or semi-liquid products such as sauces, soups, and beverages.
- Key Benefit: Attractive shelf presence and leak-proof packaging.
Each machine type caters to specific packaging needs, making it critical to match the machine to your product characteristics and industry requirements.
5. Advantages of Using Plastic Packing Machines
- Enhanced Productivity: Automated processes reduce manual labor and can often run continuously for high throughput.
- Cost Savings: While the initial investment may be high, automation lowers long-term labor costs and minimizes product waste.
- Improved Product Presentation: Consistent, high-quality seals and branding elements create a polished final product.
- Increased Safety & Hygiene: Eliminates direct human contact with products, mitigating the risk of contamination.
- Regulatory Compliance: Many machines can be fitted with monitoring features that record packaging conditions, assisting in audits and certifications.
By investing in a plastic packing machine, you not only streamline your operations but also position your brand as reliable and forward-thinking.
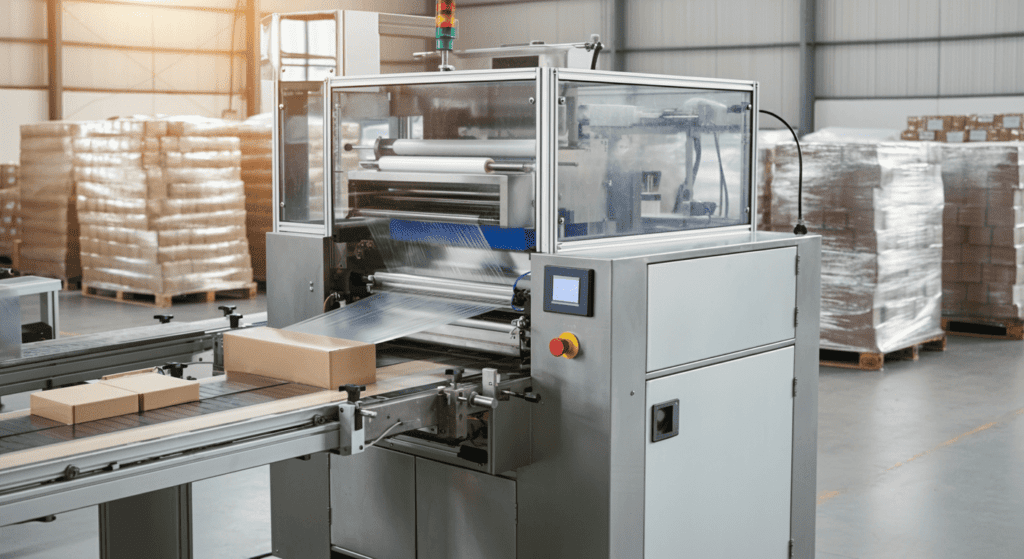
6. Common Challenges and How to Overcome Them
While plastic packing machines bring a host of benefits, it’s important to be aware of potential pitfalls:
- Film Tearing:
- Cause: Improper film tension or sealing temperature.
- Solution: Regularly calibrate the sealing bars and monitor tension settings.
- Seal Failure:
- Cause: Dirty sealing surfaces, inconsistent heat distribution.
- Solution: Clean sealing areas daily and use recommended temperature profiles for each plastic film.
- Jamming or Product Misalignment:
- Cause: Inaccurate conveyor speeds, blockages in feeding mechanisms.
- Solution: Adjust conveyor speeds and regularly remove debris.
- Machine Downtime:
- Cause: Insufficient maintenance, worn-out parts.
- Solution: Follow a preventive maintenance schedule and keep essential spare parts on hand.
By addressing these challenges proactively, you’ll maintain uptime, reduce operational costs, and ensure consistent quality.
7. How to Choose the Right Plastic Packing Machine
Selecting the perfect plastic packing machine can feel daunting. Here are the main criteria to guide your decision:
- Product Type & Volume:
- High-speed models are ideal for mass production, but may be overkill for smaller runs.
- Ensure the machine can handle your specific product size, weight, and shape.
- Budget & ROI:
- Factor in not just the price of the machine but also installation, training, and maintenance.
- Consider your ROI timeline—machines that run 24/7 offer faster payback.
- Scalability & Flexibility:
- Look for modular designs you can easily upgrade.
- If you anticipate adding new product lines, opt for a machine that accommodates diverse packaging formats.
- Integration with Existing Systems:
- Machines with standardized interfaces can integrate with your ERP or supply chain software.
- Consider the ease of adding feeders, labelers, or check-weighers.
- Vendor Reputation & Support:
- Read reviews, ask for client references, and check how responsive their customer service is.
- Ongoing support and training are crucial for smooth operations.
An informed choice sets the stage for increased productivity, fewer downtimes, and overall operational success.
8. Maintenance Tips for Longevity and Reliability
Plastic packing machines can be long-term investments. Here’s how to ensure they live up to their full potential:
- Daily Cleaning:
- Remove film residues and product spills.
- Clean sealing bars to prevent seal failures.
- Lubrication Schedule:
- Follow manufacturer guidelines for lubricating bearings, gears, and chains.
- Proper lubrication reduces friction and extends part life.
- Scheduled Inspections:
- Weekly checks for wear on belts, cutting knives, and seal bars.
- Monthly or quarterly reviews of electrical wiring and sensors.
- Spare Parts Inventory:
- Keep critical components like belts, sensors, and sealing bars on hand.
- Minimizes downtime when something eventually fails.
- Staff Training:
- Ensure operators understand correct machine settings and troubleshooting procedures.
- Properly trained staff are the first line of defense against breakdowns.
By making maintenance part of your daily routine, your machine will reward you with consistent performance and minimal unplanned downtime.
9. Cost Analysis: Balancing Upfront Investment and ROI
Buying a plastic packing machine is a significant expense, especially for small to mid-sized companies. However, when you factor in the long-term gains, the investment often pays for itself. Here’s a simplified breakdown:
- Upfront Costs:
- Machine purchase price
- Installation and setup fees
- Training for staff
- Operational Costs:
- Electricity consumption
- Maintenance and parts replacement
- Consumable packaging materials
- Return on Investment Factors:
- Increased production throughput
- Reduced labor costs
- Decreased product waste due to improved packaging consistency
- Enhanced brand reputation leading to higher sales
Many companies see a positive return within one to two years, particularly if their products are in high demand and the machine runs multiple shifts.
10. Sustainability and Eco-Friendly Packaging Practices
Plastic packaging has faced scrutiny for its environmental impact. Modern plastic packing machines are increasingly designed to accommodate eco-friendly packaging materials:
- Biodegradable Films:
- Machines can be modified to seal plant-based or compostable materials.
- Ideal for brands aiming to reduce their carbon footprint.
- Recyclable Plastics:
- Polyester (PET) and polyethylene (PE) films can often be recycled, provided they are separated from contaminants.
- Some suppliers offer films that include post-consumer recycled content.
- Reducing Material Waste:
- Automated tension and trimming controls minimize excess film usage.
- Inline quality checks catch errors early, reducing rework.
- Energy-Efficient Machinery:
- Advanced models feature energy-saving modes, automated shutdown, and improved insulation around heat seal bars.
By proactively embracing sustainability, you meet evolving consumer expectations and mitigate future regulatory compliance issues.
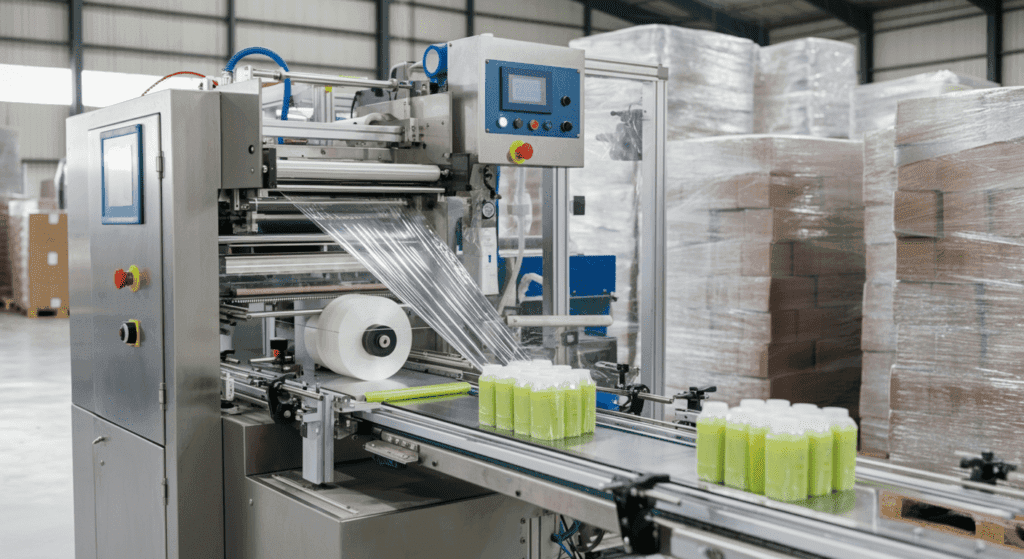
11. Case Studies: Real-World Success Stories
Case Study 1: High-Speed Snack Packaging
- Industry: Snack Foods
- Challenge: A medium-sized snack company struggled with manual bagging, leading to inconsistent sealing and high labor costs.
- Solution: They invested in a vertical form-fill-seal (VFFS) machine with advanced control features.
- Outcome: Production rates doubled within six months, packaging errors decreased by 40%, and the company recouped its investment in under two years.
Case Study 2: Expanding a Frozen Food Line
- Industry: Frozen Foods
- Challenge: Perishable products demanded secure, airtight packaging, and manual methods were slow and inconsistent.
- Solution: A combination of vacuum sealing and nitrogen flushing was integrated into an automated line.
- Outcome: Extended product shelf life by 30%, significantly reduced waste, and improved brand image for freshness and quality.
Case Study 3: Sustainable Coffee Packaging
- Industry: Specialty Coffee
- Challenge: A coffee roaster aimed to switch to biodegradable films without compromising quality.
- Solution: The roaster upgraded to an HFFS machine compatible with compostable materials.
- Outcome: Garnered positive customer feedback for eco-friendly practices, expanded distribution into eco-conscious retail chains, and increased market share.
These real-world examples underscore how plastic packing machines can revolutionize a packaging process, driving both operational efficiency and brand credibility.
12. Frequently Asked Questions (FAQ)
Q1: What is the average lifespan of a plastic packing machine?
The lifespan typically ranges from 7 to 15 years, depending on usage intensity and maintenance quality. Regular maintenance is the biggest factor in maximizing longevity.
Q2: Can plastic packing machines handle multiple product types?
Yes. Many machines are designed with modular features allowing quick changeovers between different products or packaging sizes. Always confirm compatibility with your supplier.
Q3: How do I know if I need a vertical or horizontal form-fill-seal machine?
- VFFS Machines: Ideal for free-flowing products like snacks or grains.
- HFFS Machines: Suited for products that need careful placement, like biscuits or items that lie flat.
Q4: Is it difficult to train staff to operate a plastic packing machine?
Most modern machines feature user-friendly touchscreens and straightforward interfaces. Training typically ranges from a few days to a couple of weeks, depending on the complexity of the system.
Q5: Are there financing or leasing options for acquiring these machines?
Yes. Many manufacturers and third-party finance companies offer leasing or payment plans, making it easier for businesses with limited capital to invest in automation.
Conclusion & Next Steps
Plastic packing machines have become an essential asset for companies looking to optimize their packaging processes. From protecting products and reducing waste to enhancing brand presentation and complying with regulatory standards, these machines offer a host of benefits that can significantly impact your bottom line. By carefully considering factors like product type, scalability, budget, and sustainability goals, you’ll be well-positioned to select the right equipment for your unique needs.
Key Takeaways
- Automating your packaging process increases efficiency and consistency.
- Maintenance and operator training are critical for reliability.
- Sustainability is no longer optional—choose eco-friendly films and energy-efficient models.
- The right machine not only boosts productivity but also elevates your brand’s market position.
Ready to take the next step? Whether you’re exploring a new venture or looking to replace an outdated system, investing in the right plastic packing machine can set you apart in a crowded marketplace. For more insights, check out our resource hub on packaging technologies, or reach out to our team of experts for personalized recommendations.
Stay Connected with EngiTech
EngiTech is your trusted source for in-depth knowledge on industrial mechanical engineering machines and technologies. Stay ahead with the latest innovations, expert insights, and practical guides designed to help you make informed decisions for your business and engineering needs. Join our growing community of professionals and industry leaders to stay updated and competitive in the ever-evolving world of industrial technology.