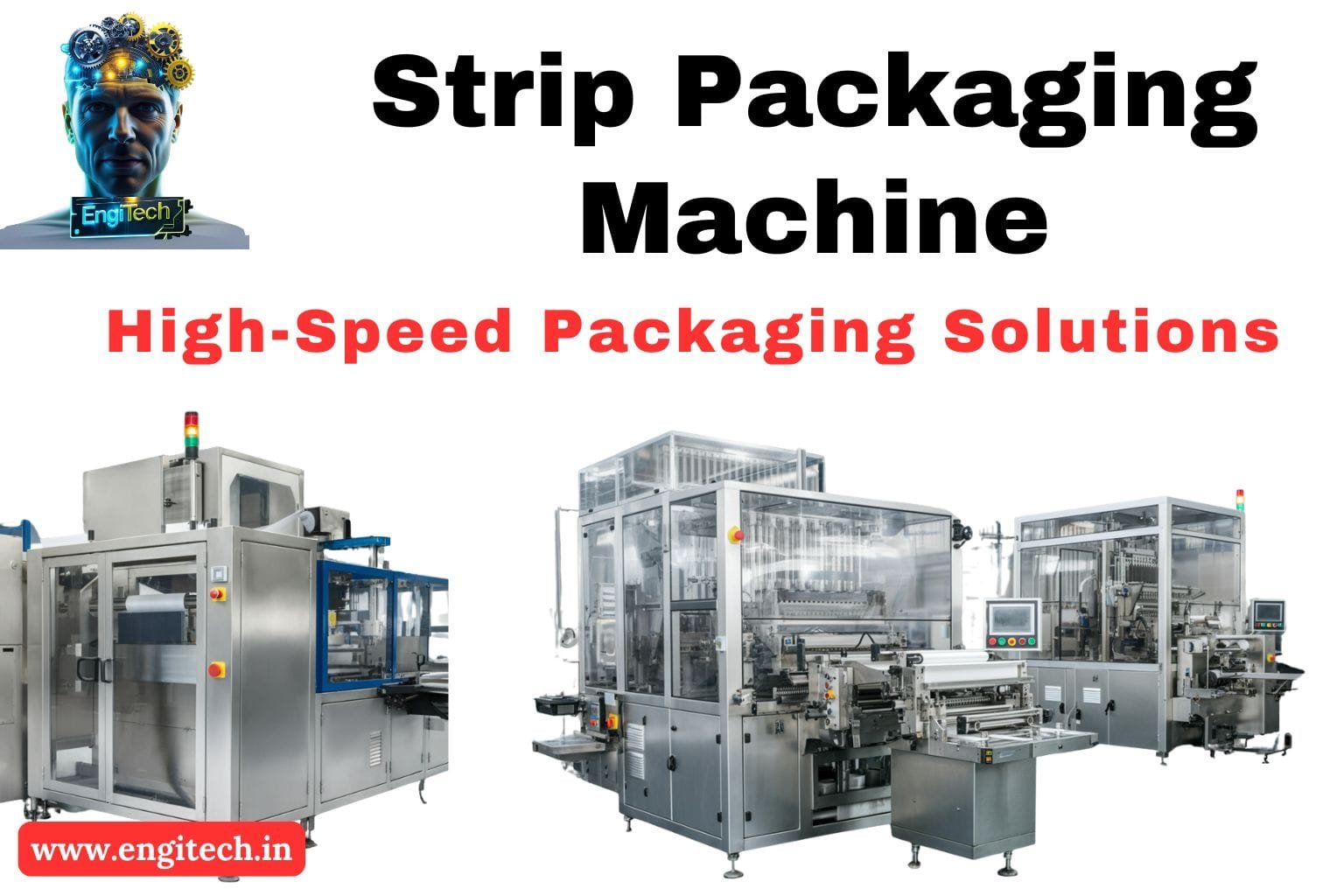
In today’s fast-paced pharmaceutical and healthcare industries, efficiency and precision are everything. That’s exactly why the strip packaging machine has become an indispensable asset for manufacturers seeking high-speed solutions and accurate dose delivery. Whether you’re a production manager exploring new packaging machinery or a healthcare professional curious about medication delivery, this guide will walk you through the what, why, and how of strip packaging machines—shedding light on their core features, benefits, and best practices.
By the end of this guide, you’ll be equipped with expert-backed insights, real-world examples, and actionable steps to optimize your packaging line. Let’s delve into everything you need to know about one of the most transformative pieces of equipment in pharmaceutical and medical device packaging.
Table of Contents
Understanding the Basics of Strip Packaging
What is Strip Packaging?
Strip packaging is a specialized method of enclosing individual doses or units—usually tablets, capsules, or small medical devices—between layers of heat-sealable films, such as aluminum foil or transparent plastic. Each individual dose is sealed in its own pocket, which helps protect the product from moisture, light, or other environmental factors. Once sealed, these pockets can be easily torn open by the end user.
Unlike blister packaging, which often uses pre-formed plastic cavities sealed with a film or foil backing, strip packaging places individual items between two flexible layers that are sealed on all sides. This not only provides a high level of barrier protection but also makes it easier for manufacturers to produce continuous strips of individually packaged units.
Why Does Strip Packaging Matter?
In the realm of pharmaceutical packaging, maintaining dose accuracy, product integrity, and user convenience is paramount. Strip packaging meets all three of these critical needs:
- Dose Accuracy: Each strip contains precisely one dose, eliminating confusion or potential overdosing.
- Product Integrity: The hermetic seal ensures the product remains uncontaminated, preserving its potency.
- User Convenience: Patients can easily tear off a single dose and carry it on the go without bulky or complicated packaging.
Given the current emphasis on safety, especially within pharma manufacturing, strip packaging has become a go-to solution for many over-the-counter (OTC) medications and prescription drugs.
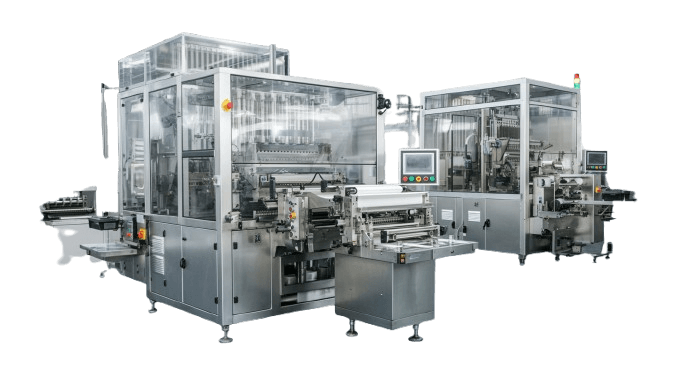
Key Components of a Strip Packaging Machine
Feeder Mechanisms
A strip packaging machine typically includes a feeder system that aligns tablets, capsules, or small medical devices in a uniform manner. The feeder ensures items are consistently oriented and spaced before moving into the sealing chamber. Depending on the product, feeders may use vibratory bowls, rotary dispensers, or gravity chutes.
Heat Sealing Stations
At the heart of any strip packaging operation lies the heat sealing station. This component applies controlled heat and pressure to bond two layers of packaging material—usually foil, plastic film, or both—around each item. Depending on the machine, there may be multiple sealing stations for progressive sealing, cutting, and trimming.
Cutting and Perforation Assembly
Once sealed, individual doses must be separated or perforated. High-speed strip packaging machines often include rotary knives or reciprocating cutters that slice the sealed film into single-dose packs or multi-unit strips. Some models incorporate perforation rollers that allow the end-user to tear off a single dose quickly.
Control Panel and Sensors
Modern machines integrate PLC (Programmable Logic Controller) systems and an array of sensors for real-time monitoring. These sensors check everything from temperature consistency in the heat sealing module to the presence of each product in the feeder. An advanced control panel gives operators immediate data on machine speed, temperature settings, and overall operational status, ensuring minimal downtime and a high level of quality assurance.
How a Strip Packaging Machine Works
Step-by-Step Process
- Product Feeding: Tablets, capsules, or devices are loaded into the machine’s feeder. Automated systems ensure that each item drops in perfect alignment onto the packaging film.
- Film Feeding: Two rolls of packaging material—either foil or a combination of foil and plastic film—are unrolled from opposite sides of the machine.
- Sealing and Forming: The first heat sealing station bonds the films around each product. Temperature, pressure, and sealing time are carefully regulated to achieve a hermetic seal.
- Cooling and Inspection: Some machines include a cooling step right after sealing, which helps to stabilize the bond before cutting. Optical or mechanical sensors inspect the formed strip for missing products, double fills, or seal inconsistencies.
- Cutting and Perforation: A knife or perforation assembly cuts the long strip into individual single-dose packages or multi-dose strips, depending on the user’s requirements.
- Discharge and Collection: The finished strips are then discharged onto a conveyor or into a collection bin, ready for further packaging processes such as cartoning or case packing.
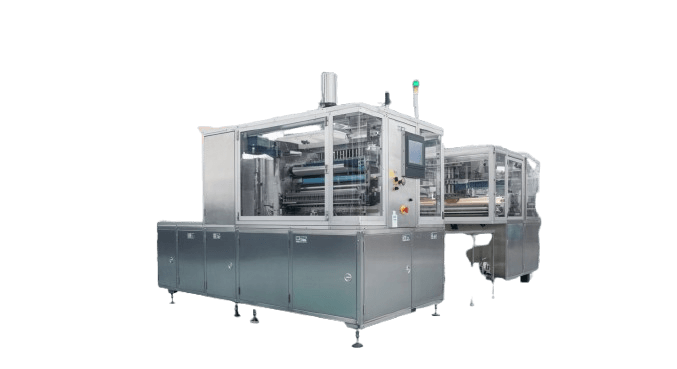
Automation and Efficiency
Many modern strip packaging machines emphasize packaging automation to reduce labor costs and improve accuracy. Automated product feeders, servo-driven motors, and integrated quality control systems are standard in high-end models. This level of automation becomes vital in large-scale high-speed packaging lines, where any bottleneck can drastically reduce overall productivity.
Essential Features and Specifications
Throughput and Speed
One of the first specifications to consider is the machine’s throughput, typically measured in strips per minute or doses per minute. For large-scale pharma manufacturing, you may need equipment capable of producing thousands of strips per hour without compromising on seal integrity.
Material Compatibility
Strip packaging machines can work with different films, including aluminum foil, laminated film, paper-foil laminates, and medical-grade plastics. The machine should offer adjustable sealing parameters to accommodate varying thicknesses and material compositions.
Seal Integrity and Validation
In a regulated industry, every seal must be tamper-proof and contamination-free. Machines often come with built-in validation features such as in-line checks, seal strength testing, and automatic rejection of faulty packages. Consistency in seal integrity not only protects consumers but also helps manufacturers maintain compliance with global regulations like the FDA’s 21 CFR Part 210-211.
Cleanroom Compatibility
For medical or sterile packaging applications, the machine must operate in a controlled environment. Features like stainless-steel construction, HEPA filtration for the workspace, and easy-to-clean surfaces ensure the machine meets stringent quality assurance standards.
Advantages of Using a Strip Packaging Machine
Extended Shelf Life
Strip packaging typically offers an excellent barrier against moisture, oxygen, and light—three primary culprits behind product degradation. By sealing each dose individually, manufacturers can significantly extend a product’s shelf life, making strip packaging ideal for medications prone to moisture damage.
Enhanced Dose Safety and Convenience
Because each strip contains exactly one dose, patients and caregivers benefit from clear dosage control. This is particularly useful in hospitals or long-term care facilities, where medication errors can lead to serious health complications. Moreover, single-dose strip packaging cuts down on waste and makes it easier for patients to transport medication discretely.
Cost-Effectiveness and Efficiency
While the initial investment in a strip packaging machine can be considerable, the long-term benefits often justify the cost. Automated feeding and sealing mechanisms reduce labor expenses, minimize material waste, and boost overall throughput. The high-speed production of individually sealed units translates into substantial savings and rapid return on investment (ROI).
Versatility
From tablet packaging to smaller medical devices like test strips or syringes, modern machines can adapt to a wide array of products. Quick-changeover features, modular feeder systems, and programmable settings make it possible to handle multiple product types on a single line.
Industry Applications and Real-World Examples
Pharmaceuticals and Nutraceuticals
The pharmaceutical sector is the largest user of strip packaging machinery. Over-the-counter (OTC) pain relievers, cold and flu tablets, and dietary supplements often rely on strip packaging to provide single doses. This approach ensures the correct dosage, simplifies inventory management, and meets consumer demand for portability.
Real-World Example: A large OTC drug manufacturer implemented a high-speed strip packaging machine for its line of pediatric cold tablets. By automating the packaging process, the company reduced manual labor by 40%, decreased contamination risks, and extended product shelf life by up to 12 months.
Medical Devices
Beyond medications, strip packaging machines are also used to package small medical devices. Sterile strips containing catheters, test strips for glucose monitoring, or single-use syringes can be efficiently packaged and protected from external contaminants.
Real-World Example: A healthcare provider used strip packaging for distributing individual test strips in remote clinics. The single-use packets maintained sterility and made it easier to transport the test strips across various locations without damaging them.
Veterinary Medicine
Veterinary clinics and animal healthcare manufacturers often use strip packaging for tablets and chewables meant for pets. Proper portion control is critical for animal medications, and strip packaging ensures the right dose each time.
Selecting the Right Strip Packaging Machine for Your Needs
Assessing Production Volume
Before selecting a strip packaging machine, consider your current and projected production volumes. Are you producing on a massive scale, or is your operation more niche? High-volume manufacturers may require fully automated, continuous-motion machines, whereas smaller facilities may opt for semi-automatic models that balance speed with cost-effectiveness.
Material Compatibility and Product Specifications
Knowing the thickness and type of your packaging material is essential. If your product is sensitive to oxygen or moisture, you’ll likely require foil with high barrier properties. Alternatively, if you need consumers to see the product, a transparent film packaging might be more appropriate.
Additionally, confirm the machine can handle the dimensions of your specific product—tablet diameter, capsule length, or device shape. Mismatch between product size and feeder design is a common source of jams and downtime.
Regulatory and Quality Requirements
In highly regulated environments like pharmaceuticals or medical device packaging, you need a machine that meets local and international standards. Features such as automated in-line inspection, seal validation, and batch documentation can streamline compliance audits.
Budgeting and ROI Analysis
While it’s tempting to purchase a machine with every available feature, cost-to-benefit analysis is crucial. Identify which features will generate the most tangible improvements to your operations—faster throughput, fewer rejects, less downtime—and invest accordingly.
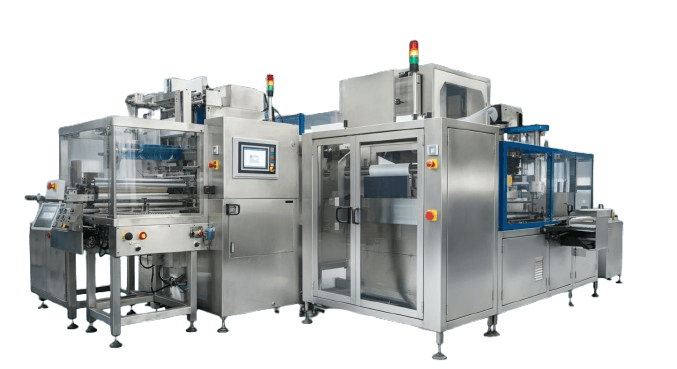
Best Practices for Installation and Maintenance
Proper Site Preparation
Before your strip packaging machine arrives, ensure your facility is equipped with the proper electrical supply, ventilation, and flooring. Large machines require a stable foundation to minimize vibrations that might affect sealing and cutting precision. If your operations involve handling sensitive or sterile items, consider installing cleanroom partitions and HEPA filters.
Staff Training and SOPs
A highly automated machine still requires skilled technicians to operate and maintain it. Develop standard operating procedures (SOPs) that cover everything from initial startup protocols to daily cleaning routines. Training sessions should emphasize safety, product handling, and the basics of troubleshooting common mechanical or electrical issues.
Preventive Maintenance
Routine checks can prolong the lifespan of critical machine parts and minimize downtime. Key areas to monitor include sealing jaws, heater elements, cutting blades, sensors, and motors. Lubrication schedules, filter changes, and calibration of temperature and pressure settings should be documented and performed at regular intervals. Tracking maintenance data helps identify potential problems before they become costly breakdowns.
Software Updates and Continuous Improvement
Modern strip packaging machines rely heavily on software for motion control, data logging, and quality checks. Stay updated with the latest firmware releases from the manufacturer, as these may fix bugs, enhance machine efficiency, or introduce new features. Periodic software audits and system backups are equally important to safeguard operational data and maintain compliance records.
Frequently Asked Questions
1. How does a strip packaging machine differ from a blister packaging machine?
A strip packaging machine seals products between two layers of flexible film, typically without forming pre-molded cavities. In contrast, blister packaging relies on a pre-formed plastic or aluminum cavity sealed with a lid material. Strip packaging often offers a slimmer, more flexible format and is ideal for certain tablets, capsules, or small medical devices.
2. Can a strip packaging machine handle different product sizes?
Yes, most modern machines include adjustable feeder systems and sealing stations to accommodate various product sizes. However, extensive differences in size or shape may require custom tooling or additional machine modules.
3. What materials are commonly used in strip packaging?
Common materials include foil sealing laminates (aluminum foil, paper-foil, plastic-foil combinations) and transparent films. The choice depends on the product’s sensitivity to factors like moisture and light, as well as branding requirements (e.g., wanting consumers to see the product).
4. How do I ensure quality assurance with a strip packaging machine?
Look for machines with built-in quality checks like optical sensors, missing product detectors, and automated reject stations. Regular calibration of temperature and pressure settings, as well as preventive maintenance on critical parts, also ensures consistent seal quality.
5. Is strip packaging more expensive than traditional packaging methods?
While the initial investment in machinery may be higher, the long-term operational costs—especially for large volumes—can be quite competitive. Strip packaging often results in less material waste and reduced labor, which may offset the upfront expenditure.
Conclusion
In an era where speed, quality, and user convenience define market success, a strip packaging machine stands out as a game-changer for pharmaceutical and medical device manufacturers. It safeguards product integrity, ensures precise dosing, and bolsters brand reputation by meeting the highest standards of safety and compliance. From its automated feeding systems to sophisticated heat sealing technology, this piece of packaging equipment embodies the next frontier in efficient, high-speed, and reliable packaging solutions.
If you’re ready to elevate your packaging line, now is the time to explore how a strip packaging machine can transform your operations. Whether you manage a large-scale pharma facility or a specialized healthcare startup, adopting the right machinery can streamline workflows, reduce errors, and enhance the end-user experience. For more insights on optimizing your packaging processes, feel free to explore our related resources or contact us for a personalized consultation. We’d love to hear about your unique challenges and help you find the right solution.
Ready to take the next step? Share this article with your colleagues, leave a comment with any questions or thoughts, and explore our additional guides to gain a deeper understanding of the world of strip packaging machines. By implementing the strategies discussed here, you’ll be well on your way to achieving a more efficient, compliant, and customer-focused packaging line—paving the way for sustained success in a competitive industry.
Stay Connected with EngiTech
EngiTech is your trusted source for in-depth knowledge on industrial mechanical engineering machines and technologies. Stay ahead with the latest innovations, expert insights, and practical guides designed to help you make informed decisions for your business and engineering needs. Join our growing community of professionals and industry leaders to stay updated and competitive in the ever-evolving world of industrial technology.