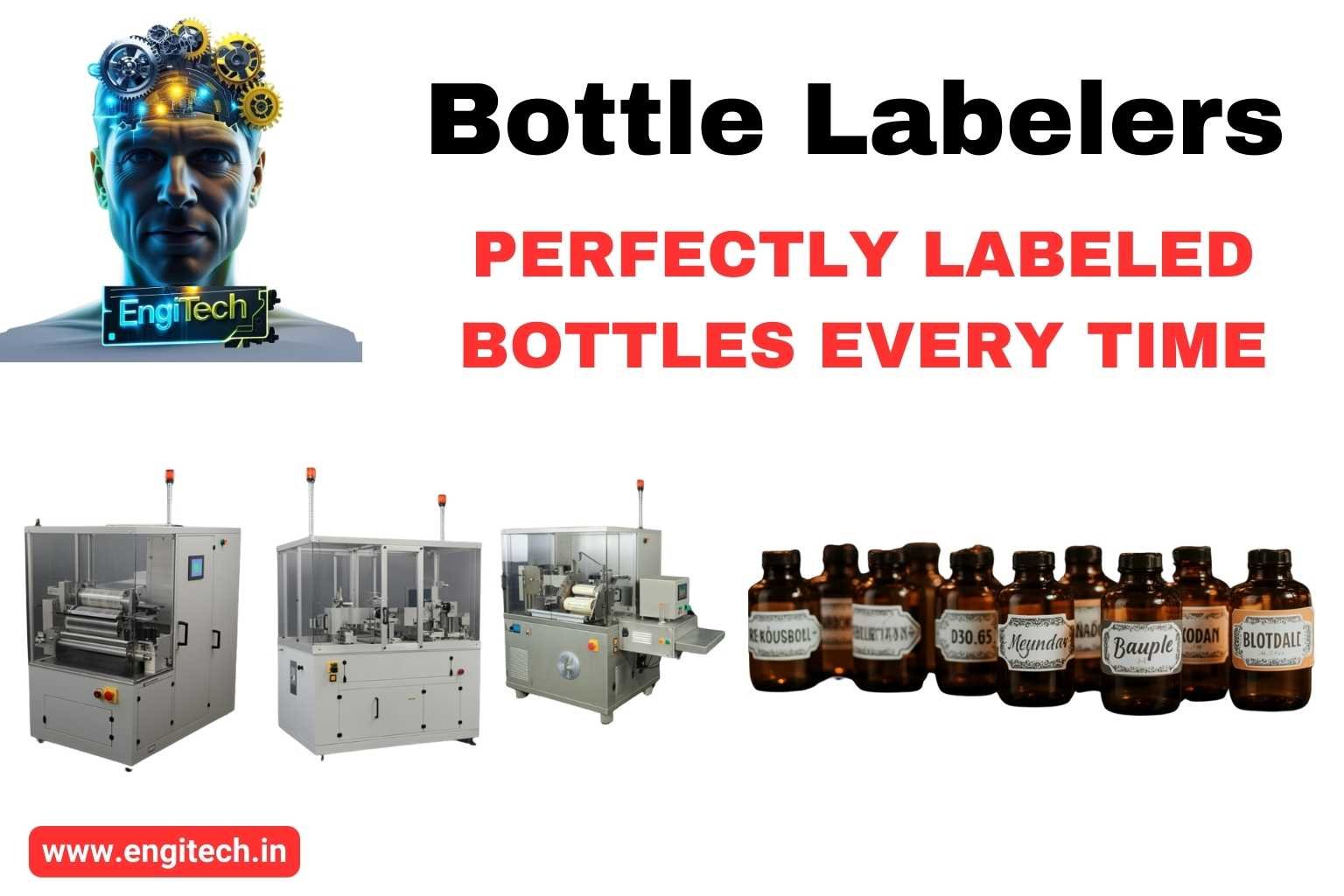
If you’ve ever reached for a bottle of your favorite craft soda, artisanal beer, or luxury skincare serum and noticed its immaculate, professional-looking label, you can thank a bottle labeler for that polished presentation. In today’s crowded marketplace, a captivating label can make your product stand out on the shelf, build brand loyalty, and ensure you’re meeting regulatory requirements. But selecting the right bottle labeler for your specific needs—whether you’re a burgeoning home-based business or a large-scale manufacturer—requires some insight into the fundamentals of labeling technology, best practices, and industry standards.
In this ultimate guide, we’ll explore everything from the basic principles of bottle labeling to advanced automation systems, offering you practical tips and expert insights to help you make the best possible decision. By the time you finish reading, you’ll know how to pick a labeler that aligns with your operational goals, your budget, and your brand image. Ready to learn how to achieve perfectly labeled bottles every time? Let’s dive in.
Table of Contents
1. Why Bottle Labeling Matters More Than You Think
When people discuss product branding, conversations often center on logos, color palettes, and packaging design. Labeling can sometimes be treated as an afterthought—yet it’s the first thing customers see when they hold a product in their hands. An expertly placed, visually compelling label fosters immediate brand recognition and trust. Consider the following aspects:
- Shelf Appeal: According to a study by the Point of Purchase Advertising International (POPAI), over 70% of buying decisions occur in-store. A striking label can significantly influence that decision.
- Compliance & Safety: Regulatory bodies like the U.S. Food & Drug Administration (FDA) or the Alcohol and Tobacco Tax and Trade Bureau (TTB) require specific information on certain labels. A good bottle labeler helps you place the required text in a consistent, legible manner.
- Brand Storytelling: In the craft beverage and artisan food movements, labels do more than list ingredients. They share stories, highlight artisanal processes, and evoke emotions. Proper labeling technology ensures these narratives are presented flawlessly.
In other words, labeling isn’t just a checkbox on your to-do list—it’s a fundamental aspect of product presentation and regulatory compliance. That’s why choosing the right bottle labeler matters.
2. Understanding Different Types of Bottle Labelers
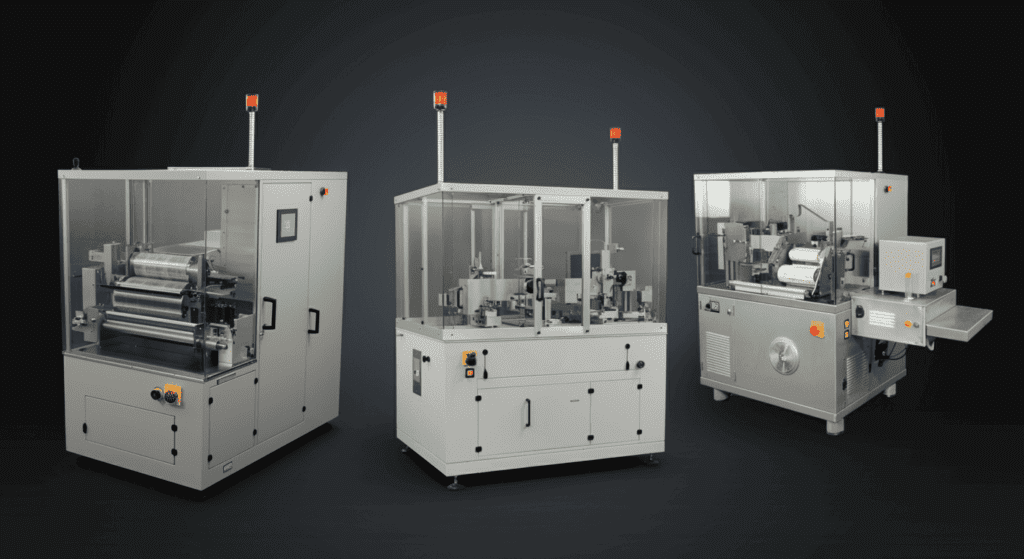
Bottle labelers come in various shapes, sizes, and automation levels. Your choice depends on factors such as your production volume, labor costs, budget constraints, and the complexity of your label designs.
2.1 Manual Bottle Labelers
- How They Work: Operated by hand, where an operator manually positions the bottle and rolls or presses the label onto the container.
- Ideal For: Small businesses with low production volumes, home brewers, boutique skincare lines, or test product runs.
- Pros:
- Low initial investment
- Compact and portable
- Simple to operate with minimal training
- Cons:
- Limited speed and consistency
- Operator fatigue can lead to irregular placements
Despite these drawbacks, manual labelers are cost-effective solutions for startups or niche manufacturers who don’t need to churn out thousands of bottles per hour.
2.2 Semi-Automatic Bottle Labelers
- How They Work: A semi-automatic machine requires some operator interaction (usually placing and removing bottles), but the label application process is mechanized.
- Ideal For: Mid-sized operations that have outgrown manual methods but aren’t quite ready for full automation.
- Pros:
- Faster and more consistent than manual labelers
- Generally more affordable than fully automated systems
- Still requires human oversight, which can be useful for quality control
- Cons:
- Labor costs remain significant
- Throughput may be insufficient for very large-scale operations
Semi-automatic labelers offer a sweet spot for businesses in growth mode, balancing efficiency with reasonable capital outlay.
2.3 Automatic Bottle Labelers
- How They Work: Fully automated systems feed bottles along a conveyor and apply labels without direct human intervention. Some advanced units can apply multiple labels per container (front, back, and neck) in a single pass.
- Ideal For: High-volume manufacturers, co-packers, and any operation that values speed, consistency, and scalability.
- Pros:
- Maximizes throughput and efficiency
- Minimizes labor costs
- Delivers precise, repeatable label placement
- Cons:
- High upfront cost
- Requires more complex setup and maintenance
- Steeper learning curve for operators
If your target is to label thousands—or even tens of thousands—of bottles daily, full automation might be the only viable route to maintain high efficiency and quality standards.
3. Key Features to Look For in a Bottle Labeler
No matter which type of machine you choose, you should assess these critical features before purchasing:
- Label Applicator Versatility
Look for systems that can handle different label materials (paper, plastic, foil) and adhesives (hot melt, pressure-sensitive). Versatility ensures you won’t have to replace your machine if you change your label design. - Adjustable Settings
The ability to fine-tune label placement, speed, and tension is crucial. A good bottle labeler offers easy adjustments to accommodate various bottle shapes and sizes. - Throughput & Speed
Match the labeler’s rated speed (bottles per minute/hour) to your production goals. Overshooting speed requirements can waste capital; undershooting leads to production bottlenecks. - Accuracy & Consistency
Look for features like guide rails, sensors, and servo motors that help maintain label alignment. Consistent label placement builds consumer trust and reinforces brand quality. - Ease of Maintenance
Machines with fewer moving parts generally require less frequent servicing. Check for readily available spare parts and comprehensive customer support. - Space & Footprint
If you’re limited on factory floor space or operate out of a small workshop, consider the machine’s dimensions and ease of installation.
4. Industry-Specific Labeling Requirements
Every industry has its set of labeling regulations and market norms. Understanding these nuances is pivotal to selecting the right bottle labeler and designing your labels effectively.
4.1 Food & Beverage Industry
- Regulatory Bodies: FDA, TTB for alcoholic beverages, and other local authorities.
- Key Label Elements: Ingredient lists, nutritional facts, allergen warnings, net quantity, and UPC barcodes.
- Labeler Considerations:
- Ability to place front and back labels accurately
- Options for tamper-evident or shrink sleeve labeling (if required)
- Sanitary and washdown-compatible designs for food safety compliance
4.2 Cosmetics & Personal Care
- Regulatory Bodies: FDA for cosmetic labeling in the United States, plus international bodies for export.
- Key Label Elements: Ingredient list in descending order, product volume, brand claims (e.g., organic, cruelty-free).
- Labeler Considerations:
- High aesthetic standards for premium brand perception
- Ability to handle various container shapes (rounded, oval, tapered)
- UV or water-resistant label options for bathroom or shower products
4.3 Pharmaceuticals & Nutraceuticals
- Regulatory Bodies: FDA for drug and supplement facts, plus relevant international bodies.
- Key Label Elements: Batch numbers, expiration dates, dosage information, and disclaimers.
- Labeler Considerations:
- Extremely high accuracy to avoid mislabeling
- Capabilities for lot coding, barcodes, and tamper-evident seals
- Potentially specialized software integration for serialization
4.4 Industrial Chemicals & Cleaning Products
- Regulatory Bodies: Environmental Protection Agency (EPA), Occupational Safety and Health Administration (OSHA), and international equivalents.
- Key Label Elements: Hazard symbols (e.g., GHS pictograms), safety instructions, chemical ingredients.
- Labeler Considerations:
- Durability to handle more corrosive or abrasive environments
- Compatibility with large or oddly shaped containers
- High-adhesion label material that withstands chemicals or industrial handling
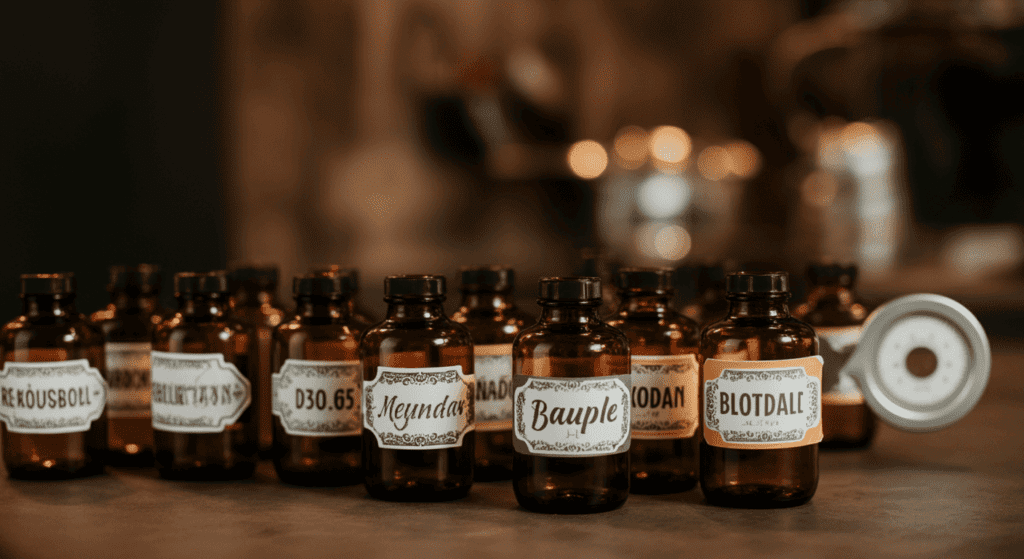
5. How to Choose the Right Bottle Labeler for Your Business
Selecting a bottle labeler entails more than just picking the most advanced machine within your budget. Each business has unique operational, financial, and branding needs.
5.1 Assessing Production Volume
- Small Batch: Manual or semi-automatic machines might be sufficient, especially if you produce under a few thousand bottles weekly.
- Growing Mid-Range: A semi-automatic labeler can handle moderate volumes without huge labor costs.
- High Volume: Fully automated systems become a necessity once you’re consistently producing thousands of bottles per day.
5.2 Budget Considerations
- Initial Investment vs. Operating Costs: A lower-cost manual labeler has minimal upfront cost but high labor expenses. A fully automated system costs more initially but can slash labor needs in the long run.
- Leasing & Financing: Some manufacturers offer leasing or financing plans. Crunch the numbers to see if the monthly payments align with your cash flow.
5.3 Label Material & Adhesive Compatibility
Not all machines handle every label material seamlessly. If your brand identity relies on high-end metallic foils or textured papers, ensure your chosen labeler supports these options.
5.4 Customization & Future Scalability
If your product line might expand to different bottle shapes or sizes, or you foresee significantly higher sales volumes, invest in a labeler that can grow with you. Modular or upgradable systems may have a higher price tag but save you money in the long run.
6. Step-by-Step Guide to Perfect Label Placement
Selecting the ideal bottle labeler is half the battle. You also need to master the practical aspects of label application to present your products in the best light.
6.1 Bottle Preparation
- Clean & Dry: Residues from manufacturing or filling can compromise label adhesion.
- Temperature Considerations: Ensure bottles are at the recommended application temperature for your label adhesive.
- Inspect for Defects: Discard bottles with cracks, deformities, or contaminants that could ruin label placement.
6.2 Label Selection & Design
- Material Choice: Paper, synthetic, or foil-based labels each have unique visual and functional properties.
- Graphics & Branding: High-resolution images, legible fonts, and consistent color schemes build brand identity.
- Regulatory Text: List ingredients, net weight, or disclaimers exactly as required by law.
- Proofing & Testing: Print samples and apply them to actual bottles to test durability and overall look.
6.3 Calibration & Setup of Your Bottle Labeler
- Machine Alignment: Adjust guide rails or bottle holders so each container moves into the exact labeling position.
- Label Web Tension: Improper tension can cause the label to skew or tear.
- Speed Synchronization: For automated lines, match the label dispensing speed to the conveyor speed.
- Sensor Checks: Photoelectric or ultrasonic sensors detect bottle positioning. Confirm they’re aligned and calibrated.
6.4 Quality Control & Troubleshooting
- Visual Inspections: Regular spot checks ensure the label is straight and bubble-free.
- Adhesion Tests: Lightly rub the label edges to check for lifting or curling.
- Machine Maintenance: Clean the rollers, sensors, and any part that contacts labels or bottles.
- Root Cause Analysis: If a batch of labels is misapplied, evaluate whether the issue stems from the labeler, the label material, or human error.
7. Advanced Automation: When Is It Time to Upgrade?
As your business scales, the manual or semi-automatic solution that once served you well may become a bottleneck—pun intended. Here are some indicators it might be time to upgrade to an automated bottle labeler:
- Exceeding Production Capacity: Your current system can’t keep up with orders, leading to shipping delays and lost sales.
- High Labor Costs: Skilled labor for manual or semi-automatic labeling might be more expensive than financing an automated system over the long term.
- Frequent Human Error: Label misplacements can damage brand reputation, especially if they become a recurring issue.
- Complex Labeling Needs: You require multi-label applications (front, back, neck, security seal) and desire consistent, high-speed accuracy.
Modern automated labelers offer advanced features like programmable logic controllers (PLCs), servo-driven label applicators, and integrated vision systems that verify accurate label placement in real time. While the initial cost can be intimidating, the long-term gains in efficiency, consistency, and labor savings often justify the investment.
8. Maintenance & Best Practices for Longevity
Proper care of your bottle labeler ensures a long operational life and consistent label placement.
- Scheduled Cleaning: Dust, adhesive residue, and bottle debris can accumulate on rollers, belts, and sensors. Wipe down or blow off components regularly.
- Lubrication: If the manufacturer recommends lubricating mechanical parts, follow the specified intervals and use the correct lubricants.
- Software Updates: Automated labelers often have firmware or software updates. Installing these can improve performance and fix bugs.
- Operator Training: Well-trained staff catch small problems before they become larger issues. Periodic refresher courses help maintain high quality.
- Backup Components: Keep essential spares like drive belts, sensors, and rollers on hand. When a part inevitably wears out, you’ll minimize downtime.
9. Cost-Benefit Analysis: Is the Investment Worth It?
Investing in a bottle labeler—especially an automated one—is a significant financial decision. A straightforward cost-benefit analysis can clarify whether the purchase is prudent.
- Direct Costs: Purchase price, installation, maintenance, and energy consumption.
- Indirect Costs: Labor time saved, fewer label errors, improved brand perception, and increased production capacity.
- ROI Timeline: Many businesses find that an automated labeler pays for itself within a year or two, especially when labor and waste reduction are factored in.
As an example, imagine a mid-sized brewery that invests in a semi-automatic labeler for $20,000. If this upgrade saves them $2,000 per month in labor costs and reduces labeling errors by 20%, they might recover their initial outlay in under a year. Moreover, an efficient labeling process boosts output and frees employees to tackle other tasks like product development or marketing.
10. Frequently Asked Questions (FAQ)
Q1: What is the difference between a manual and an automatic bottle labeler?
A manual bottle labeler requires the operator to hand-position each bottle and apply the label manually. It’s generally best for small batches or startup ventures. An automatic bottle labeler, on the other hand, automates the entire process. Bottles travel on a conveyor, and the label is applied without direct human intervention, making it ideal for high-volume or high-speed operations.
Q2: How can I ensure accurate label placement on tapered or uniquely shaped bottles?
Unique shapes can challenge even the best bottle labeler. Look for machines offering adjustable rollers, sensors, or specialized attachments designed for unusual geometries. Running test batches and calibrating your labeler carefully can also help guarantee consistent placement.
Q3: What type of label material works best for beverage bottles?
For beverage bottles that may be refrigerated or immersed in ice, water-resistant or synthetic labels such as polypropylene or polyester are often recommended. These materials resist moisture damage and maintain a vibrant appearance even under damp conditions. Always confirm your labeler can handle the material’s thickness and adhesive type.
Q4: How do I comply with regulatory requirements for food and beverage labels?
Check guidelines from the FDA (or the equivalent authority in your region) for ingredient listing, nutritional facts, and net quantity declarations. If you’re producing alcoholic beverages, consult the TTB for alcohol content labeling rules. Ensure your label layout leaves enough space for all mandated information, and test-run a few labeled bottles to verify compliance.
Q5: Are there financing options available for high-end automatic labelers?
Yes. Many labeler manufacturers and equipment financing companies offer lease or financing plans that break down the cost into manageable monthly payments. The key is to weigh the monthly cost against the productivity gains and labor savings you’ll enjoy from an automated system.
Conclusion
A well-applied label can be the difference between a product that blends into the background and one that captivates shoppers from the moment they see it on the shelf. From manual labelers that help small-scale artisans maintain hand-crafted charm, to fully automated systems that power high-volume production lines, there’s a bottle labeler for every business need. By considering factors like production volume, budget, label materials, and compliance requirements, you can choose a machine that not only meets your current demands but also grows with you.
Remember, labeling isn’t just an operational detail—it’s a critical component of brand storytelling, consumer trust, and regulatory compliance. The investment you make in the right labeler pays dividends in labor savings, fewer product returns due to mislabeling, and an elevated brand image.
Stay Connected with EngiTech
EngiTech is your trusted source for in-depth knowledge on industrial mechanical engineering machines and technologies. Stay ahead with the latest innovations, expert insights, and practical guides designed to help you make informed decisions for your business and engineering needs. Join our growing community of professionals and industry leaders to stay updated and competitive in the ever-evolving world of industrial technology.