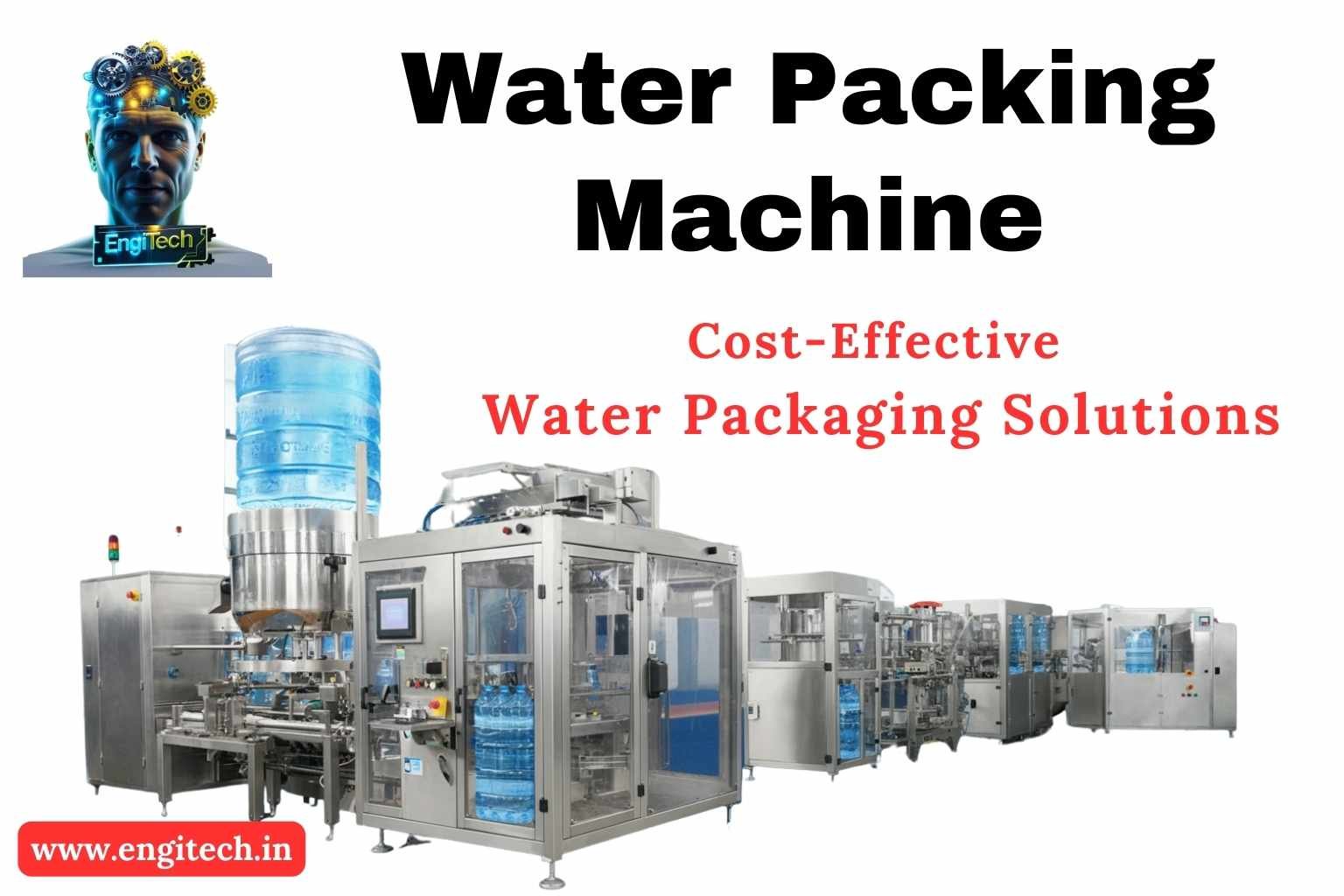
Clean, potable water is one of our most basic necessities, yet delivering it safely and efficiently remains a challenging task for many businesses and communities worldwide. Whether you’re a budding entrepreneur entering the beverage industry or an established water purification company seeking to expand, investing in the right water packing machine can make all the difference.
In today’s market, customers expect hygienic, tamper-proof, and well-branded water packaging that instills confidence in your product. From large-scale bottled water lines to compact, automatic water packing machines designed for small operations, there are countless ways to streamline your water packaging processes and meet stringent regulatory requirements.
In this comprehensive guide, we’ll explore the ins and outs of selecting, operating, and maintaining a water packing machine. We’ll also discuss the latest trends, answer common questions, and provide real-world tips so you can reduce downtime, cut costs, and provide safe drinking water in a manner that truly stands out. By the end of this article, you’ll have a clear roadmap for finding the best water packing machine for your unique needs and ensuring that each drop you package meets the highest standards of quality.
Table of Contents
1. Understanding the Importance of Water Packaging
Packaging water may appear straightforward at first glance: fill a container, seal it, and distribute to consumers. However, the process behind the scenes is far more complex—and crucial—than people often realize. Water is not just another beverage; it is an essential resource that people trust to be pure and safe. Any contamination, inefficiency, or poor packaging can lead to serious health concerns and tarnish a brand’s reputation almost immediately.
A water packing machine addresses many pain points by automating processes, reducing human contact, improving hygiene, and enabling consistent packaging quality. Beyond mere convenience, here are a few reasons why water packaging is of paramount importance:
- Safety and Hygiene: Proper packaging prevents bacterial contamination, protects the water from external pollutants, and ensures consumers receive water that meets (or exceeds) safety standards.
- Shelf Life: High-quality, tamper-resistant packaging extends shelf life and preserves the product’s taste and purity.
- Brand Identity: Customized packaging with clear labels, unique shapes, and eye-catching design elements can help distinguish your product in a crowded market.
- Consumer Confidence: A well-sealed, tamper-proof bottle or pouch instills trust. People want to be certain that the water they drink is free from contaminants and has undergone rigorous quality control.
By recognizing the critical role packaging plays in consumer safety and brand positioning, you’ll have a deeper appreciation for investing in the right water packing machine.
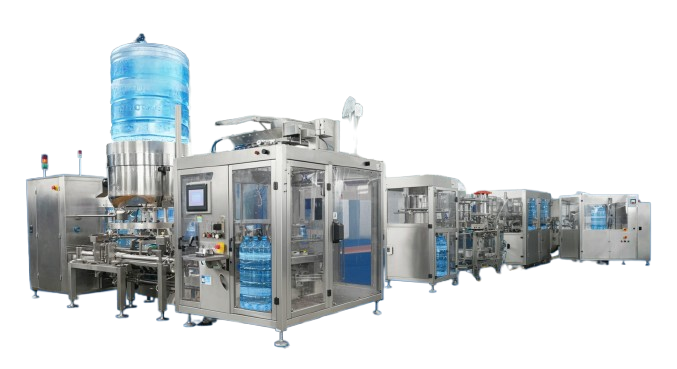
2. Overview of Water Packing Machines
A water packing machine is a specialized piece of equipment designed to automate and streamline the process of filling and sealing containers—bottles, pouches, cups, or jars—with clean water. This machinery is engineered for precision, hygiene, and efficiency, and can accommodate varying production scales, from small local bottlers to massive industrial facilities.
Core Functions of a Water Packing Machine
- Filling
The machine measures and dispenses precise quantities of water into containers. This automated approach helps maintain product consistency, minimizing both overfill and underfill. - Sealing
Once filled, containers are sealed securely—often via capping, heat-sealing, or other tamper-resistant methods—to protect against leakage and contamination. - Labeling and Coding
Many modern machines offer integrated labeling and date coding functionalities, ensuring compliance with regulatory requirements for traceability and branding. - Sterilization and Hygiene
High-end water packing machines often include sterilization features such as UV lamps or ozone treatments that keep water and containers free from microbial contamination.
Who Uses Water Packing Machines?
- Bottled Water Companies: Large-scale facilities producing thousands (or millions) of bottled units daily.
- Small-Scale Enterprises: Local businesses that offer purified drinking water to neighboring communities.
- Disaster Relief Organizations: Quick and reliable access to safe water is vital, especially in crisis scenarios.
- Food & Beverage Conglomerates: Entities that offer multiple product lines, including bottled water, juices, and other beverages requiring sterile filling.
Whether you’re aiming for 500 bottles an hour or 50,000 bottles a day, there’s a water packing machine configuration suited to your production scale and budget.
3. Types of Water Packing Machines
Not all water packing machines are created equal. Each type has unique advantages, limitations, and use cases. Understanding these differences is key to making an informed purchase.
3.1 Automatic Water Packing Machines
- What They Are: Fully automated systems that handle everything from container feeding to labeling, sealing, and discharge.
- Why They Matter: Ideal for medium to large operations aiming to reduce labor costs and human error.
- Benefits:
- High throughput and efficiency.
- Consistent filling accuracy.
- Minimal manual intervention needed.
3.2 Semi-Automatic Water Packing Machines
- What They Are: Combine manual and automated processes—operators may place containers on the machine, and the machine handles filling and sealing.
- Why They Matter: Excellent for businesses transitioning from purely manual operations to full automation, or for companies that produce smaller batches.
- Benefits:
- Lower initial investment compared to full automation.
- Flexible operation, balancing efficiency with human oversight.
3.3 Manual Water Packing Machines
- What They Are: Heavily dependent on human labor for filling and sealing, often used in low-volume contexts.
- Why They Matter: Suitable for micro-entrepreneurs who are starting on a shoestring budget or operating in remote areas with minimal resources.
- Benefits:
- Lowest capital cost.
- Straightforward to operate; minimal technical expertise required.
3.4 Pouch Filling Machines
- What They Are: Specialized systems for filling water into pouches (sometimes called sachets) instead of bottles.
- Why They Matter: Common in regions where bottled water is cost-prohibitive or where flexible packaging is preferred for transport and storage.
- Benefits:
- Lightweight, compact packaging.
- Often lower packaging costs.
- Reduced plastic usage in some designs.
3.5 Cup Filling and Sealing Machines
- What They Are: Designed for dispensing water into individual cups with heat-sealed lids—popular in hospitality, airlines, and events.
- Why They Matter: Convenient for single-serving water portions, reducing waste and spillage.
- Benefits:
- Streamlined for on-the-go consumption.
- Good branding opportunities on the lid.
Selecting the right machine type depends on your production requirements, budget, market preferences, and the form factor you want to offer (bottles vs. pouches vs. cups).
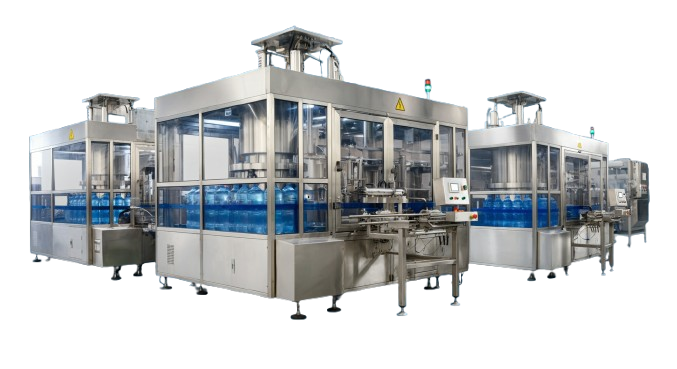
4. Key Factors to Consider Before Purchasing
Purchasing a water packing machine is not a trivial decision. It’s a significant capital investment that impacts the efficiency, reputation, and profitability of your operation. Below are some crucial considerations:
- Production Capacity
- Ask Yourself: How many units per hour do I need to produce to meet demand without overextending?
- Why It Matters: Overestimating capacity leads to wasted resources, while underestimating capacity can stunt growth and cause stock shortages.
- Level of Automation
- Ask Yourself: Do I want fully automated, semi-automated, or manual processes?
- Why It Matters: Higher automation typically means lower labor costs but increased upfront costs and potentially more complex maintenance.
- Type of Packaging
- Ask Yourself: Bottles, pouches, cups, or something else?
- Why It Matters: Different packaging types cater to different consumer preferences and logistical constraints.
- Budget Constraints
- Ask Yourself: What’s my total budget for purchase, installation, and maintenance?
- Why It Matters: The true cost extends beyond the machine’s purchase price. Factor in installation, operator training, parts, and possible upgrades.
- Available Space
- Ask Yourself: How much floor space do I have in my facility?
- Why It Matters: Large-scale machines demand ample room, as well as considerations for material handling and operator movement.
- Regulatory Compliance
- Ask Yourself: Which local or international safety and hygiene standards must I meet?
- Why It Matters: Non-compliance can result in heavy fines, product recalls, or even the shutdown of your operation.
- Machine Brand Reputation and Support
- Ask Yourself: Does the manufacturer provide reliable after-sales service, spare parts availability, and technical support?
- Why It Matters: Post-purchase support can significantly influence your machine’s long-term performance and ROI.
- Potential for Expansion
- Ask Yourself: Am I planning to scale up production in the near future?
- Why It Matters: Buying a machine you outgrow too quickly can be a costly mistake. Invest in machinery that can adapt or expand as your business evolves.
Spending time on thorough research and due diligence will help you find a machine that aligns with your goals and proves cost-effective in the long run.
5. Step-by-Step Setup Process
Once you’ve chosen a water packing machine, the real work of setting it up to function optimally begins. Here’s a simplified, step-by-step look at what the process typically involves:
- Pre-Installation Preparation
- Inspect your facility’s layout and determine the best location for the machine. Consider water supply lines, electrical connections, drainage, and ventilation.
- Ensure that your floor can handle the machine’s weight and any additional load from water storage.
- Unboxing and Assembly
- Carefully uncrate the machine following the manufacturer’s guidelines.
- Assemble any external components like conveyor belts, filling heads, or sealing stations under the supervision of a qualified technician.
- Water and Utility Connections
- Connect the machine to a secure and potable water source.
- Double-check for leaks or pressure inconsistencies that could affect performance.
- Hook up necessary utilities, including electrical power, compressed air (if needed), and drainage.
- Sterilization and Line Flushing
- Clean and sterilize all contact surfaces before running your first batch.
- Flush the lines with disinfectant or any recommended cleaning solution to eliminate residual debris or microorganisms.
- Initial Test Run
- Conduct a dry run (no water) to confirm that the belts, motors, and other mechanical parts function without issues.
- Move on to a wet run with water containers to gauge filling accuracy, sealing performance, and the overall flow.
- Adjust settings (filling levels, temperature for heat sealing, labeling alignment) based on test outcomes.
- Inspection and Quality Checks
- Examine filled containers for any signs of underfilling, leakage, or poor sealing.
- Retest until you’re confident every unit meets your quality standards.
- Documentation and Standard Operating Procedures (SOPs)
- Create detailed SOPs for daily operation, periodic cleaning, troubleshooting, and maintenance.
- Train your team thoroughly on these SOPs to ensure consistency.
A well-planned setup phase pays dividends in the form of fewer breakdowns, higher output quality, and smoother day-to-day operations.
6. Best Practices for Operation and Maintenance
Even the most advanced water packing machine can break down or yield subpar results without the proper care and operation techniques. Here are some best practices to implement from day one:
- Routine Cleaning and Sanitization
- Implement a scheduled cleaning regime (e.g., daily, weekly, monthly) based on workload and manufacturer recommendations.
- Use food-grade cleaning agents and strictly follow guidelines to avoid chemical residues.
- Regular Filter Replacement
- Most machines feature water filters or sediment traps that help maintain water purity. Replace these filters according to schedule to prevent clogging and contamination.
- Lubrication of Moving Parts
- Moving components (e.g., gears, conveyor belts, pulleys) require periodic lubrication to reduce wear and tear.
- Select lubricants that are safe for use near consumable products.
- Calibration Checks
- Over time, filling nozzles and measuring systems may drift from their original settings. Conduct periodic calibration to maintain accurate fill levels.
- Record-Keeping
- Maintain logs of cleaning, calibration, repairs, and any observed anomalies.
- Detailed records help spot trends, schedule preventive maintenance, and demonstrate compliance with audits.
- Operator Training and Skill Development
- Provide comprehensive training for all staff operating or maintaining the machine.
- Encourage continuous learning on new features, safety protocols, and troubleshooting techniques.
- Scheduled Downtime for Inspection
- Plan for downtime to thoroughly inspect all machine components, replace worn parts, and make necessary adjustments.
- Preventive maintenance is nearly always more cost-effective than emergency repairs.
By investing in proper upkeep and skilled operators, you’ll maximize your water packing machine’s lifespan, minimize unexpected downtime, and maintain the consistent product quality your customers demand.
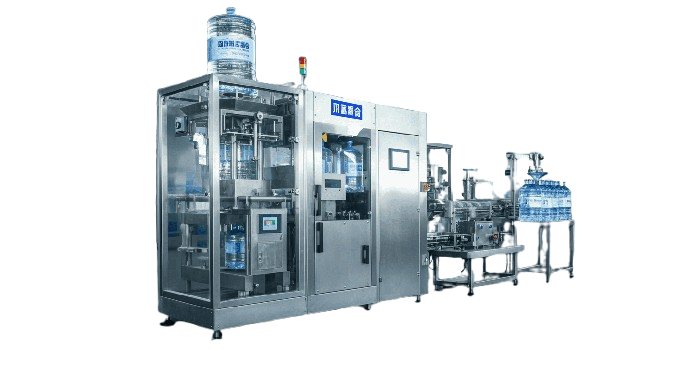
7. Common Challenges and Their Solutions
Despite best efforts, issues can arise in any automated or semi-automated process. Recognizing early symptoms and implementing quick fixes can save valuable time and resources.
7.1 Leakage or Improper Sealing
- Symptoms: Water seeps out of containers, or seals appear loose.
- Causes: Incorrect sealing temperature, malfunctioning sealing heads, worn gaskets, or misalignment.
- Solutions:
- Recalibrate the heat-sealing unit, ensuring temperature settings match the packaging material’s specifications.
- Replace worn parts, such as sealing rings or gaskets.
- Realign sealing heads to ensure even pressure distribution.
7.2 Inconsistent Fill Levels
- Symptoms: Containers are either underfilled (leading to customer complaints) or overfilled (causing spillage and wastage).
- Causes: Sensor misalignment, pump malfunction, or calibration drift.
- Solutions:
- Regularly calibrate filling sensors.
- Inspect pumps or valves for clogs or mechanical failure.
- Ensure containers are properly positioned under the filling heads.
7.3 Frequent Downtime and Repairs
- Symptoms: Regular breakdowns, slow production rates, rising repair costs.
- Causes: Poor maintenance practices, incorrect operation, or aging machinery.
- Solutions:
- Strictly follow preventive maintenance schedules.
- Retrain operators on proper usage protocols.
- Consider upgrading components or the entire machine if it consistently underperforms or has reached its end-of-life.
7.4 Contamination or Off-Taste
- Symptoms: Customers complain about unusual flavors or develop health issues after consuming the water.
- Causes: Dirty contact surfaces, microbial growth in hoses or tanks, poor source water quality.
- Solutions:
- Increase frequency of cleaning and sanitization, including the water supply lines.
- Use UV or ozone treatments to purify water.
- Regularly test source water for contaminants; install additional filtration if necessary.
Proactive monitoring and training are your biggest allies. Addressing small issues quickly often prevents them from escalating into major production stoppages or safety hazards.
8. Regulatory Compliance and Standards
In many regions, water is classified as a food product, subjecting it to rigorous safety standards. Depending on where you operate, different governing bodies—such as the U.S. Food and Drug Administration (FDA) or the European Food Safety Authority (EFSA)—will have guidelines you must follow.
Key Areas of Compliance
- Labeling Requirements
- Regulations often mandate listing source, nutritional information, and bottling details on the label.
- Date coding is critical for traceability.
- Packaging Standards
- Container materials must be food-grade and free from harmful chemicals like BPA if you’re marketing your product as health-centric.
- Seals must be tamper-evident for consumer safety.
- Facility Hygiene
- Strict guidelines on facility cleanliness, employee hygiene, and pest control ensure the product remains safe from contamination.
- Audits and Inspections
- Periodic site visits and inspections by health authorities validate ongoing compliance.
- Proper record-keeping simplifies this process and builds trust with regulators.
- Water Quality Testing
- Regular lab testing to confirm the water meets microbiological and chemical safety standards.
- Documentation of test results is often required by authorities.
A well-configured water packing machine that meets these regulatory standards not only keeps you lawful but also fosters consumer trust. Non-compliance, on the other hand, can result in severe penalties, including hefty fines, product recalls, and reputational damage that’s hard to recover from.
9. Emerging Trends in Water Packaging
The global push for sustainability, coupled with technological advancements, is shaping how companies package and market drinking water. Keeping an eye on these trends can help you future-proof your operation and distinguish your brand.
9.1 Eco-Friendly Packaging
- Trend: Companies are exploring biodegradable or recyclable materials to reduce plastic waste. Some are moving toward paper-based bottles or compostable pouches.
- Why It Matters: Consumers and environmental organizations increasingly demand eco-responsible packaging solutions.
9.2 Smart Packaging and Traceability
- Trend: Advanced labeling and QR codes allow customers to trace the water’s source, see real-time quality metrics, or learn about the brand’s sustainability efforts.
- Why It Matters: Engages consumers digitally, fosters trust, and offers valuable data for companies to refine their supply chain.
9.3 Automation and AI Integration
- Trend: Machines equipped with AI can predict maintenance needs, adjust filling levels dynamically, and minimize human intervention for higher consistency.
- Why It Matters: Reduces downtime, labor costs, and the risk of human error.
9.4 Customized Packaging for Branding
- Trend: Short-run digital printing and modular filling lines allow for hyper-customization of labels and packaging design.
- Why It Matters: Offers smaller brands the opportunity to stand out with unique, limited-edition packaging, boosting marketing impact.
9.5 Health-Focused Innovations
- Trend: Infused waters (vitamins, minerals, electrolytes) are on the rise, requiring specialized filling systems that can handle additives while preserving product stability.
- Why It Matters: Expands revenue streams by tapping into functional beverage markets.
Staying abreast of these trends not only improves your operational efficiency but also positions your brand as forward-thinking and responsible—qualities that resonate with modern consumers.
10. FAQs About Water Packing Machines
Below are frequently asked questions that potential buyers often have about water packing machines. Providing quick and direct answers can help you anticipate user queries and optimize for Google’s Featured Snippet.
Q1: What is the price range for a water packing machine?
Answer: The cost varies widely depending on the machine’s capacity, level of automation, and brand. Entry-level, manual systems might start around a few thousand dollars, while fully automated, high-capacity lines can reach well into the hundreds of thousands.
Q2: How do I choose the right packaging type?
Answer: It depends on your market. Bottled water remains popular for convenience and brand appeal, while pouches are more cost-effective and eco-friendly. Cups are ideal for single servings at events or hospitality settings.
Q3: Are water packing machines only for large-scale operations?
Answer: Not at all. You can find machines designed for small to medium enterprises, even those with limited space or budget. Semi-automatic and manual machines cater specifically to these segments.
Q4: How often should I maintain or service the machine?
Answer: Follow the manufacturer’s guidelines, typically involving daily cleaning, weekly checks, and more thorough monthly or quarterly inspections. Keep detailed logs to ensure compliance and track performance.
Q5: What should I look for in after-sales support?
Answer: Prioritize manufacturers or suppliers with a solid reputation for responsive customer service, easy access to spare parts, and comprehensive technical training. A good support system dramatically prolongs your machine’s lifespan and efficiency.
Q6: Do I need any special licensing to operate a water packing machine?
Answer: Regulations vary by location. Generally, you’ll need food-grade facility licenses, water quality certifications, and compliance with local health and safety regulations. Check with your local authorities for exact requirements.
Conclusion
When it comes to ensuring safe, reliable, and appealing water packaging, investing in the right water packing machine is an absolute game-changer. From small-scale operations looking for semi-automated solutions to large enterprises in need of fully automated lines, the range of options is vast—but so are the opportunities. By carefully evaluating factors such as production capacity, budget, packaging types, and compliance standards, you’ll be well on your way to selecting a machine that boosts efficiency, upholds quality, and helps your brand thrive.
Key Takeaways
- Precision and Hygiene: A top-quality water packing machine reduces contamination risks and ensures accurate fill levels.
- Scalability: Match your production capacity with a system you won’t outgrow overnight.
- Regulatory Compliance: Meeting health and safety guidelines isn’t just a legal obligation—it’s a cornerstone of customer trust.
- Maintenance Matters: Consistent upkeep, training, and record-keeping will prolong equipment life and avert costly breakdowns.
- Future-Proofing: Keep an eye on emerging trends like eco-friendly materials, AI-driven automation, and enhanced traceability to stay ahead in the market.
Ready to Elevate Your Water Packaging?
- Contact Us today to learn more about our selection of innovative water packing machines and how they can fit into your production line.
- Join Our Community by subscribing to our newsletter, where we share the latest industry news, tips, and case studies on water packaging.
- Read More: Check out our other in-depth articles on sustainability in packaging, global regulatory trends, and tips for scaling a beverage business.
Invest in the right machine, adopt best practices, and you’ll soon see how a robust water packing system can enhance not only the safety and quality of your product, but also your reputation in a highly competitive industry. Make the choice today, and watch your operations flow more smoothly than ever—one well-packaged bottle (or pouch) at a time.
Stay Connected with EngiTech
EngiTech is your trusted source for in-depth knowledge on industrial mechanical engineering machines and technologies. Stay ahead with the latest innovations, expert insights, and practical guides designed to help you make informed decisions for your business and engineering needs. Join our growing community of professionals and industry leaders to stay updated and competitive in the ever-evolving world of industrial technology.