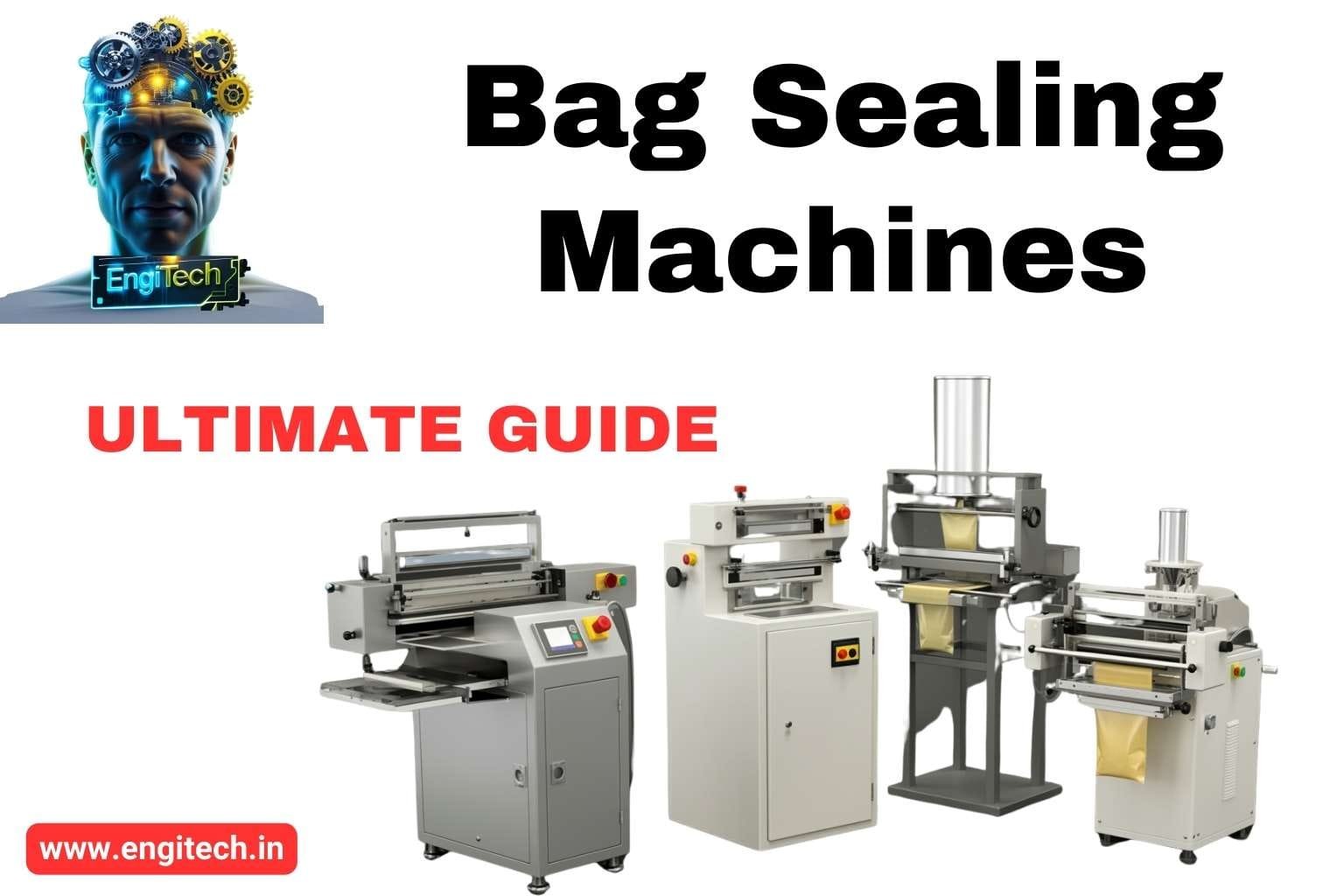
Imagine spending hours meticulously packing products—whether it’s snacks, electronics, or medical supplies—only to find that your seals are inconsistent or your bags are prone to leaks. It’s frustrating, it costs money, and it can damage your brand reputation. A bag sealing machine addresses these pain points by ensuring airtight, reliable seals that keep products fresh, safe, and presentation-ready.
In this comprehensive guide, you will discover the different types of bag sealing machines, how to pick the right one for your business needs, and advanced tips to optimize your packaging line for efficiency. Whether you’re a startup looking to streamline production or a large enterprise aiming for peak performance, this ultimate guide will help you achieve perfect seals every single time.
Table of Contents
1. Why Bag Sealing Machines Matter
When it comes to packaging, few components are as critical as the seal. After all, a package that can’t hold its contents securely is doomed from the start. Bag sealing machines play a pivotal role in various industries, from food processing to pharmaceuticals. Here’s why these machines are indispensable:
- Product Integrity: A well-sealed bag prevents contamination, spoilage, and tampering, preserving product quality and safety.
- Extended Shelf Life: An airtight seal can significantly lengthen a product’s usability, especially in the case of perishable goods like fresh produce or meat.
- Professional Presentation: Crisp, secure seals look more polished and make your products more appealing to customers.
- Compliance with Regulations: Many industries must adhere to strict packaging guidelines. A reliable bag sealing machine helps maintain compliance with safety and quality standards.
- Cost Efficiency: Reducing product waste and returns due to faulty packaging translates into lower operational expenses.
Whether you run a small artisanal food business or manage a large-scale manufacturing operation, leveraging a bag sealing machine ensures that every bag you seal meets the highest standards of quality.
2. How a Bag Sealing Machine Works: The Basics
A bag sealing machine’s core function is to fuse layers of bag material into a sturdy, leak-proof seal. While there are various models and types, most bag sealing machines operate on a few common principles:
- Heat Application: Many machines rely on heated bars or strips to melt the plastic layers at the point of contact. Once the material fuses and cools, the seal hardens.
- Compression: Along with heat, precise pressure is applied to ensure the molten plastic is pressed firmly together.
- Cooling & Solidification: After the bag’s edges melt, the seal area cools down quickly, locking the material in place.
- Automation Levels: Ranging from manual impulse sealers to fully automated continuous band sealers, bag sealing machines can be tailored to the production pace you need.
Understanding these fundamentals helps you troubleshoot minor issues, optimize settings, and get the most out of your equipment.
3. Types of Bag Sealing Machines
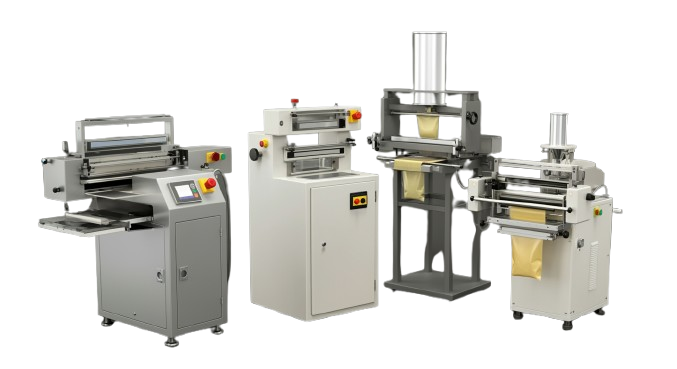
Not all bag sealing machines are created equal. From tabletop impulse sealers suitable for small businesses to high-speed industrial continuous band sealers, there’s a machine for every packaging requirement. Here’s an in-depth look at the most common types:
3.1 Impulse Sealers
- What They Are: Impulse sealers use a brief, high-current pulse of electricity to heat a sealing wire that bonds the bag.
- Ideal For: Low-to-moderate production volumes, small bag sizes, and businesses needing a budget-friendly yet reliable option.
- Advantages:
- Energy-efficient (current flows only when sealing).
- Easy to operate with minimal training.
- Suitable for sealing polyethylene and polypropylene materials.
- Limitations:
- Not optimal for continuous high-volume production.
- Seal width may be limited.
3.2 Heat Sealers
- What They Are: Heat sealers provide consistent, often adjustable, heat along a sealing bar to fuse bag layers.
- Ideal For: Medium-to-high production volumes, diverse bag materials like laminated films or foil.
- Advantages:
- Consistent heat application suitable for thicker materials.
- Adjustable temperature controls for various bag types.
- Usually faster than basic impulse sealers.
- Limitations:
- Consumes more power due to continuous heating.
- May require cooling mechanisms or fans in high-speed settings.
3.3 Continuous Band Sealers
- What They Are: Continuous band sealers use conveyor belts to move bags through heated sealing sections, perfect for automating a production line.
- Ideal For: High-volume operations, especially in food packaging, pharmaceuticals, and large-scale manufacturing.
- Advantages:
- Rapid and consistent sealing speed.
- Can handle different bag materials and thicknesses.
- Often equipped with date coding or embossing features.
- Limitations:
- Higher initial investment compared to simpler sealers.
- Requires more maintenance due to moving parts.
3.4 Vacuum Sealers
- What They Are: Vacuum sealers extract air from the bag before sealing, prolonging shelf life for products sensitive to oxygen.
- Ideal For: Food items like meat, cheese, and nuts; electronics and medical devices needing moisture-free packaging.
- Advantages:
- Increases product shelf life.
- Protects against freezer burn and oxidation.
- Some models allow gas flushing for delicate products.
- Limitations:
- Generally more expensive.
- Not all product types need vacuum packaging.
3.5 Specialty Sealers (Ultrasonic, Induction, etc.)
- What They Are: These include ultrasonic sealers, which use high-frequency vibrations instead of heat, and induction sealers commonly used for bottle caps.
- Ideal For: Niche applications where heat might damage the product or when specialized seals (like tamper-evident seals) are needed.
- Advantages:
- Reduced risk of heat-related damage.
- Often more precise and faster for specialized needs.
- Limitations:
- High-cost equipment.
- May require specialized bag materials or formats.
Choosing the right type of bag sealing machine depends on multiple variables, including your production scale, budget, and the specific materials you’re sealing.
4. Choosing the Right Sealer: Key Considerations
Whether you’re upgrading from a manual process or selecting your first machine, choosing the right bag sealer involves a nuanced approach. Below are the key factors to consider:
4.1 Production Volume
- Low to Moderate Volume: An impulse sealer or a basic heat sealer usually suffices.
- High Volume: A continuous band sealer or automated system is more cost-effective in the long run.
4.2 Bag Material and Thickness
- Poly Bags & Lightweight Films: Impulse sealers and heat sealers work well.
- Foil or Multi-Layer Laminates: Requires a sealer with adjustable temperature controls, typically a heat sealer or continuous band sealer.
4.3 Budget Constraints
- Initial Costs vs. Operational Costs: While impulse sealers are cheaper to buy, they might not be efficient for large operations. Continuous band sealers are pricier upfront but can reduce labor and packaging time significantly.
4.4 Additional Features
- Coding or Embossing: Some sealers can print batch codes or expiration dates on the seal.
- Nitrogen Flushing or Vacuum: Ideal for products that are sensitive to air.
- Portability: Smaller tabletop models are easy to move around; industrial sealers are typically fixed in one location.
4.5 Regulatory and Quality Requirements
- Food Safety Standards: If you’re packaging food, make sure the machine meets local health regulations (e.g., FDA standards in the U.S.).
- ISO or GMP Compliance: For pharmaceutical or medical packaging, consider machines that can integrate seamlessly into a certified production environment.
By analyzing these considerations, you can narrow down your options and invest in a bag sealing machine that aligns with both your production goals and budgetary constraints.
5. Industry-Specific Applications
A bag sealing machine is versatile enough to serve multiple industries, each with unique requirements:
5.1 Food & Beverage
- Common Uses: Sealing snacks, coffee beans, powdered drink mixes, fresh produce.
- Key Requirements: Hygienic design, adjustable temperature for various packaging films, possibly nitrogen flushing to extend shelf life.
5.2 Pharmaceuticals & Healthcare
- Common Uses: Sterile packaging for medical devices, samples, powders, and pills.
- Key Requirements: Highly precise sealing, compliance with standards like ISO 11607, potential integration with cleanroom operations.
5.3 Electronics
- Common Uses: Anti-static or moisture-barrier bags for circuit boards and components.
- Key Requirements: Reliable seals to protect against humidity, static electricity, and dust.
5.4 Industrial & Chemical
- Common Uses: Packaging granular chemicals, fertilizers, or construction materials.
- Key Requirements: Durable sealing for heavier, thicker bags; advanced sealing materials that resist corrosive substances.
5.5 E-commerce & Retail
- Common Uses: Poly mailers for apparel, small gadgets, and other e-commerce items.
- Key Requirements: Fast throughput, tamper-evident seals, aesthetically pleasing finishes.
Identifying your industry’s specific demands ensures that you choose a bag sealing machine that delivers consistent, high-quality results.
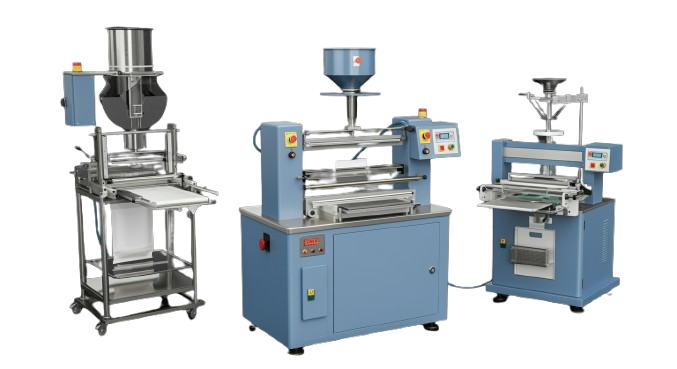
6. Step-by-Step Guide to Setting Up Your Bag Sealing Machine
Setting up your new bag sealing machine correctly from Day One can save you from a slew of headaches later on. Here’s a concise roadmap:
- Unpack & Inspect
- Carefully unbox the machine.
- Verify that all parts, cables, and manuals are included.
- Choose an Optimal Location
- Ensure a flat, stable surface for tabletop models.
- For larger industrial machines, pick a space with adequate ventilation and easy access for maintenance.
- Electrical & Safety Checks
- Confirm voltage and power requirements.
- Check for proper grounding to avoid electrical hazards.
- Install Sealing Bars or Belts
- Follow manufacturer guidelines for attaching the heating elements or conveyor belts.
- Ensure everything is tightened and aligned for smooth operation.
- Configure Settings
- Adjust temperature, pressure, and conveyor speed (if applicable) according to bag material.
- Perform a quick test run using sample bags to fine-tune these settings.
- Train Operators
- Provide hands-on training for staff.
- Emphasize safety procedures and routine checks.
- Document & Store Manuals
- Keep user manuals and service guides accessible.
- Maintain a record of initial calibration settings for future reference.
By following these steps meticulously, you set a solid foundation for your packaging line to operate with minimal downtime and maximum efficiency.
7. Best Practices for Optimal Seals
Producing perfect seals consistently can be challenging without a well-thought-out approach. Here are some best practices to keep in mind:
7.1 Preheat and Calibration
- Why It Matters: An underheated sealer results in weak, inconsistent seals, while overheating can melt the bag material.
- Actionable Tip: Run a few test seals each day, especially during shift changes, to confirm temperature settings.
7.2 Material Selection and Preparation
- Why It Matters: Not all plastic films or materials fuse at the same temperature.
- Actionable Tip: Match the bag material to the machine’s temperature range. Remove any moisture or dust from the bag edges before sealing.
7.3 Proper Alignment and Pressure
- Why It Matters: Uneven pressure or misalignment leads to incomplete or crooked seals.
- Actionable Tip: Regularly inspect the sealing jaws or belts for wear. Replace them when necessary.
7.4 Consistent Feed Rate
- Why It Matters: A feed rate that’s too fast can compromise seal integrity, while too slow might cause scorching.
- Actionable Tip: Synchronize conveyor speed (if using a continuous band sealer) with product output to maintain consistency.
7.5 Routine Testing
- Why It Matters: Packaging regulations and quality assurance protocols often require tensile strength tests or leak tests.
- Actionable Tip: Implement weekly or monthly QC checks where you apply gentle pressure or submerge sealed bags in water to detect leaks.
Applying these best practices significantly reduces the likelihood of faulty seals, customer returns, and wasted material.
8. Maintenance and Troubleshooting
Even the most high-end bag sealing machine can run into hiccups if not maintained properly. Below are vital tips and a quick troubleshooting guide:
8.1 Preventive Maintenance
- Regular Cleaning: Wipe down sealing bars or belts to remove residue from melted plastic.
- Lubrication: For machines with moving parts, follow manufacturer guidelines for lubrication.
- Inspection: Conduct routine checks for signs of wear, including cracks in the sealing bar or frayed wires.
8.2 Common Issues & Fixes
- Weak or Incomplete Seals
- Possible Causes: Incorrect temperature, insufficient pressure, dirty or worn sealing bar.
- Solution: Increase temperature incrementally, adjust pressure settings, or replace worn parts.
- Overheating or Melting Bags
- Possible Causes: Temperature set too high, machine left on without cooldown breaks.
- Solution: Lower temperature settings, schedule brief cooldown intervals if operating continuously.
- Crooked Seals
- Possible Causes: Misaligned conveyor belt or sealing bars.
- Solution: Re-align equipment components and ensure the bag feeds straight into the sealer.
- Machine Won’t Turn On
- Possible Causes: Blown fuse, loose power connection, or internal electrical fault.
- Solution: Check power source, replace fuses, or consult a certified technician if needed.
Incorporating a maintenance schedule into your standard operating procedures (SOPs) can minimize downtime and extend the lifespan of your equipment.
9. Emerging Trends in Sealing Technology
The packaging industry is evolving rapidly, and the bag sealing machine is no exception. Staying updated on new developments can give your business a competitive edge. Here are some trends worth watching:
9.1 Smart Sensors and IoT Integration
Modern machines are increasingly equipped with sensors that monitor temperature, seal integrity, and real-time performance. This data can be integrated into an IoT (Internet of Things) platform, enabling predictive maintenance and remote monitoring.
9.2 Sustainability in Packaging
As consumers and governments place more emphasis on eco-friendly practices, manufacturers are developing sealers that work efficiently with biodegradable or compostable films. Innovations in heat application also aim to lower energy consumption.
9.3 Automation and Robotics
For large-scale operations, robotic arms and automated conveyor systems are streamlining the packaging process. Bag sealing machines can be part of a fully automated line that includes filling, labeling, and palletizing.
9.4 Laser Sealing and Ultrasonic Innovations
These cutting-edge technologies minimize heat exposure, making it possible to seal delicate, heat-sensitive materials. Laser sealing can be more precise and faster for certain specialized applications.
Staying ahead of these trends not only optimizes your packaging process but also positions your brand as forward-thinking and environmentally responsible.
FAQs: Your Top Bag Sealing Machine Questions Answered
Q1. How do I determine if my bag sealing machine is food-safe?
Look for machines that comply with local and international hygiene standards, such as USDA or FDA regulations in the United States. Stainless steel construction and easy-to-clean surfaces are also strong indicators of food-safe design.
Q2. Which bag materials work best with an impulse sealer?
Impulse sealers are generally best suited for polyethylene (PE) and polypropylene (PP) bags with relatively thin gauges. Thicker or multi-layer films might require higher-end or continuous heat sealers.
Q3. How often should I replace the sealing elements?
This depends on the frequency of use and the thickness of the materials sealed. Signs like inconsistent sealing temperatures, obvious wear, or fraying on the wire or Teflon strip indicate that it’s time for a replacement.
Q4. Can I seal multiple layers or multiple bags at once?
Sealing multiple layers is possible if your machine’s temperature and pressure settings can handle it. However, stacking multiple bags simultaneously is often discouraged because it can lead to inconsistent seals or partial fusion.
Q5. Is vacuum sealing necessary for all food products?
No. Vacuum sealing is essential for products highly sensitive to oxygen (like meat, cheese, or coffee). If you’re sealing snack foods or items that aren’t prone to rapid spoilage, a traditional heat or impulse sealer may suffice.
Real-World Success Stories
Nothing speaks louder than real-world examples. Businesses across different sectors have leveraged a bag sealing machine to transform their packaging processes:
Case Study 1: Gourmet Coffee Startup
- Challenge: A small coffee brand struggled with inconsistent bag seals leading to customer complaints about stale beans.
- Solution: They invested in a continuous band sealer with a nitrogen-flushing feature.
- Result: Products stayed fresher for longer, customer satisfaction skyrocketed, and they reported a 30% increase in repeat purchases.
Case Study 2: Online Apparel Store
- Challenge: This e-commerce retailer was using manual sealing methods for poly mailers, causing slow turnaround and a high error rate.
- Solution: A semi-automatic impulse sealer sped up their order fulfillment process.
- Result: Packaging time was cut in half, leading to fewer shipping delays and improved customer reviews.
Case Study 3: Medium-Sized Electronics Manufacturer
- Challenge: Sensitive components were frequently damaged by humidity and electrostatic discharge during transit.
- Solution: The company integrated a vacuum sealer with anti-static bag materials into their line.
- Result: A dramatic reduction in product returns and a reinforced reputation for quality, boosting B2B partnerships.
These examples illustrate how choosing the right bag sealing machine and optimizing its use can create tangible benefits—from product integrity to brand credibility.
Conclusion: Sealing Your Path to Success
A bag sealing machine is more than just a piece of equipment; it’s a strategic investment in the quality, efficiency, and reputation of your brand. Whether you’re shipping artisanal goods to discerning customers or producing industrial components in bulk, a well-chosen and well-maintained sealer can make all the difference. By understanding the various types of sealers, following best practices, and staying informed about technological advancements, you’ll create packaging that stands out for its reliability and professionalism.
Remember, the journey doesn’t end at purchasing a bag sealing machine. Proper training, maintenance, and a willingness to adapt to emerging trends will ensure you maximize your return on investment. Start small if you must, but keep an eye on how each step can enhance your overall packaging line. In today’s competitive market, that attention to detail can define your success.
Stay Connected with EngiTech
EngiTech is your trusted source for in-depth knowledge on industrial mechanical engineering machines and technologies. Stay ahead with the latest innovations, expert insights, and practical guides designed to help you make informed decisions for your business and engineering needs. Join our growing community of professionals and industry leaders to stay updated and competitive in the ever-evolving world of industrial technology.