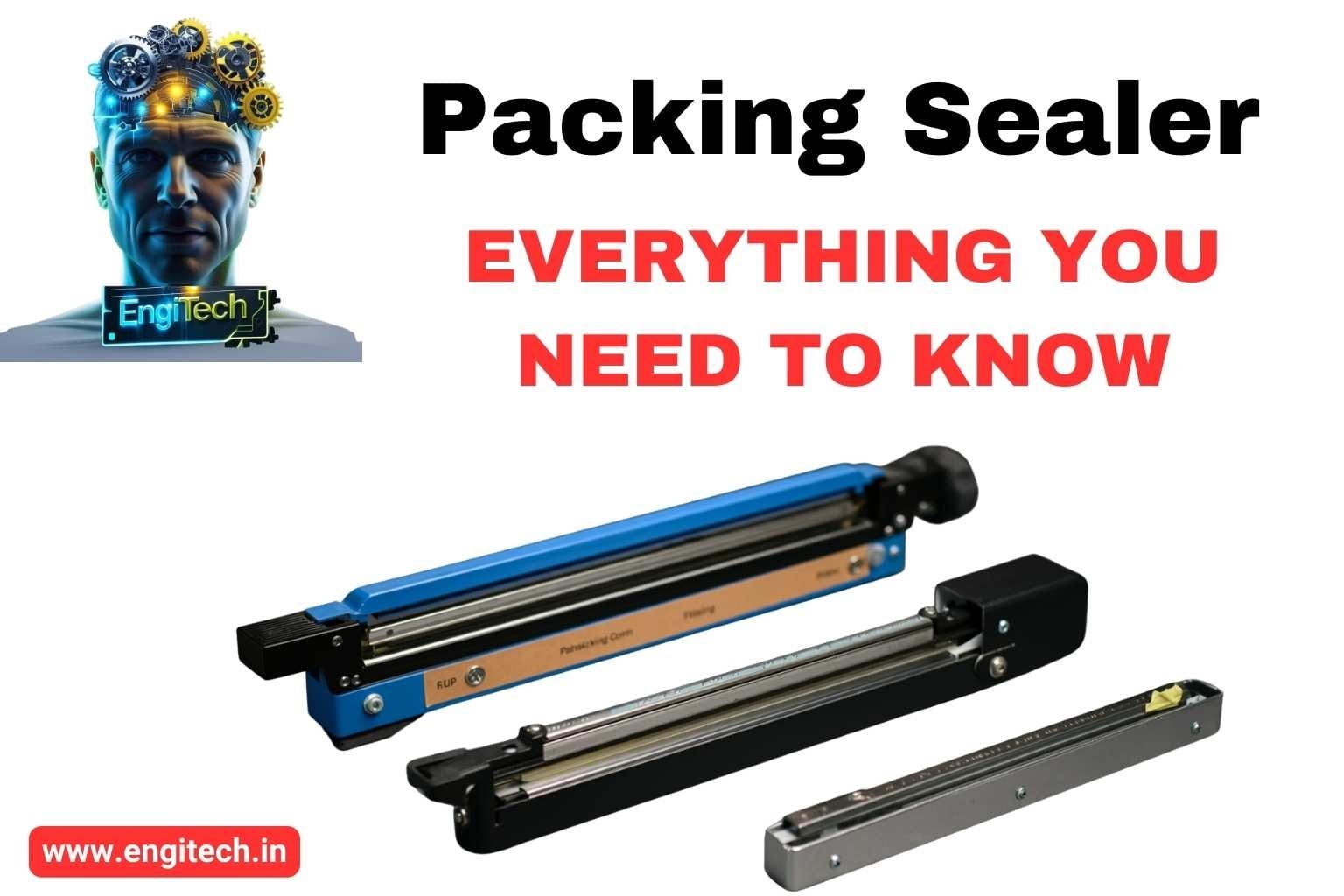
In today’s fast-paced world of shipping, eCommerce, and global trade, a reliable packing sealer can be the unsung hero that keeps businesses running smoothly. Whether you’re an online entrepreneur shipping handmade products around the globe, a food manufacturer needing airtight solutions, or a logistics manager overseeing high-volume packaging lines, the right sealer can make or break your operation. In this comprehensive guide, you’ll discover the different types of packing sealers, how they work, why they matter, and how to select the perfect one for your specific application. We’ll also explore expert-backed insights to ensure you get the most out of your packing sealer, improve efficiency, and optimize packaging workflows—all while maintaining consistent, high-quality seals.
By the end of this guide, you’ll have an in-depth understanding of modern packing sealer technologies, best practices, and maintenance routines. Most importantly, you’ll learn how to leverage the right sealing solutions to streamline your operations and boost customer satisfaction. So, if you’re ready to learn everything there is to know about this essential packaging powerhouse, let’s dive right in.
Table of Contents
What Is a Packing Sealer and Why Is It Important?
A packing sealer, also known as a packaging sealer or sealing machine, is a piece of equipment specifically designed to close and secure packages, bags, cartons, or pouches. The main purpose of a packing sealer is to protect the enclosed items from environmental factors such as moisture, dust, and bacteria, all while maintaining product integrity throughout shipping, handling, and storage.
The Role of Packing Sealers in Today’s Market
- Customer Satisfaction
Properly sealed products arrive in pristine condition, reducing returns and dissatisfaction. A robust seal ensures minimal leakage, breakage, or contamination, which can directly impact your brand’s reputation. - Cost Savings
Effective sealing minimizes waste, preserves product quality, and reduces the need for costly reworks or replacements. With fewer damaged goods, companies can save significantly on logistics and product costs over time. - Compliance with Regulations
In many industries—especially food, pharmaceuticals, and chemicals—strict regulations govern the packaging process. Packing sealers help ensure compliance by providing consistent, reliable seals that meet government and industry standards. - Brand Image & Credibility
A neat, airtight package suggests professionalism and high quality. Investing in the right packing sealer can boost brand credibility and set your products apart from the competition.
The Main Types of Packing Sealers
Understanding the various types of packing sealers helps you choose the most suitable option for your needs. Below are some of the most common categories:
Impulse Sealers
- How They Work: Impulse sealers use a short burst of electricity to heat the sealing bar. The heat melts the plastic layers together to form a tight seal. Once the bar cools, the seal is complete.
- Common Uses: Ideal for sealing bags made of polyethylene (PE) or polypropylene (PP). They’re popular in smaller-scale operations, such as boutique shops or online sellers who need to seal small to medium-sized packages.
- Advantages:
- Energy Efficient: They only use power during the moment of sealing.
- Ease of Use: Generally simple to operate with minimal training.
- Cost-Effective: An economical choice for low- to medium-volume operations.
Continuous Band Sealers
- How They Work: Continuous band sealers use a conveyor belt and rotating sealing bands that pass over the bag’s open end. The machine applies heat and pressure, creating a secure seal as the bag moves along.
- Common Uses: Ideal for mid- to high-volume packaging operations where speed and consistency are crucial, such as food processing plants and larger manufacturing facilities.
- Advantages:
- High Throughput: Capable of sealing many bags per minute.
- Consistent Seal Quality: Uniform heat application ensures reliability.
- Versatile: Can handle multiple bag sizes and materials.
Vacuum Sealers
- How They Work: These sealers remove air from the package before sealing, creating a vacuum environment that can extend product shelf life.
- Common Uses: Widely used in the food industry for perishable items like meat, cheese, coffee, and produce. Also popular in electronics packaging to prevent corrosion and moisture damage.
- Advantages:
- Extended Shelf Life: Significantly slows down oxidation and microbial growth.
- Reduced Storage Space: Vacuum-packed items are more compact.
- Enhanced Product Presentation: Tightly sealed packages look professional and appealing.
Heat Shrink Sealers
- How They Work: Heat shrink sealers typically involve two steps: sealing the package in shrink film and then applying heat (usually via a heat gun or a heat tunnel) to shrink the film around the product.
- Common Uses: Common in retail packaging, gift baskets, and consumer goods, where visual presentation is key.
- Advantages:
- Protective and Tamper-Evident: The shrink film fits snugly, providing protection and making tampering obvious.
- Professional Aesthetic: Shrink-wrapped items often look more appealing, which can boost product value.
- Versatile Packaging Options: Works with multiple shapes and sizes, from gift baskets to DVD cases.
Carton Sealers
- How They Work: Carton sealers are designed to seal the flaps of corrugated boxes using adhesives, such as tape or glue, creating a robust seal along the top and bottom.
- Common Uses: Heavily used in shipping and logistics for product distribution.
- Advantages:
- High Speed: Automated carton sealers can process large volumes quickly.
- Secure Closure: Ensures boxes remain sealed during transit.
- Reduced Labor: Streamlines warehouse operations and cuts down on manual taping tasks.
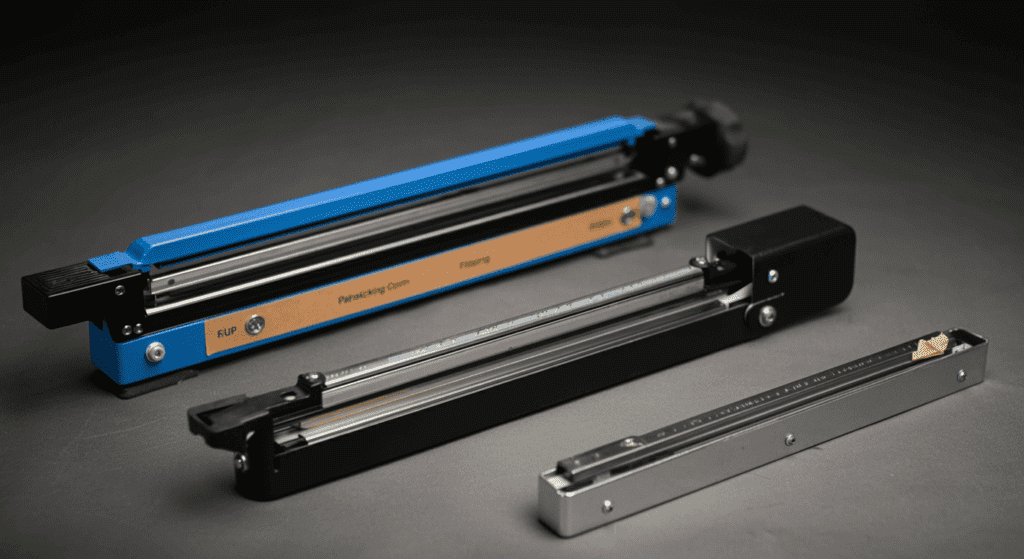
Key Features to Consider When Choosing a Packing Sealer
With numerous models and variations on the market, selecting the best packing sealer can be daunting. Here are the core features you should evaluate:
Material Compatibility
- Why It Matters: Not all sealers handle the same materials. For instance, impulse sealers work well with poly bags, while vacuum sealers require special vacuum pouches.
- Tip: Determine the film thickness, composition, and sealing temperature range needed for your product packaging.
Seal Width and Length
- Why It Matters: Different sealers offer varying sealing widths and lengths. A narrow seal might suffice for lightweight goods, but heavier or thicker packages often require a broader seal.
- Tip: Consider your package dimensions and contents. Bulkier, heavier items may need a wider seal to hold them securely.
Production Speed & Volume
- Why It Matters: A small business with modest order volumes can thrive with an impulse sealer. Large-scale manufacturing facilities typically need high-speed continuous or automated systems.
- Tip: Estimate your daily, weekly, or monthly output and choose a model that meets or exceeds that capacity for future scaling.
Automation Level
- Why It Matters: Manual and semi-automatic sealers often require more labor, while fully automated systems can operate with minimal human intervention.
- Tip: Balance your budget with labor costs. High-volume operations usually find automated sealers more cost-effective long-term.
Maintenance Requirements
- Why It Matters: Every machine needs care. Some sealers have more parts that can wear out, while others have simpler designs.
- Tip: Check for easy-to-replace parts, reliable customer support, and whether the manufacturer offers service plans.
Safety Features
- Why It Matters: Packaging equipment can pose risks if not properly designed. Look for machines with built-in safety mechanisms like emergency stop buttons, heat shields, and regulated temperature controls.
- Tip: Ensure the model you select complies with local and international safety standards relevant to your industry.
Understanding the Science of Heat Sealing
For many packing sealer systems, heat plays a crucial role in the sealing process. Knowing a bit about the science can help you troubleshoot issues, optimize machine settings, and maintain consistent quality.
- Melting Point of Packaging Material
Each plastic or polymer has a unique melting point. If the temperature is too low, the seal won’t bond properly. If it’s too high, you risk burning or weakening the material. - Dwell Time
Dwell time refers to how long the sealing bar remains in contact with the material. Adjusting this correctly is critical for forming a secure seal without damaging the plastic. - Pressure
Pressure ensures the layers bond after being heated. Improper pressure—too low or too high—can result in weak seals or rippled edges. - Cooling Period
Sealing surfaces need adequate time to cool before moving the package. This “cool down” ensures the plastic sets firmly, preventing any immediate seal breakage.
Step-by-Step Guide to Operating a Basic Packing Sealer
While each machine has its own specifics, the following generalized steps apply to many packing sealer models. Always consult your equipment manual for exact guidelines.
- Prepare the Sealing Area
- Clear any clutter to avoid obstructions.
- Ensure the area is clean and free of dust or moisture.
- Power On and Set Parameters
- Adjust temperature settings according to the packaging material.
- Set dwell time or conveyor speed for continuous band sealers.
- Check that pressure settings match your bag thickness.
- Position the Package
- Place the open end of the bag or pouch under the sealing bar (for impulse sealers) or on the conveyor (for continuous sealers).
- Ensure a straight alignment for a uniform seal.
- Activate the Machine
- For impulse sealers, press down the sealing bar until the indicator light switches off. For continuous sealers, allow the bag to move along the conveyor.
- Vacuum sealers require you to close the lid and let the pump remove air before sealing.
- Inspect the Seal
- Check for wrinkles, incomplete bonding, or burn marks.
- Perform quick stress tests (light tug) to ensure the integrity of the seal.
- Shut Down and Clean
- Turn off the machine if you won’t be using it for an extended period.
- Wipe down the sealing bar and any surfaces to remove residues.
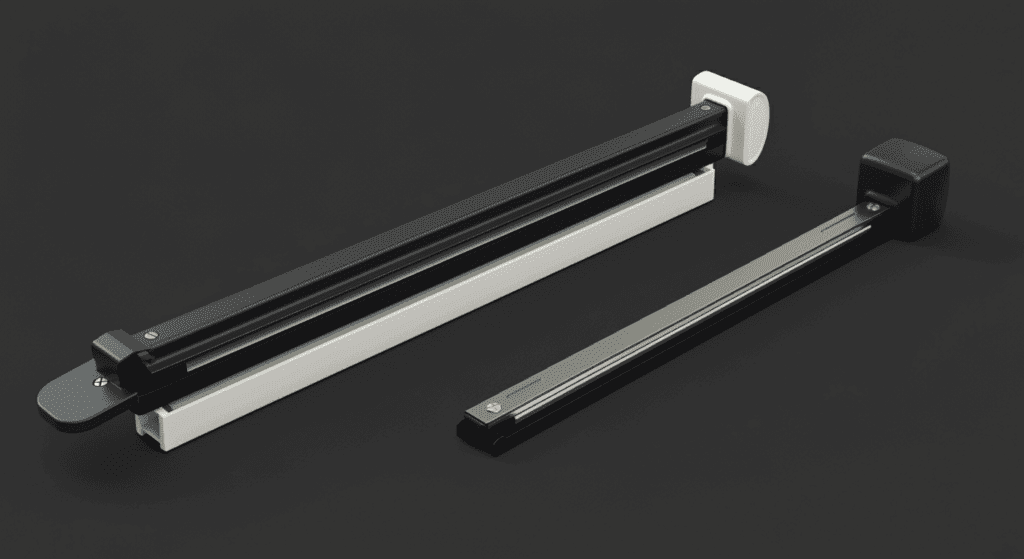
Best Practices for Prolonging the Life of Your Packing Sealer
Owning a packing sealer can be a substantial investment. Proper care and maintenance can significantly extend its service life and maintain quality performance.
Regular Cleaning
- What to Do: Remove any plastic buildup or debris on the sealing surface after each use. Residue can interfere with heat transfer and degrade seal quality.
- How Often: Ideally after every production run. At minimum, perform a thorough cleaning at the end of each day.
Lubrication and Calibration
- What to Do: Some machines have moving parts that require lubrication. Over time, repeated use can cause parts to shift slightly, leading to uneven seals or misalignment.
- How Often: Follow the manufacturer’s guidelines—some recommend weekly checks, while others might be monthly.
Inspect Wearable Parts
- What to Do: Sealing wires, Teflon strips, and conveyor belts can wear down over time. Regularly inspect them for fraying or damage.
- How Often: Monthly or after high-volume runs. Replace parts immediately if you notice any significant wear.
Maintain Optimal Temperature Control
- What to Do: Monitor your machine’s thermostat to ensure it remains accurate. Calibrate if you notice inconsistent seal quality.
- How Often: At least once every quarter or as indicated by the machine’s performance.
Keep Spare Parts on Hand
- What to Do: Stock essential replacement parts like sealing wires, Teflon tapes, and fuses.
- Why: Downtime can be costly. Having spares ensures minimal disruption to your production line if parts fail unexpectedly.
Advanced Technologies and Innovations in Packing Sealers
As with many industries, sealing technology is continually evolving. Modern packing sealer models often incorporate innovations designed to enhance speed, reduce energy consumption, and deliver airtight results.
Smart Sensors and Automation
- Benefits: Sensors detect the exact thickness of the material and automatically adjust temperature and pressure. Real-time monitoring ensures minimal human error.
IoT Integration
- Benefits: Internet-connected sealers can provide performance analytics and predictive maintenance alerts. This proactive approach can prevent breakdowns before they occur.
Ultrasonic Sealing
- Overview: Instead of heat, ultrasonic sealers use high-frequency vibrations to fuse materials.
- Advantages: No risk of burns or scorching, and the process is often faster with less energy consumption.
Eco-Friendly Sealing Materials
- Trend: Packaging suppliers are offering compostable or biodegradable films, aligning with growing sustainability demands.
- Impact: Businesses can adopt greener practices without compromising on seal strength or reliability.
Common Pitfalls and How to Troubleshoot
Even the most reliable packing sealer can encounter hiccups. Here’s how to troubleshoot common issues:
- Weak or Incomplete Seals
- Cause: Temperature too low, insufficient dwell time, or poor pressure.
- Solution: Increase temperature incrementally, extend dwell time, or check for obstructions preventing adequate pressure.
- Burn Marks or Melting
- Cause: Temperature too high or dwell time is too long.
- Solution: Lower the heat setting or reduce dwell time to avoid overheating the material.
- Wrinkled Seals
- Cause: Excessive pressure or bag misalignment.
- Solution: Decrease pressure settings and ensure the material lies flat before sealing.
- Air Leaks in Vacuum Seals
- Cause: Punctures in the bag, worn-out sealing wire, or incorrect vacuum cycle.
- Solution: Replace the bag if damaged, inspect and replace worn wires, and verify the vacuum settings for your bag thickness.
- Machine Overheating or Frequent Shutdowns
- Cause: Overuse, blocked vents, or electrical faults.
- Solution: Allow the unit to cool, clean ventilation ports, and check the electrical connections.
Packaging Regulations and Quality Control
In some industries—especially food, pharmaceuticals, and medical devices—packing sealers play a crucial role in regulatory compliance. Here’s what you need to know:
Food Safety Standards
- Compliance: Agencies like the FDA often require packaging materials and processes to meet specific sanitation and seal integrity standards.
- Best Practice: Use food-grade materials and ensure the machine’s design prevents any contamination (e.g., easy-to-clean surfaces).
Pharmaceutical Guidelines
- Requirements: Certain medications need tamper-evident seals. Vacuum packaging or specialized seals can confirm product integrity.
- Tip: Keep detailed records of sealing temperatures and times for traceability.
Quality Control Inspections
- Purpose: Routine checks guarantee that every package meets the required standards.
- Process: Random sampling of sealed products, performing stress tests, and verifying seal uniformity.
FAQs About Packing Sealer
Below are answers to some of the most frequently asked questions. These insights will help you achieve a better understanding of packing sealers, troubleshoot effectively, and optimize your workflow.
Q1: Can I use the same packing sealer for different bag materials?
A: It depends on the sealer’s specifications. Some sealers can handle a range of materials (like PE, PP, and laminated films) as long as you adjust the temperature. Always confirm with the manufacturer.
Q2: How do I know if my seal is strong enough?
A: Perform a manual stress test by gently tugging both sides of the seal. If it holds without separating or wrinkling, it’s likely sufficient. For stricter quality control, use a burst tester or specialized equipment to measure seal strength.
Q3: Are vacuum sealers worth the investment for non-food products?
A: Absolutely. While vacuum sealers are popular for food preservation, they’re also invaluable for protecting electronics, precision parts, and items sensitive to moisture or oxidation.
Q4: Do I need a special plug or power supply for high-powered sealers?
A: High-capacity or industrial sealers may require dedicated electrical circuits or specific voltage requirements. Always check power specifications to ensure a safe setup.
Q5: How long should a properly maintained packing sealer last?
A: With regular cleaning, part replacement, and correct usage, a quality packing sealer can last upwards of 5-10 years or more. Maintenance is key to extending its operational life.
More References:
- World Packaging Organisation (WPO) – International body for packaging standards and innovations.
- Institute of Packaging Professionals (IoPP) – Industry research, certifications, and educational resources.
How to Implement Schema Markup for Packing Sealer Content
Schema markup can boost your visibility on search engines and increase your chances of earning a Featured Snippet. For packing sealer content:
- Article Schema: Identifies your post as a comprehensive article, enhancing its chances of ranking.
- FAQ Schema: Mark up the FAQ section to help search engines display rich results and direct readers to your answers quickly.
- How-To Schema: If you’ve included step-by-step instructions (as above), consider adding How-To schema to highlight this section.
Conclusion: Elevate Your Packaging Process with the Right Packing Sealer
A packing sealer is more than just a machine—it’s an investment in product quality, brand reputation, and operational efficiency. By choosing the right type of sealer, properly maintaining it, and staying updated on the latest packaging innovations, you can significantly reduce product damage, meet regulatory requirements, and keep your customers happy. Whether you’re a small business owner shipping handcrafted items or a major manufacturer dealing with high-volume orders, the right packing sealer can streamline your workflow and give you a competitive edge.
Remember, a reliable seal protects not only your products but also your relationship with customers. We hope this guide has illuminated the key considerations, technologies, and best practices for selecting and using a packing sealer effectively. If you have any questions, suggestions, or experiences to share, we’d love to hear from you. Reach out, leave a comment, or share this post with others who might benefit from learning more about packing sealers. By taking these expert-backed steps, you’ll be well on your way to packaging success—one impeccable seal at a time.
Stay Connected with EngiTech
EngiTech is your trusted source for in-depth knowledge on industrial mechanical engineering machines and technologies. Stay ahead with the latest innovations, expert insights, and practical guides designed to help you make informed decisions for your business and engineering needs. Join our growing community of professionals and industry leaders to stay updated and competitive in the ever-evolving world of industrial technology.