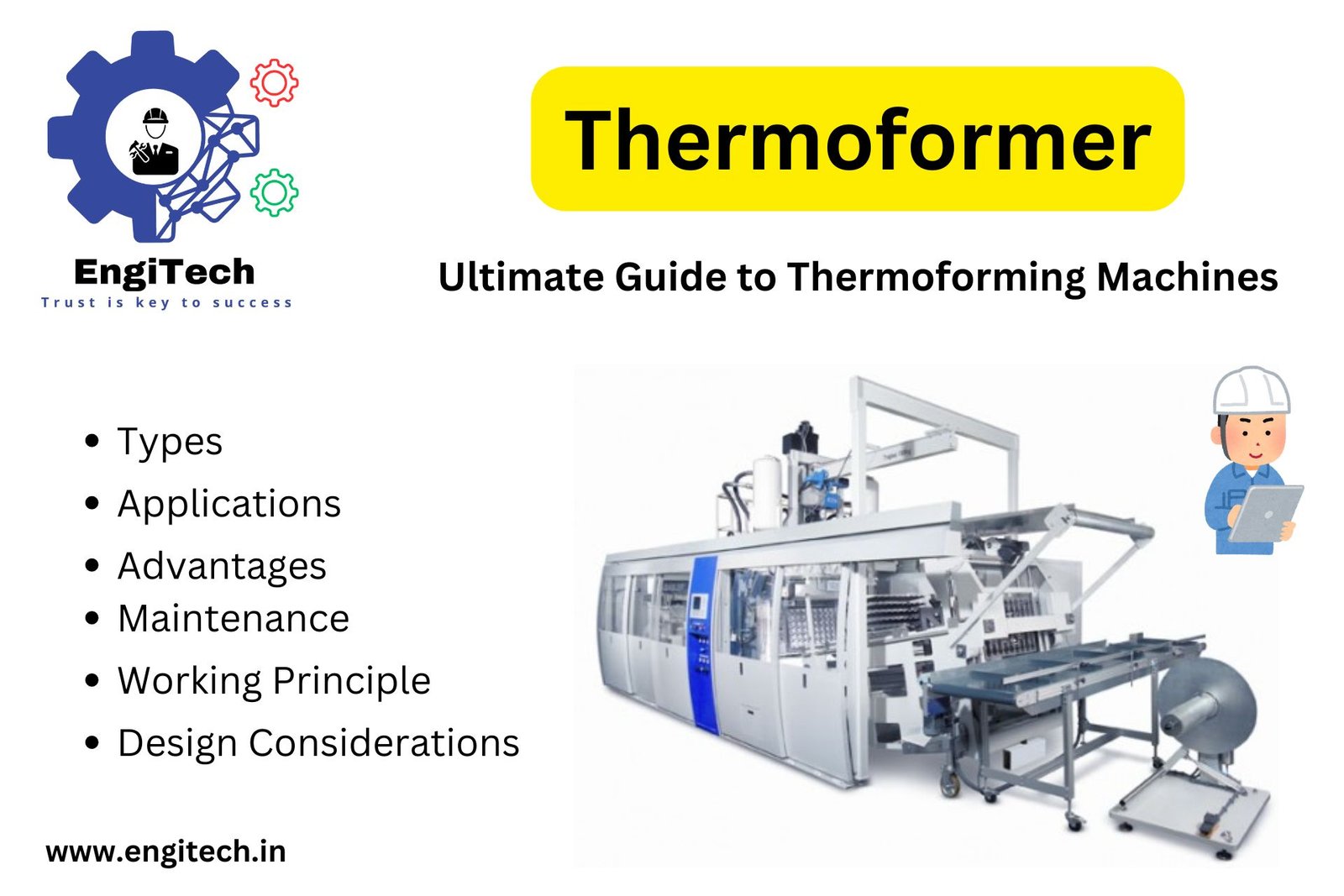
Thermoforming is an essential process in the manufacturing industry, particularly in producing plastic products with intricate shapes and designs. If you are seeking in-depth knowledge about thermoforming, thermoforming machines, and thermoforming equipment, this guide will provide detailed insights that cater to knowledge seekers, students, and professionals alike.
Our expert engineers have curated this content to ensure that you understand the core aspects, solve common queries, and gain valuable insights.
Table of Contents
Introduction to Thermoforming
Thermoforming is a manufacturing process that involves heating a plastic sheet until it becomes pliable, then forming it into a specific shape using a mold, and finally trimming it to create a finished product. Thermoformers, also known as thermoforming machines, are the primary equipment used in this process. The applications of thermoforming are vast, ranging from packaging, automotive parts, and consumer goods to medical devices.
The importance of understanding thermoforming lies in its widespread use and the critical role it plays in creating everyday items. By the end of this guide, you will have a solid understanding of thermoforming, the types of thermoforming machines, the equipment used, and the best practices to ensure quality production.
Understanding Thermoformers
What is a Thermoformer?
A thermoformer is a machine specifically designed to perform the thermoforming process. It heats plastic sheets and molds them into desired shapes. Thermoformers come in various sizes and capabilities, depending on the complexity of the product being manufactured. These machines are crucial for industries that require high-precision plastic components.
Types of Thermoformers
- Vacuum Forming Machines: These are the most common type of thermoformers. In vacuum forming, a plastic sheet is heated until it is pliable and then sucked down onto a mold by a vacuum. This process is ideal for simple designs and is cost-effective for low to medium production runs.
- Pressure Forming Machines: Pressure forming is a step up from vacuum forming. In this process, additional pressure is applied to the plastic sheet to ensure it conforms tightly to the mold. This technique is used for more complex shapes and detailed designs.
- Twin Sheet Thermoforming Machines: As the name suggests, twin sheet thermoforming involves forming two plastic sheets simultaneously, which are then fused together to create a hollow part. This method is commonly used for producing items like pallets, tanks, and structural components.
- Heavy Gauge Thermoformers: These machines are designed for forming thick plastic sheets, typically used in producing large, durable components such as automotive parts, enclosures, and heavy-duty containers.
Key Components of Thermoforming Machines
- Heating System: The heating system is a critical component of a thermoformer. It ensures that the plastic sheet is heated uniformly to the desired temperature. The system can be infrared, radiant, or contact heating, depending on the machine.
- Mold: The mold is the form over which the heated plastic sheet is shaped. Molds can be made from various materials, including aluminum, wood, or composite materials, depending on the production requirements and budget.
- Clamping Unit: The clamping unit holds the plastic sheet in place during the heating and forming process. It is essential for maintaining the sheet’s position to ensure accurate forming.
- Vacuum and Pressure Systems: These systems apply the necessary forces to shape the plastic sheet onto the mold. The vacuum system removes air between the sheet and the mold, while the pressure system adds external force for more detailed shaping.
- Cooling System: After forming, the plastic needs to be cooled to retain its shape. The cooling system ensures that the formed part cools evenly, preventing warping or deformation.
- Trimming and Finishing Units: Once the plastic part is formed and cooled, it is trimmed to remove excess material and achieve the final dimensions. Finishing units may also include processes like deburring, polishing, or adding surface textures.
Thermoforming Process : Step-by-Step Guide
1. Material Selection
Choosing the right plastic material is the first step in the thermoforming process. Common materials include ABS, PVC, PET, HDPE, and polystyrene. Each material has unique properties that make it suitable for specific applications. For instance, PET is commonly used for packaging due to its clarity and strength, while ABS is preferred for automotive parts because of its toughness.
2. Sheet Heating
The selected plastic sheet is loaded into the thermoformer, where it is heated until it becomes pliable. The heating process must be carefully controlled to ensure even heating, as uneven heating can result in poor quality or defects in the final product.
3. Forming
Once the plastic sheet reaches the desired temperature, it is formed over the mold using vacuum, pressure, or a combination of both. The forming process is critical, as it determines the shape and quality of the final product.
4. Cooling
After forming, the plastic part must cool down while still on the mold. This step is crucial to ensure that the part retains its shape and dimensional accuracy. Cooling can be natural or assisted by fans or water systems.
5. Trimming and Finishing
The formed part is trimmed to remove any excess material and achieve the final product dimensions. Additional finishing processes may be applied depending on the requirements, such as adding surface textures or coatings.
Applications of Thermoforming
Thermoforming is a versatile process used in various industries. Here are some common applications:
- Packaging: Thermoforming is widely used in the packaging industry to produce clamshells, blisters, trays, and containers. The process allows for creating lightweight, durable, and cost-effective packaging solutions.
- Automotive: In the automotive industry, thermoforming is used to produce parts like dashboards, door panels, and interior trim. The ability to create large, complex shapes makes thermoforming ideal for automotive applications.
- Medical Devices: Thermoforming is also used in the medical field to produce items like surgical trays, diagnostic equipment housings, and prosthetic components. The process ensures high precision and hygiene, essential in medical applications.
- Consumer Goods: From refrigerator liners to bathtubs, thermoforming is used to create various consumer goods. The process allows for high customization and aesthetic flexibility, making it popular in consumer products.
- Aerospace: The aerospace industry uses thermoforming to produce lightweight and durable components for aircraft interiors. The ability to create intricate shapes while maintaining strength is a significant advantage of thermoforming in aerospace applications.
Advantages of Thermoforming
Cost-Effectiveness
Thermoforming is a cost-effective manufacturing process, especially for low to medium production runs. The initial investment in molds and equipment is relatively low compared to other plastic forming methods like injection molding.
Design Flexibility
One of the key advantages of thermoforming is its design flexibility. It allows for creating complex shapes and designs, making it suitable for a wide range of applications. The ability to produce both small and large parts adds to its versatility.
Quick Turnaround Time
Thermoforming offers a faster production cycle compared to other methods. The simplicity of the process, combined with the ability to quickly change molds, allows manufacturers to respond swiftly to market demands.
Material Efficiency
Thermoforming is an efficient process in terms of material usage. The ability to trim and recycle excess material reduces waste, making it an environmentally friendly option.
Challenges in Thermoforming
While thermoforming offers numerous advantages, it also presents some challenges:
Material Limitations
Not all plastic materials are suitable for thermoforming. Some materials may not respond well to the heating process or may not form correctly, leading to limitations in material selection.
Thickness Uniformity
Maintaining uniform thickness throughout the formed part can be challenging, especially for complex shapes. Uneven thickness can lead to weak spots and affect the structural integrity of the final product.
Tooling Costs
While thermoforming is generally cost-effective, the cost of creating molds can be high, especially for complex designs. Tooling costs can be a significant factor for small production runs.
Post-Processing Requirements
Thermoformed parts often require additional post-processing, such as trimming, drilling, or surface finishing. These steps add to the production time and cost.
Best Practices in Thermoforming
To achieve high-quality results in thermoforming, it’s essential to follow best practices:
1. Material Selection
Choose the right material based on the application’s requirements. Consider factors like strength, flexibility, and heat resistance when selecting materials.
2. Mold Design
Invest in high-quality molds to ensure accurate and consistent forming. The mold design should consider factors like shrinkage, draft angles, and parting lines to avoid defects.
3. Temperature Control
Maintain precise temperature control during the heating process. Uneven heating can lead to warping, bubbles, or other defects in the final product.
4. Quality Control
Implement strict quality control measures throughout the thermoforming process. Regularly inspect formed parts for defects and ensure that they meet the required specifications.
5. Efficient Trimming
Optimize the trimming process to minimize waste and ensure that the final product meets the desired dimensions. Consider using automated trimming systems for high-volume production.
Future Trends in Thermoforming
As technology advances, the thermoforming industry is also evolving. Here are some future trends to watch:
1. Automation
Automation is becoming increasingly prevalent in thermoforming, with automated systems handling everything from sheet loading to trimming. This trend is expected to continue, leading to higher efficiency and lower labor costs.
2. Sustainable Materials
With growing environmental concerns, there is a push towards using more sustainable materials in thermoforming. Biodegradable and recyclable plastics are gaining popularity, and future developments in material science are likely to drive this trend further.
3. Advanced Molding Techniques
New molding techniques, such as 3D-printed molds, are being explored in thermoforming. These techniques offer greater flexibility and faster prototyping, opening up new possibilities for customization.
4. Integration with Industry 4.0
The integration of thermoforming with Industry 4.0 technologies, such as IoT and data analytics, is expected to enhance process control and quality assurance. Real-time monitoring and predictive maintenance can lead to improved production efficiency and reduced downtime.
Expert Insights on Thermoforming
Our expert engineers emphasize the importance of understanding the nuances of thermoforming to optimize production quality. According to our experts:
- “Material selection is critical. Always consider the end-use environment and mechanical requirements when choosing materials.”
- “Investing in high-quality molds pays off in the long run. It reduces defects and ensures consistent part quality.”
- “Temperature control cannot be overstated. Proper heating is the foundation of a successful thermoforming process.”
- “Automation is the future. Embrace it to stay competitive and improve production efficiency.”
These insights are based on years of experience in the industry and are designed to guide you in making informed decisions when working with thermoforming.
FAQs on Thermoforming:
- What is thermoforming?
- Thermoforming is a manufacturing process where a plastic sheet is heated to a pliable forming temperature, shaped into a specific form using a mold, and then trimmed to create a finished product.
- What materials can be used in thermoforming?
- Common materials used in thermoforming include ABS, PET, PVC, polystyrene, polycarbonate, and polyethylene. The choice of material depends on the desired properties of the final product.
- What are the different types of thermoforming processes?
- The primary types of thermoforming processes are vacuum forming, pressure forming, and twin sheet thermoforming. Each process is suited for different applications and product complexities.
- What are thermoforming machines used for?
- Thermoforming machines are used to produce a wide range of plastic products, including packaging, automotive parts, consumer goods, medical devices, and more.
- How do vacuum forming and pressure forming differ?
- Vacuum forming uses a vacuum to pull the heated plastic sheet against the mold, while pressure forming uses both vacuum and additional air pressure to achieve more detailed shapes and textures.
- What are the advantages of thermoforming over injection molding?
- Thermoforming is generally more cost-effective for low to medium production runs, offers quicker turnaround times, and provides greater design flexibility for large or intricate parts.
- What factors should be considered when choosing a thermoforming material?
- Factors include the material’s strength, flexibility, heat resistance, chemical resistance, and suitability for the intended application (e.g., food packaging, automotive components).
- What is the typical thickness range for thermoformed products?
- Thermoformed products can range from thin gauge (0.1mm) for packaging to thick gauge (up to 12mm) for industrial parts. The thickness depends on the application and required strength.
- How does the cooling process affect thermoforming?
- Proper cooling is essential to prevent warping and ensure the final product retains its shape and dimensions. Cooling can be natural or assisted by air or water systems.
- What are common defects in thermoformed products and how can they be prevented?
- Common defects include warping, bubbles, uneven thickness, and surface imperfections. These can be prevented by maintaining consistent heating, proper mold design, and using quality materials.
- How are thermoformed products trimmed and finished?
- After forming, products are trimmed using cutting tools or laser cutters to remove excess material. Finishing processes may include deburring, polishing, or adding surface textures.
- What is twin sheet thermoforming?
- Twin sheet thermoforming involves forming two plastic sheets simultaneously and then fusing them together to create a hollow part. This method is often used for structural components.
- What are the latest trends in thermoforming technology?
- Current trends include automation, the use of sustainable materials, advanced molding techniques such as 3D-printed molds, and integration with Industry 4.0 technologies for enhanced process control.
- What industries use thermoforming?
- Thermoforming is used across various industries, including packaging, automotive, medical, consumer goods, aerospace, and more.
- How do I choose the right thermoforming machine for my needs?
- Consider factors such as the size and complexity of the parts, production volume, material compatibility, and budget when choosing a thermoforming machine.
These FAQs are designed to address the most common questions related to thermoforming, providing clear and concise answers that help readers better understand the process and its applications.
Conclusion
Thermoforming is a versatile and widely used manufacturing process that offers numerous advantages in terms of cost, design flexibility, and efficiency. Whether you are a student, knowledge seeker, or working professional, understanding the intricacies of thermoforming, thermoforming machines, and thermoforming equipment is essential for optimizing production and achieving high-quality results.
By following the best practices outlined in this guide and staying updated on industry trends, you can harness the full potential of thermoforming in your applications. Remember, successful thermoforming is a blend of art and science, and with the right knowledge, you can master this process to create exceptional products.
From EngiTech Team
EngiTech our ultimate destination for cutting-edge insights and expert knowledge on industrial mechanical engineering machines. From state-of-the-art dryers and blowers to the latest advancements in thermoforming and beyond, we provide in-depth resources designed to empower engineers, professionals, and industry leaders. Stay ahead of the curve with our expertly crafted content, tailored to solve your most complex challenges and optimize your engineering processes. Explore our comprehensive guides, stay updated on the latest innovations, and transform your expertise with EngiTech – where technology meets industry excellence.