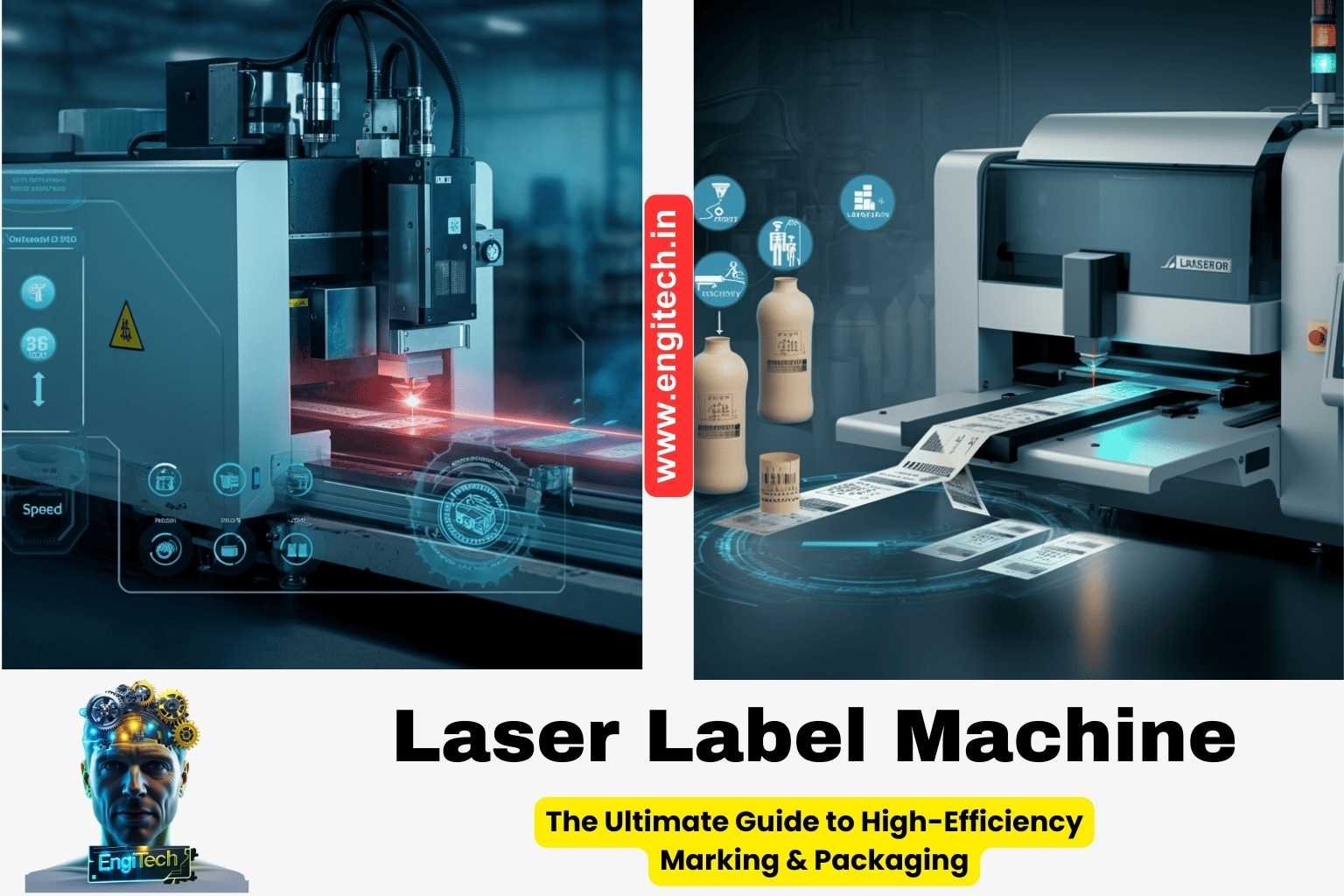
In a world where first impressions are make-or-break, your product’s label can be the deal clincher. Gone are the days when businesses simply slapped a sticker on a box and hoped it would hold up through shipping and handling. Now, laser label machine technology is changing the game—offering stunning precision, speed, and durability. In this comprehensive guide, you’ll learn the ins and outs of laser labeling technology, from how it works to why it’s quickly becoming an essential tool across multiple industries. By the end, you’ll be equipped with the insights and strategies you need to integrate a laser label machine into your operations successfully.
Table of Contents
Introduction: Why Laser Labeling Matters
Labels are more than just a functional add-on; they are an extension of your brand’s identity. Think about the last time you grabbed a product off the shelf because it caught your eye. Often, it’s the label’s design, clarity, and overall presentation that compel us to pick it up. This is where a laser label machine comes in, setting a new standard in quality and durability.
Today’s consumers expect perfection down to the smallest details, and retailers are increasingly strict about package labeling standards. From crisp barcodes to tamper-proof authentication marks, laser labeling meets these high expectations while maintaining efficiency. If you’re aiming for that “wow” factor and a consistent brand image, laser technology can be your secret weapon. In the sections ahead, we’ll dive into exactly why laser labeling stands out and how it can transform your packaging process.
Understanding Laser Label Machines
A laser label machine is a specialized device designed to etch or mark various surfaces with unparalleled precision. Unlike traditional labels that rely on adhesives, ink, or thermal transfer, laser labeling physically alters the surface layer to create a lasting mark. This offers huge benefits in terms of longevity and clarity, especially for products that go through rigorous shipping or are exposed to extreme environments.
The Evolution of Labeling Technology
Labeling technology has come a long way since the days of manual stamping and hand-lettered tags. Initially, businesses relied on mechanical processes like embossing or letterpress printing. Over time, inkjet printers became popular for their speed, while thermal transfer printers offered better durability. However, each of these came with trade-offs—be it in cost, maintenance, or label lifespan. Laser labeling rose to prominence by addressing many of these challenges head-on. Today, it’s often seen as the pinnacle of labeling innovation, merging speed, efficiency, and resilience in one streamlined process.
Common Challenges Solved by Laser Labeling
- Wear and Tear: Ink-based labels often fade over time, especially in harsh environments. Laser markings withstand friction, water exposure, and chemicals far better.
- Costly Consumables: Traditional labeling involves ink, ribbons, or adhesives. Laser systems remove the need for these recurring consumables, saving money in the long run.
- Legibility Issues: A blurred or smudged barcode can lead to logistical nightmares. Laser etching, in contrast, produces crisp, easy-to-scan codes and text.
- Environmental Concerns: Ink cartridges and adhesive-based labels create waste. Laser marking is more eco-friendly, aligning with green initiatives.
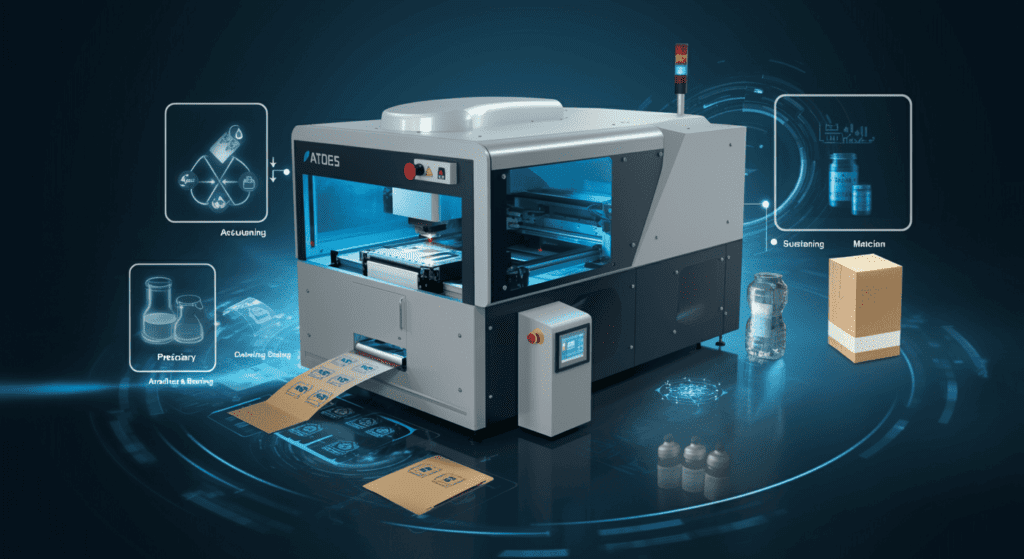
How Does a Laser Label Machine Work?
Laser label machines operate on a fairly straightforward principle but rely on sophisticated technology to make it happen. A laser beam is generated and precisely guided by mirrors or galvanometers to “mark” the surface of the material. Depending on the settings, the laser can either remove a thin layer of material, cause chemical changes to create contrast, or engrave a deep mark for a tactile effect.
The Science Behind Laser Marking
At its core, laser marking involves using concentrated light energy to modify the surface of a material. When a beam of light at a specific wavelength hits a substrate—be it metal, plastic, or glass—it causes localized heating, melting, or vaporization. The exact mechanism can vary:
- Engraving: The laser ablates (removes) the material to create a recessed mark.
- Annealing: Heat from the laser induces changes in the material’s color without removing layers, ideal for stainless steel and titanium.
- Foaming: Tiny gas bubbles are formed in plastic materials, leading to a raised, lighter-colored mark.
Key Components of a Laser Label Machine
- Laser Source: This generates the beam. Common types include CO₂, fiber, and UV lasers.
- Galvo Scanner or Mirrors: Precisely direct the laser beam across the target surface.
- Control Software: Allows operators to adjust settings like speed, intensity, and design layout.
- Cooling System: Prevents the laser from overheating during extended use.
- Enclosure or Housing: Often equipped with safety features like interlocks and viewing windows.
Types of Laser Labeling Technologies
Laser labeling isn’t a one-size-fits-all solution. Depending on your industry and materials, certain laser types may be more advantageous than others. Here’s a look at the three most common laser technologies in labeling and marking.
CO₂ Laser vs. Fiber Laser vs. UV Laser
- CO₂ Laser:
- Wavelength: 10.6 µm (micrometers)
- Best For: Organic materials like wood, paper, certain plastics, and glass
- Pros: Widely available, cost-effective for non-metal applications
- Cons: Not ideal for bare metals without a special coating
- Fiber Laser:
- Wavelength: 1.06 µm
- Best For: Metals (stainless steel, aluminum, copper), hard plastics, and ceramics
- Pros: Extremely efficient, longer lifespan, minimal maintenance
- Cons: Higher initial cost compared to CO₂ lasers
- UV Laser:
- Wavelength: ~355 nm (nanometers)
- Best For: Heat-sensitive materials like certain plastics, glass, and even some electronics
- Pros: Produces very fine, high-contrast markings with minimal thermal damage
- Cons: More expensive and complex, often used in specialized industries (e.g., medical devices)
Industry Applications
- Food and Beverage: Marking expiration dates, batch numbers, and barcodes on packaging.
- Pharmaceuticals: Creating tamper-proof seals and micro-text for anti-counterfeiting measures.
- Automotive: Etching VIN (Vehicle Identification Numbers) and part numbers on metal components.
- Electronics: Labeling circuit boards and plastic casings without damaging internal components.
- Medical Devices: Ensuring sterile, corrosion-free markings on surgical tools and implants.
Each of these industries has specific quality and regulatory requirements, making a laser label machine invaluable for compliance and branding alike.
Key Benefits of Using a Laser Label Machine
1. Speed and Efficiency
A well-tuned laser label machine can mark thousands of items in a single shift without compromising on quality. Whether it’s small text or large logos, lasers operate at high speeds—often completing a mark in seconds. This is especially advantageous in large-scale manufacturing environments where downtime can be costly.
2. Durability and Clarity
Because laser marking physically alters the surface, the resultant label remains intact under conditions that might obliterate ink-based markings. Laser-etched codes remain scannable after exposure to high heat, moisture, chemicals, or abrasives. This durability is critical in fields like aerospace and automotive, where component traceability must remain intact for years.
3. Cost-Effectiveness
Although the initial investment in a laser label machine can be higher than traditional systems, the long-term cost savings are significant:
- No consumables: Eliminate ink, ribbons, or special labeling adhesives.
- Reduced downtime: Fewer mechanical parts that wear out.
- Less waste: No misprints or peeling labels heading to the landfill.
Over time, these savings often justify the upfront expense and offer a strong return on investment.
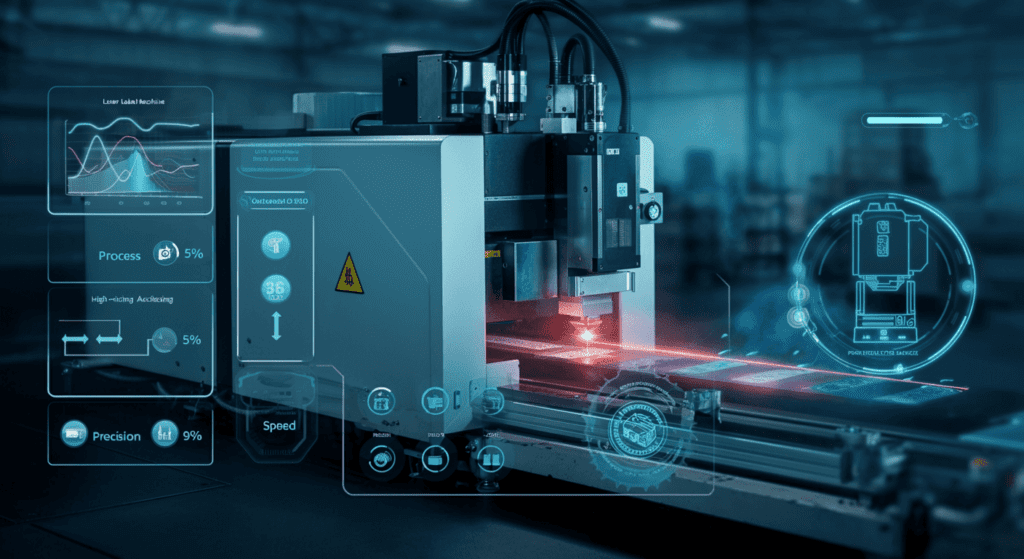
How to Choose the Right Laser Label Machine
Production Volume and Material Compatibility
Start by evaluating your production goals:
- Daily Throughput: How many parts, packages, or products do you need to label each day?
- Material Types: Metals, plastics, paper, glass, or composites—each may require different laser wavelengths.
- Marking Requirements: Do you need deep engraving, or are surface markings sufficient?
Match your needs to a system capable of handling your typical workflow without sacrificing quality. For instance, if you’re predominantly marking metallic parts, a fiber laser is often the best choice. If you’re dealing with packaging materials like cardboard or thin plastics, a CO₂ system might be more cost-effective.
Software and Integration
Modern laser label machines aren’t stand-alone pieces of equipment; they’re integral parts of streamlined production lines. Ensure that:
- Software Integration: The control software supports your preferred graphics file formats (e.g., .EPS, .AI) and can interface with ERP or warehouse management systems.
- User-Friendly Interface: Operators should be able to configure label designs quickly and efficiently.
- Automation Capabilities: If you plan to scale, look for features like conveyor belt integration or robotic arms for material handling.
Maintenance and Safety Considerations
Any high-tech equipment requires periodic checks to sustain optimal performance. Laser systems, in particular, need close attention to safety, given the potential hazards of intense light beams.
Routine Maintenance Routines
- Regular Cleaning: Remove dust or debris from mirrors, lenses, and ventilation systems.
- Alignment Checks: Incorrectly aligned mirrors can diminish marking quality and strain the laser source.
- Software Updates: Keep the control software current to fix bugs and improve performance.
- Professional Servicing: Periodic tune-ups by certified technicians can catch minor issues before they escalate into costly downtime.
Safety Measures and Regulations
Laser labeling equipment generally includes built-in safety features like enclosures and interlocks, but it’s vital to adhere to industry-specific guidelines:
- Laser Safety Classes: Class 1 enclosures are often considered the safest for industrial environments.
- Training: All operators should undergo laser safety training to understand potential risks and emergency procedures.
- Personal Protective Equipment (PPE): Protective eyewear rated for the specific laser wavelength is mandatory when the beam is exposed.
Organizations like OSHA (Occupational Safety and Health Administration) and ANSI (American National Standards Institute) provide comprehensive guidelines on workplace laser safety. Make sure you consult the relevant regulations in your region.
Real-World Success Stories
From automotive giants to boutique craft breweries, the adoption of laser label machines has skyrocketed in recent years. Here are two brief examples that illustrate its transformative impact:
- Automotive Parts Supplier: A supplier specializing in metal engine parts switched from ink-based labeling to fiber laser systems. By eliminating smudged barcodes and mislabeled parts, they reduced returns by 30% and saved thousands of dollars in ink costs each month.
- Artisanal Food Producer: A small organic jam company invested in a compact CO₂ laser label machine to etch expiration dates and batch codes on glass jars. The crisp, permanent markings boosted consumer confidence and met strict retail regulations—leading to a higher acceptance rate from major grocery chains.
These anecdotes highlight how laser labeling can streamline operations and strengthen brand trust, regardless of company size.
Implementing a Laser Label Machine: Step-by-Step Guide
1. Assess Your Business Needs
Begin by outlining your specific objectives:
- Label Complexity: Do you need simple text or intricate graphics?
- Batch Sizes: Large, continuous runs or small custom batches?
- Budget Constraints: Evaluate both capital expenditure and long-term operational costs.
Consult multiple vendors for demonstrations and quotes. Ask about warranty coverage, training, and after-sales support—these details often separate the good suppliers from the great ones.
Internal Linking Tip: For a deeper dive into analyzing production workflows, check out our [Production Optimization Tips] article.
2. Installation and Training
Once you’ve selected your laser label machine, installation typically involves:
- Site Prep: Ensure you have the necessary power supply, ventilation, and space for the enclosure or workstation.
- Calibration: Technicians will calibrate the laser to meet your exact requirements, such as marking depth and contrast.
- Training Sessions: Operators and maintenance staff should receive hands-on training. This is essential for safely running the machine and performing routine upkeep.
During the training phase, encourage your team to ask detailed questions and experiment with different marking parameters. Understanding how to tweak speed, power, and frequency will pay off immensely in production efficiency.
3. Quality Control and Troubleshooting
Even with a top-of-the-line system, hiccups can happen. Common issues include:
- Light Marks: Often indicate that power settings are too low or the laser lens is dirty.
- Overburning: Can result from excessive laser intensity or slow marking speeds.
- Alignment Problems: If your marks shift or appear inconsistent, the galvanometer or mirror alignment might be off.
Implement a quality control protocol that periodically checks marked samples against predefined standards. Keeping a log of your settings can help operators quickly pinpoint and correct issues.
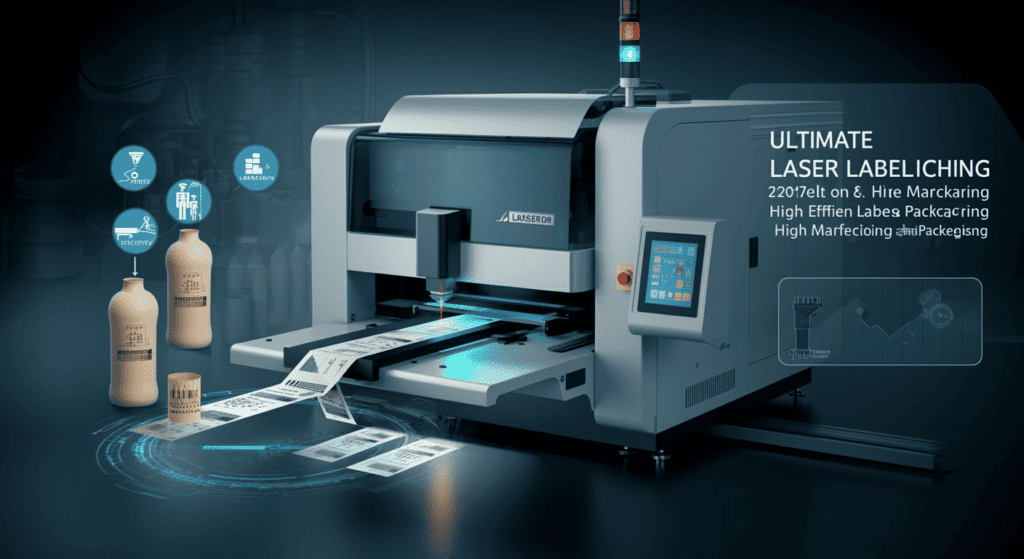
FAQs About Laser Label Machines
- How much does a laser label machine cost?
Prices vary widely, starting from around $10,000 for basic entry-level models and going up to $100,000+ for advanced industrial systems. Factors influencing cost include laser type (CO₂, fiber, UV), wattage, and automation features. - Is a laser label machine faster than traditional labeling methods?
Generally, yes. Laser marking can be extremely quick, especially for smaller labels or text. When properly configured, it often outperforms ink-based methods while maintaining high precision. - Can laser labeling handle color markings?
True color markings are limited. Most laser-etched marks are grayscale or black. However, certain lasers can induce color changes in metals or special plastics. If color is critical to your branding, explore specialized lasers or coatings. - What’s the difference between laser labeling and inkjet printing?
Inkjet printing applies liquid ink on the surface, which can fade or smudge over time. Laser labeling alters the material itself, offering greater permanence, especially in harsh conditions. Inkjet systems require consumables, while laser labeling is largely consumable-free. - Do I need special ventilation for laser labeling?
It depends on the material. Marking plastics or other composites can generate fumes, so a fume extractor or ventilation system is often recommended or required by workplace regulations.
Conclusion: Your Next Steps
A laser label machine isn’t just a purchase—it’s a strategic investment in your brand’s future. By enhancing speed, durability, and overall presentation, laser technology ensures your labels remain legible and visually striking throughout your product’s lifecycle. In industries where precision and compliance can make or break your reputation, laser labeling stands out as the gold standard.
Whether you’re a small business aiming to elevate your packaging game or a large enterprise streamlining high-volume operations, adopting a laser labeling solution could be the move that sets you apart from the competition. Ready to get started? Contact our team today to discuss your specific needs, schedule a demo, or explore our range of laser label machines tailored for different materials and production scales.
Remember, the right laser label machine can be a game-changer. It not only improves labeling quality and consistency but also positions your brand as forward-thinking and quality-obsessed. Make the leap today, and watch your product packaging transform into a key selling point that resonates with both retailers and consumers alike.
Stay Connected with EngiTech
EngiTech is your trusted source for in-depth knowledge on industrial mechanical engineering machines and technologies. Stay ahead with the latest innovations, expert insights, and practical guides designed to help you make informed decisions for your business and engineering needs. Join our growing community of professionals and industry leaders to stay updated and competitive in the ever-evolving world of industrial technology.