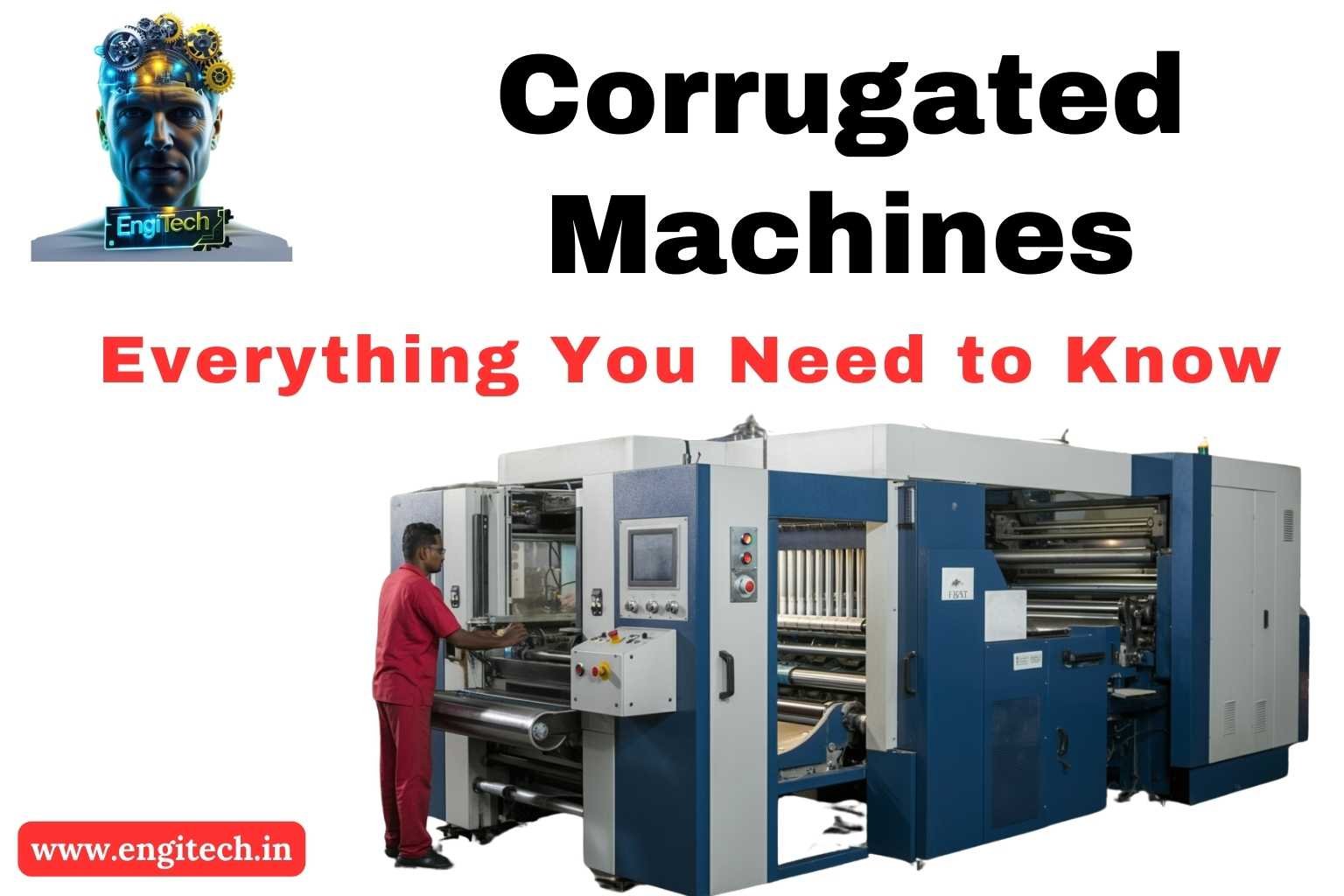
In today’s fast-paced world of packaging and logistics, companies are always looking for ways to reduce costs, speed up production, and maintain consistent product quality. That’s where the corrugated machine comes in—a powerful technology that transforms paper into the corrugated cardboard used for boxes and packaging. If you’re in the market for a corrugated machine or simply want to understand how this essential piece of equipment can revolutionize your operations, you’ve come to the right place. Within this guide, we’ll explore what a corrugated machine is, how it works, the different types available, and best practices for running a successful, efficient packaging line.
By the end of this article, you’ll have a comprehensive understanding of corrugated machinery, including actionable tips on selecting the right model, optimizing production, reducing waste, and maximizing ROI. Whether you’re new to the packaging industry or looking to upgrade your existing corrugated machine, this guide will walk you through every step in a practical, easy-to-understand manner. Let’s dive in.
Table of Contents
1. What Is a Corrugated Machine?
A corrugated machine is specialized equipment used to produce corrugated boards, which are then converted into boxes and other packaging solutions. At its core, the machine combines layers of paper—liner paper and fluted paper—by bonding them together with adhesives under heat and pressure. The result is a strong, lightweight, and customizable material ideal for protecting goods during shipping and handling.
From e-commerce giants needing custom shipping boxes to local businesses wrapping their fragile items, corrugated boxes are indispensable. The corrugated machine forms the backbone of this supply chain, providing speed, consistency, and quality. Whether you opt for a fully automated setup or a semi-automatic line, these machines help you control every aspect of box production, from flute profiles to board thickness and printing options.
2. Why Corrugated Packaging Matters
Corrugated packaging is more than just a simple box. It’s a critical element in modern commerce, impacting everything from brand image to operational efficiency. Here’s why corrugated packaging is so essential:
- Protection and Durability: Corrugated boards are engineered to absorb shocks, protect goods from damage, and withstand rough handling.
- Customization: Corrugated materials can be cut, folded, and printed to meet specific branding and sizing requirements.
- Cost-Effectiveness: Compared to many other packaging materials, corrugated boards are relatively inexpensive and widely available.
- Eco-Friendliness: Corrugated board can be recycled and reused, making it a greener choice for packaging.
- Versatility: From shipping boxes to retail-ready packaging, corrugated cardboard can be adapted for multiple applications.
Given these advantages, investing in a corrugated machine can significantly enhance your ability to meet growing demand, uphold brand integrity, and keep costs under control—all while being kind to the environment.
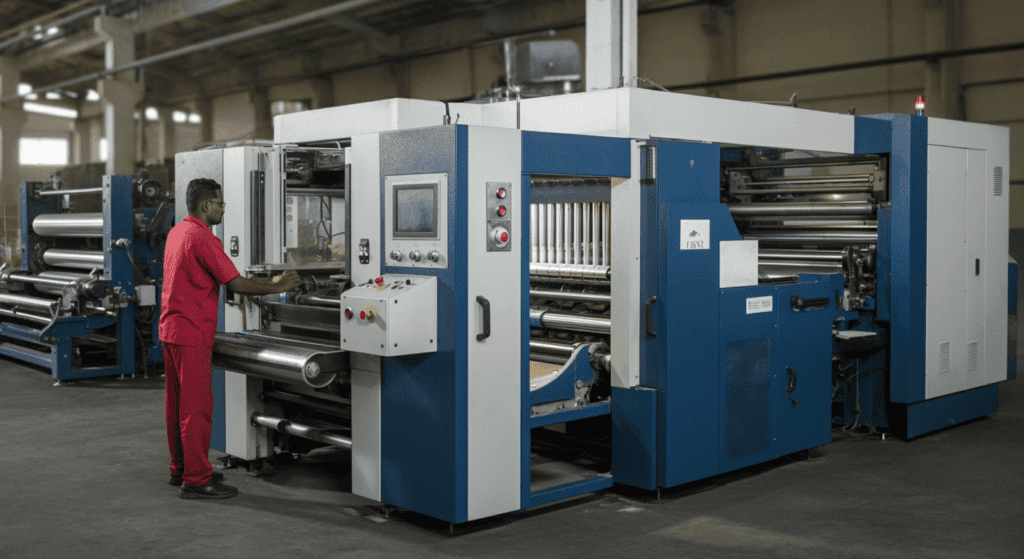
3. How Corrugated Machines Work: The Basics
Before you finalize a purchase decision on a corrugated machine, it’s crucial to understand how it operates. While specific models can vary, most corrugated machines include the following core processes:
- Paper Unwinding: Rolls of liner and medium (fluting paper) are fed into the machine.
- Preheating: The paper is heated to prepare it for the fluting process.
- Corrugating (Fluting): A corrugating roll forms the medium into a wave-like structure, called a flute.
- Glue Application: A thin layer of adhesive is applied to the tips of the flutes.
- Bonding the Layers: The fluted medium is bonded to the liner(s) to form single or double-wall corrugated board.
- Drying and Curing: Heat and pressure ensure the glue sets properly, creating a rigid board.
- Cutting and Slitting: The corrugated sheet is cut to the desired size and trimmed.
- Stacking and Delivery: The final corrugated boards are stacked for further processing or direct shipping.
Throughout these steps, advanced control systems help maintain consistent temperature, pressure, and speed, ensuring high-quality boards that meet specific performance criteria.
4. Key Components of a Corrugated Machine
Although different models can have varying configurations, most corrugated machines share the following critical components:
- Mill Roll Stand: Holds and feeds paper rolls into the machine.
- Preheater: Warms the liner and fluting medium to make them easier to form and bond.
- Single Facer Unit: Creates the fluted medium by passing paper through corrugating rolls.
- Glue Application System: Dispenses adhesive accurately to flute tips.
- Double Backer: Bonds the second liner to the fluted medium in a multi-layer process.
- Heating Sections: Use steam or electricity to help the adhesive cure.
- Cut-Off Knife and Slitter-Scorer: Cuts and scores the corrugated board into specified dimensions.
- Stacker: Organizes and stacks the finished boards for easy handling.
Understanding these components is vital for seamless operation, especially when troubleshooting issues or scheduling maintenance.
5. Types of Corrugated Machines
5.1 Corrugated Box Manufacturing Machine
A corrugated box manufacturing machine focuses on producing fully formed boxes with flaps and scoring marks. These machines often integrate with folder-gluers and printing sections to handle the entire box production line.
5.2 Corrugated Cardboard Production Line
A corrugated cardboard production line is a large-scale setup usually found in integrated paper mills or large packaging companies. It contains multiple sections—each specialized in a phase of corrugated board production, from paper unwinding to final stacking.
5.3 Corrugated Packaging Equipment
This term broadly encompasses machinery used in the entire corrugated packaging process. It includes feeders, glue stations, printing presses, slotters, die-cutters, and more.
5.4 Corrugated Board Machine
A corrugated board machine specifically manufactures sheets of corrugated board, which can later be converted into boxes, partitions, or other packaging forms. It typically includes a single-facer, a glue station, and a double-backer.
5.5 Automatic Corrugated Machine
An automatic corrugated machine automates most or all aspects of production, minimizing manual intervention. They are ideal for large-scale operations that require high-speed production with minimal downtime.
5.6 High-Speed Corrugated Machine
A high-speed corrugated machine can produce corrugated boards at a rapid rate—often exceeding 250 meters per minute. These are best suited for facilities that handle massive production volumes and have stringent deadlines.
5.7 Corrugator Line
A corrugator line is essentially the entire production line where multiple modular units are joined to form a cohesive system. It allows for customization, enabling businesses to add or remove modules based on specific requirements.
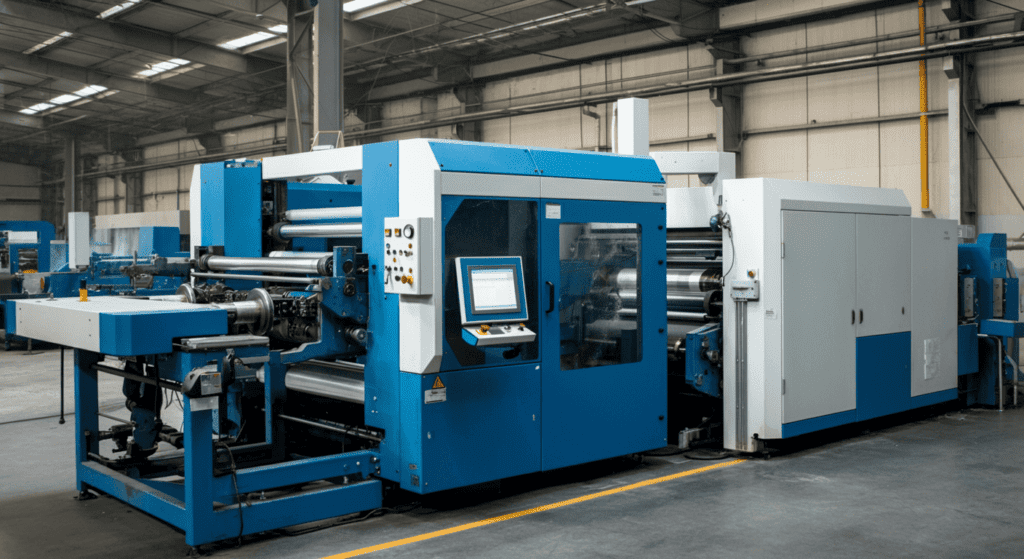
6. Choosing the Right Corrugated Machine for Your Business
Selecting the perfect corrugated machine depends on a variety of factors, and making the right choice ensures you’re able to meet production demands without overspending. Here’s what to consider:
- Production Volume: Evaluate how many corrugated boards or boxes you need to produce daily or monthly. High-speed corrugated machines are ideal for large-scale operations, but they might be overkill for smaller facilities.
- Budget: The cost of corrugated machinery ranges widely. Semi-automatic machines are generally less expensive but may require more labor. Fully automated setups have a higher initial investment but can save money in the long run through reduced labor costs and higher throughput.
- Space Requirements: Measure your facility to ensure you have adequate floor space and ceiling height for the machine and any auxiliary equipment like conveyors or stackers.
- Customization Needs: If you handle multiple box sizes or custom printing, look for a machine that accommodates quick setup changes and integrates with printing systems.
- Speed and Efficiency: Consider the trade-off between production speed and operational complexity. A high-speed corrugated machine could require more skilled labor and frequent maintenance.
- Automation Level: Determine how much of your operation you want to automate. While full automation reduces human error, it typically requires a larger upfront investment.
- Support and Training: Opt for manufacturers or suppliers who offer comprehensive training, reliable customer service, and easy access to spare parts.
Pro Tip: Always read product reviews, consult with machine operators, and request a trial run or a factory visit to see the equipment in action before committing to a purchase.
7. Setting Up Your Corrugated Machine Production Line
Launching a new corrugated machine production line or upgrading an existing one involves several key steps:
- Facility Layout:
- Allocate space for the machine, raw material storage, and finished goods.
- Ensure adequate room for forklifts, pallet jacks, and maintenance access.
- Power and Utilities:
- Corrugated machinery typically requires stable electricity and steam.
- Check local utility rates and availability of resources like water if the machine uses steam systems.
- Installation and Calibration:
- Have professionals assemble and calibrate the machine.
- Verify that each module—single facer, double backer, slitter-scorer—is aligned correctly.
- Operator Training:
- Train staff on machine operation, safety protocols, and basic troubleshooting.
- Document standard operating procedures (SOPs) for consistent performance.
- Quality Control Measures:
- Establish checkpoints to measure board thickness, flute profile, and bonding strength.
- Use digital measuring tools or specialized testing equipment.
- Safety Protocols:
- Provide protective gear like safety glasses and gloves.
- Implement lockout-tagout (LOTO) procedures to safely power down the machine for maintenance.
- Testing and Ramp-Up:
- Run test batches before full-scale production to identify bottlenecks.
- Make incremental adjustments in speed, temperature, or glue application.
By thoroughly planning your production line setup, you reduce the risk of costly downtime and ensure a smoother transition to full-scale production.
8. Maintenance and Troubleshooting
Even the best corrugated machine will require regular maintenance to operate at peak efficiency. Here are some best practices:
- Daily Inspections:
- Check rollers, belts, and adhesive levels at the start of each shift.
- Verify the tension of belts and the alignment of corrugating rolls.
- Scheduled Maintenance:
- Replace worn-out parts like bearings or belts before they fail.
- Lubricate moving components according to the manufacturer’s recommendations.
- Cleaning:
- Remove dust, debris, and glue residue to prevent jams or heat inefficiency.
- Pay special attention to the corrugating rolls and glue stations.
- Troubleshooting Common Issues:
- Uneven Flutes: Could result from incorrect roll pressure or damaged corrugating rolls.
- Delamination: Often caused by insufficient glue, improper temperature, or speed that is too fast.
- Warped Boards: Frequently a sign of uneven drying or mismatched liner tension.
- Machine Downtime: May be related to faulty sensors, loose wiring, or PLC (Programmable Logic Controller) errors.
- Documentation:
- Keep a maintenance log for each piece of machinery.
- Document every repair, replacement, and inspection for future reference.
By paying close attention to routine maintenance and addressing problems as soon as they arise, you’ll prolong your machine’s lifespan and maintain consistent product quality.
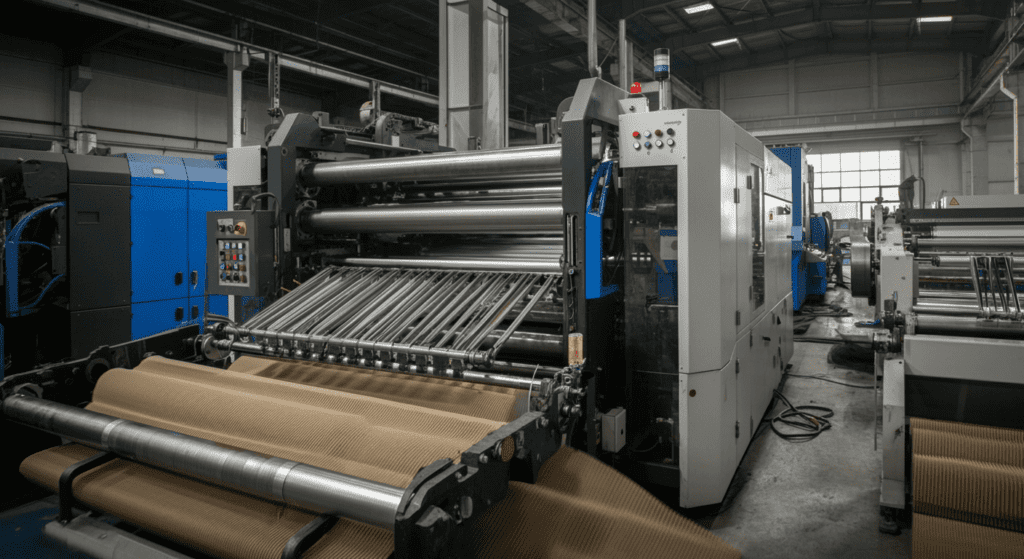
9. Environmental Benefits of Corrugated Packaging
The modern consumer is increasingly eco-conscious, and corrugated packaging fits neatly into green initiatives:
- Recyclable Material: Corrugated boards are made primarily from paper, which is one of the most recyclable materials globally.
- Renewable Resources: Many paper mills source their raw materials from sustainably managed forests.
- Reduced Carbon Footprint: The lightweight nature of corrugated board reduces transportation costs and emissions.
- Reusable and Biodegradable: Corrugated boxes can be reused multiple times and will biodegrade in natural environments.
- Minimal Waste Production: Advanced corrugated machines can optimize paper usage and reduce waste, further lessening environmental impact.
Considering these eco-friendly advantages, integrating a corrugated machine into your business helps position your brand as responsible and forward-thinking—a significant selling point in today’s market.
10. Cost-Efficiency and ROI
Investing in a corrugated machine might seem overwhelming initially, but the long-term benefits often outweigh the costs:
- Reduced Outsourcing: Producing your own corrugated boards or boxes can eliminate the need to rely on external suppliers.
- Scalability: As demand grows, you can increase production by adding shifts or upgrading certain modules.
- Quality Control: Controlling each aspect of production in-house ensures consistent quality, reducing returns or product damage.
- Bulk Material Savings: Purchasing paper in large rolls can be more economical than buying ready-made boxes.
- Automation Efficiencies: Automated or high-speed corrugated machines can significantly reduce labor costs, leading to faster ROI.
Case Study Example: A mid-sized e-commerce company invested in a semi-automatic corrugated machine. Initially, the upfront cost was substantial. However, within a year, they saw a 20% reduction in packaging expenses and a 15% increase in customer satisfaction due to fewer damaged shipments. Over three years, their ROI soared as they scaled up production and handled custom box requests in-house.
11. Innovations in Corrugated Machinery
The corrugated packaging industry has seen steady growth and technological advancements. Here are some trends shaping the future:
- Digital Printing Integration: Newer machines can print high-resolution graphics directly on corrugated boards, eliminating the need for separate printing processes.
- Smart Sensors and IoT: Sensors can detect tension, temperature, and adhesive levels in real-time, sending automatic alerts to operators or adjusting settings automatically.
- Energy-Efficient Models: Improvements in heating systems and conveyor motors reduce energy consumption and operational costs.
- Modular Upgrades: Manufacturers offer modular components like additional single-facer units or upgraded cut-off knives, allowing you to expand production capabilities without replacing the entire line.
- Automated Data Analytics: Built-in software can track production metrics, quality parameters, and maintenance schedules, simplifying decision-making and predictive maintenance.
By staying updated on these innovations, you can future-proof your investment and maintain a competitive edge.
12. Frequently Asked Questions (FAQs)
Q1. What Is the Average Lifespan of a Corrugated Machine?
A well-maintained corrugated machine can last anywhere from 10 to 20 years. Lifespan depends on factors like quality of initial components, operational intensity, and how diligently maintenance is performed.
Q2. How Fast Can a High-Speed Corrugated Machine Operate?
High-speed corrugated machines can run at speeds exceeding 250 meters per minute. Some advanced models can even reach over 300 meters per minute, but this depends on production requirements and machine capabilities.
Q3. What Are the Common Flute Profiles in Corrugated Packaging?
The most common flute profiles include A, B, C, E, and F. Each flute type differs in height and thickness, offering various degrees of cushioning, stacking strength, and printability.
Q4. Can I Use Recycled Paper on a Corrugated Machine?
Yes, you can. Modern corrugated machines are designed to handle recycled paper grades, although you might need to adjust machine settings like adhesive spread and tension control.
Q5. Is Full Automation Necessary for Small to Mid-Sized Businesses?
Not necessarily. While an automatic corrugated machine offers efficiency and reduced labor costs, small to mid-sized operations may find semi-automatic machines more budget-friendly and easier to operate.
Conclusion and Next Steps
From understanding the mechanical components to optimizing production for maximum ROI, a corrugated machine is a transformative investment for businesses that rely on corrugated packaging. Whether you’re producing standard shipping boxes or intricate custom designs, the right machine can elevate your packaging game to new heights.
Stay Connected with EngiTech
EngiTech is your trusted source for in-depth knowledge on industrial mechanical engineering machines and technologies. Stay ahead with the latest innovations, expert insights, and practical guides designed to help you make informed decisions for your business and engineering needs. Join our growing community of professionals and industry leaders to stay updated and competitive in the ever-evolving world of industrial technology.