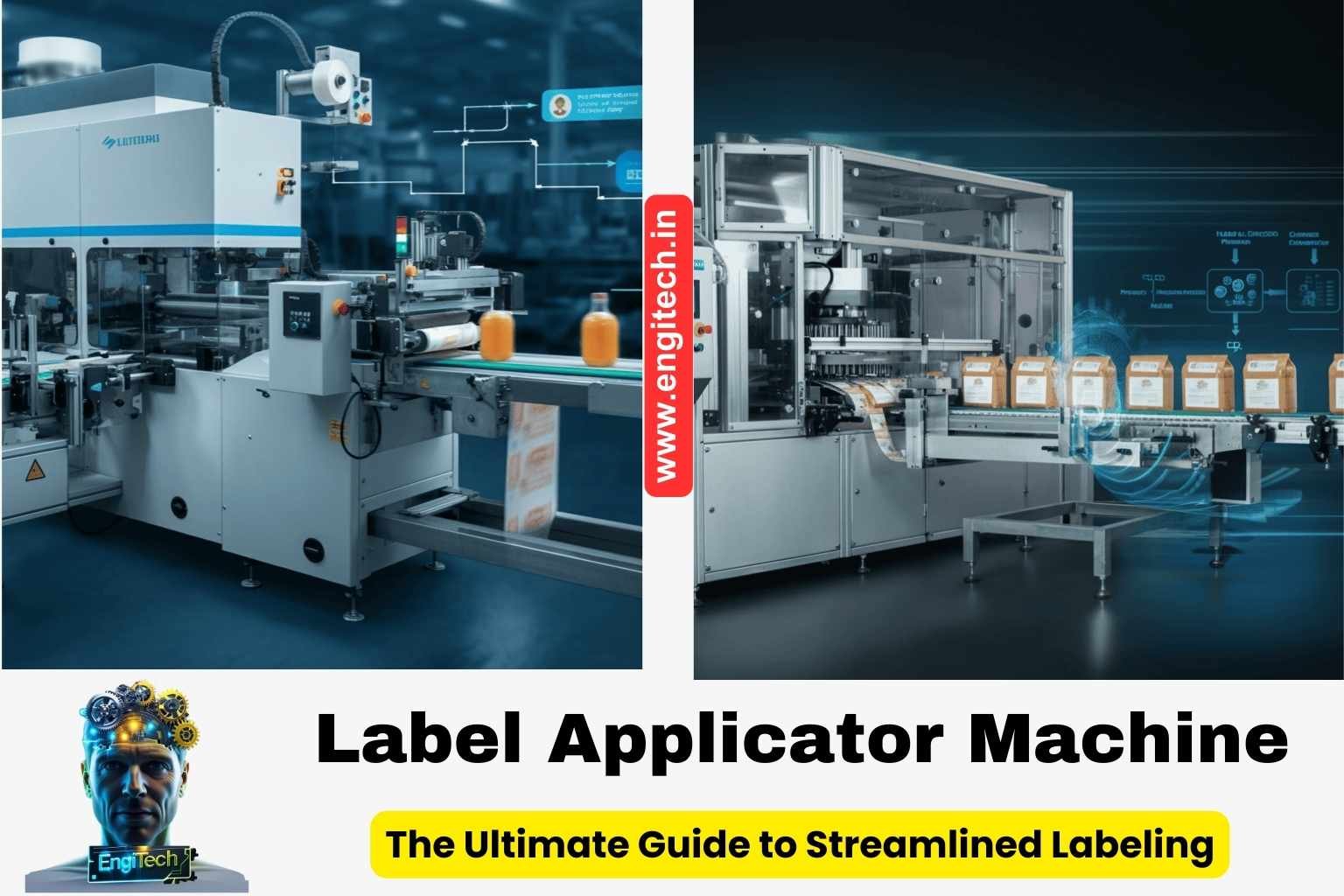
In the ever-evolving world of modern manufacturing and packaging, precision and efficiency are no longer optional—they’re essential. If you’ve ever struggled with inconsistent labeling, wasted materials, or increased labor costs, you’re not alone. Manual labeling methods often lead to misaligned or poorly stuck labels that undermine a product’s professional appearance. Enter the label applicator machine—a game-changer in product identification and branding that offers precision, speed, and streamlined workflows.
In this in-depth guide, we’ll explore every critical aspect of label applicators, from basic principles to advanced automation. Whether you’re a small business striving to project a polished image or a large-scale manufacturer optimizing for high-volume output, this authoritative resource will help you make an informed decision. By the end, you’ll understand what makes a good label applicator machine, how to select the right features, and why investing in the right equipment can catapult your brand credibility and operational efficiency to new heights.
Table of Contents
Introduction: Why Labeling Matters
Picture this: you’re holding two nearly identical bottles of hand sanitizer in your hands. One label is slightly crooked and has bubbles trapped underneath; the other is crisp and aligned perfectly. Which product would you trust more? Labels do more than just provide essential information—they convey a brand’s commitment to quality and attention to detail. A well-labeled product exudes professionalism, helps consumers identify your brand on crowded shelves, and communicates legitimacy and credibility.
But labeling is about more than aesthetics. Labels offer vital compliance information like ingredients, expiration dates, batch numbers, or barcodes. They keep businesses in line with regulatory requirements and help consumers make informed decisions. That’s why investing in a label applicator machine is not just a matter of speed; it’s a matter of ensuring consistent, accurate, and compliant labeling.
What Is a Label Applicator Machine?
A label applicator machine is specialized equipment designed to apply self-adhesive labels onto products, packages, bottles, boxes, or containers. Its core function is to automate or semi-automate the labeling process, reducing manual labor and minimizing errors. Most machines feature mechanisms for peeling labels off their backing and accurately placing them on the desired surface at consistent angles, pressures, and speeds.
How It Works
- Feeding Mechanism: Labels are loaded on a roll or spool.
- Peeling Mechanism: The machine peels the label from its liner or backing paper.
- Application: Using a roller or tamp, it applies consistent pressure to secure the label.
- Advancement: The machine indexes or advances to the next label, ready for the next product.
Depending on the complexity of the equipment, some label applicator machines also integrate printing modules for dynamic data like batch codes and expiration dates.
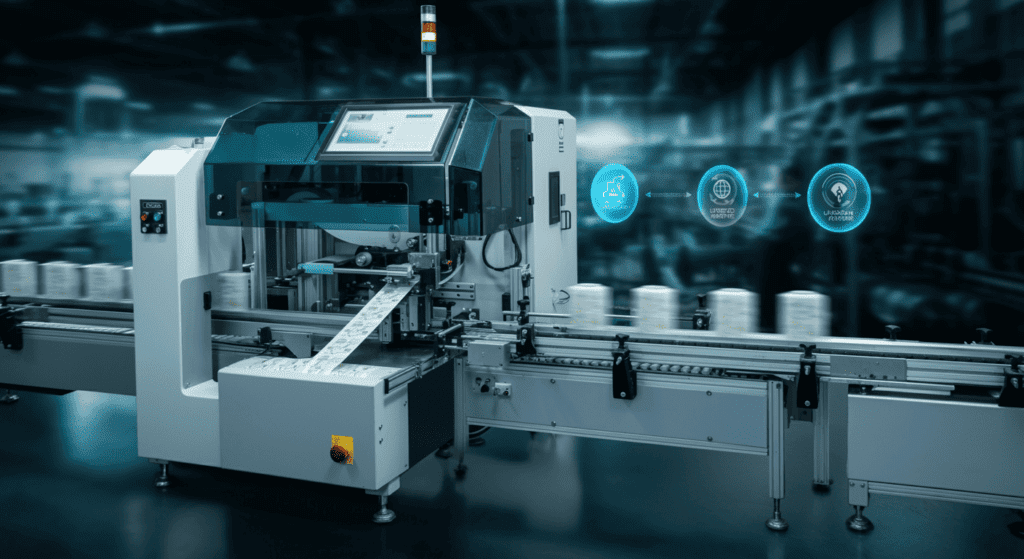
Key Benefits of Using a Label Applicator Machine
Automating the labeling process can feel like a big leap, especially for smaller businesses. However, the rewards go far beyond basic time-saving benefits.
- Consistency and Accuracy
Machines apply the same level of pressure and alignment every single time, ensuring your brand image is always impeccable. - Higher Throughput
A label applicator machine can label hundreds or even thousands of items per hour, far outpacing manual workflows. - Cost Efficiency
While the upfront investment might be significant, long-term operational costs often decrease. You’ll minimize labor expenses, reduce waste from misapplied labels, and optimize output. - Flexibility
Modern applicators can handle various label shapes, sizes, and materials, making them adaptable to multiple product lines. - Regulatory Compliance
Labeling machines that include print-and-apply modules ensure crucial details (e.g., lot numbers, barcodes, nutritional info) are always correct and legible, helping you meet industry standards. - Enhanced Brand Perception
Clean, accurately placed labels scream professionalism, which can sway consumer decisions and encourage repeat purchases.
Types of Label Applicator Machines
The labeling industry offers a wide array of machines, each tailored to different needs and production scales. Understanding the categories can help you zero in on the model that matches your throughput requirements, budget, and level of automation.
1. Semi-Automatic Labelers
- How They Work: An operator typically places a product in position and activates the machine—often with a foot switch or button—to apply the label.
- Ideal For: Small to medium operations where production speed is important but full automation may not be feasible.
- Key Advantage: More affordable than fully automated systems and easier to set up, making them perfect for smaller production runs or startups.
2. Fully Automatic Labelers
- How They Work: These systems feature conveyors that move products along a production line. The machine automatically detects each item’s position and applies the label.
- Ideal For: High-volume operations that demand fast, consistent output.
- Key Advantage: Maximizes throughput and minimizes human intervention, which drives labor costs down.
3. Print-and-Apply Systems
- How They Work: A hybrid solution that first prints variable data (such as batch numbers, barcodes, or product details) and then applies the label to the product.
- Ideal For: Businesses requiring frequent label changes or custom data on each label—common in pharmaceuticals, food manufacturing, or e-commerce packaging.
- Key Advantage: Offers real-time labeling flexibility, making it easy to switch label designs or update product information on the fly.
4. Inline vs. Rotary Labeling Machines
- Inline Labeling Machines:
- Designed to apply labels to products as they move in a straight line.
- Often used for cylindrical or flat surfaces.
- Typically handle moderate speeds but can be scaled up with advanced features.
- Rotary Labeling Machines:
- Position products around a rotating carousel or turret.
- Ideal for complex shapes or high-speed production lines (commonly seen in the beverage industry).
- Provide exact product handling at very high speeds, but tend to be more expensive.
Critical Features to Look For
Selecting the right label applicator machine is an investment. Keep an eye on these features to ensure your choice delivers both immediate and long-term ROI:
- Speed and Throughput
- Machines are often rated by products labeled per minute or hour.
- Consider current production levels and factor in growth projections.
- Label Size Range
- Some machines accommodate only specific label dimensions; others are more versatile.
- Double-check that the system can handle all your current and future label sizes.
- Ease of Integration
- If you already have a packaging line, the label applicator machine must integrate seamlessly with your conveyors, product sensors, and other machinery.
- User Interface and Controls
- Look for intuitive touchscreens or control panels.
- Machines with robust software controls are easier to fine-tune, resulting in fewer errors.
- Material Compatibility
- Ensure the machine supports the types of labels you use (paper, plastic, metallic, etc.) and the product surfaces you need (glass, plastic, cardboard, etc.).
- Print Modules
- If you need variable data printed on each label, confirm that the machine includes or supports print heads from reliable brands.
- Changeover Efficiency
- Frequent product or label changes can bottleneck your operations. A machine that offers quick changeover features (e.g., adjustable guides, tool-free adjustments) saves time.
- Built-In Diagnostics
- Advanced systems offer on-screen troubleshooting, automatic alerts for low label supply, or jam detection to keep your line running smoothly.
- Maintenance and Durability
- Choose reputable manufacturers known for sturdy construction and reliable after-sales support.
- Stainless steel frames are particularly valuable in food, beverage, and pharmaceutical environments.
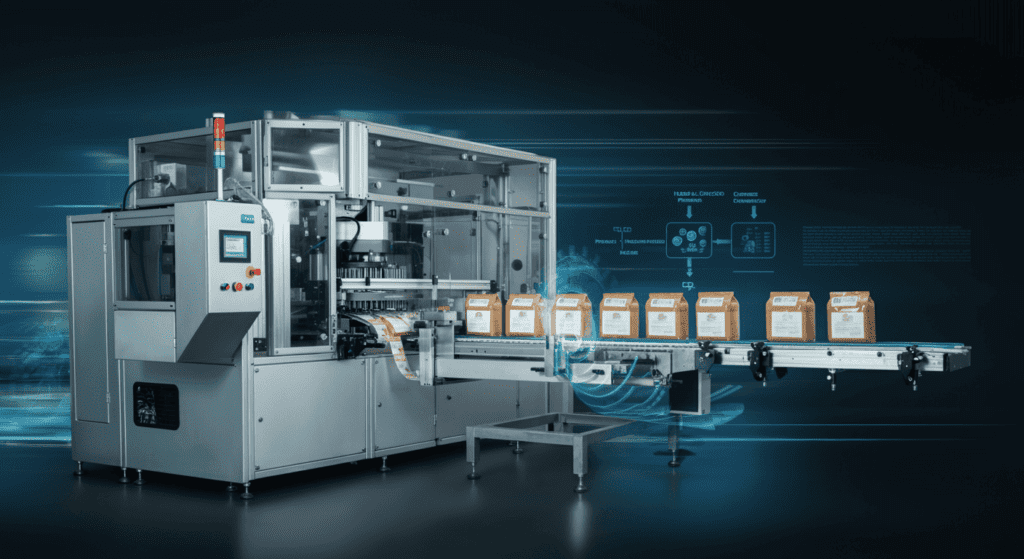
Industry Applications
A label applicator machine is versatile equipment that finds use across multiple industries. Each sector has unique requirements, but the overarching benefit is consistent, professional labeling.
- Food & Beverage
- Bottles, jars, cartons, and flexible packaging.
- Compliance with labeling regulations (e.g., nutritional info, expiration dates).
- High-speed, high-volume lines often use rotary labeling machines.
- Pharmaceuticals
- Critical for batch tracking, safety seals, and detailed product info.
- Print-and-apply systems frequently used to incorporate real-time variable data.
- Must meet stringent compliance standards (e.g., FDA).
- Cosmetics & Personal Care
- Demand for aesthetically pleasing labels that align with brand identity.
- Unique container shapes (e.g., oval, tapered) often require specialized labelers.
- Chemical & Industrial Products
- Drum labeling, hazardous materials labeling, or product warnings.
- Rugged machines needed for harsh industrial environments.
- E-Commerce & Logistics
- Shipping labels, barcodes, and address details.
- Automated print-and-apply systems often integrate with inventory software.
- Automotive
- Parts identification, branding, compliance labeling.
- Durable materials are used for labels to withstand extreme temperatures and wear.
How to Choose the Right Machine for Your Needs
An ill-suited labeler can stall production, inflate costs, and hamper your brand’s presentation. To get it right, analyze your operational constraints, growth trajectory, and specific application requirements:
- Assess Production Volume
- How many products do you label daily, weekly, monthly?
- If you foresee major expansion, choose a machine that can handle higher throughput or be upgraded easily.
- Product Dimensions and Shapes
- Cylindrical bottles vs. rectangular boxes vs. unique shapes.
- Certain labelers are better suited to specific geometry.
- Label Complexity
- Single label vs. front-and-back vs. wrap-around.
- Machines designed for multiple label placements might cost more but prevent future upgrade hassles.
- Budget Considerations
- Factor in purchase price, training, maintenance, and potential downtime.
- A semi-automatic model may suffice for smaller operations, while larger plants might require fully automated solutions.
- Regulatory Requirements
- If your products require detailed information (food, pharma, chemical), a print-and-apply system may be your best bet.
- Trial Runs and Prototyping
- Request a demo or trial run of the machine with your actual labels and products.
- This “try before you buy” approach helps confirm real-world performance.
Installation and Setup Best Practices
Investing in a state-of-the-art label applicator machine is only half the battle. Proper installation and setup ensure you extract every ounce of efficiency and minimize potential downtime.
- Site Preparation
- Ensure adequate floor space and stable, level surfaces.
- Check for proper electrical, air (if pneumatics are involved), and network connections.
- Operator Training
- Knowledgeable staff are less likely to make costly errors.
- Comprehensive training should cover everything from machine operation to basic troubleshooting.
- Calibration and Testing
- After physical setup, run calibration tests.
- Fine-tune label position, conveyor speed, and pressure settings.
- Safety Protocols
- Provide clear signage and user guidelines around the machinery.
- Train operators in emergency stop procedures and safe cleaning methods.
- Integration with Existing Lines
- Synchronize the labeler’s speed with upstream and downstream operations (e.g., filling, capping).
- Use communication protocols (e.g., PLC systems) for seamless performance.
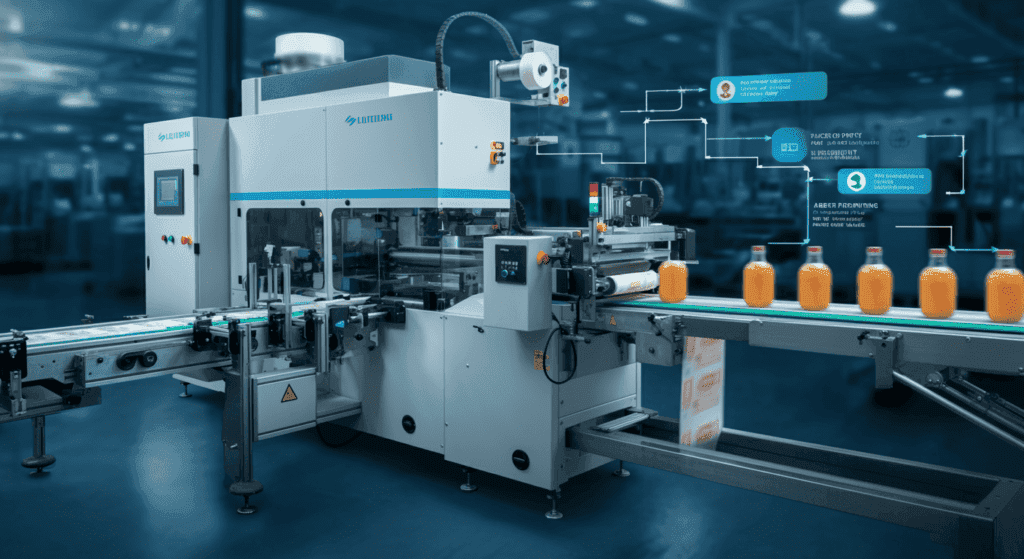
Maintenance and Troubleshooting
Like any mechanical system, label applicator machines require consistent upkeep for optimal performance. A proactive approach can significantly lower total cost of ownership and extend the machine’s lifespan.
- Routine Cleaning
- Remove label residue, dust, or debris that can cause jams.
- Use manufacturer-recommended cleaning agents to avoid damaging sensitive components.
- Scheduled Maintenance
- Adhere to a regular maintenance schedule for lubricating parts, inspecting belts, and replacing wear items.
- Keep an organized record of maintenance activities for accountability and warranty protection.
- Troubleshooting Common Issues
- Label Misalignment: Check roller tension, label sensor calibration, and product guides.
- Frequent Jams: Inspect peeling plate angles, label roll tension, or adhesive buildup.
- Poor Adhesion: Ensure the applicator is applying enough pressure and that environmental conditions (temperature, humidity) are appropriate.
- Spare Parts Inventory
- Keep an inventory of essential spare parts like rollers, sensors, and belts.
- Quick replacement cuts downtime significantly.
- Professional Support
- Partner with manufacturers or authorized dealers offering reliable after-sales support.
- Remote diagnostics and on-site service can save valuable time.
Emerging Trends and Advanced Technologies
As manufacturing and packaging evolve, so do labeling technologies. Staying ahead of these trends not only future-proofs your operations but can also provide a competitive edge.
- Vision and Inspection Systems
- Advanced label applicator machines can integrate cameras to verify label placement, orientation, or presence of required codes.
- Real-time inspection helps maintain quality standards and reduces rework.
- IoT and Smart Connectivity
- Some modern machines offer cloud connectivity for remote monitoring, diagnostics, and software updates.
- Managers can track performance, troubleshoot issues, and update label designs from anywhere.
- Robotics Integration
- Robotic arms can feed products to label applicators or handle complex shapes.
- Ideal for high-speed operations or environments with strict cleanliness standards.
- Sustainability Focus
- Eco-friendly label materials, reduced adhesive usage, and lower energy consumption.
- Many brands now look for “green” labeling solutions to align with corporate social responsibility goals.
- Augmented Reality (AR) for Training
- AR glasses and digital manuals help technicians visualize machine components and perform more efficient diagnostics.
- Can significantly reduce operator errors and training time.
Frequently Asked Questions (FAQ)
Below are some commonly asked questions about label applicator machines. If you’re aiming for a Google Featured Snippet, consider formatting your FAQs with structured data (FAQ schema) to enhance visibility in search results.
- Q: Can I use the same label applicator machine for different container shapes?
A: Many machines are designed with adjustable guides and modular components, making it possible to handle various shapes. However, extreme differences in container geometry may require specialized fixtures or multiple labelers. - Q: How do I maintain the correct label orientation on curved surfaces?
A: Machines equipped with wrap-around labeling modules or advanced alignment sensors can ensure that labels stay straight on cylindrical or curved surfaces. Proper setup and calibration are crucial. - Q: Is a print-and-apply system necessary if I only change labels occasionally?
A: Print-and-apply is best for real-time data and frequent label changes. If your labels rarely change, a simpler applicator might suffice. However, consider long-term needs as your product line evolves. - Q: What is the typical speed of a fully automatic label applicator machine?
A: Speeds vary widely, from 30 products per minute for basic models up to 600+ products per minute for high-end systems. Your required throughput will determine which model is appropriate. - Q: Do I need a conveyor system, or can I feed products manually?
A: Semi-automatic machines allow manual feeding, perfect for lower volumes. For larger volumes, integrating a conveyor can dramatically increase consistency and speed.
Conclusion and Next Steps
A reliable, high-quality label applicator machine is more than a tool—it’s the backbone of a polished, compliant, and efficient packaging line. By automating the labeling process, you eliminate many of the human errors and inefficiencies that can plague manual methods. Consistent labeling speaks volumes about your brand’s professionalism, increases consumer confidence, and keeps you ahead of regulatory demands.
Whether you’re a small-scale artisan producer or a high-volume manufacturer, finding the right system boils down to understanding your production needs, the specifics of your container types, and any compliance mandates you must meet. The benefits—improved accuracy, faster throughput, and a stronger bottom line—make a label applicator machine a strategic investment that pays dividends in the long run.
Ready to optimize your packaging operations and elevate your brand’s presence on store shelves? Reach out to our labeling experts today for personalized advice, product demonstrations, and deeper insights into how a label applicator machine can transform your production line. Have any questions or experiences to share? Leave a comment below—your insights could be the missing piece for someone else’s labeling success story.
Stay Connected with EngiTech
EngiTech is your trusted source for in-depth knowledge on industrial mechanical engineering machines and technologies. Stay ahead with the latest innovations, expert insights, and practical guides designed to help you make informed decisions for your business and engineering needs. Join our growing community of professionals and industry leaders to stay updated and competitive in the ever-evolving world of industrial technology.