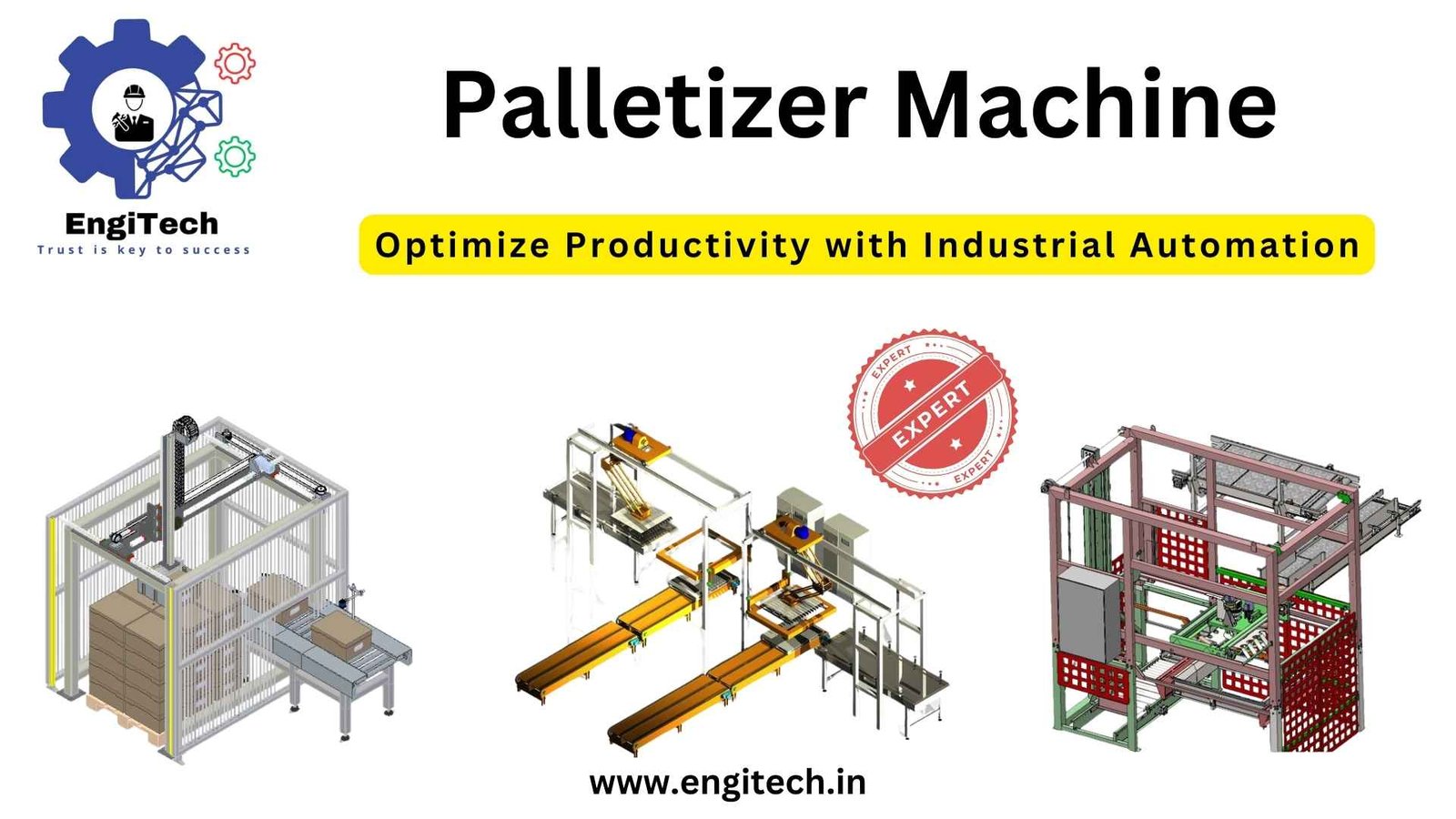
In today’s fast-paced industrial world, efficiency is key. Whether in manufacturing, warehousing, or logistics, automation has revolutionized how products are handled and moved. One essential piece of equipment in this automation process is the palletizer. In this comprehensive guide, we will explore everything you need to know about palletizers, their importance in industrial operations, and how choosing the right palletizer machine can improve productivity. We’ll also dive into the different types of palletizers, including the advanced robotic palletizer, and why they are essential in modern industrial setups.
If you’re looking to optimize your operations, reduce labor costs, and boost your production line efficiency, keep reading to discover how palletizers can help you achieve these goals.
Table of Contents
What is a Palletizer?
A palletizer is a machine used to automatically stack products on a pallet. It’s widely used in industries such as food and beverage, pharmaceutical, manufacturing, and distribution centers. The main function of a palletizer is to take products from a conveyor belt and arrange them in a pre-determined pattern on a pallet. Once the pallet is fully stacked, it’s ready for shipping or storage.
Palletizers come in various forms, but the end goal is the same: to streamline the process of stacking products, reducing the need for manual labor, and improving the overall efficiency of the supply chain.
Importance of Palletizers in Industrial Automation
In modern industrial operations, where time is money, the use of palletizers can significantly reduce labor costs, minimize human error, and improve safety. Manual pallet stacking is time-consuming and physically demanding. Automating this task with a palletizer machine ensures that pallets are stacked quickly and uniformly, leading to fewer workplace injuries and faster throughput.
Types of Palletizers
Palletizers come in several different varieties, each suited to specific types of products and production environments. Below, we’ll cover the main types of palletizers and their specific use cases.
1. Conventional Palletizer
A conventional palletizer typically uses a mechanical arm or push bar to arrange products on a pallet. These machines are widely used due to their simplicity and cost-effectiveness. They are ideal for industries that need to palletize large, uniform products at high speeds.
2. Robotic Palletizer
A robotic palletizer uses robotic arms equipped with grippers or vacuum suction cups to pick and place products on pallets. These machines offer unparalleled flexibility and precision, making them suitable for industries that handle products of varying sizes and shapes. Robotic palletizers are increasingly popular in food and beverage, pharmaceuticals, and e-commerce industries due to their adaptability and ease of programming.
Key advantages of robotic palletizers include:
- Flexibility in handling multiple product types.
- High accuracy and precision in palletizing patterns.
- Scalability in production lines.
3. Semi-Automatic Palletizer
A semi-automatic palletizer requires some level of human intervention, usually for loading products onto a conveyor. However, the actual stacking process is automated. These are suitable for small to mid-sized operations that don’t require the full automation offered by robotic systems.
4. Low-Level Palletizer
In low-level palletizers, products are stacked from a low height. These machines are used for lightweight or fragile products that might be damaged if dropped from a higher height.
How Does a Palletizer Machine Work?
The working principle of a palletizer machine involves several key components, including the infeed conveyor, product sorting mechanism, and the stacking section. The infeed conveyor brings products to the palletizer, where they are arranged into a specific pattern. Once the required pattern is achieved, the palletizer moves the products onto a pallet, either using a mechanical push or a robotic arm. The process repeats until the pallet is fully loaded.
Robotic palletizers, in particular, are equipped with advanced vision systems that help in detecting product size and positioning, ensuring that every product is placed perfectly.
Benefits of Using a Palletizer
1. Increased Efficiency
Using a palletizer can drastically reduce the time it takes to stack products. Automated palletizers can handle multiple products simultaneously, allowing for faster production cycles and increased throughput.
2. Labor Cost Reduction
One of the main reasons companies invest in palletizers is to reduce labor costs. Manual pallet stacking requires a significant amount of labor, and there’s always the risk of injury due to heavy lifting. A palletizer eliminates these concerns.
3. Improved Safety
Workplace injuries related to manual lifting are common in industries that involve product handling. By using a palletizer machine, companies can ensure the safety of their workers, as the machine takes over the strenuous task of stacking products.
4. Product Damage Reduction
Manual palletizing often leads to inconsistent stacking, which increases the likelihood of product damage during transportation. Palletizers provide uniform, secure stacking, significantly reducing the risk of damage.
Choosing the Right Palletizer
Choosing the right palletizer depends on several factors, including the type of product, production volume, and available space. Here’s what to consider when selecting the best palletizer for your operation:
- Type of Product: The weight, size, and shape of the product are critical factors in determining the type of palletizer. For lightweight or fragile items, a low-level or robotic palletizer may be more suitable, while heavier products may require a conventional palletizer.
- Production Speed: If you need to palletize products at high speeds, conventional palletizers are generally more suited to high-volume operations. However, robotic palletizers offer flexibility and can handle different products with minimal setup time.
- Available Space: Some palletizers require more floor space than others. Robotic palletizers, while more flexible, often take up more room than their conventional counterparts. Be sure to consider your facility’s layout when choosing a machine.
- Budget: The cost of a palletizer can vary significantly depending on its type and capabilities. While robotic palletizers offer greater flexibility, they tend to be more expensive than conventional machines. However, the long-term benefits in terms of reduced labor costs and increased efficiency often justify the higher upfront investment.
Future Trends in Palletizing Technology
As industries continue to embrace automation, palletizing technology is evolving rapidly. The future of palletizing lies in advanced robotics, AI, and machine learning. Here are some emerging trends:
- Collaborative Robots (Cobots) Cobots are robots designed to work alongside humans. In the palletizing world, cobots can assist in complex tasks that require both human intuition and robotic precision. These machines are particularly useful in industries where space is limited or where human-robot collaboration is necessary.
- AI-Driven Palletizing Systems Artificial intelligence (AI) is making palletizing systems smarter. AI algorithms can optimize palletizing patterns, reducing the amount of space needed and ensuring the most secure stacking. These systems can also learn and adapt to changes in product size and weight, making them more versatile.
- Sustainability and Energy Efficiency As companies strive to reduce their environmental footprint, energy-efficient palletizers are becoming more popular. Newer models use less power while maintaining high productivity levels, contributing to a more sustainable operation.
Common Challenges in Palletizing and How to Overcome Them
Even with advanced technology, palletizing can present certain challenges. Here’s how to overcome some of the most common issues:
1. Product Inconsistency
Solution: Use vision systems and advanced sensors to detect inconsistencies in product shape and size. Robotic palletizers equipped with such technology can adjust their movements to account for these variations.
2. Space Constraints
Solution: Choose a compact robotic palletizer or a vertical palletizer that takes up less floor space.
3. Cost of Automation
Solution: While the initial investment in a palletizer can be high, the long-term savings in labor and increased efficiency often outweigh the costs. Additionally, leasing options or phased investments can make automation more affordable.
FAQs related to palletizers, their operation, and their role in industrial automation:
- What is a palletizer, and how does it work?
A palletizer is a machine designed to automate the stacking of products onto pallets for shipping or storage. It works by arranging products in a specific pattern on a conveyor system and then transferring them onto a pallet. Depending on the type, this process can be done mechanically or using a robotic arm. - What are the different types of palletizers?
The main types of palletizers are:- Conventional Palletizers
- Robotic Palletizers
- Semi-Automatic Palletizers
- Low-Level Palletizers Each type serves different industrial needs based on product size, shape, and production speed.
- What is the difference between a robotic palletizer and a conventional palletizer?
A conventional palletizer uses mechanical movements to arrange products, while a robotic palletizer utilizes a robotic arm with grippers or suction cups to pick and place products onto pallets. Robotic palletizers are generally more flexible and accurate, making them ideal for handling diverse products. - What industries typically use palletizers?
Palletizers are widely used in industries such as:- Food and Beverage
- Pharmaceuticals
- Manufacturing
- E-commerce and Warehousing
These industries benefit from the efficiency and safety palletizers bring to product stacking and transportation.
- How can a palletizer improve my business operations?
Palletizers increase productivity by automating the labor-intensive task of stacking products, reducing the need for manual labor, decreasing product damage, and improving workplace safety. They also help streamline the shipping process, leading to faster order fulfillment and reduced operational costs. - What are the key advantages of using a robotic palletizer?
Key benefits of robotic palletizers include:- Flexibility to handle different product sizes and shapes
- High precision in stacking
- Easy reprogramming for new products
- Reduced risk of workplace injuries
- Scalability for future production needs
- How do I choose the right palletizer for my business?
The right palletizer depends on several factors:- Type of product (size, weight, fragility)
- Production speed and volume
- Available floor space
- Budget constraints A consultation with a palletizer provider can help identify the best solution based on your specific operational needs.
- What is the cost of a palletizer, and is it worth the investment?
The cost of a palletizer varies depending on its type and capabilities. Conventional palletizers are generally more affordable, while robotic systems are more expensive. However, the return on investment (ROI) in terms of labor savings, increased efficiency, and reduced product damage often justifies the upfront cost. - Can a palletizer handle multiple product types simultaneously?
Yes, especially robotic palletizers, which are highly adaptable and can be programmed to handle different product types and sizes on the same line. Conventional palletizers may require more manual adjustments or setups to switch between product types. - What maintenance does a palletizer require?
Regular maintenance of palletizers involves:
- Checking the mechanical and electrical systems
- Lubricating moving parts
- Inspecting sensors and robotic arms (for robotic palletizers)
- Software updates (for robotic and AI-driven systems) Maintenance schedules depend on usage, but regular check-ups ensure optimal performance and a longer lifespan for the machine.
Conclusion
Investing in a palletizer machine is a smart move for any business looking to improve efficiency, reduce labor costs, and ensure workplace safety. Whether you’re handling lightweight products or heavy goods, there’s a palletizer that fits your needs. With advancements in robotic palletizers and AI-driven systems, the future of palletizing is both exciting and promising.
If you’re ready to take the next step in automating your production line, explore EngiTech’s comprehensive resources on palletizing technology. Stay updated with the latest innovations and applications that can revolutionize your industrial processes. Visit EngiTech today and discover how palletizers can transform your operations!