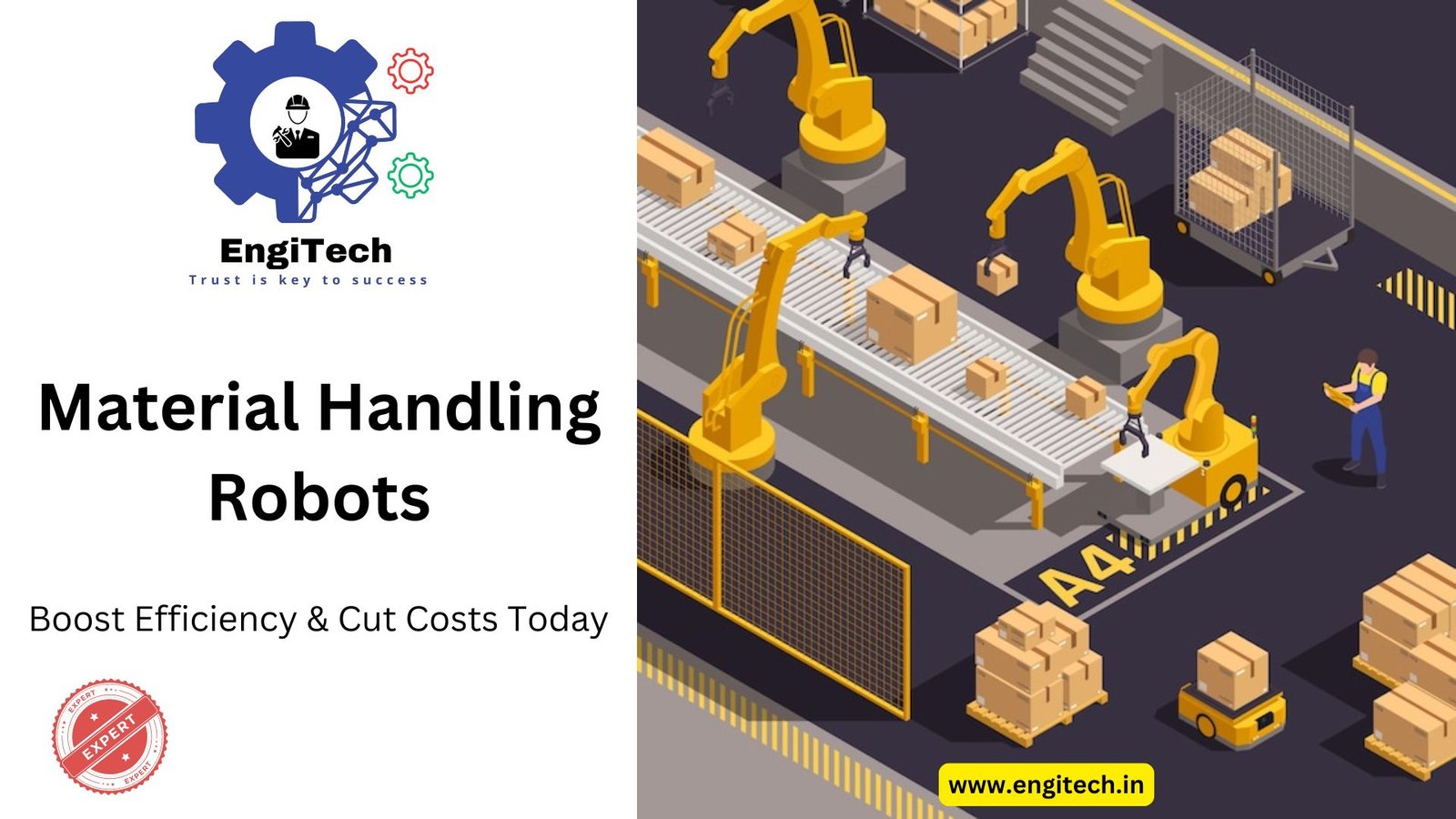
In today’s fast-paced industrial landscape, Material Handling Robots are transforming the way companies manage, transport, and store materials. These robots play a critical role in enhancing efficiency, minimizing human error, and reducing labor costs across various industries. Whether you’re involved in manufacturing, logistics, or warehousing, understanding how material handling robots work and their benefits is crucial for staying competitive.
In this comprehensive guide, we’ll dive deep into the world of material handling robots, exploring how they work, their types, applications, and how they can drive operational efficiency. We’ll also discuss the latest advancements in robotics and offer expert insights into how these machines can revolutionize your business.
Table of Contents
What Are Material Handling Robots?
Material Handling Robots are automated machines designed to move, control, store, and protect materials throughout the manufacturing and distribution process. These robots can handle tasks such as picking, packing, palletizing, sorting, and transporting materials within a facility.
The integration of robotics in material handling systems helps businesses automate repetitive tasks, reduce human labor, and increase throughput. From small-scale operations to large industrial settings, these robots are essential for improving efficiency and ensuring smooth production workflows.
The Role of Material Handling Robots in Industry
Material handling robots are central to smart factories and Industry 4.0 technologies. They are critical in the following areas:
- Improved Efficiency: Robots can work 24/7 without fatigue, significantly increasing productivity.
- Enhanced Safety: They can take over hazardous or physically demanding tasks, reducing the risk of injury.
- Cost Savings: By automating manual processes, companies can save on labor costs and reduce operational expenses.
- Precision and Accuracy: Robots perform tasks with a high degree of accuracy, reducing errors and enhancing product quality.
The widespread adoption of these robots signals a shift toward more automated, data-driven industrial processes that ensure consistency and scalability.
Types of Material Handling Robots
1. Pick-and-Place Robots
Pick-and-place robots are widely used in assembly lines and packaging industries. These robots are designed to pick up objects from one location and place them in another with extreme precision and speed.
Applications:
- Sorting and packaging items
- Handling fragile components in electronics
- Assembling parts in automotive manufacturing
2. Automated Guided Vehicles (AGVs)
AGVs are mobile robots that follow predefined paths to transport materials within a facility. They are commonly used in warehouses and production plants for moving goods between various stations.
Applications:
- Transporting raw materials to production lines
- Moving finished products to storage areas
- Supporting warehouse logistics
3. Robotic Palletizers
Robotic palletizers are designed to stack products onto pallets for transportation or storage. These robots are widely used in industries where palletizing large quantities of goods is necessary.
Applications:
- Food and beverage industries
- Consumer goods packaging
- Warehouse distribution
4. Collaborative Robots (Cobots)
Cobots are designed to work alongside human workers, assisting them in tasks that require precision and strength. Unlike traditional industrial robots, cobots are equipped with advanced sensors that ensure safe interaction with humans.
Applications:
- Assisting in lifting heavy objects
- Assembly line support
- Packaging and quality control
Key Benefits of Material Handling Robots
1. Increased Throughput
One of the most significant advantages of material handling robots is their ability to increase throughput. By automating repetitive tasks such as picking, sorting, and transporting materials, these robots can work faster and more efficiently than humans, leading to higher production rates.
2. Improved Workplace Safety
Material handling often involves heavy lifting and hazardous environments. Robots can take over these tasks, reducing the risk of workplace injuries and accidents. For example, robotic palletizers eliminate the need for manual stacking, which can be physically taxing and dangerous for workers.
3. Cost-Effectiveness
While the initial investment in material handling robots may seem substantial, the long-term cost savings are significant. Companies save on labor costs, reduce downtime due to worker fatigue, and minimize the costs associated with workplace injuries. Additionally, robots can operate continuously, increasing overall production efficiency.
4. Accuracy and Precision
Material handling robots are equipped with sensors and advanced algorithms that allow them to perform tasks with high precision. This ensures that materials are handled correctly, minimizing the risk of damage and improving the overall quality of the final product.
Latest Advancements in Material Handling Robots
The field of robotics is continuously evolving, and material handling robots are no exception. Here are some of the latest advancements that are shaping the future of material handling:
1. Artificial Intelligence (AI) Integration
The integration of AI into material handling robots allows these machines to learn from their environment and optimize their performance over time. AI-powered robots can identify patterns, predict outcomes, and make real-time adjustments, improving their efficiency and adaptability.
2. Advanced Sensors and Vision Systems
Modern material handling robots are equipped with advanced sensors and vision systems that allow them to “see” and navigate their environment. These systems enable robots to handle a variety of materials, from fragile items to large, bulky objects, with precision.
3. Collaborative Robotics
As mentioned earlier, collaborative robots (cobots) are designed to work alongside humans. The development of cobots has opened up new possibilities for material handling, allowing businesses to automate tasks that were previously too complex for traditional robots.
4. Mobile Robotics and Autonomous Systems
Mobile robots, including AGVs, are becoming increasingly autonomous. These robots can navigate complex environments, avoid obstacles, and even communicate with other machines to optimize material flow within a facility.
How Material Handling Robots Drive Operational Efficiency
By automating various tasks in material handling, robots streamline operations and reduce inefficiencies. Here’s how material handling robots contribute to operational efficiency:
- Automated Sorting: Robots can sort items based on size, weight, or other criteria, ensuring materials are processed quickly and accurately.
- Reduced Downtime: Unlike human workers, robots do not need breaks, which allows them to operate continuously, minimizing downtime.
- Scalability: Material handling robots can be easily scaled to meet increasing production demands, ensuring businesses can adapt to market changes without compromising efficiency.
How to Choose the Right Material Handling Robot for Your Business
Choosing the right material handling robot depends on several factors:
- Application Needs: Determine what tasks the robot will perform—whether it’s picking, packing, palletizing, or transporting materials.
- Payload Capacity: Ensure the robot can handle the weight and size of the materials it will transport.
- Speed and Accuracy: Consider how quickly and accurately the robot needs to perform its tasks.
- Integration with Existing Systems: The robot should integrate seamlessly with your current material handling systems, such as conveyors, AGVs, or warehouse management systems (WMS).
Future Trends in Material Handling Robotics
The future of material handling robotics is promising, with several trends shaping the industry:
- 5G-Enabled Robots: With faster communication and data transmission, 5G will enable more responsive and efficient material handling robots.
- Robotic Process Automation (RPA): The integration of RPA will further automate repetitive tasks, making material handling processes more efficient.
- Sustainable Robotics: Companies are increasingly adopting eco-friendly robots that consume less energy, helping to reduce their carbon footprint.
FAQs related to Material Handling Robots:
1. What are material handling robots used for?
Material handling robots are used to automate tasks such as moving, sorting, packing, palletizing, and transporting materials within industrial environments like warehouses, manufacturing plants, and distribution centers.
2. How do material handling robots work?
These robots operate using programmed algorithms, sensors, and vision systems to detect and interact with materials. They are controlled through software, allowing them to perform tasks like picking and placing items, transporting goods, and handling repetitive tasks with high precision.
3. What are the different types of material handling robots?
The most common types include pick-and-place robots, automated guided vehicles (AGVs), robotic palletizers, and collaborative robots (cobots). Each type specializes in specific tasks such as lifting, transporting, or sorting materials.
4. What industries benefit from material handling robots?
Material handling robots are used in various industries, including manufacturing, logistics, e-commerce, automotive, food and beverage, pharmaceuticals, and warehousing. They help increase efficiency and reduce labor costs in these industries.
5. What are the advantages of using material handling robots?
The key advantages include increased productivity, enhanced workplace safety, cost savings, precision in handling, and the ability to operate continuously without fatigue, leading to overall operational efficiency.
6. How much do material handling robots cost?
The cost of material handling robots varies depending on the type, capabilities, and level of automation required. A simple robot may cost between $50,000 to $100,000, while more advanced systems with AI or mobile capabilities can range from $150,000 to $500,000 or more.
7. What is the role of collaborative robots (cobots) in material handling?
Collaborative robots, or cobots, are designed to work alongside human workers, assisting in tasks that require precision, strength, or repetitive actions. They enhance human capabilities and improve safety in material handling operations.
8. Can material handling robots integrate with existing systems?
Yes, material handling robots can be integrated with existing systems like conveyors, warehouse management systems (WMS), and automated storage and retrieval systems (AS/RS) to create a seamless and efficient material flow within facilities.
9. How do material handling robots improve workplace safety?
By taking over physically demanding or hazardous tasks, such as heavy lifting or working in dangerous environments, material handling robots reduce the risk of injuries and accidents, making workplaces safer for human employees.
10. What are the latest advancements in material handling robotics?
Recent advancements include the integration of AI and machine learning, advanced vision systems, autonomous mobile robots (AMRs), and improved collaborative robotics (cobots). These technologies allow robots to learn, adapt, and operate autonomously in dynamic environments.
11. How do I choose the right material handling robot for my business?
Choosing the right robot depends on your specific needs, including the type of tasks, payload capacity, speed, precision, and the ability to integrate with your existing systems. It’s essential to evaluate your business requirements and consult with robotics experts before making a decision.
12. What is the ROI of implementing material handling robots?
The return on investment (ROI) for material handling robots typically comes from increased efficiency, reduced labor costs, minimized errors, and enhanced safety. While the upfront cost can be high, many companies see a positive ROI within 1-2 years of implementation.
Conclusion
Material handling robots are revolutionizing industries by automating tasks, improving efficiency, and enhancing workplace safety. By incorporating these robots into your operations, you can optimize material flow, reduce costs, and stay competitive in a rapidly evolving market.
Whether you’re looking to improve your warehouse logistics, enhance manufacturing efficiency, or simply stay ahead of the technological curve, material handling robots are a must-have in today’s industrial world.
Ready to explore more about material handling solutions? Visit EngiTech for the latest insights and innovations in industrial automation. Stay ahead with comprehensive resources on cutting-edge technology, trends, and applications.