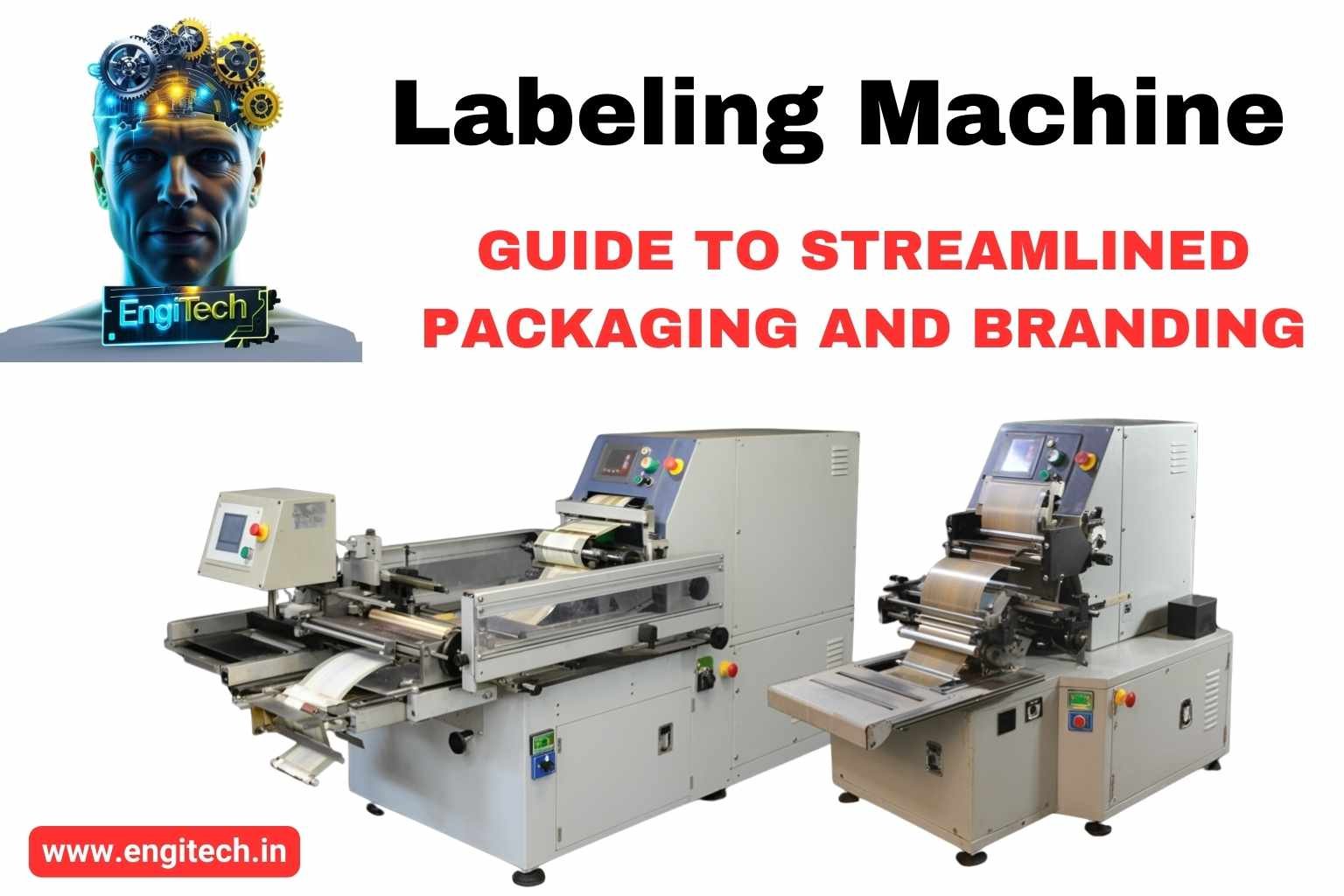
In this in-depth guide, we’re going to explore every aspect of labeling machines, from their core functions and technology to troubleshooting tips, cost considerations, and advanced strategies for optimizing your production line. Whether you’re a brand-new entrepreneur dipping your toes into the world of product packaging or a seasoned production manager seeking to update and streamline operations, this guide will provide all the insights you need to harness the power of labeling machinery. By the end, you’ll know exactly which labeling system suits your needs, how to maintain it, and how to use it to propel your business forward in an increasingly saturated marketplace.
Have you ever wondered why some products practically jump off the shelf and grab your attention while others remain overlooked? A major part of that shelf appeal rests on how well a product is labeled. In today’s hyper-competitive marketplace, a top-quality labeling machine can make all the difference, ensuring consistent, professional, and legally compliant labels for your products. From small-scale operations to massive manufacturing lines, businesses depend on reliable labeling equipment to meet consumer demands, stand out on crowded store shelves, and maintain compliance with ever-changing regulations.
Table of Contents
1. Understanding Labeling Machines
A labeling machine is specialized equipment designed to dispense and apply labels—such as product descriptions, branding details, barcodes, and regulatory information—onto various types of packaging, containers, or products. It handles tasks that might otherwise be performed manually, drastically reducing errors and improving throughput.
From small manual devices for limited-volume tasks to large-scale automatic labeling machine setups integrated with high-speed production lines, these solutions have become indispensable in a broad range of industries. If you’ve ever received a food item with a nutritional fact label or purchased a bottle of water with a perfectly aligned sticker, chances are that the label was applied by a professional labeling system.
Why Automated Labeling Is Critical
- Consistency: Uniform placement across thousands (or even millions) of products.
- Speed: Automated machines can label at rates impossible to achieve by hand, enhancing operational efficiency.
- Accuracy: Reduced errors in label placement or misprints, saving costs and protecting brand image.
- Regulatory compliance: Ensures correct labels with mandatory information like batch codes, expiry dates, or disclaimers are placed accurately.
By streamlining these tasks, labeling equipment frees up labor resources for other critical responsibilities, such as quality control, product innovation, and customer engagement.
2. Why Labeling Matters in Modern Industries
It’s easy to underestimate the power of a simple label—until you realize how deeply it affects consumer perception, compliance with regulations, and brand identity. For instance, the Food and Drug Administration (FDA) mandates strict labeling guidelines in the food and pharmaceutical sectors. Meanwhile, a strong label design can communicate the value and uniqueness of your product in mere seconds.
Impact on Branding and Marketing
- Brand Recognition: A well-designed label instantly signals what your brand stands for.
- Shelf Appeal: Bold, clear labels catch the eye and help differentiate your products in competitive retail environments.
- Customer Trust: Transparent and accurate product information reassures consumers, building confidence and loyalty.
Enhancing Operational Efficiency
- Inventory Management: Barcodes and QR codes speed up scanning and tracking.
- Regulatory Compliance: Automated labeling ensures correct data placement and reduces human error.
- Scalability: As your business grows, an industrial labeling machine can expand capacity without sacrificing quality.
When labels are done right, they bridge the gap between your product’s physical presentation and consumer trust, making labeling machines crucial investments for sustained growth.
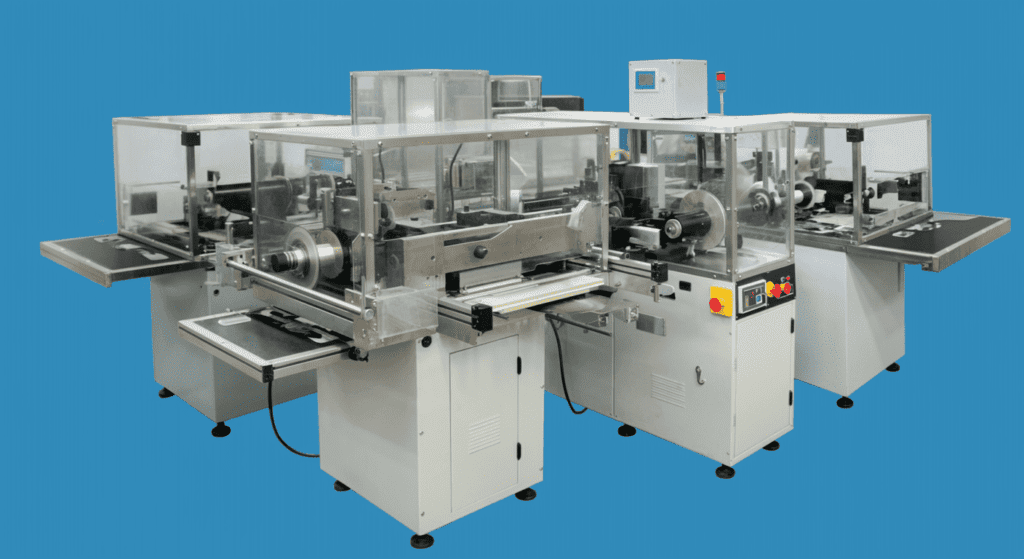
3. Core Components of a Labeling Machine
Though there are countless labeling machine designs, most systems include a few essential components:
- Label Dispenser or Feeder: Releases labels from a roll or sheet.
- Applicator: Places the label onto the container or product. May use a brush, tamp, or air-blast mechanism.
- Conveyor System (if Automatic): Moves products or containers to the application point at a controlled speed.
- Sensors and Controls: Detect container position and synchronize label release.
- Printer (Optional): Some machines can print date codes, batch information, or barcodes right before application.
- Rewind/Reel Mechanism: Collects the backing paper after labels have been dispensed.
Each element works in harmony, ensuring consistent label placement, maintaining production speed, and minimizing downtime. When evaluating a machine, paying attention to these components can reveal much about reliability, maintenance requirements, and suitability for your production line.
4. Types of Labeling Machines
To select the right labeling system, you must understand the different categories commonly available on the market.
4.1 Pressure-Sensitive Labeling Machines
The most widespread type, these machines apply labels that are already coated with an adhesive. Once the label’s backing is peeled away, it’s ready for immediate application.
Key Advantages
- Quick and easy to set up
- Versatile for various container shapes
- Minimal mess compared to glue-based systems
4.2 Hot Melt Glue Labeling Machines
In this category, hot glue is applied to either the label or the container. The label adheres to the product once the glue sets.
Key Advantages
- Ideal for high-speed lines
- Commonly used for wrap-around labels
- Can handle a variety of label materials
4.3 Shrink Sleeve Applicators
Shrink sleeve labeling uses a plastic sleeve that is placed over the product and then shrunk to fit its shape using heat or steam tunnels.
Key Advantages
- 360-degree branding and information space
- Tamper-evident capabilities
- Unique shapes can be labeled with ease
4.4 Print and Apply Labeling Machines
These systems print variable data (like batch codes, barcodes, and real-time info) just before the label is placed on the product.
Key Advantages
- Perfect for on-demand labeling
- Reduces wasted labels due to design changes
- Highly customizable for different runs
4.5 In-Line vs. Rotary Labeling Machines
- In-Line Labeling Machines: Move products in a straight line along a conveyor. They are simpler to set up and more affordable but can be slower than rotary solutions.
- Rotary Labeling Machines: Products are positioned on rotating carousels that can handle high-speed labeling with greater precision, frequently used in large-scale bottling or canning lines.
Understanding the distinctions between these labeling machine types helps you match the best fit to your production requirements, product type, and budget constraints.
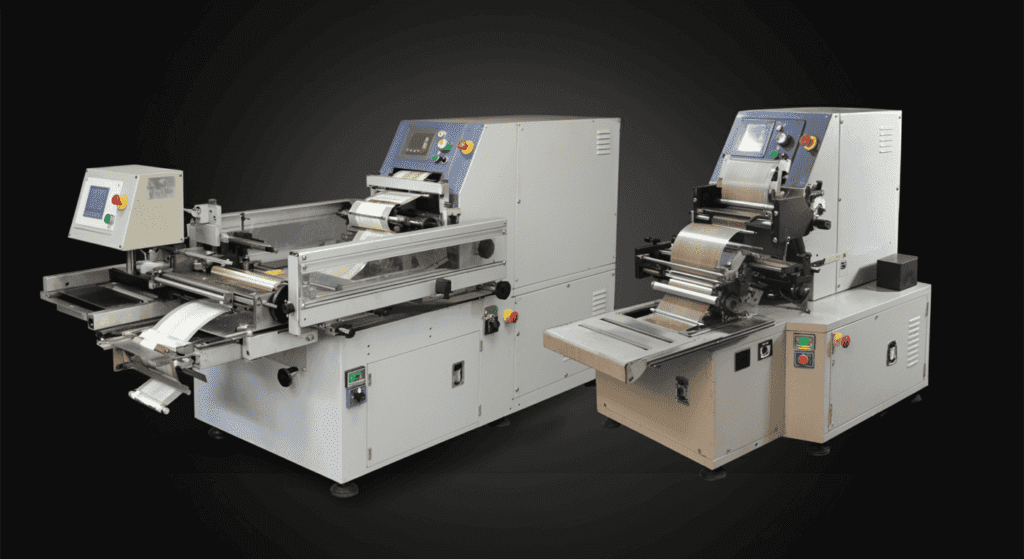
5. Choosing Between Manual, Semi-Automatic, and Automatic Systems
5.1 Manual Labeling Machines
Best For: Very small businesses or artisanal operations where the production scale is limited.
Pros:
- Low upfront cost
- Simple to operate
- Minimal maintenance
Cons: - Labor-intensive
- Slower output
- Inconsistent application possible
5.2 Semi-Automatic Labeling Machines
Best For: Small to medium-scale production where some automation is desired, but the full capabilities of a high-end machine are not yet necessary.
Pros:
- Faster than manual methods
- Less prone to errors
- Affordable compared to fully automated systems
Cons: - Requires an operator to load and align products
- Throughput remains limited
5.3 Automatic Labeling Machines
Best For: Mid to large-scale manufacturers that prioritize speed, precision, and scalability.
Pros:
- Maximum output
- Minimal labor involvement
- High accuracy and consistency
Cons: - Higher initial investment
- Requires technical expertise for setup and maintenance
Choosing the right level of automation hinges on your production volume, labor resources, and long-term growth strategy. It often makes sense to invest in an automatic labeling machine if you anticipate scaling up to meet rising demand.
6. Key Considerations Before Purchasing a Labeling Machine
Before diving into any major equipment purchase, it’s crucial to assess your unique requirements and constraints.
- Production Volume
- Estimate the number of products you need to label per day, week, or month.
- Project your future growth to avoid outgrowing your machine too soon.
- Container Shape and Size
- Cylindrical bottles? Square containers? Unique shapes?
- Ensure your labeling system can handle these variations effectively.
- Label Type
- Pressure-sensitive, glue-based, shrink sleeves, etc.
- Consider any special finishes, textures, or adhesives.
- Integration With Existing Lines
- How easily can the new machine slot into your current production layout?
- Check compatibility with conveyor speeds and upstream/downstream equipment.
- Regulatory Demands
- Some industries require precise date codes or tamper-evident labels.
- Confirm that your chosen system can handle these requirements.
- Maintenance and Technical Support
- Factor in the availability of spare parts, service technicians, and documentation.
- Look for a supplier with reliable customer support for minimal downtime.
- Budget and ROI
- Price is important, but so is the return on investment.
- Calculate labor savings, error reduction, and potential for increased throughput.
By considering these aspects thoroughly, you can shortlist labeling machines that match both your operational demands and financial parameters, setting yourself up for smoother production and fewer headaches.
7. Step-by-Step Guide to Label Application
Even with an advanced industrial labeling machine, proper setup and procedure remain critical for optimal results. Below is a high-level overview:
- Preparation of Containers
- Clean and dry all surfaces to remove dirt, dust, or oil.
- Align containers so they are stable and ready for conveyor movement.
- Label Roll Setup
- Ensure the label roll is correctly mounted and threaded through the dispenser.
- Check tension and alignment to avoid label slippage or wrinkling.
- Sensor Calibration
- Calibrate sensors to detect gaps between labels, container position, and the product’s leading edge.
- Run test cycles to confirm accurate detection.
- Applicator Adjustment
- Depending on the label type, fine-tune air pressure (for air-blow systems) or tamping pressure (for tamp applicators).
- Verify the correct angle for label contact.
- Test Run
- Start the machine at a low speed to test label placement on a few sample containers.
- Make micro-adjustments to placement and tension if needed.
- Increase Throughput
- Gradually increase speed to operational levels once confident in accuracy.
- Continuously monitor for misalignment or feed issues.
- Ongoing Quality Checks
- Regularly inspect labels, verifying placement, adhesion, and print clarity.
- Keep an eye on sensor performance and alignment to catch minor issues early.
By following these steps, even high-speed lines can maintain near-perfect labeling accuracy, preserving brand image, cutting down reworks, and staying in compliance with labeling regulations.
8. Regulatory and Compliance Factors
Different industries have different mandates, so a thorough understanding of compliance is vital. Here are a few key considerations:
- FDA Regulations (Food & Pharma): Nutritional facts, ingredient lists, and dosage instructions must be legible and accurate.
- EU Labeling Laws: Include clear allergen information, usage guidelines, and disclaimers.
- Hazardous Substances Labeling: Chemicals and industrial products often require specialized labeling to communicate risks and safe handling instructions.
- Barcoding and Serialization: Certain sectors need unique barcodes or serial numbers to trace products through the supply chain.
Failing to comply can result in costly recalls, legal penalties, and damage to brand reputation. A robust labeling machine, equipped with print-and-apply features or advanced vision inspection systems, can automatically verify compliance with minimal human involvement.
9. Cost Implications and ROI
Upfront Costs
- Machine Purchase: Varies by brand, capacity, level of automation, and extra features.
- Installation and Training: Technicians may charge extra, or you might require travel expenses.
- Spare Parts and Consumables: Label rolls, adhesives, and printer ribbons can add to monthly overhead.
Long-Term Savings
- Reduced Labor Costs: Automated systems free up staff for more strategic tasks.
- Lower Error Rates: Mistakes can be expensive, especially if large batches are mislabeled.
- Scalability: Easily ramp up production without purchasing an entirely new system.
Calculating ROI
- Compare the cost of manual labeling (labor + error) versus the investment in automation.
- Factor in growth projections: if you aim to double production in a year, an automatic machine might pay for itself more quickly.
- Assess intangible benefits like improved brand reputation and faster time to market.
Many businesses find that the transition to an automatic labeling machine pays for itself in under a year, particularly if they operate in a fast-moving consumer goods sector where efficiency is paramount.
10. Common Challenges and Troubleshooting
Even top-of-the-line labeling machines can experience hiccups. Below are some typical issues and potential fixes:
- Label Misalignment
- Cause: Incorrect tension or miscalibrated sensors
- Solution: Adjust tension settings, re-check sensor positioning, or clean sensor surfaces
- Wrinkled or Torn Labels
- Cause: High-speed application, poor surface contact, or dusty environment
- Solution: Slow down the application speed slightly, clean surfaces, and ensure even pressure
- Jamming
- Cause: Overlapping labels on the dispenser or improper threading
- Solution: Re-thread the label roll and confirm the correct path, check for debris in the dispenser
- Adhesive Failures
- Cause: Low-quality labels or unsuitable adhesive for container material
- Solution: Use labels designed for your container’s material, store them in a climate-controlled environment
- Printer Malfunctions (in print-and-apply systems)
- Cause: Low ink ribbon tension, misaligned print head, or firmware glitches
- Solution: Realign the print head, replace the ribbon, or update firmware per manufacturer instructions
Routine maintenance schedules, proper staff training, and using recommended consumables from reputable suppliers can minimize these challenges, keeping your labeling machine running smoothly.
11. Advanced Features and Emerging Trends
The packaging and labeling sector evolves constantly with technology. Here are some cutting-edge features gaining popularity:
- Vision Inspection Systems
- Verify label presence, position, and print accuracy in real time.
- Ideal for critical industries like pharmaceuticals.
- IoT and Predictive Maintenance
- Sensors within the machine collect data to predict part failures or lubrication needs.
- Reduces unexpected downtime by signaling maintenance tasks before issues arise.
- Multi-Panel and Wrap-Around Labeling
- Innovative designs allow for multiple labels or full 360-degree coverage to maximize branding space.
- RFID Integration
- Embedding radio-frequency identification tags for advanced inventory control and anti-counterfeiting measures.
- Sustainability Initiatives
- Eco-friendly label materials and adhesives that reduce environmental impact.
- Machines optimized for thinner or compostable label substrates.
Staying ahead of these trends can significantly elevate your brand’s market position. Upgrading your labeling system to include advanced features not only improves product presentation but also future-proofs your operation against shifting consumer demands and regulations.
12. Industry-Specific Labeling Requirements
While most labeling principles are universal, certain sectors impose unique stipulations:
12.1 Food & Beverage
- Nutrition and Allergen Disclosures: Must be prominently displayed per FDA or regional authority guidelines.
- Expiration Dates: Highly regulated in many markets.
12.2 Pharmaceuticals & Healthcare
- Precision & Legibility: Mislabeling can be life-threatening, so scanning and vision systems are often mandatory.
- Serialization & Track-and-Trace: Each product may need a unique code for supply chain tracking.
12.3 Cosmetics
- Ingredient Lists: Must be clearly stated, often in multiple languages.
- Regulatory Warnings: For products like hair dyes or chemical peels, additional disclaimers may be required.
12.4 Chemical & Industrial Goods
- Hazard Symbols: OSHA or GHS-compliant symbols must be placed.
- Durability of Labels: Labels often require water resistance, UV resistance, or chemical-proof materials.
Understanding the specifics of your industry is crucial for selecting a labeling machine that can handle specialized label materials, printing needs, and quality checks.
13. Maintenance and Longevity Best Practices
To maximize the lifespan of your labeling machine and ensure minimal downtime:
- Regular Cleaning
- Wipe down sensors, rollers, and conveyor belts to remove dust and label residue.
- Keep a maintenance log detailing cleaning schedules.
- Scheduled Lubrication
- Moving parts such as gears and bearings require regular lubrication.
- Over-lubrication can attract dust, so follow manufacturer guidelines precisely.
- Software and Firmware Updates
- If your machine has digital controls, keep the software current to benefit from performance improvements and bug fixes.
- Spare Parts Inventory
- Stock critical components (belts, sensors, motors) to minimize downtime when failures occur.
- Develop a relationship with a reliable supplier.
- Operator Training
- Well-trained staff can spot minor issues before they escalate.
- Periodic training updates keep operators current on best practices.
A proactive approach ensures your automatic labeling machine or semi-automatic system keeps running at peak efficiency, saving you time and money in the long run.
14. FAQs About Labeling Machines
Below are frequently asked questions to help clarify common points of confusion:
Q1: How do I decide between pressure-sensitive and glue-based labeling?
A1: Pressure-sensitive labeling machines are typically simpler and cleaner, making them ideal for most general applications. Glue-based machines, on the other hand, excel in high-speed environments and can handle specialized label materials like paper labels for wrap-around bottle labeling.
Q2: Can a single machine label multiple container sizes and shapes?
A2: Many advanced labeling machines are quite versatile and can handle different shapes and sizes with minimal adjustments. However, extremely varied container designs might require multiple labelers or specialized change parts.
Q3: What is the expected lifespan of a quality labeling machine?
A3: With proper maintenance and periodic upgrades, a good machine can last 10-15 years or more. Regular cleaning, lubrication, and part replacements are essential to ensure longevity.
Q4: How quickly can an automatic labeling machine operate?
A4: High-speed industrial labeling machines can reach speeds of several hundred labels per minute, depending on the complexity of the application and packaging line constraints.
Q5: Is it worth integrating print-and-apply technology into my system?
A5: If you frequently need to update label information—such as batch numbers, barcodes, or variable data—then print-and-apply can save significant costs on pre-printed labels and reduce waste.
Conclusion
Labeling may seem like a minor detail in the grand scheme of product development and supply chain management, but it holds undeniable weight in customer perception, regulatory compliance, and brand trust. A robust labeling machine ensures that each product rolling off your line meets a professional standard that not only complies with industry regulations but also resonates with your target audience.
As competition grows fiercer, investing in the right system—whether a manual setup for artisanal goods or a fully automatic labeling machine integrated with a state-of-the-art vision inspection platform—can drastically improve your operational efficiency and brand credibility. When you’re ready to explore solutions tailored to your business, begin by reviewing your production volumes, container designs, and budgetary constraints. Conduct thorough research, engage with reputable suppliers, and don’t hesitate to seek expert consultation if needed.
Before you finalize your decision, consider the long-term return on investment. Upgrading your labeling machine may come with an upfront cost, but the benefits often pay off in the form of reduced errors, boosted production rates, and enhanced consumer trust. In many cases, achieving that streamlined operation can position your brand favorably, helping you stand out and scale in an ever-evolving marketplace.
Stay Connected with EngiTech
EngiTech is your trusted source for in-depth knowledge on industrial mechanical engineering machines and technologies. Stay ahead with the latest innovations, expert insights, and practical guides designed to help you make informed decisions for your business and engineering needs. Join our growing community of professionals and industry leaders to stay updated and competitive in the ever-evolving world of industrial technology.