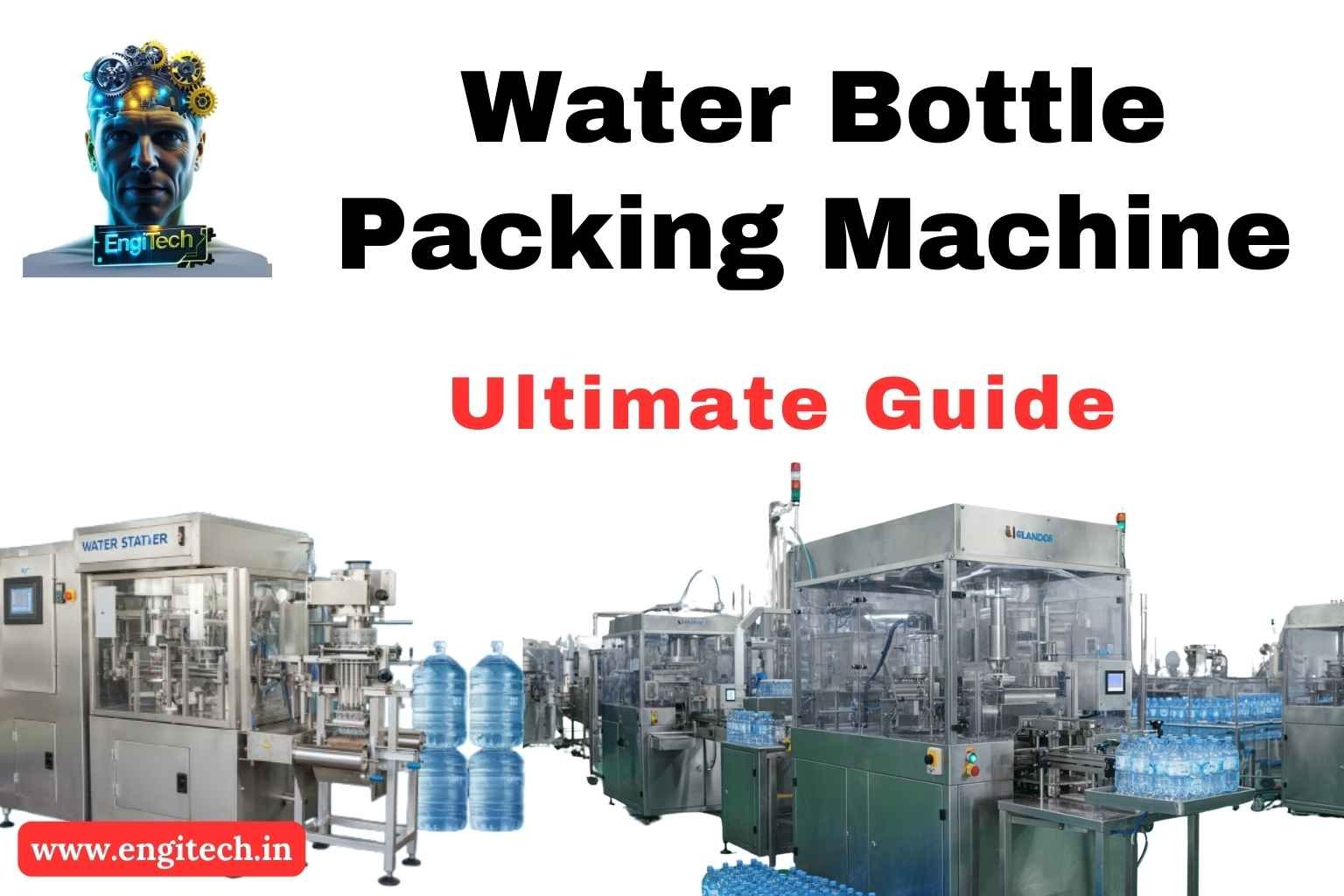
The global demand for bottled water continues to surge, and so does the need for efficient, reliable packaging solutions. For businesses aiming to streamline their operations while maintaining top-tier safety standards, a water bottle packing machine can be a real game-changer.
Whether you’re a startup stepping into the beverage industry or an established brand looking to scale up, this in-depth guide will help you navigate every aspect of investing in and operating a water bottle packing machine. By the end of this article, you’ll be equipped with actionable insights, expert tips, and the confidence to make informed decisions that propel your business forward.
Table of Contents
1. Introduction: Why Bottled Water?
For years, bottled water has been one of the fastest-growing segments in the global beverage market. According to some industry reports, worldwide bottled water consumption has risen consistently every year for over a decade. Several factors contribute to this expansion:
- Growing Health Awareness: Many consumers prefer water over sugary drinks, making bottled water a popular choice.
- Convenience: Sealed, portable bottles are easier to handle and store.
- Safe Drinking Water Initiative: In regions where tap water safety can be questionable, bottled water provides peace of mind.
But with this soaring demand, producers face their fair share of challenges: meeting high-volume orders, maintaining strict hygienic standards, and ensuring brand consistency. This is where a water bottle packing machine steps in to offer a streamlined, efficient solution.
2. What Is a Water Bottle Packing Machine?
A water bottle packing machine is a specialized piece of equipment designed to automate the process of sealing, labeling, and packaging bottled water for distribution. It typically handles multiple stages of packaging—from feeding empty bottles into the system, filling them with water, applying caps, labels, and finally grouping them into packs.
While the specific machine features may vary depending on the manufacturer and the model, the overarching goal remains consistent: to elevate efficiency and product safety while minimizing manual labor.
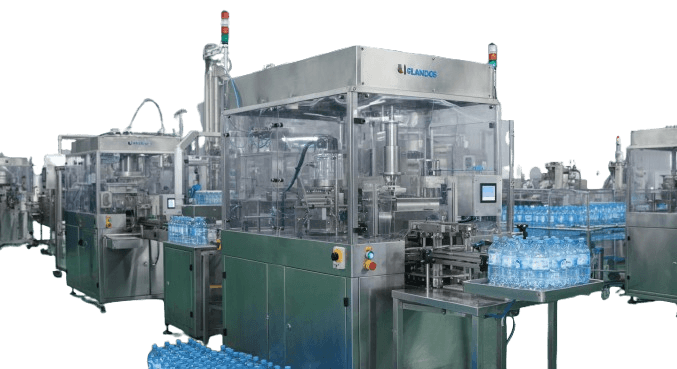
3. Understanding Key Machine Components
Before delving into the different types of machines, it’s helpful to understand the essential components that typically make up a water bottle packing machine. Getting a grasp on each part ensures you can troubleshoot issues more effectively and maintain the machine for optimal performance.
- Bottle Feeder or Unscrambler
This component aligns and positions empty bottles on a conveyor. By automating the process of feeding bottles into the packaging line, it reduces the need for manual labor and helps maintain a steady production pace. - Filler
The filler injects water into each bottle with precision. Modern machines use flow meters or level sensors to ensure accurate fill levels while preventing overflows. - Capper
As bottles move along the conveyor, the capper applies and tightens caps. In many systems, the capping mechanism is synchronized with the filler to ensure no downtime between the filling and capping processes. - Labeler
Whether you use shrink labels, pressure-sensitive labels, or wrap-around labels, the labeler ensures that each bottle is branded accurately. High-speed labelers often work with optical sensors to detect bottle orientation. - Shrink Wrapping or Carton Packing Unit
Depending on your packaging style—whether it’s shrink-wrapping packs of bottles or placing them into cartons—this section completes the final grouping step. - Control Panel and Sensors
Equipped with PLCs (Programmable Logic Controllers), control panels allow you to set parameters like fill volume and conveyor speed. Sensors help detect bottle jams, misalignment, or low material supply.
Understanding these components is critical for day-to-day operation. Moreover, it ensures you can converse intelligently with service technicians and quickly order the right spare parts when necessary.
4. Types of Water Bottle Packing Machines
Choosing the right machine depends largely on your production volume, budget, and operational style. Below are some of the common types you’ll encounter:
A. Semi-Automatic Packing Machines
Semi-automatic machines automate only part of the packaging process. Operators might need to manually load bottles or apply caps. These systems are typically less expensive and are suitable for small-scale operations.
- Pros:
- Lower upfront cost
- Simpler maintenance
- Cons:
- Lower production speed
- Higher labor requirements
B. Fully Automatic Packing Machines
Fully automatic machines manage the entire process—from feeding empty bottles to final packing—without significant human intervention. They’re ideal for large-scale facilities aiming for high output.
- Pros:
- High throughput
- Consistent quality
- Reduced labor costs
- Cons:
- Higher initial investment
- More complex maintenance requirements
C. Monoblock Systems
Monoblock machines combine filling, capping, and labeling into a single, compact unit. They’re designed to save floor space and increase operational efficiency.
- Pros:
- Space-efficient
- Synchronization of multiple tasks
- Cons:
- Limited customization options
- Higher cost for multi-functionality
D. Customized or Modular Lines
For businesses with unique requirements—such as bottling flavored water, handling multiple bottle sizes, or integrating advanced filtration systems—customized or modular packing lines can be configured to accommodate these needs.
- Pros:
- Tailor-made to specific requirements
- Scalable for future expansion
- Cons:
- Longer lead times for design and installation
- Potentially higher initial investment
Selecting the right type of machine is a balance between your current operational demands, budget, and long-term growth strategy. It’s often wise to think ahead; even if your current production volume is modest, investing in a slightly larger system can pay off if you anticipate rapid growth.
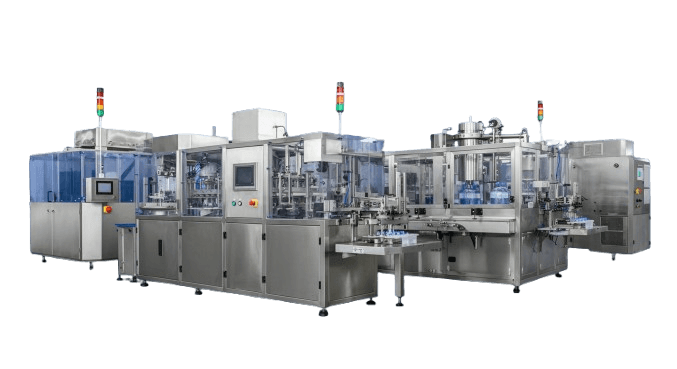
5. Step-by-Step Overview of the Packing Process
Knowing how the packing process works helps you optimize each stage. Below is a typical sequence from start to finish:
- Bottle Loading
- Empty bottles are loaded onto a conveyor or into a bottle unscrambler.
- The system orients the bottles upright to ensure smooth transition to the next stage.
- Water Filling
- Each bottle passes under the filler, which dispenses a pre-set volume of water.
- Advanced systems use sensors to prevent spillage and ensure consistent fill levels.
- Capping
- The bottle moves to the capping station, where caps are automatically placed and tightened.
- Capping torque is adjusted to prevent leaks while ensuring consumer-friendly removal.
- Label Application
- A labeler affixes brand labels precisely.
- Optical sensors detect bottle orientation for correct label placement, minimizing errors.
- Coding/Batch Numbering
- Some machines include a coding unit that prints date, batch number, or other vital information for traceability.
- This step is crucial for meeting regulatory and quality-control requirements.
- Shrink Wrapping or Carton Packing
- Single bottles or multi-packs are wrapped in plastic shrink film or placed into cartons for easy distribution.
- This ensures that products remain secure and tamper-evident during transit.
- Quality Inspection
- Cameras, sensors, or manual checks may be used to spot damaged bottles or incorrect labeling.
- Bottles that don’t meet set criteria are separated from the production line.
- Storage and Palletizing
- Packed bottles are then stacked onto pallets, ready for shipping or storage.
- Automated palletizing systems can further reduce manual handling.
By understanding each step, you can identify where bottlenecks or errors might occur. This knowledge allows for a more targeted approach to troubleshooting and machine upgrades.
6. Advantages of Automating Your Packing Line
Shifting from a manual or semi-automatic setup to a fully automated water bottle packing machine can feel daunting. However, the benefits often justify the investment:
- Consistent Product Quality
Automated systems enforce uniform filling levels and proper capping torque, reducing the risk of leaks or underfilled bottles. - Enhanced Productivity
A fully automated line can operate at speeds far exceeding manual labor. This translates into higher daily output and the ability to fulfill large orders swiftly. - Cost Savings Over Time
While automation involves a higher upfront cost, the long-term savings in labor and minimized waste often result in a quicker return on investment. - Reduced Error Rate
Automation drastically cuts down on human errors such as misapplied labels or inconsistent fills. - Improved Workplace Safety
Repetitive tasks like capping and labeling can strain human workers. Automation reduces workplace injuries and the associated costs. - Scalability
Need to ramp up production for a seasonal spike or a new product line? Automated systems can adapt to different bottle sizes and production speeds more easily than manual setups.
7. Common Challenges and How to Solve Them
Even the most sophisticated machine encounters hiccups. Being prepared can make all the difference:
- Bottle Jams
- Cause: Bottles not oriented correctly or conveyor speed set too high.
- Solution: Integrate bottle unscramblers and use sensors to detect misalignments. Regularly clean conveyors and align guides.
- Label Misalignment
- Cause: Improper calibration of label applicators or sensor issues.
- Solution: Routine calibration checks and scheduled maintenance. Keep labelers free from dirt and adhesive buildup.
- Inconsistent Fill Levels
- Cause: Flow meter or filling valve malfunction.
- Solution: Regularly inspect and clean fill nozzles and flow meters. Schedule calibration to maintain accuracy.
- Excessive Downtime
- Cause: Poor planning for spare parts, lack of trained personnel, or frequent machine breakdowns.
- Solution: Maintain a critical parts inventory and ensure staff are well-trained. Adopt a preventive maintenance strategy.
- Sanitation Concerns
- Cause: High humidity in the production area, bacterial growth in water lines, or contamination on conveyor belts.
- Solution: Implement rigorous cleaning protocols, use food-grade lubricants, and ensure water lines are sealed and regularly sanitized.
An efficient troubleshooting process typically involves a combination of daily visual inspections, data tracking on performance metrics, and immediate corrective action when a problem is spotted.
8. Factors to Consider Before Purchasing
Choosing the right water bottle packing machine is a multi-layered decision. Here’s what to keep in mind:
- Production Capacity
- Assess both your current output and future expansion goals. Overshooting capacity can be costly, while undershooting can stifle growth.
- Budget Constraints
- Factor in not just the purchase price but also installation costs, training, maintenance, and energy consumption.
- Floor Space and Layout
- Ensure your facility can accommodate the machine’s dimensions, including space for maintenance access and safety clearances.
- Regulatory Compliance
- Check whether the machine meets local and international standards, like FDA, ISO, or other food-grade regulations.
- After-Sales Support
- Quality technical support is vital. A great machine can become a liability if spare parts are hard to find or technicians are not readily available.
- Customization Options
- If your product line includes flavored water, sparkling beverages, or various bottle sizes, choose a machine with enough versatility to handle these nuances.
- Integration with Existing Systems
- If you already have a bottling line or an ERP (Enterprise Resource Planning) system, verify that the new packing machine is compatible with them.
9. Maintenance Tips for Longevity
A water bottle packing machine can serve you reliably for a decade or more if maintained properly. Here are best practices to ensure its longevity:
- Daily Inspections
- Check for leaks, worn belts, or loose bolts. Identifying issues early prevents major breakdowns.
- Lubrication Schedule
- Moving parts should be lubricated per the manufacturer’s guidelines. Choose food-grade lubricants where product contact is possible.
- Filter and Nozzle Checks
- If your machine includes filtration for the water supply, replace filters regularly to avoid clogs. Clean fill nozzles daily.
- Calibration
- Periodically calibrate sensors, flow meters, and capping torque. Minor drifts in calibration can accumulate into big problems over time.
- Software Updates
- Modern machines come with PLCs or even IoT capabilities. Keep the software updated to benefit from improved efficiencies and bug fixes.
- Scheduled Deep Cleaning
- Beyond daily cleaning, plan monthly or quarterly deep cleans to remove hidden debris. This is especially crucial for preventing mold or bacterial growth.
- Employee Training
- Train your operators on machine functionality and basic troubleshooting. An informed workforce leads to fewer operational mistakes.
10. Cost Analysis and ROI Expectations
One of the most pressing questions for any business owner or production manager is the return on investment. While the cost of a water bottle packing machine can vary from a few thousand dollars for a semi-automatic model to hundreds of thousands for a fully integrated high-speed line, the potential ROI can be substantial.
- Direct Labor Savings
- By automating, you can redirect manual labor to more value-added tasks, reducing repetitive strain injuries and lowering labor costs.
- Reduced Waste and Product Loss
- Automation minimizes the chances of overfilling or spillage, both of which can erode profit margins.
- Increased Throughput
- A faster line enables you to take on larger orders and potentially negotiate better distribution deals.
- Long-Term Gains
- High-quality packaging boosts brand reputation, leading to repeat business and customer loyalty.
While exact ROI timelines differ based on production volume and machine cost, a well-chosen, efficiently run packing line can often pay for itself within two to five years.
11. Environmental Considerations and Sustainability
With more consumers caring about the environmental impact of the products they buy, sustainability has become a key focus in the bottled water industry. Here’s how a water bottle packing machine can align with eco-friendly practices:
- Eco-Conscious Materials
- Machines can be configured to handle bottles made from recycled plastic or even biodegradable materials.
- Energy Efficiency
- Look for machines with energy-saving motors, LED lighting, and automated standby modes to reduce energy consumption.
- Reduced Packaging Waste
- Advanced shrink-wrapping techniques and precise labeling systems minimize material usage.
- Consider using thinner plastic films or biodegradable shrink wraps.
- Water Reclamation
- Some machines are designed to recirculate rinse water, significantly reducing water waste.
- Green Certifications
- Investing in machinery with recognized green certifications can bolster your brand image and help meet regulatory requirements.
Sustainability isn’t just about ethics— it’s also a strong market differentiator. An environmentally conscious brand can attract a broader consumer base and enhance overall trustworthiness.
12. Future Trends in Water Bottle Packing Technology
Technology in the packaging sector evolves rapidly. Staying ahead of emerging trends can give your business a competitive edge:
- Industry 4.0 and IoT
- Machines are increasingly equipped with sensors and connectivity features, enabling real-time performance monitoring and predictive maintenance.
- Smart Materials
- Biodegradable plastics, edible packaging, and novel materials are under constant development. As these become commercially viable, machine manufacturers will adapt to handle them.
- Robotics and AI
- AI-driven sorting and robotic palletizing are likely to become more commonplace, further reducing manual labor and errors.
- Personalization and Customization
- On-demand label changes, personalized bottle designs, and variable printing are becoming easier, allowing brands to create niche offerings with minimal downtime.
- Virtual and Augmented Reality
- Training operators and performing remote machine diagnostics using VR or AR could reduce machine downtime and simplify complex repairs.
By keeping an eye on these trends, you can make more informed decisions about upgrading or purchasing new equipment, ensuring that your operations remain both relevant and profitable.
13. FAQs
Q1: How often should I schedule maintenance for my water bottle packing machine?
It depends on usage and manufacturer recommendations. Generally, plan for daily inspections, monthly lubrication and calibration checks, and comprehensive quarterly services. Preventive maintenance goes a long way in avoiding breakdowns.
Q2: Can a single machine handle multiple bottle sizes?
Yes, many modern machines are adjustable and come with interchangeable parts such as bottle guides and filling heads. However, ensure these adjustments are straightforward if you plan to switch sizes frequently.
Q3: Are water bottle packing machines difficult to operate?
Most systems are designed for user-friendly operation with an intuitive control panel. Adequate training and clear Standard Operating Procedures (SOPs) make it easy for operators to handle day-to-day tasks.
Q4: What certifications should I look for in a machine?
Depending on your region, look for compliance with FDA standards (if operating in the U.S.), ISO certifications, CE marking (for the European market), or other local food-grade regulations.
Q5: How do I ensure the water used is safe and contamination-free?
Incorporate a reliable filtration or purification system upstream. Regularly test water quality, maintain pipes and tanks, and keep the filling environment clean and sealed to prevent external contamination.
Conclusion
A water bottle packing machine stands at the heart of any modern bottling operation, providing consistency, efficiency, and scalability. From selecting the right model and setting up a robust maintenance routine to embracing emerging trends like IoT and AI, the choices you make can directly influence your bottom line and brand reputation.
Whether you’re taking your first steps in bottled water production or upgrading an existing line, remember that success hinges on informed decision-making. We encourage you to:
- Optimize and Expand: As your operation grows, look for complementary equipment—like advanced blowers or dryers—to further enhance efficiency and product safety.
- Evaluate Your Needs Thoroughly: Balance your current production volumes and growth projections.
- Research and Compare: Don’t settle for the first option you come across. Seek detailed proposals and compare service contracts.
- Stay Current: Keep an eye on technology trends that could give you a competitive advantage.
Final Note: A well-chosen water bottle packing machine is more than a piece of equipment— it’s a strategic investment that amplifies your brand, boosts your operational efficiency, and ensures you stand out in a crowded marketplace.
Stay Connected with EngiTech
EngiTech is your trusted source for in-depth knowledge on industrial mechanical engineering machines and technologies. Stay ahead with the latest innovations, expert insights, and practical guides designed to help you make informed decisions for your business and engineering needs. Join our growing community of professionals and industry leaders to stay updated and competitive in the ever-evolving world of industrial technology.