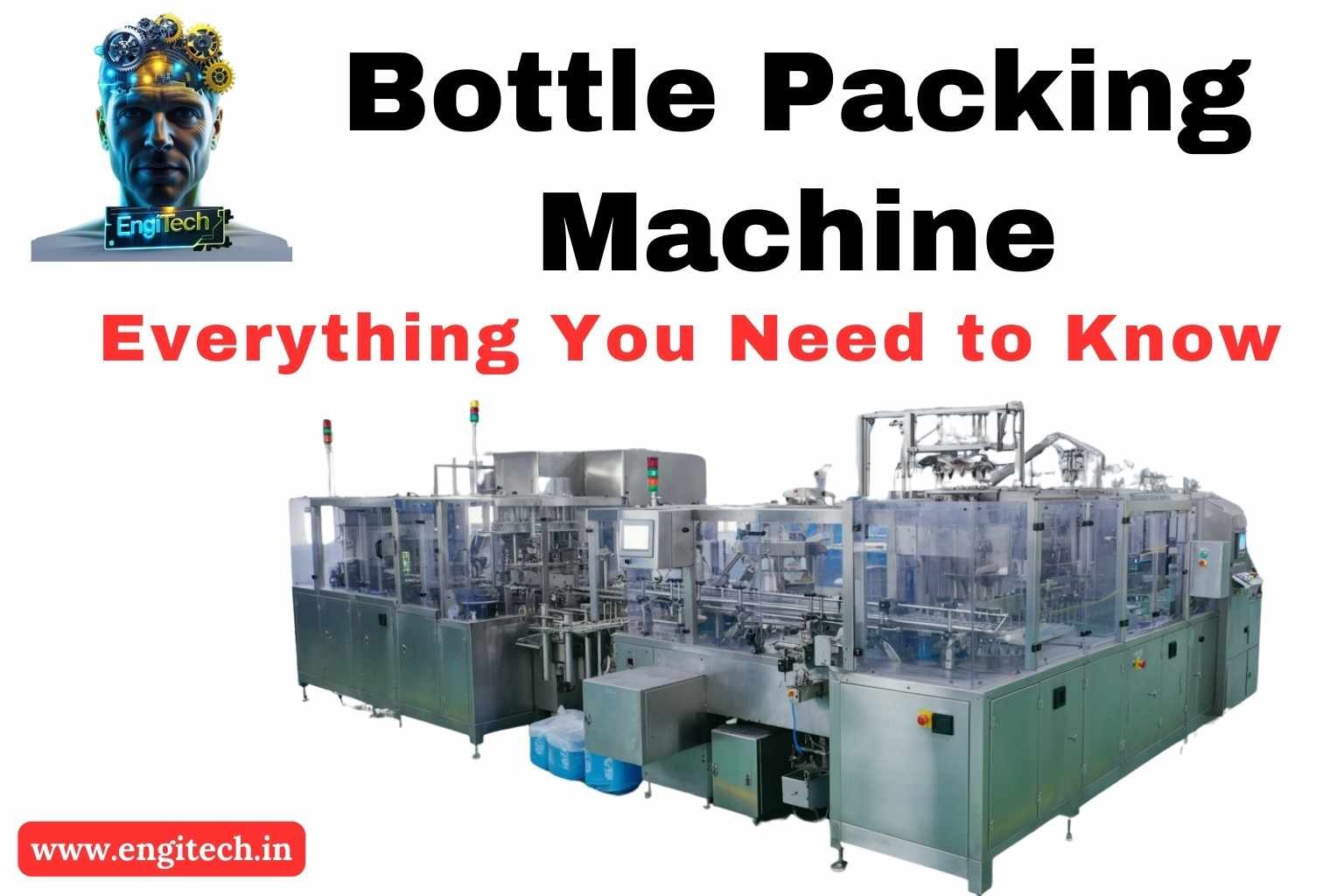
In a world increasingly driven by efficiency, speed, and precise quality control, the bottle packing machine stands out as a game-changing piece of equipment for countless manufacturers. Whether you’re running a small beverage startup, a large pharmaceutical facility, or anything in between, having a dedicated system for bottling and packing can revolutionize your operational workflow. In this comprehensive guide, we’ll dive deep into everything you need to know about bottle packing machines. From an in-depth look at how they work to practical advice on choosing the right model for your needs, you’ll walk away with a thorough understanding that can elevate your packaging line.
By the time you finish reading, you’ll be equipped to navigate the industry’s best practices, spot innovative trends, and troubleshoot issues that may arise. Most importantly, you’ll learn how a bottle packing machine can significantly reduce costs while boosting production quality and volume—an irresistible trifecta for anyone looking to gain a competitive edge. So, buckle up for a journey that explores the heart and soul of automated bottling technology.
Table of Contents
What Is a Bottle Packing Machine?
A bottle packing machine is specialized packaging equipment designed to handle the intricate process of filling, sealing, labeling, and sometimes even palletizing bottles of various shapes and sizes. Typically used to package liquids such as water, carbonated drinks, juices, sauces, and even chemicals, these machines automate essential production steps to minimize manual labor and human error.
While the term “bottle packing machine” might conjure an image of a single apparatus, in reality, this equipment often consists of multiple integrated components, such as a bottle unscrambler (for orienting empty containers), a filling station, a capping station, and a labeling unit. Some advanced models include inspection systems for quality checks and conveyors for streamlined product flow. When properly configured, a bottle packing machine seamlessly orchestrates all these tasks in a synchronized manner.
Key Benefits at a Glance:
- Increased throughput and speed
- Consistent fill levels and capping
- Reduced labor costs
- Enhanced hygiene and quality control
The Importance of a Bottle Packing Machine in Modern Manufacturing
Modern manufacturing thrives on efficiency, consistency, and the ability to scale up production when needed. Manually filling and capping bottles is not only slow but also prone to significant errors. Overfilling, underfilling, contamination, and sealing problems can quickly eat into profits and harm your brand’s reputation.
- Scalability: One of the top reasons businesses invest in an automatic or semi-automatic bottle packing machine is the ease of scaling production. When consumer demand spikes, these machines can be calibrated for higher throughput in a matter of hours rather than days.
- Quality Assurance: Integrating a machine-based quality check ensures every bottle meets stringent criteria. This is particularly crucial in sectors such as pharmaceuticals and food & beverage, where contamination risks must be carefully managed.
- Cost-Efficiency: Over the long term, these machines pay for themselves. Lower labor needs, reduced wastage, and faster turnaround times all translate to improved profitability.
- Competitive Edge: In a saturated marketplace, a consistently packaged, visually appealing product can make all the difference. A high-quality bottle packing machine helps maintain brand uniformity, ensuring your product stands out on retail shelves.
Ultimately, adopting automated bottle packing technology is akin to future-proofing your operations. As market demand for speed and consistency continues to grow, having an automated solution in place not only addresses current needs but also positions your company for long-term success.
Key Components and How They Work
To understand how a bottle packing machine can revolutionize your packaging line, it’s important to break down its core components and how each element contributes to the overall process:
- Bottle Unscrambler:
- Purpose: Orients bottles and lines them up for the filling station.
- How It Works: Bottles are fed into a rotating hopper and exit in an upright position, ready for filling.
- Filling Station:
- Purpose: Dispenses the correct volume of product into each bottle.
- How It Works: Using volumetric, gravimetric, or flow meter–based methods, this station ensures accuracy down to milliliters or even microliters, depending on the product.
- Capping Station (or Capper):
- Purpose: Seals the bottle with a cap or lid to prevent leaks and contamination.
- How It Works: After a sensor confirms bottle presence, a cap is placed and tightened or sealed, sometimes using torque control.
- Labeling Unit:
- Purpose: Applies labels or shrink sleeves to identify the product and provide branding and regulatory information.
- How It Works: Bottles pass through a roller or belt system where adhesive labels or sleeves are applied at a designated speed.
- Inspection System (Optional):
- Purpose: Checks fill levels, label placement, or cap alignment to ensure product consistency and detect quality issues.
- How It Works: Cameras and sensors automatically scan bottles for any anomalies, rejecting faulty items from the production line.
- Conveyor System:
- Purpose: Transports bottles from one station to the next without manual intervention.
- How It Works: Motorized belts set to various speeds synchronize with other stations, ensuring a consistent flow of products.
- Control Panel:
- Purpose: Central hub to manage operations, set speeds, and monitor performance metrics.
- How It Works: Operators can program fill volumes, capping torque, labeling speeds, and other parameters for different production runs.
Each part of this system can be individually tailored to the type of product you’re handling, the desired packaging speed, and industry regulations. The result is a coordinated ballet of mechanical and electronic components working in harmony.
Types of Bottle Packing Machines
Bottle packing machines are not a one-size-fits-all solution. Various models cater to specific industries, production scales, and packaging needs. Here’s an overview of the major categories:
Semi-Automatic Bottle Packing Machines
Ideal for: Small to medium-scale businesses, boutique operations, pilot plants.
- Characteristics: Require some manual intervention—usually in feeding bottles or capping.
- Advantages: Lower initial investment, easier to maintain, and highly flexible for different bottle sizes.
- Disadvantages: Limited throughput and relies partially on human labor.
Fully Automatic Bottle Packing Machines
Ideal for: Large-scale manufacturing facilities that demand high throughput.
- Characteristics: Complete automation from unscrambling to capping, labeling, and even palletizing.
- Advantages: Faster production rate, minimal human error, reduced labor costs in the long run.
- Disadvantages: Higher upfront cost, more complex to set up, and typically requires skilled technicians for maintenance.
Rotary vs. In-Line Systems
- Rotary Systems:
- High Speed: Rotary machines feature multiple filling heads arranged in a circular configuration.
- Efficiency: They can fill, cap, and label simultaneously, offering high throughput.
- Cost: Generally higher-priced, best suited for large-scale or mass-production scenarios.
- In-Line Systems:
- Sequential Flow: Bottles move in a straight line from one station to the next.
- Flexibility: Easier to switch out components or handle different bottle formats.
- Cost: Often more affordable than rotary but slightly slower.
When choosing a type of bottle packing machine, consider factors like production volume, budget, product viscosity, and space constraints. What works perfectly for a small artisan sauce business may be inadequate for a multinational soft drinks manufacturer, and vice versa.
Step-by-Step Process of Bottle Packing
Understanding the sequence of events in a bottle packing line clarifies why each component is vital. Below is a generalized step-by-step overview:
- Bottle Loading and Orientation
- Operators or automated loaders place bottles into a feeding system, which orients them upright.
- Filling
- Bottles pass under nozzles calibrated for precise fill volumes. Depending on the liquid’s viscosity—be it water, syrups, or oils—filling speeds and nozzles differ.
- Capping
- Once filled, the bottle enters the capping station. Caps are fed from a bowl feeder or hopper and placed onto the bottle, sealed using torque or heat, depending on the cap type.
- Labeling
- Before labeling, a sensor detects bottle presence. The machine applies labels using rollers or shrink sleeves. A quick sensor check confirms correct label placement.
- Quality Inspection
- Advanced lines use cameras to verify seal integrity and label accuracy. Bottles that fail these checks are automatically removed from the line.
- Secondary Packaging (Optional)
- Depending on your setup, bottles might move on to case packers or tray formers for further packaging.
- Palletizing (Optional)
- Fully automated systems include robotic palletizers that stack finished cases onto pallets for shipping.
Each stage of this process can be adapted to meet specific product requirements. For instance, bottles containing carbonated beverages may need special filling techniques to manage foam and pressure. Pharmaceutical bottles might require sterile filling environments and specialized capping mechanisms to maintain product integrity.
Industries That Benefit from Bottle Packing Machines
Virtually any industry dealing with liquid or semi-liquid products in bottles can benefit significantly from an automated packing system. Some notable examples include:
- Food & Beverage:
- Examples: Juices, soft drinks, dairy products, sauces, and condiments.
- Requirements: Hygiene compliance (FDA standards), accurate filling to avoid overflow, tamper-evident seals.
- Pharmaceuticals & Healthcare:
- Examples: Syrups, vitamins, liquid medications.
- Requirements: Strict aseptic conditions, accurate dosing, child-resistant caps.
- Cosmetics & Personal Care:
- Examples: Shampoos, lotions, perfumes.
- Requirements: Viscosity management, visually appealing labeling, sometimes specialized capping (like pumps or sprays).
- Chemical & Industrial:
- Examples: Cleaning solutions, automotive fluids, lubricants.
- Requirements: Corrosion-resistant materials, safety features for hazardous substances, anti-static systems.
- Household Goods:
- Examples: Liquid detergents, fabric softeners, dishwashing liquids.
- Requirements: Foam control during filling, accurate fill levels, child-proof capping.
The versatility of bottle packing machines makes them a staple across multiple market segments. With the right attachments, nozzles, and compliance protocols, these systems can handle virtually any type of liquid product.
Key Factors to Consider Before Purchasing
Investing in a bottle packing machine is a major capital decision. To ensure you make the right choice, weigh the following considerations carefully:
- Production Capacity
- Determine your current and projected volume needs. Overestimating leads to unnecessary costs; underestimating can bottleneck growth.
- Budget vs. ROI
- While a fully automatic system offers high efficiency, the upfront costs can be steep. Run a cost-benefit analysis to calculate how quickly you can recoup your investment.
- Flexibility
- If you plan on packaging multiple product types or varying bottle sizes, consider a versatile system that can adapt with minimal changeover time.
- Space Constraints
- Assess the layout of your production floor. Make sure the system you choose fits well and allows comfortable operator movement and future expansions.
- Regulatory Compliance
- In industries like pharmaceuticals or food & beverage, you’ll need to meet regional and international standards (e.g., FDA, ISO). Verify the machine’s compliance features.
- Ease of Maintenance
- Complex machinery with specialized parts may lead to longer downtimes. Look for suppliers with reliable service contracts and local support networks.
- Training and Labor
- Skilled operators and technicians can significantly reduce the learning curve. Factor in training costs and the level of expertise needed.
- Automation Level
- Higher automation often equates to less labor but more complex setups. Decide on a balance that fits your resources and long-term plans.
Pro Tip: Always ask for customer references or case studies from the machine supplier. This real-world feedback can shed light on potential hidden costs or performance issues.
Maintenance, Best Practices, and Compliance
Maintaining your bottle packing machine is crucial to ensure a consistent output and long operational life. Neglecting preventive care can lead to unexpected downtimes, which are costly in both time and materials. Here’s how to keep your line running smoothly:
- Regular Cleaning and Sanitization
- Importance: Residue build-up can compromise bottle filling accuracy, increase contamination risks, and affect flavor or chemical composition.
- Best Practice: Schedule a daily cleaning routine for contact parts and a thorough weekly or monthly sanitation procedure.
- Routine Inspections
- Importance: Early detection of wear and tear can prevent catastrophic failures.
- Best Practice: Inspect conveyor belts, nozzles, sealing tools, and electrical connections weekly.
- Lubrication and Parts Replacement
- Importance: Proper lubrication helps reduce friction and extends part longevity.
- Best Practice: Keep track of parts that have a recommended lifespan (e.g., O-rings, gaskets, belts). Replace them preemptively to avoid breakdowns.
- Data Logging and Software Updates
- Importance: Modern machines often include PLCs (Programmable Logic Controllers) and software that log performance data.
- Best Practice: Regularly review data logs to spot dips in efficiency or anomalies. Update software to benefit from bug fixes and improved functionalities.
- Compliance Checks
- Importance: In highly regulated fields (like pharmaceuticals or food processing), audits require complete documentation of machine maintenance and sanitation protocols.
- Best Practice: Keep clear, time-stamped records of all cleaning, calibrations, and repairs. This practice not only ensures compliance but also instills trust with regulators and customers.
Latest Innovations and Trends in Bottle Packing Machines
The packaging industry is constantly evolving, with breakthroughs and technological leaps making bottle packing machines more efficient, precise, and user-friendly. Here are a few cutting-edge trends gaining momentum:
- Robotics and AI Integration
- Impact: Highly adaptable robotic arms are increasingly deployed for complex tasks like product inspection or specialized capping. AI algorithms can predict machine failures before they occur, minimizing downtime.
- Smart Sensors and IIoT (Industrial Internet of Things)
- Impact: Sensors collect real-time data on fill volumes, temperatures, vibration levels, and more. IIoT-enabled machines can send notifications for preventive maintenance, significantly reducing operational delays.
- Sustainability Focus
- Impact: Manufacturers are developing eco-friendly solutions to minimize plastic usage. Some machines are designed to handle biodegradable or lightweight bottle materials without compromising quality.
- Modular Designs
- Impact: Instead of buying a single, monolithic system, companies can opt for modular designs that allow them to upgrade or switch out specific modules (like labeling or capping) as needs evolve.
- High-Precision Micro-Dosing
- Impact: Especially relevant for pharmaceutical and cosmetic industries, micro-dosing capabilities ensure near-perfect accuracy in liquid fills, reducing expensive product waste.
By keeping an eye on these innovations, you can future-proof your investment and maintain a competitive edge. When scouting new machines, ask suppliers about their roadmap for integrating robotics, AI, or IIoT features.
Cost Considerations and ROI
Any high-value equipment purchase begs the question: “Is this worth it?” Here’s how to make a sound financial assessment:
- Initial Capital Outlay
- Fully automatic systems can range from tens of thousands to several hundred thousand dollars, depending on brand, capacity, and optional features.
- Semi-automatic machines typically fall on the lower end of the price spectrum.
- Operating Expenses
- Labor: Reduced labor costs are one of the main advantages, but remember to budget for at least a few skilled operators or technicians.
- Maintenance: Factor in the cost of replacement parts, lubricants, and consumables.
- Efficiency Gains
- Throughput: A machine’s speed directly impacts how many bottles can be processed per hour. Over a year, a seemingly small increase in output can translate to massive revenue gains.
- Quality Control: Fewer rejects and less wastage contribute to cost savings.
- Payback Period
- Calculation Formula: Payback Period=Initial InvestmentAnnual Net Cash Flow Savings \text{Payback Period} = \frac{\text{Initial Investment}}{\text{Annual Net Cash Flow Savings}}
- Example: If you spend $100,000 on a system and estimate $40,000 in annual savings from labor reduction and improved efficiency, your payback period is 2.5 years.
- Financing Options
- Some manufacturers offer leasing or financing plans, reducing the upfront burden. Explore these options if your business model requires a gradual capital expenditure.
In most cases, well-chosen automated machinery pays for itself within a few years—often sooner if production volumes are high. The key is to match the machine’s capabilities with your actual needs without overspending on features you won’t use.
Q&A: Frequently Asked Questions
Below are some commonly asked questions about bottle packing machines, aimed at clarifying queries many first-time buyers or operators encounter:
1. Can a single machine handle multiple bottle sizes and shapes?
Yes, many modern machines are highly adaptable. In-line systems are generally more flexible and easier to adjust. You may need to swap out or adjust specific parts like filling nozzles, capping heads, or label applicators.
2. How important is it to have a dedicated operator for the machine?
While fully automatic machines require minimal human intervention, a dedicated operator or technician is crucial for monitoring performance, loading materials (like caps and labels), and troubleshooting minor issues. Regular supervision ensures continuous uptime and quality output.
3. What about packaging compliance for industries like pharmaceuticals?
It’s absolutely critical. You’ll need machines that meet stringent regulations such as FDA or GMP standards. Look for specialized features like laminar flow hoods, HEPA filters, or validated cleaning processes if you’re in pharma or similarly regulated fields.
4. Are bottle packing machines compatible with sustainable packaging materials?
Yes. Many newer models are designed to handle biodegradable or lightweight PET bottles. Check with the manufacturer about compatibility and recommended settings for eco-friendly materials.
5. How do I ensure a smooth setup post-purchase?
Work closely with the supplier for proper training and installation guidelines. Many reputable manufacturers provide on-site setup and calibration services, along with training sessions for your staff.
Conclusion: The Future of Automated Bottle Packing & CTA
As consumer demand for quick and reliable products continues to soar, the bottle packing machine stands at the forefront of modern packaging solutions. From scaling your production to meeting rigid quality standards, an automated system brings speed, consistency, and adaptability that manual labor simply can’t match. With the rise of advanced technologies like AI-driven analytics and modular design, the future of bottle packing promises even greater efficiency and customization.
Ready to take your packaging process to the next level? Whether you’re in the initial research stage or already convinced of the benefits, now is the time to act. Explore our article to deepen your understanding. You can also reach out to us for personalized advice tailored to your industry, production scale, and budget constraints.
By choosing the right bottle packing machine, you’re not just investing in equipment—you’re investing in a more efficient, profitable, and innovative future for your business. Embrace the power of automation today, and let your products shine on shelves tomorrow.
Stay Connected with EngiTech
EngiTech is your trusted source for in-depth knowledge on industrial mechanical engineering machines and technologies. Stay ahead with the latest innovations, expert insights, and practical guides designed to help you make informed decisions for your business and engineering needs. Join our growing community of professionals and industry leaders to stay updated and competitive in the ever-evolving world of industrial technology.