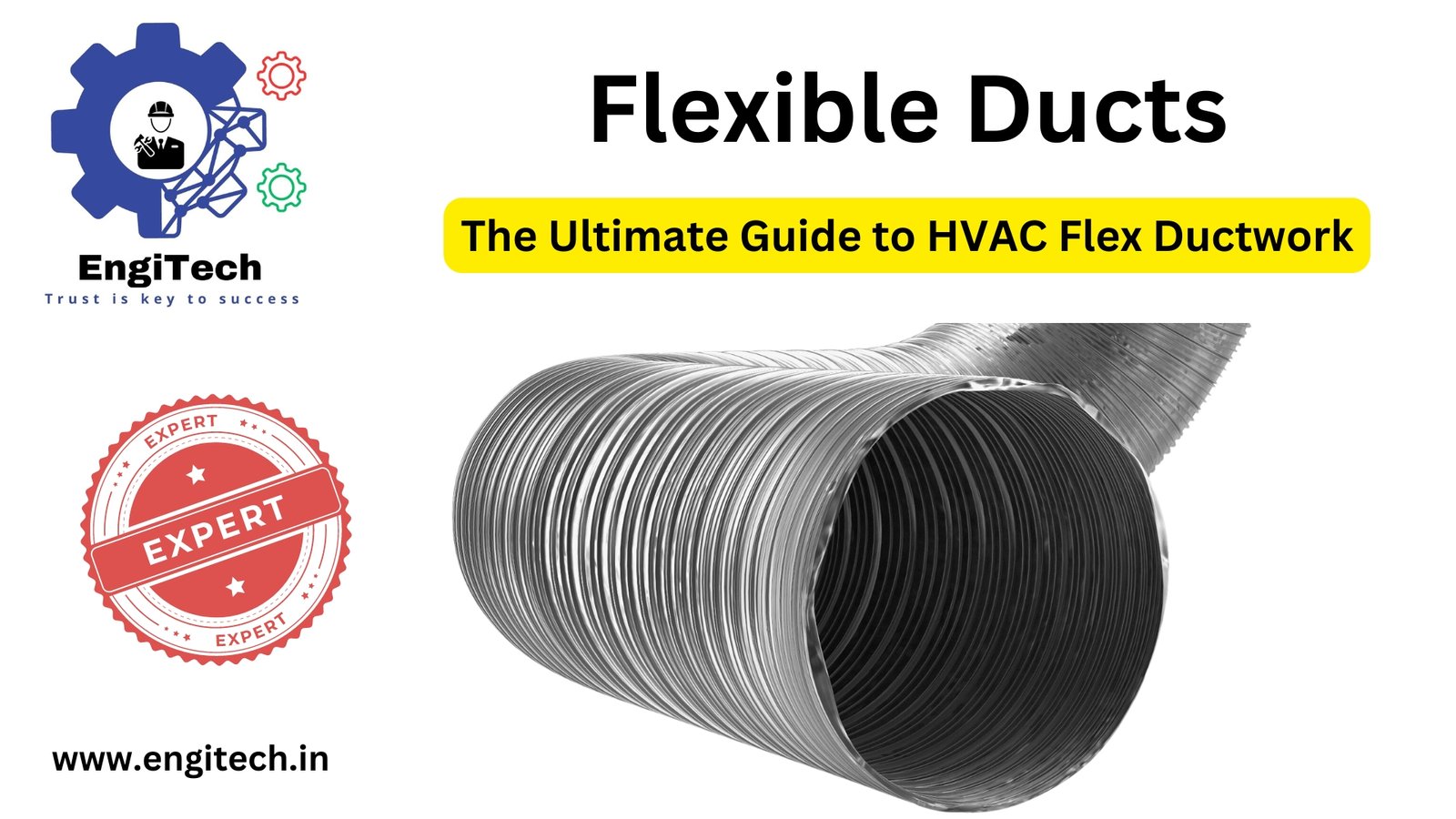
Have you ever wondered what makes your HVAC system work so efficiently throughout your home? The answer might be snaking through your walls, attic, or crawlspace right now. Flexible ducts are the unsung heroes of modern heating and cooling systems, providing the vital pathways that deliver comfortable air throughout buildings of all sizes. Whether you’re a homeowner looking to understand your HVAC system better, a DIY enthusiast planning a home renovation, or a professional seeking to refresh your knowledge, this comprehensive guide to flexible ducts will give you everything you need to know.
In today’s energy-conscious world, understanding the components of your HVAC system—particularly flexible ducts—can lead to significant improvements in energy efficiency, indoor air quality, and overall comfort. With the right knowledge about flexible ducts, you can make informed decisions that could save you thousands of dollars over time while creating a healthier living environment.
Table of Contents
What Are Flexible Ducts?
Flexible ducts (also called flex ducts) are pliable air distribution channels used in heating, ventilation, and air conditioning (HVAC) systems. Unlike rigid metal ducts, flexible ducts can bend and twist to navigate through tight spaces and around obstacles, making them particularly valuable in residential installations and retrofit projects.
The Anatomy of a Flexible Duct
Understanding the construction of flexible ducts helps explain their performance characteristics and applications:
- Inner Core: The innermost layer is typically made of a wire coil covered with a polymer material. This layer creates the main air passage and provides structural support.
- Insulation Layer: Surrounding the inner core is an insulation layer, usually made of fiberglass or similar material. This component helps maintain temperature and prevents condensation.
- Vapor Barrier: The outermost layer is a durable vapor barrier that protects the insulation from moisture damage and provides some resistance against physical damage.
- End Connectors: Most flexible ducts come with reinforced ends that allow them to connect securely to HVAC equipment, register boots, or other ductwork components.
Types of Flexible Ducts
Not all flexible ducts are created equal. The market offers several variations designed for specific applications:
Non-Insulated Flexible Ducts
These basic ducts consist of just the inner core and outer jacket without insulation. They’re primarily used in:
- Internal applications where temperature loss isn’t a concern
- Short runs within conditioned spaces
- Return air applications
- Areas with minimal temperature differentials
Insulated Flexible Ducts
The most common type for residential HVAC applications, these ducts include all layers mentioned earlier. They’re essential for:
- Supply air distribution
- Applications where energy efficiency is a priority
- Installations in unconditioned spaces like attics or crawlspaces
- Preventing condensation in humid environments
Acoustic Flexible Ducts
These specialized ducts have additional sound-absorbing properties:
- Enhanced inner liner designed to reduce airflow noise
- Thicker insulation that dampens sound transmission
- Premium choice for applications where noise reduction is essential
- Often used in office buildings, recording studios, or quiet residential zones
Benefits of Flexible Ducts in HVAC Systems
Flexible ducts have revolutionized residential HVAC installations, offering numerous advantages over traditional rigid ductwork:
Installation Advantages
- Ease of Installation: Their pliable nature allows installers to route them around obstacles without requiring complex fittings or connections.
- Time Efficiency: Installation can be completed in a fraction of the time needed for rigid duct systems, reducing labor costs significantly.
- Adaptability: Flexible ducts can conform to unusual spaces and building configurations that would challenge rigid systems.
- Reduced Material Requirements: Fewer connectors, elbows, and transition pieces are needed, simplifying the overall system design.
Performance Benefits
- Sound Attenuation: The flexible construction and insulation naturally dampen sound transmission, creating quieter HVAC operation.
- Thermal Efficiency: High-quality insulated flexible ducts minimize heat transfer, maintaining desired air temperatures from the equipment to the outlet.
- Condensation Prevention: The vapor barrier and insulation work together to prevent moisture problems that could lead to mold or water damage.
- Vibration Isolation: Flexible ducts can absorb equipment vibrations, preventing them from transferring throughout the ductwork system.
Economic Considerations
- Lower Initial Cost: Compared to rigid metal ductwork, flexible ducts typically cost less for both materials and installation.
- Reduced Labor Expenses: Faster installation translates directly to lower labor costs.
- Fewer Specialized Tools: Installation requires simpler tools than those needed for cutting and connecting metal ductwork.
- Easy Replacement: When sections need repair or replacement, swapping out flexible ducts is straightforward and cost-effective.
Potential Drawbacks and Limitations
Despite their many advantages, flexible ducts aren’t perfect for every application. Understanding their limitations is crucial for proper system design:
Performance Considerations
- Airflow Resistance: The corrugated interior surface creates more friction than smooth metal ducts, potentially reducing airflow efficiency.
- Durability Concerns: Flexible ducts are more vulnerable to physical damage from pests, maintenance activities, or accidental impacts.
- Lifespan: While high-quality flexible ducts can last 15-20 years with proper installation, they generally don’t match the multi-decade lifespan of well-maintained metal ducts.
- Sag and Compression Issues: Improper installation can lead to sagging or compression, which drastically reduces airflow capacity.
Installation Challenges
- Proper Support Requirements: Flexible ducts need adequate support to prevent sagging, typically every 4-5 feet.
- Connection Integrity: Creating airtight connections requires attention to detail and proper sealing techniques.
- Radius Limitations: Sharp bends can restrict airflow, requiring careful planning to maintain appropriate turning radiuses.
- Space Requirements: While flexible, these ducts still need sufficient clearance to maintain proper airflow capacity.
Proper Installation Practices for Flexible Ducts
The performance and longevity of flexible ducts depend heavily on proper installation. Following industry best practices ensures optimal system operation:
Planning and Preparation
- Route Planning: Map the most direct paths possible, minimizing bend angles and overall duct length.
- Sizing Calculations: Determine the appropriate duct diameter based on required airflow and system design.
- Support Strategy: Plan support locations before beginning installation, ensuring they’ll be at appropriate intervals.
- Material Selection: Choose the right R-value (insulation rating) based on local building codes and climate considerations.
Installation Steps
- Stretch the Duct: Fully extend the duct to its rated length before installation to minimize airflow resistance.
- Create Gentle Bends: Maintain a bend radius of at least 1.5 times the duct diameter to prevent airflow restrictions.
- Secure Properly: Use approved hanging straps at 4-5 foot intervals, ensuring they support the duct without compressing the insulation.
- Make Airtight Connections: Use approved tapes or mastics on inner liner connections, then secure with approved mechanical fasteners.
- Seal the Vapor Barrier: After connecting the inner core, seal the outer vapor barrier using approved materials to maintain the insulation integrity.
- Insulate Connections: Ensure all metal connectors are properly insulated to prevent condensation and heat transfer.
Common Installation Mistakes to Avoid
- Excessive Length: Installing more duct than necessary increases system resistance and reduces efficiency.
- Sharp Bends: Creating turns with less than the recommended radius significantly restricts airflow.
- Over-Compression: Squeezing ducts through tight spaces compresses the inner core and reduces airflow capacity.
- Inadequate Support: Insufficient supporting straps lead to sagging, which traps air and reduces system efficiency.
- Improper Sealing: Failing to seal connections properly results in air leakage, wasted energy, and potential moisture problems.
- Routing Through Extreme Environments: Exposing flexible ducts to excessive heat or cold can degrade their performance and lifespan.
Maintenance and Troubleshooting
Even well-installed flexible ducts require periodic maintenance to ensure optimal performance:
Regular Maintenance Tasks
- Visual Inspection: Check for signs of damage, sagging, or compressed sections at least annually.
- Support Verification: Ensure hanging straps remain intact and properly positioned.
- Connection Assessment: Verify that all connections remain sealed and secure.
- Cleanliness Check: Look for evidence of dust buildup, moisture, or mold growth that might indicate problems.
- Insulation Integrity: Confirm that the outer vapor barrier hasn’t been compromised, which could lead to insulation damage.
Common Problems and Solutions
- Reduced Airflow:
- Check for kinks or compression in the duct runs
- Verify that ducts haven’t been crushed by stored items or maintenance activities
- Ensure registers and grilles aren’t blocked
- Noise Issues:
- Look for sections vibrating against structures or other objects
- Check for proper support to prevent movement during system operation
- Verify that connections are secure and not generating whistling sounds
- Temperature Control Problems:
- Inspect for tears in the vapor barrier that might compromise insulation
- Check for air leaks at connections
- Verify that ducts in unconditioned spaces have adequate insulation values
- Odor or Air Quality Concerns:
- Inspect for evidence of moisture or mold within the system
- Check that all connections are properly sealed to prevent drawing air from undesirable sources
- Consider professional cleaning if buildup is evident
When to Replace Flexible Ducts
No building component lasts forever, and flexible ducts are no exception. Consider replacement when:
- The outer vapor barrier shows significant damage that can’t be effectively repaired
- The inner core has collapsed or been seriously compromised
- There’s evidence of widespread mold contamination within the system
- The ducts have reached their expected service life (typically 15-20 years)
- System efficiency has noticeably declined despite addressing other potential causes
Flexible Ducts vs. Rigid Ducts: Making the Right Choice
Both flexible and rigid duct systems have their place in modern HVAC design. Understanding the comparative strengths of each helps inform the right decisions for specific applications:
When Flexible Ducts Excel
- Residential Applications: The ease of installation and adaptability make flexible ducts ideal for most home HVAC systems.
- Retrofit Projects: When working in existing structures with space constraints, flexible ducts can navigate around obstacles more easily.
- Budget-Sensitive Installations: The lower initial cost makes flexible ducts attractive for projects with tight budgets.
- Sound-Sensitive Environments: The natural sound-dampening properties benefit noise-conscious applications.
- Short Run Applications: For shorter duct runs, the slightly higher friction loss of flexible ducts is typically negligible.
When Rigid Ducts May Be Preferred
- Commercial Systems: Larger commercial HVAC systems often benefit from the durability and lower friction loss of rigid ducts.
- High-Velocity Systems: Applications requiring maximum airflow efficiency may perform better with smooth-interior rigid ducts.
- Exposed Installations: When ductwork will be visible, rigid ducts often provide a more finished appearance.
- Very Long Runs: For extended duct runs, the cumulative friction loss of flexible ducts might become significant.
- Extreme Environmental Conditions: In particularly harsh environments, rigid ducts may offer greater durability.
Hybrid Systems: The Best of Both Worlds
Many modern HVAC installations use a strategic combination of rigid and flexible ducts:
- Main Trunks: Using rigid ducts for main supply and return trunks maximizes system efficiency.
- Branch Runs: Employing flexible ducts for branch lines to individual registers simplifies installation.
- Equipment Connections: Flexible connections to HVAC equipment help isolate vibration and accommodate thermal expansion.
- Acoustic Sections: Incorporating flexible duct sections specifically to reduce noise transmission in critical areas.
Energy Efficiency Considerations
In today’s energy-conscious world, understanding how flexible ducts impact system efficiency is crucial:
Insulation Values and Energy Conservation
- R-Value Significance: The R-value of duct insulation directly impacts energy efficiency, with higher values reducing heat transfer more effectively.
- Climate-Appropriate Selection: Cold climate installations generally benefit from higher R-values (R-8 or greater), while moderate climates might perform adequately with R-6.
- Location-Based Requirements: Ducts in unconditioned spaces like attics or crawlspaces need more insulation than those running through conditioned areas.
- Code Compliance: Local building codes typically specify minimum insulation requirements based on climate zone and installation location.
Reducing Energy Loss Through Better Design
- Minimizing Duct Length: Shorter, more direct runs reduce friction loss and energy requirements.
- Optimizing Duct Diameter: Properly sized ducts balance airflow needs with energy efficiency.
- Eliminating Unnecessary Bends: Each bend increases system resistance, so minimizing turns improves efficiency.
- Proper Sealing: Ensuring all connections are airtight prevents conditioned air from escaping before reaching its destination.
- Strategic Zoning: Using flexible ducts to create effective zoning systems can significantly reduce overall energy consumption.
The Cost of Poor Installation
Improper flexible duct installation can significantly impact energy bills:
- Compressed Ducts: Studies show that compressed flexible ducts can reduce airflow by up to 40%, forcing HVAC equipment to work harder.
- Leaky Connections: Even small leaks at connections can waste 20-30% of conditioned air, according to Energy Star.
- Inadequate Insulation: Poorly insulated ducts in unconditioned spaces can lose up to 30% of heating or cooling energy.
- Excessive Bending: Sharp bends can increase system resistance by the equivalent of adding many additional feet of duct length.
Indoor Air Quality and Flexible Ducts
The relationship between flexible ducts and indoor air quality deserves special attention:
Potential Air Quality Concerns
- Dust Accumulation: The corrugated interior surface can collect dust and debris over time.
- Moisture Issues: Improperly installed insulation can lead to condensation and potential mold growth.
- Material Off-Gassing: Some lower-quality flexible ducts may release volatile organic compounds (VOCs) initially.
- Air Leakage: Leaks can draw in air from unconditioned spaces, potentially introducing contaminants.
Minimizing Air Quality Risks
- Choose Quality Materials: Select flexible ducts certified by recognized industry organizations like UL or GREENGUARD.
- Ensure Proper Installation: Correct installation prevents issues like condensation that could lead to mold growth.
- Consider Regular Cleaning: Professional duct cleaning can address dust accumulation in frequently used systems.
- Maintain Appropriate Humidity: Keeping home humidity between 30-50% helps prevent conditions favorable to mold growth.
- Monitor Filter Performance: Regular filter changes or cleaning is especially important with flexible duct systems.
Choosing the Right Flexible Ducts for Your Project
Not all flexible ducts are created equal. Making informed selection decisions ensures better performance and longevity:
Key Selection Criteria
- Insulation Rating: Select an R-value appropriate for your climate and installation location.
- Inner Core Construction: Look for reinforced inner cores that resist crushing and maintain their shape.
- Vapor Barrier Quality: Choose products with durable, tear-resistant outer jackets.
- Certification: Verify that products meet relevant standards from organizations like UL and ASTM.
- Fire Rating: Ensure compliance with local fire codes, particularly for commercial applications.
- Diameter Options: Confirm availability in the specific sizes required for your system design.
Quality Indicators
- Warranty Coverage: Better products typically offer longer warranty periods.
- Material Thickness: Heavier materials generally indicate better durability.
- Reinforcement Design: Look for designs that maintain their shape under typical installation conditions.
- Connection Features: Quality products often include reinforced end sections for more secure connections.
- Manufacturing Consistency: Uniform construction with consistent wire spacing indicates quality control.
Budget Considerations
While price shouldn’t be the only factor, understanding the cost implications helps with project planning:
- Initial vs. Lifetime Cost: Higher-quality flexible ducts may cost more initially but offer better energy efficiency and longevity.
- Installation Simplicity: Some premium products feature design elements that simplify installation, potentially reducing labor costs.
- Potential Energy Savings: Better insulation and airflow characteristics can provide ongoing energy cost reductions.
- Maintenance Requirements: Quality products typically require less frequent maintenance or replacement.
Future Trends in Flexible Duct Technology
The HVAC industry continues to evolve, with several emerging trends affecting flexible duct design and application:
Material Innovations
- Antimicrobial Treatments: Manufacturers are developing inner liners with antimicrobial properties to inhibit mold and bacteria growth.
- Advanced Insulation: New insulation materials offer higher R-values with less thickness, improving both efficiency and space utilization.
- Eco-Friendly Components: Sustainable materials are increasingly available for environmentally conscious projects.
- Smart Sensors: Some premium ducts now incorporate sensors that can detect leaks, temperature differentials, or air quality issues.
Design and Installation Advancements
- Improved Connection Systems: New connection designs are emerging that simplify installation while providing better sealing.
- Pre-Insulated Fittings: Matching pre-insulated connection components reduce thermal bridging at junction points.
- Color-Coding Systems: Some manufacturers now color-code ducts for specific applications or zones, reducing installation errors.
- Installation Tools: Specialized tools are being developed specifically for flexible duct installation, improving consistency and quality.
Regulatory Changes
- Higher Efficiency Standards: Building codes increasingly require better insulation values and lower leakage rates.
- Air Quality Requirements: Regulations regarding VOC emissions and potential contaminants continue to tighten.
- Testing Protocols: More sophisticated testing requirements are being implemented to verify system performance.
- Documentation Standards: Many jurisdictions now require more detailed documentation of duct system design and installation.
Frequently Asked Questions About Flexible Ducts
How long do flexible ducts typically last?
With proper installation and maintenance, quality flexible ducts can last 15-20 years. However, environmental factors like extreme temperatures, humidity, and physical disturbances can reduce this lifespan. Signs that flexible ducts may need replacement include visible damage to the outer jacket, collapsed sections, evidence of mold growth, or noticeable reduction in system performance.
Can flexible ducts be cleaned?
Yes, flexible ducts can be cleaned, though the process requires special care to avoid damaging the flexible material. Professional duct cleaning services use specialized tools designed to safely navigate the corrugated interior without causing tears or compression. The cleaning effectiveness depends on the duct condition and installation quality. Severely contaminated or damaged ducts may be better replaced than cleaned.
Are flexible ducts safe from a fire safety perspective?
Quality flexible ducts meet specific fire safety standards and are typically made from materials that don’t readily support combustion. However, they should be installed according to local fire codes, which often specify clearance requirements from heat sources and flame-spread ratings. Most modern flexible ducts contain flame-retardant materials in both the inner core and outer jacket.
How much should I expect to pay for quality flexible ducts?
Pricing varies significantly based on diameter, insulation value, and quality. As a general guideline, insulated 6-inch flexible ducts typically range from $1-3 per foot for standard residential products. Premium products with higher R-values, reinforced construction, or specialized features can cost $4-7 per foot. Remember that installation costs typically exceed material costs for most projects.
Can I install flexible ducts myself, or should I hire a professional?
While DIY installation is possible for those with appropriate skills and knowledge, professional installation is generally recommended for several reasons:
- Professionals understand proper sizing calculations based on airflow requirements
- They have specialized tools for secure connections and proper support
- They’re familiar with building code requirements
- They can identify potential issues before they become problems
- Professional installation often includes system balancing for optimal performance
Conclusion
Flexible ducts represent an ingenious solution to the complex challenges of air distribution in modern buildings. Their adaptability, ease of installation, and cost-effectiveness have made them the predominant choice for residential HVAC systems and many commercial applications. By understanding their strengths, limitations, and proper installation techniques, you can ensure your flexible duct system delivers optimal comfort, efficiency, and air quality for years to come.
Whether you’re building a new home, renovating an existing space, or simply seeking to improve your current HVAC performance, knowledge about flexible ducts empowers you to make informed decisions. Remember that quality materials and proper installation are not areas to compromise—they directly impact your comfort, energy bills, and indoor air quality.
As with most building components, the visible simplicity of flexible ducts belies their engineering sophistication. Their seemingly straightforward design represents decades of refinement to balance flexibility, durability, thermal performance, and airflow characteristics. By selecting appropriate products and ensuring proper installation, you harness this engineering excellence for your specific needs.
References and Further Reading
For those seeking additional information about flexible ducts and HVAC system design, the following resources provide valuable insights:
- American Society of Heating, Refrigerating and Air-Conditioning Engineers (ASHRAE) – www.ashrae.org
- Air Conditioning Contractors of America (ACCA) – www.acca.org
- North American Insulation Manufacturers Association (NAIMA) – www.naima.org
- Energy Star Duct Sealing Information – www.energystar.gov/campaign/heating_cooling/duct_sealing
- Building Performance Institute (BPI) – www.bpi.org
- International Code Council (ICC) – www.iccsafe.org
- U.S. Department of Energy – www.energy.gov/energysaver/home-heating-systems
- Environmental Protection Agency Indoor Air Quality Information – www.epa.gov/indoor-air-quality-iaq
By following best practices for installation and maintenance, you can ensure that your flexible ductwork operates at peak efficiency, helping to reduce energy costs and improve indoor air quality. For more expert tips on HVAC systems and the latest industrial innovations, be sure to visit EngiTech for comprehensive resources and industry updates.