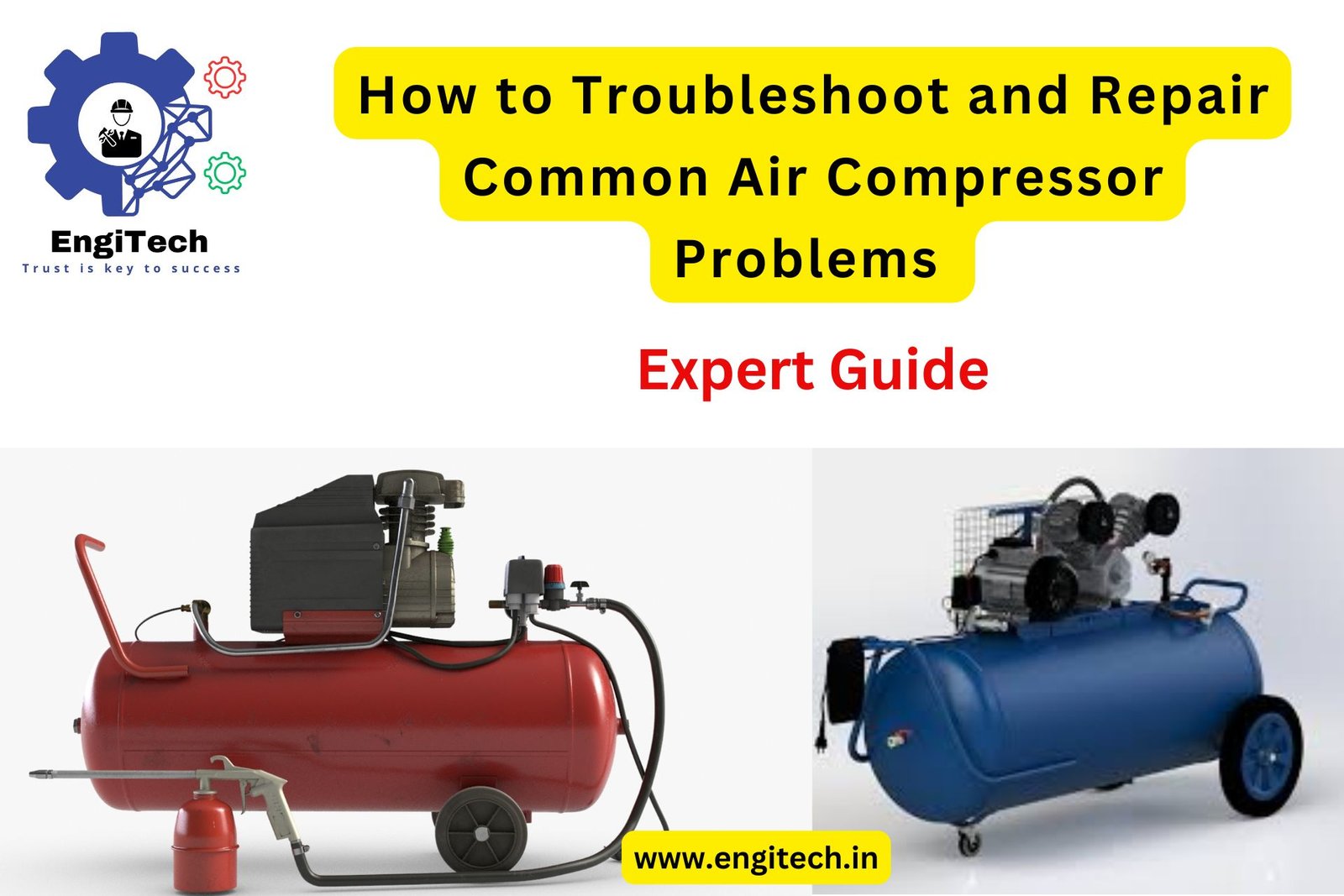
Air compressors are robust, hardworking machines found in countless industries, from manufacturing to automotive repairs. However, like any mechanical equipment, they can encounter issues that impact their performance and reliability. A sudden breakdown can disrupt operations, cause delays, and result in costly repairs if not handled promptly.
Troubleshooting and repairing air compressor problems doesn’t have to be overwhelming. With the right knowledge and approach, you can quickly identify and address common issues, saving time and money. This detailed guide covers everything from simple troubleshooting tips to advanced repair strategies, ensuring that you can confidently maintain your air compressor and keep it running at peak performance.
Table of Contents
1. Why Air Compressors Fail: Common Causes
Understanding why air compressors fail is the first step in troubleshooting and repairs. Here are some of the most common causes of compressor issues:
1.1 Overheating
Overheating is one of the leading causes of air compressor failure. When compressors overheat, they can suffer from premature wear and reduced efficiency. Possible reasons include:
- Insufficient ventilation around the compressor.
- Low oil levels or poor-quality oil causing friction.
- Clogged filters that restrict airflow.
1.2 Air Leaks
Leaks are another frequent issue in air compressor systems, leading to a loss of air pressure and inefficient operation. Common leak points include:
- Hoses and connections that become cracked or loose.
- Worn-out seals and gaskets.
- Faulty valves or couplings.
1.3 Electrical Failures
Electrical components like motors, switches, and circuit breakers can fail due to:
- Overloading the system beyond its capacity.
- Wiring issues that cause short circuits or poor connections.
- Burnt-out fuses or malfunctioning pressure switches.
1.4 Low Pressure
Low pressure can result from several issues, including:
- Faulty pressure regulators.
- Clogged intake filters.
- Broken unloader valves that prevent the compressor from building pressure.
2. How to Troubleshoot Air Compressor Problems
Troubleshooting air compressor problems is a step-by-step process that helps you identify the root cause of the issue. Below are some troubleshooting strategies for common air compressor problems:
2.1 Checking for Air Leaks
Leaks are one of the most common issues that reduce efficiency in an air compressor system. To check for leaks:
- Turn off the compressor and depressurize the system.
- Inspect all connections for visible cracks or damage. Focus on hose connections, fittings, and air valves.
- Use soapy water to spray on hoses, pipes, and connections. If you see bubbles forming, you’ve found a leak.
- Tighten or replace damaged parts as necessary.
2.2 Inspecting the Oil Level
Low oil levels can cause overheating and increase wear on internal components. To check the oil level:
- Locate the oil dipstick (for lubricated compressors).
- Remove the dipstick and wipe it clean.
- Reinsert the dipstick and remove it again to check the oil level.
- If the oil is low, top it off with the recommended compressor oil. If it’s dirty, consider changing the oil completely.
2.3 Evaluating the Pressure
If your compressor is not reaching the desired pressure levels, follow these steps:
- Check the pressure gauge for accuracy.
- Inspect the pressure switch for any malfunctions. This switch controls when the compressor cycles on and off.
- Examine the intake filter for blockages. Dirty filters restrict airflow and can cause low pressure.
- Check the unloader valve, which may be stuck in the open position, preventing the compressor from building pressure.
3. Common Air Compressor Problems and Solutions
Here are detailed solutions for some of the most frequent air compressor issues:
3.1 Air Compressor Won’t Start
If your compressor doesn’t start, it could be due to electrical issues or mechanical failures. To address this problem:
- Check the power supply and ensure the compressor is plugged in properly.
- Inspect the circuit breaker to see if it has been tripped. Reset it if necessary.
- Test the pressure switch and pressure gauge to ensure they are functioning correctly.
- If the motor doesn’t run even when power is supplied, inspect the motor starter or capacitor for signs of failure.
3.2 Air Compressor Is Too Noisy
Excessive noise from an air compressor can be alarming. Here’s how to fix it:
- Check for loose parts like bolts, screws, and connections that may cause vibrations.
- Inspect the motor and pump for wear or damage. Worn-out components can cause increased noise levels.
- Examine the compressor’s mounting pads for wear. Install vibration-damping pads if necessary.
- Lubricate moving parts as needed to reduce friction and noise.
3.3 Air Compressor Loses Pressure
A drop in pressure can lead to ineffective tool operation. Here’s how to resolve this:
- Inspect the air filter for dirt and debris that may be clogging it. Clean or replace it if necessary.
- Check the hose and fittings for leaks. Even small leaks can cause significant pressure loss.
- Test the unloader valve to ensure it’s closing correctly. A malfunctioning valve can lead to pressure loss.
- Inspect the compressor’s check valve for any blockages or damage.
3.4 Compressor Is Overheating
Overheating is a serious issue that can cause long-term damage to your compressor. To prevent overheating:
- Ensure proper ventilation around the compressor. Excessive heat can accumulate if the unit is in a poorly ventilated area.
- Check the oil levels and ensure the oil is clean. Replace the oil if it appears dark or dirty.
- Clean the air filter to allow proper airflow, which is critical for cooling the compressor.
- Check the cooling fan (if applicable) to ensure it is functioning properly.
4. How to Perform Basic Air Compressor Repairs
For some issues, basic repairs can be done by yourself without the need for a professional. Here’s how to perform basic air compressor repairs:
4.1 Replacing the Air Filter
A clogged air filter can cause reduced airflow and inefficient operation. To replace it:
- Turn off the compressor and unplug it from the power supply.
- Locate the air filter and remove it from its housing.
- Insert the new filter, ensuring it is properly seated.
- Reassemble the compressor and check that the filter is secure.
4.2 Replacing the Pressure Switch
If the pressure switch is malfunctioning, it will prevent the compressor from turning on or off. To replace it:
- Unplug the compressor and relieve the pressure from the system.
- Disconnect the wires from the old pressure switch.
- Remove the pressure switch from its housing and install the new one.
- Reconnect the wires and test the system to ensure proper operation.
4.3 Changing the Oil
If the oil is dirty or low, it’s important to change it regularly. To change the oil:
- Turn off and unplug the compressor.
- Locate the oil drain valve and place a container underneath.
- Open the drain valve and allow the old oil to fully drain.
- Close the valve, refill with the appropriate oil, and check the oil level.
5. When to Call a Professional
While many air compressor issues can be fixed with basic troubleshooting and repairs, some problems may require professional intervention. Call a technician if:
- The motor or compressor pump is damaged beyond repair.
- You are unable to identify the root cause of the problem.
- Complex electrical issues are involved.
- Your compressor is still under warranty, and repairs may be covered.
FAQs About Air Compressor Troubleshooting and Repairs
1. How do I know if my air compressor is overheating?
Overheating in an air compressor is usually accompanied by hot air blowing from the unit, excessive noise, and a sharp drop in performance. If your compressor feels unusually hot to the touch or shuts off unexpectedly, it might be overheating. Common causes include insufficient ventilation, low oil levels, or clogged filters. To prevent overheating, ensure proper airflow around the compressor, check and replace filters, and monitor oil levels regularly.
2. What causes an air compressor to lose pressure?
Air compressor pressure loss can be caused by several issues, including air leaks, clogged air filters, or a faulty pressure switch. Leaks in the hose, couplings, or seals are the most common culprits. Inspect all components for visible damage or loose connections. If the problem persists, check the intake filter for blockages and replace it if necessary. A malfunctioning unloader valve can also lead to pressure loss.
3. How do I repair an air compressor that won’t start?
If your air compressor won’t start, first check if it’s properly plugged in and the circuit breaker hasn’t tripped. Inspect the power switch and ensure the compressor is receiving electricity. If the compressor still doesn’t start, it might be due to a faulty motor or capacitor. Test the motor starter and capacitor for any signs of failure, and replace them if necessary. If you’re unsure, it’s best to consult a professional.
4. Can I fix an air compressor leak myself?
Yes, you can repair small air compressor leaks yourself. First, turn off the compressor and depressurize the system. Inspect all hoses, fittings, and valves for visible damage. Tighten any loose connections and replace worn-out seals, O-rings, or gaskets. If the leak is large or in a hard-to-reach area, you may need to call a professional technician for assistance.
5. How often should I perform maintenance on my air compressor?
Routine maintenance is crucial to keep your air compressor running efficiently. It’s recommended to perform basic maintenance tasks such as checking oil levels, inspecting filters, and tightening fittings every 1-3 months, depending on usage. Additionally, change the oil every 500-1,000 operating hours or as specified in the manufacturer’s manual. Keep an eye on the air filter and replace it when it’s clogged or dirty. Regular maintenance can help prevent breakdowns and extend the lifespan of your compressor.
Conclusion
Regular maintenance and quick troubleshooting are key to ensuring your air compressor runs smoothly. By understanding the most common issues and knowing how to address them, you can prevent downtime and extend the lifespan of your compressor. Remember, while simple repairs can often be done yourself, never hesitate to consult a professional for more complex issues. With these tips and strategies, you can keep your air compressor in optimal condition and avoid costly repairs down the road.
For more expert tips on air compressors and other industrial machinery, explore more resources on EngiTech and stay updated on the latest innovations in industrial technologies.