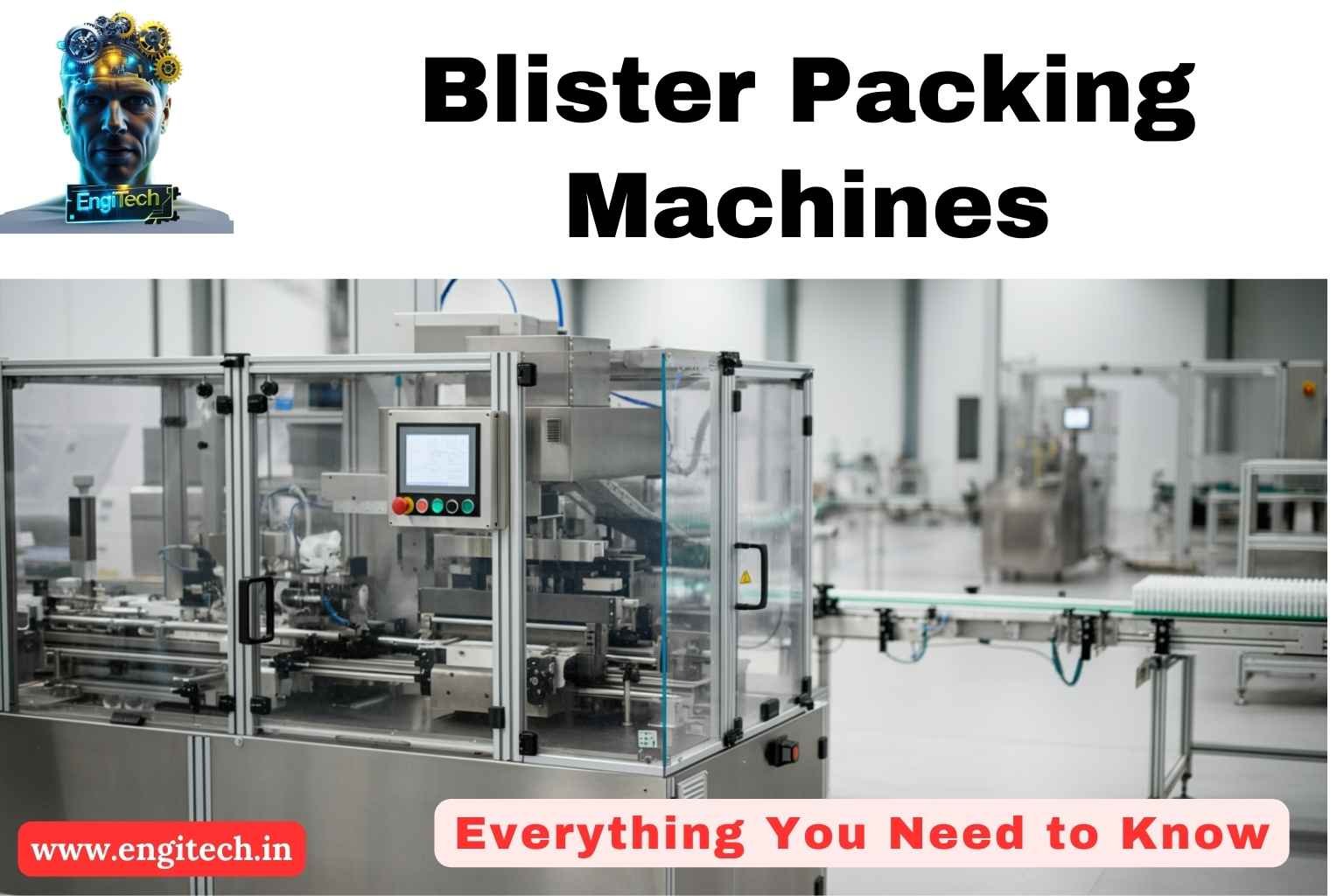
Blister packing machines have become a cornerstone in modern manufacturing, particularly in the pharmaceutical, food, and consumer goods industries. If you’re looking to improve product integrity, extend shelf life, and maintain stringent quality standards, a blister packing machine could be your ideal solution. In this comprehensive guide, we’ll take you through every aspect of these versatile machines—from how they work to best practices for maintenance and troubleshooting to how you can optimize your packaging line for maximum efficiency.
Whether you’re a seasoned packaging professional or exploring automation for the first time, this guide will help you make an informed decision. By the end, you’ll have a holistic understanding of blister packing machines, their components, their benefits, and the latest industry trends.
Table of Contents
1. What Is a Blister Packing Machine?
A blister packing machine is a specialized piece of equipment designed to package products—usually small consumer items, pharmaceuticals (like tablets or capsules), and certain food items—into a sealed cavity or pocket made from plastic or foil. This process protects the product from external factors like humidity, contamination, and physical damage, while also displaying the product in a user-friendly and tamper-evident format.
This packaging technique is widely popular because it combines efficiency, cost-effectiveness, and compliance with various regulatory standards. In industries where product safety and integrity are paramount, blister packing machines have become an indispensable part of the production line.
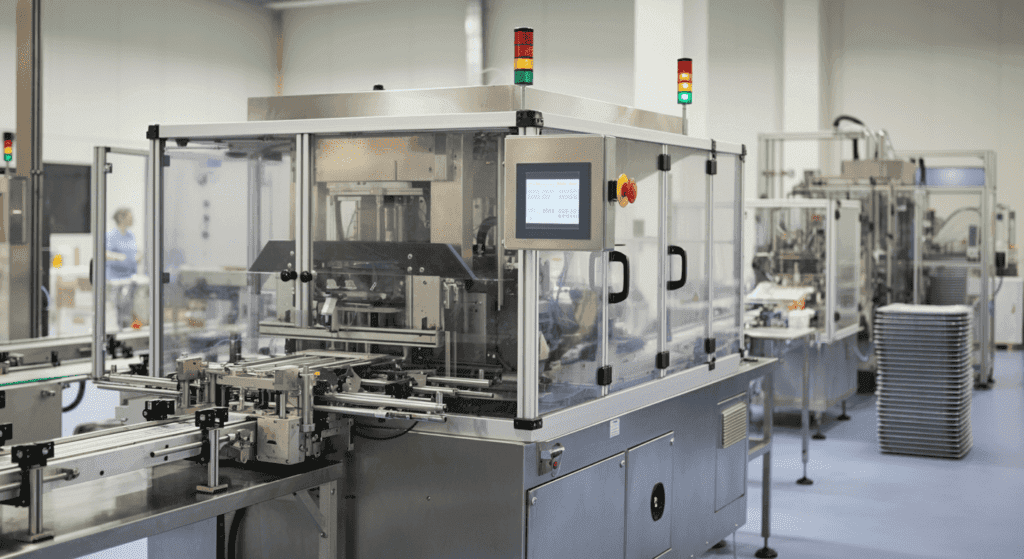
2. Why Blister Packaging Matters: Key Benefits
Blister packaging isn’t just about aesthetics or convenience; it delivers tangible benefits across different industries. Below are some core advantages:
- Product Protection
- Shields items from moisture, dust, and handling damage.
- Extends shelf life in pharmaceutical and food industries.
- Compliance and Traceability
- Offers tamper-evident seals and meets FDA and other global regulatory standards.
- Facilitates serialization and labeling for pharmaceuticals, enhancing traceability.
- Branding and Presentation
- Transparent plastic blister allows consumers to see the product, boosting trust.
- Customizable packaging materials support branding and promotional opportunities.
- Ease of Use
- Blister cards are lightweight, easily transportable, and often include perforations for single servings or doses.
- Customers find blister packs simpler to open and store compared to bulk packaging.
- Cost-Efficiency
- Automated processes reduce labor costs.
- Exact dosing or portion control limits product waste.
Blister packs offer a powerful combination of consumer appeal, product protection, and regulatory compliance. For businesses, they represent an all-in-one solution that can streamline packaging operations while enhancing brand image.
3. How Blister Packing Machines Work: The Basic Process
Though specific configurations vary, the fundamental blister packing process generally unfolds as follows:
- Material Feeding
- Plastic or foil material (thermoform or cold-form) feeds into the machine from a roll.
- The machine aligns these materials accurately to ensure uniformity.
- Forming
- The machine heats the plastic to a malleable state for thermoforming or presses the material into shape for cold forming.
- Molds create the cavities or “blisters.”
- Product Placement
- Products (tablets, capsules, consumer goods) are fed into the formed pockets either manually or via automatic feeders.
- Sealing
- A backing material—often foil or paper—covers the cavities.
- Heat (in thermoforming) or mechanical pressure (in cold forming) seals the backing material to the formed cavities, creating airtight or moisture-resistant chambers.
- Cutting and Trimming
- The machine cuts the continuous strip into individual packages or multi-product blister cards.
- Some machines include perforating units for easy separation of single doses or items.
- Quality Inspection
- Vision systems or manual checks verify seal integrity and product accuracy.
- Defective packs get rejected automatically.
- Discharge
- Finished blister packs exit the machine, ready for secondary packaging or direct shipment.
This automated sequence ensures high throughput, minimal manual handling, and consistent quality, making blister packing machines indispensable for high-volume production lines.
4. Types of Blister Packing Machines: Thermoforming vs. Cold Forming
Blister packing machines generally fall into two main categories: thermoforming and cold forming. Each has unique benefits and applications.
Thermoforming Blister Packing Machines
- Process: The plastic film is heated until it becomes pliable, then molded into shape.
- Applications: Widely used for pharmaceuticals (tablets, capsules), consumer goods (batteries, electronics), and food items.
- Advantages:
- Clear visibility of product.
- Usually faster throughput.
- Less material waste compared to cold forming.
- Limitations:
- Not suitable for highly light- or moisture-sensitive products if the plastic layer is not adequately protective.
Cold Forming Blister Packing Machines
- Process: The aluminum-based laminate is pressed into shape without the use of heat.
- Applications: Ideal for moisture- and light-sensitive products, like certain pharmaceutical tablets and capsules.
- Advantages:
- Excellent barrier against water vapor, oxygen, and UV light.
- Often used in high-end pharma products.
- Limitations:
- More expensive material costs.
- Opaque packaging (product is not visible).
- Slower line speed compared to thermoforming.
When selecting between thermoforming and cold forming, consider product sensitivity, material costs, and desired production speed. High-barrier protection is essential for pharmaceuticals with moisture or UV sensitivity, often making cold forming the preferred choice. Meanwhile, thermoforming is ideal for mass-market products where visibility and high throughput are priorities.
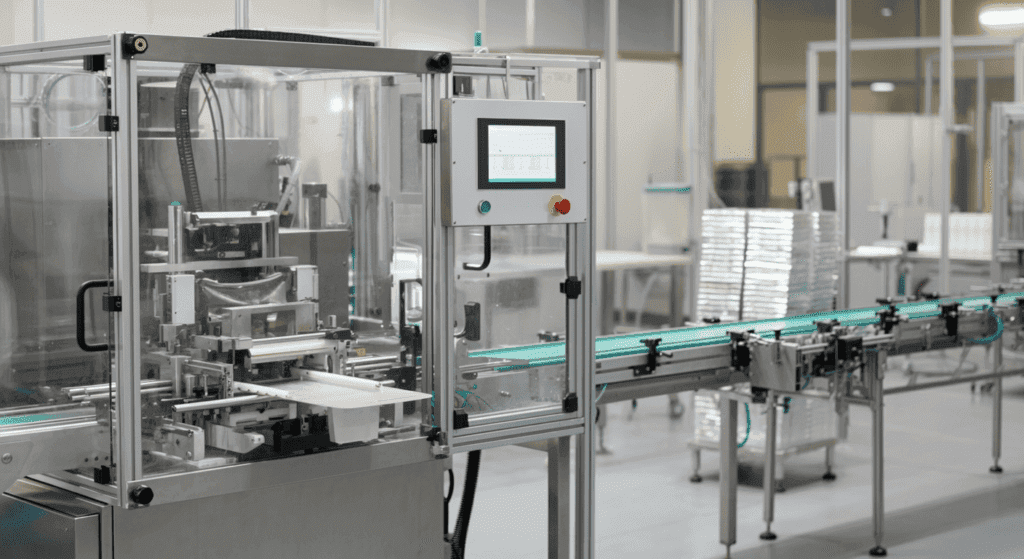
5. Primary Industries and Applications
While blister packing machines are frequently associated with the pharmaceutical sector, their versatility spans multiple industries:
- Pharmaceutical Industry
- Capsules, tablets, softgels, and even medical devices (e.g., syringes).
- Ensures dosage accuracy and extends shelf life.
- Food & Nutrition
- Confectioneries, gum, nutraceutical supplements.
- Portion control and protective sealing against moisture.
- Consumer Electronics & Hardware
- Batteries, small electronic components, USBs.
- Tamper-evident packaging and secure display.
- Cosmetics & Personal Care
- Single-use facial masks, sample sachets, small beauty tools.
- Enhanced branding and consumer convenience.
- Automotive & Industrial
- Small spare parts, fuses, screws, and bolts.
- Ease of organization and reduced risk of contamination.
In virtually any domain that demands product protection, portion control, or strong brand presentation, blister packing machines can offer a significant value-add.
6. Key Components and Functionality
Despite variations across models and manufacturers, most blister packing machines share these core components:
- Feeding Rollers
- Guide the plastic or foil material into the machine.
- Maintain consistent tension to prevent tearing or misalignment.
- Forming Station
- Heats (thermoforming) or presses (cold forming) material into blister pockets.
- Precise temperature and pressure control are crucial for consistent quality.
- Product Feeding System
- Tablets or other items are placed into the formed pockets through automated feeders, robotic arms, or manual loading.
- Advanced sensors ensure correct product count and positioning.
- Sealing Station
- Adheres lidding material to blister cavities with heat or pressure.
- Regulated temperature and sealing time help achieve hermetic or moisture-resistant seals.
- Cutting and Trimming Unit
- Shapes the continuous web into individual blister packs or strips.
- Optional perforating tools allow for multi-pack configurations.
- Reject Mechanism
- Removes faulty blisters or misfeeds from the line.
- Often integrated with camera-based inspection systems.
- Control Panel / PLC System
- Operators can adjust speed, temperature, pressure, and other variables.
- Modern machines often feature touchscreen interfaces and can store multiple production recipes.
- Safety Enclosures
- Guard doors and sensors help prevent accidents.
- Essential for compliance with workplace safety regulations.
Understanding these components helps you evaluate machine features and capabilities more effectively, ensuring you invest in equipment that aligns with your production goals.
7. How to Choose the Right Blister Packing Machine
Selecting an optimal blister packing machine can be a game-changer for your manufacturing line. Here are essential considerations:
- Production Volume
- Calculate your daily, weekly, or monthly output requirements.
- Look for machines with suitable speed (cycles per minute) and capacity.
- Product Sensitivity
- Moisture- or UV-sensitive items may necessitate cold forming.
- For general consumer goods, thermoforming usually suffices.
- Material Compatibility
- Check if the machine can handle various films like PVC, PVDC, Alu-Alu.
- Multilayer laminates may require specialized forming stations.
- Automation Level
- Determine if you need semi-automatic or fully automated lines with robotic feeders.
- Factor in workforce costs and floor space.
- Regulatory Compliance
- For pharmaceuticals, ensure the machine meets GMP and FDA guidelines.
- Verify if specialized features like batch coding or serialization are included.
- Customization and Flexibility
- Look for adjustable forming depth, seal size, and tooling options.
- This flexibility allows you to package different products on one machine.
- Service and Support
- Does the manufacturer provide training, spare parts, and technical assistance?
- Quick turnaround on maintenance can minimize downtime.
- Budget
- Balance immediate costs with long-term operational savings.
- A higher initial investment in a robust machine often leads to better ROI through reduced waste and downtime.
Begin your search by identifying your core priorities—speed, compliance, automation, or budget. Then, match those with manufacturers or suppliers who have a proven track record in your industry.
8. Best Practices for Maintenance, Care, and Safety
A well-maintained blister packing machine offers reliable performance, fewer breakdowns, and longer service life. Below are proven strategies for keeping your equipment in peak condition:
- Scheduled Inspections
- Conduct regular check-ups for wear-and-tear on heating elements, sealing jaws, and feeding systems.
- Follow the manufacturer’s recommended maintenance interval.
- Lubrication and Cleaning
- Keep moving parts lubricated to reduce friction and avoid overheating.
- Clean sealing surfaces and cutters daily to prevent residue buildup that can compromise seal integrity.
- Calibration
- Periodically calibrate temperature sensors and pressure gauges.
- Even slight deviations can lead to defective seals or forming issues.
- Training
- Ensure all operators receive proper training on running, cleaning, and troubleshooting the machine.
- Knowledgeable staff can quickly spot and resolve minor issues before they escalate.
- Use Genuine Spare Parts
- Rely on authorized parts to maintain machine specifications and safety standards.
- Counterfeit parts can shorten machine life and compromise safety.
- Safety Checks
- Verify that guard doors, emergency stop buttons, and light curtains are functional.
- Document and promptly address any observed hazards.
- Data Logging and Analytics
- Advanced machines allow for real-time performance tracking.
- Use these insights to optimize settings and anticipate maintenance needs.
By integrating these best practices into your daily, weekly, and monthly routines, you not only prolong your machine’s lifespan but also minimize costly downtime and potential safety risks.
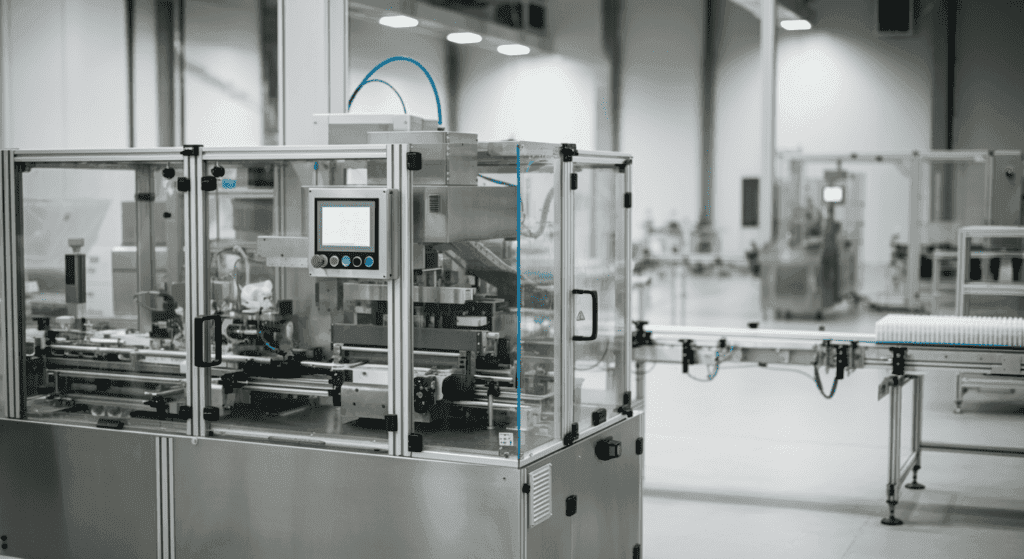
9. Troubleshooting Common Issues
Even the most advanced blister packing machines encounter occasional hiccups. Here’s a quick guide to diagnosing and resolving frequent problems:
- Poor Seal Integrity
- Cause: Incorrect temperature, insufficient pressure, dirty sealing jaws.
- Solution: Clean jaws, calibrate temperature settings, check seal alignment.
- Blister Deformation or Wrinkles
- Cause: Overheating or uneven temperature distribution.
- Solution: Adjust heater settings, ensure uniform pressure during the forming stage.
- Misalignment in Product Placement
- Cause: Faulty feeding mechanism, inconsistent product sizes, or sensor failure.
- Solution: Inspect feeder, recalibrate sensors, confirm product dimensions match machine specs.
- Material Jams
- Cause: Incorrect film tension, debris in feeding rollers.
- Solution: Clear debris, fine-tune tension settings, ensure the film roll is not damaged.
- Excessive Material Waste
- Cause: Improper cutting alignment, inefficient forming layouts.
- Solution: Adjust die-cut settings, explore alternative tooling for better space utilization.
- Machine Overheating or Frequent Shutdowns
- Cause: Lack of lubrication, overuse without breaks, malfunctioning cooling systems.
- Solution: Improve ventilation, schedule downtime for cooling, perform routine lubrication.
A systematic approach to troubleshooting—root cause analysis followed by corrective action—helps maintain high efficiency and reduces production losses.
10. Future Trends in Blister Packaging and Machine Technology
The blister packaging landscape continues to evolve with technological advancements and changing consumer demands. Key future trends include:
- Smart Packaging
- Integration of NFC (Near Field Communication) tags or QR codes to track product authenticity and provide user information.
- Potential for real-time temperature and humidity monitoring.
- Sustainable Materials
- Growing shift toward recyclable or biodegradable films.
- Ongoing R&D in plant-based polymers to reduce environmental impact.
- Industry 4.0 and IIoT (Industrial Internet of Things)
- Machines equipped with sensors for predictive maintenance and performance analytics.
- Cloud-based dashboards allow remote monitoring and instant adjustments.
- Robotic Integration
- Automated picking and placing robots can handle complex shapes and high-speed tasks.
- Reduced labor costs and higher accuracy.
- Customization and On-Demand Production
- Modular designs allow quick tooling changes for different blister sizes or product lines.
- Suited for short runs or fast-changing consumer trends.
Staying ahead of these developments can give you a competitive edge, allowing your packaging line to adapt quickly to market demands and regulatory shifts.
11. FAQs: Your Blister Packing Machine Questions Answered
Q1. What types of films are compatible with most blister packing machines?
Most standard blister packing machines handle PVC, PVDC, and aluminum foil (for cold forming). Some advanced models also accommodate multi-layer laminates or eco-friendly materials, depending on your specific product requirements.
Q2. Can one blister packing machine handle multiple product shapes and sizes?
Yes. Many machines come with modular or easily switchable tooling. You can often adjust cavity depth, seal area, and form size to accommodate different products, although more complex shapes may require specialized tooling.
Q3. How do I ensure my blister packing process meets FDA or GMP standards?
Focus on hygiene, traceability, and quality control:
- Maintain a clean environment and regular machine cleaning schedule.
- Integrate vision systems to detect product or seal defects.
- Keep detailed documentation for batch numbers, material sources, and production runs.
Q4. What is the average lifespan of a blister packing machine?
A well-maintained machine can operate effectively for 10+ years. Regular maintenance, timely part replacements, and operator training significantly extend service life.
Q5. How can I reduce material waste?
Optimizing your die layouts, ensuring correct film tension, and reducing line speed during problematic runs are effective strategies. Continuous data monitoring can also highlight inefficiencies and areas for improvement.
Conclusion & Next Steps
Blister packing machines represent a powerful, versatile, and efficient way to package products ranging from pharmaceutical tablets to small consumer electronics. By offering robust product protection, user-friendly portioning, and regulatory compliance, blister packaging has become a go-to solution for manufacturers worldwide. When properly maintained, these machines deliver consistent output, high-quality seals, and minimal downtime—vital components for a profitable production line.
As you evaluate your packaging options, consider your specific product sensitivities, desired output volume, and regulatory demands. Invest in a machine that offers the right balance of speed, adaptability, and material compatibility. Once you’ve implemented a blister packing system, remember that routine maintenance, operator training, and regular process optimization are the keys to long-term success.
Ready to transform your packaging line? Explore our in-depth resources on packaging automation or contact our team to discuss tailored solutions. Whether you’re upgrading existing equipment or building a new facility, our experts can guide you every step of the way. Don’t forget to share this article with colleagues or on social media to help others discover the benefits of blister packing machines.
Stay Connected with EngiTech
EngiTech is your trusted source for in-depth knowledge on industrial mechanical engineering machines and technologies. Stay ahead with the latest innovations, expert insights, and practical guides designed to help you make informed decisions for your business and engineering needs. Join our growing community of professionals and industry leaders to stay updated and competitive in the ever-evolving world of industrial technology.