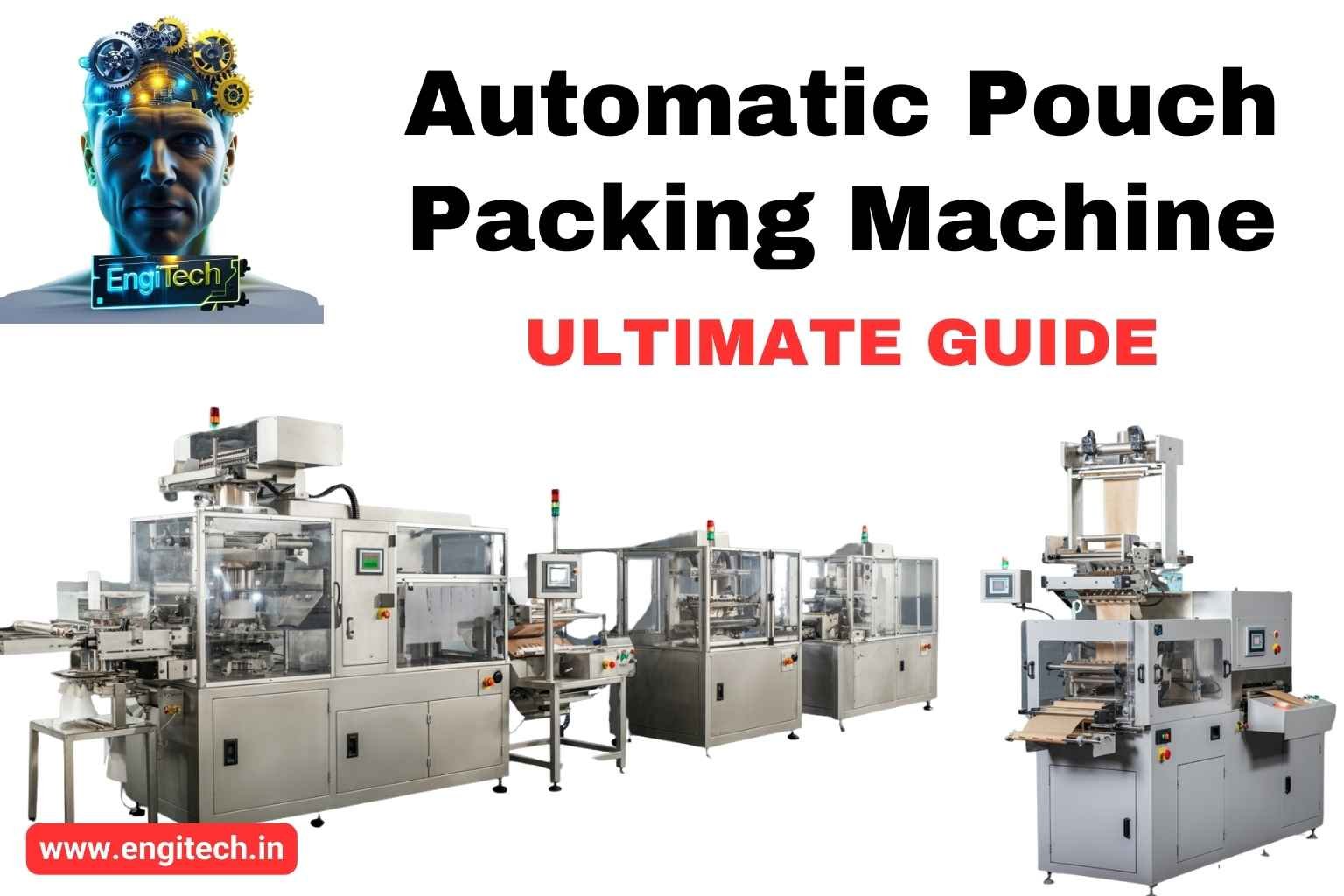
In a world where consumers expect speed, convenience, and reliability, businesses across various sectors are constantly looking for ways to optimize their packaging processes. That’s where the Automatic Pouch Packing Machine comes in—an innovative piece of packaging equipment that quickly and accurately fills, seals, and delivers pouches of all sizes and materials.
If you’ve been searching for a way to reduce labor costs, minimize product waste, and stay competitive in an ever-evolving market, you’re in the right place. In this in-depth guide, you’ll discover everything you need to know about automatic pouch packing machines, including how they work, the benefits they offer, and how to select the perfect pouch packing solutions for your specific business.
By the end, you’ll be equipped with expert-backed insights and actionable advice, ensuring you’re prepared to implement or upgrade to the most efficient packaging solutions available.
Table of Contents
1. Introduction to Automatic Pouch Packing Machines
From snack foods to industrial chemicals, automatic pouch packing machines have revolutionized how manufacturers, distributors, and retailers handle product packaging. These devices automate the entire process—bag formation, product filling, sealing, and sometimes even labeling—dramatically boosting throughput and consistency.
But what precisely makes an automatic pouch packing machine stand out compared to manual or semi-automatic methods? The short answer: efficiency, accuracy, and reliability. With technological advancements, pouch packing solutions can handle a wide range of product types—solid, liquid, powder, granular—while maintaining exact measurements and minimal waste.
Moreover, as consumer preferences shift toward more sustainable packaging and portion control, the convenience of pouches can’t be understated. Flexible packaging offers lightweight, portable options for end users, which can also translate into lower shipping costs and reduced carbon footprint for businesses.
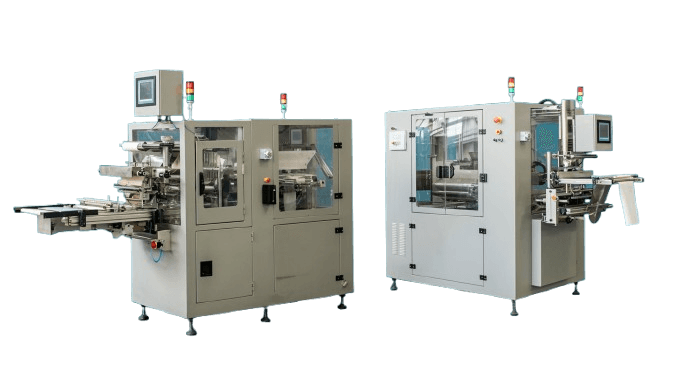
2. How Does an Automatic Pouch Packing Machine Work?
Understanding the mechanics of an automatic pouch packing machine starts with the process flow. While specifics can vary based on make and model, most machines follow a similar sequence:
- Pouch Feeding:
- Pre-formed pouches are typically loaded into a pouch feeding station. Alternatively, with vertical form fill seal machines, the packaging film is pulled from a roll to form the pouch on the spot.
- A set of grippers or a rotary carousel often transports each pouch along different stations.
- Pouch Opening and Shaping:
- Vacuum suction cups or mechanical arms open the pouch.
- Internal air blowers may help fully open and shape it for product filling.
- Product Filling:
- The product—be it a powder, liquid, or solid—is dispensed into the open pouch via a filling station.
- Filling accuracy is managed by weighers, volumetric fillers, or pumps, depending on the product consistency.
- Sealing and Coding:
- The filled pouch passes to a sealing station.
- Heat-sealing or ultrasonic sealing may be used to close the pouch.
- An inkjet or thermal transfer printer might add production dates, batch codes, or other required details.
- Final Discharge:
- The sealed pouch is released onto a conveyor or into a collection bin.
- Optional inspection stations check for seal integrity or weight compliance.
This entire sequence can occur in a continuous loop, with minimal human intervention, drastically reducing the possibility of errors and contamination.
3. Key Benefits of Pouch Packaging Solutions
When you opt for an automatic pouch packing machine, you’re not just investing in hardware—you’re transforming your workflow. Here are the core benefits you can expect:
- Enhanced Efficiency:
Automated packaging systems can process hundreds, even thousands, of pouches per hour, far exceeding the output of manual labor. - Cost Savings:
While the initial investment may seem high, the long-term reduction in labor costs, product waste, and downtime often delivers significant ROI. - Improved Product Quality:
Sealing technology used in automatic machines minimizes air exposure, extending shelf life and preserving flavor, texture, or potency. - Consistent Branding:
Machines that handle printed film rolls or label application ensure each pouch displays uniform branding elements, reinforcing brand recognition. - Reduced Material Waste:
Automation brings precision. Each pouch uses the exact amount of film necessary, leading to less waste and a more eco-friendly operation. - Scalability:
As your product line or order volume expands, many pouch packing solutions can be upgraded or adjusted for higher throughput.
From a marketing standpoint, consistent and high-quality pouches elevate brand image. Customers appreciate tamper-proof seals and clearly labeled packaging, which can help your business gain a reputation for reliability and transparency.
4. Core Components of Automated Packaging Systems
An automatic pouch packing machine isn’t just a single piece of hardware—it’s an integrated system comprising multiple components. Understanding these elements helps you maintain and troubleshoot your equipment effectively:
- Feeding and Conveyor Systems:
- Feeders or conveyors ensure a steady flow of product into the filling station.
- Gripper arms or vacuum cups lift and transport pouches along the system.
- Filling Station:
- Depending on your product, a specialized filler—volumetric cup filler, auger filler, or multihead weigher—will dispense the exact quantity or weight needed.
- Sealing Mechanism:
- Heat sealing uses heated bars to melt and bond the pouch film.
- Ultrasonic sealing uses high-frequency vibrations to create a reliable seal without heat damage.
- Control Panel or Human-Machine Interface (HMI):
- Operators can adjust speed, sealing temperature, filling weight, and other parameters.
- Modern systems often include touchscreens and integrated diagnostics.
- Printing and Labeling Units:
- Inkjet printers, thermal transfer printers, or labeling units mark each pouch with dates, barcodes, or branding elements.
- Sensors and Safety Guards:
- Optical sensors detect if the pouch is correctly placed.
- Emergency stops and safety guards protect operators from moving parts.
By maintaining each component, you prevent downtime and ensure that your entire automated packaging system runs smoothly.
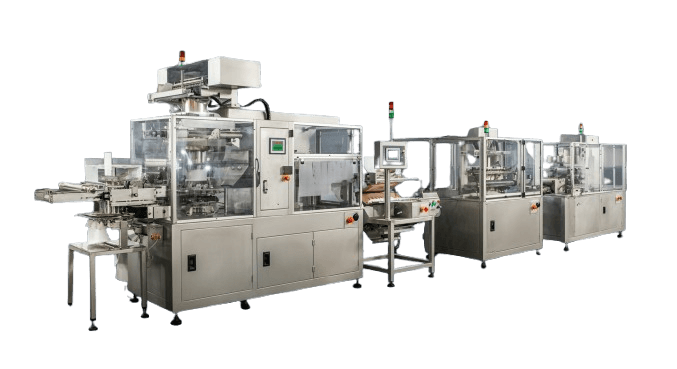
5. Types of Pouches and Materials
One of the major appeals of pouch packaging technology is its versatility. Whether you’re packaging fresh coffee grounds or detergent pods, there’s a pouch format that fits your needs. Below are some common pouch types and materials:
Pouch Types
- Stand-up Pouches (SUP):
Features a bottom gusset, allowing it to stand upright for better shelf presentation. - Flat Pouches:
A simpler design used frequently for single-serving snacks or medical applications. - Spouted Pouches:
Ideal for liquids, yogurts, or sauces; includes a resealable cap. - Retort Pouches:
Made for products requiring high-temperature processing (like ready-to-eat meals).
Materials
- Polyethylene (PE):
Common for food packaging; offers good heat-sealing properties. - Polypropylene (PP):
Known for higher heat resistance; often combined with other layers for improved barriers. - Metallized Films:
Provide excellent moisture and oxygen barriers; used for chips or coffee. - Paper-Poly Laminate:
Offers a more eco-friendly look and feel while maintaining barrier properties.
The material chosen affects factors like shelf life, sealing strength, and print quality. Always confirm compatibility with your packaging equipment and product requirements.
6. Choosing the Right Packaging Equipment
Selecting the ideal automatic pouch packing machine can be daunting, given the array of models and configurations. However, focusing on the following factors can streamline your decision:
- Product Nature
- Powder, liquid, or granule?
- Fragility (snack chips) or viscosity (pastes)?
- Different products may require specialized fillers or sealing mechanisms.
- Production Volume
- Assess your current output and anticipate future growth.
- Choose a machine that can handle peak production comfortably.
- Pouch Size and Type
- Ensure the equipment supports the largest pouch size in your lineup.
- Verify if it can handle multiple pouch formats if needed.
- Budget and ROI
- While price is a big factor, consider the machine’s total cost of ownership (maintenance, spare parts, labor savings).
- Look for financing options or leasing if immediate capital is limited.
- Machine Footprint and Layout
- Match the machine to your facility’s space constraints.
- Plan for easy access for maintenance and cleaning.
- After-Sales Support
- Prioritize brands or vendors with responsive customer service, readily available spare parts, and comprehensive training.
Don’t overlook the role of site audits. Have a packaging expert evaluate your facility to recommend a system that aligns with your operational realities and compliance standards.
7. Advanced Features and Innovations
The packaging industry is continuously evolving, introducing exciting innovations that transform the way manufacturers operate. Here are a few advanced features you might encounter in modern automatic pouch packing machines:
- Smart Sensors and IoT Integration
- Real-time performance monitoring through cloud-based dashboards.
- Predictive maintenance to minimize unexpected breakdowns.
- High-Speed Rotary Systems
- Some machines use a rotary carousel to optimize pouch-handling speed, achieving higher throughput in less space.
- Adaptive Filling Technologies
- Machines that adjust filling parameters based on real-time weight or volume readings.
- Reduces product giveaway and ensures consistent fill levels.
- Automated Changeovers
- Fast, tool-less changeovers from one pouch size or product type to another.
- Ideal for businesses offering multiple SKUs with frequent shifts.
- Enhanced Sealing Mechanisms
- Ultrasonic or laser sealing that reduces heat exposure and improves seal consistency.
- Ideal for delicate products or specialized film materials.
- Vision Inspection Systems
- Integrated cameras that check seal integrity, label placement, or even brand compliance.
- Detects defects before products leave the facility.
Investing in these innovations isn’t just about having the latest technology—it’s also about future-proofing your operations in a rapidly changing marketplace.
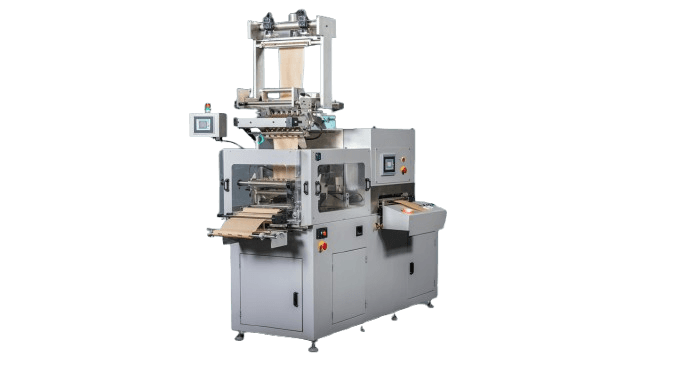
8. Optimizing Efficiency: Best Practices
Even the most advanced automatic pouch packing machine can underperform if not operated optimally. Adopting the following best practices will help you maximize efficiency and minimize downtime:
- Proper Staff Training
- Ensure that machine operators understand not just the “how” but also the “why” behind each step.
- Regular refresher courses keep everyone aligned with best practices.
- Preventive Maintenance Schedule
- Follow the manufacturer’s guidelines for cleaning, lubrication, and part replacements.
- Use checklists to track tasks and deadlines.
- Quality Control Protocols
- Periodically check pouch seals, fill weights, and printing accuracy throughout shifts.
- Quickly isolate and address any variations.
- Data Analysis
- Leverage built-in machine software or external monitoring systems to track output, waste, and downtime.
- Identify bottlenecks and recurring issues for targeted improvements.
- Continuous Improvement
- Encourage feedback from machine operators and production supervisors.
- Adapt your operations based on real-world data and evolving market demands.
By integrating these practices into your daily routine, you set the stage for a consistently high-performing packaging line.
9. Common Industries Using Pouch Packaging Technology
Pouch packaging technology is versatile enough to serve a wide range of sectors. Here are the industries that most frequently benefit from the speed and flexibility of automatic pouch packing machines:
- Food and Beverage
- Snacks, coffee, dried fruits, sauces, and ready-to-eat meals often use stand-up or retort pouches.
- Extended shelf life and portability are key selling points for consumers.
- Pharmaceuticals and Nutraceuticals
- Pill pouches, powder supplements, or single-dose liquids benefit from precise dosing.
- Tamper-evident seals and batch coding maintain regulatory compliance.
- Cosmetics and Personal Care
- Sample-size pouches, liquid soaps, shampoos, and face masks are commonly packaged in flexible formats.
- Resealable pouches are popular for travel convenience.
- Pet Food
- Both dry kibble and wet food options use stand-up pouches with resealable zippers.
- The packaging’s portability and odor containment are big consumer draws.
- Household and Industrial Chemicals
- Detergent pods, cleaning wipes, and chemicals in powdered form benefit from protective, leak-proof pouches.
- Barrier properties ensure product integrity during storage and shipping.
No matter the industry, the core value proposition remains the same: a versatile, cost-effective, and visually appealing way to package products.
10. Cost Analysis and Return on Investment
For businesses contemplating a shift to automated packaging systems, cost is usually the biggest consideration. While the upfront capital expenditure for an automatic pouch packing machine can be substantial, the long-term savings often justify the investment. Here’s how to conduct a thorough cost-benefit analysis:
- Initial Machine Cost
- The price can range from a modest sum for semi-automatic units to significant figures for high-speed, high-tech models.
- Include costs of ancillary equipment like conveyors, labelers, and integrated weighers.
- Operating Costs
- Electricity, compressed air, and maintenance expenses add to your budget.
- Factor in consumables like printing ink or specialized films.
- Labor Savings
- Compare your current labor requirements to run manual or semi-automated lines with future staffing needs post-installation.
- Fewer operators can manage the same—or higher—output.
- Waste Reduction
- Automated systems dispense precise product quantities and use exact amounts of packaging film.
- Lower material waste translates directly to cost savings.
- Increased Throughput and Revenue
- Higher speed and efficiency let you meet larger orders or diversify your product range.
- Reduced lead times can attract more clients, potentially increasing market share.
- ROI Timeline
- Most businesses see a return on their investment within 1-3 years, depending on the production volume and machine cost.
- Plan for a realistic break-even point, then factor in profits from expanded capacity.
By evaluating these variables, you’ll gain a clear picture of how an automatic pouch packing machine can reshape your profitability and competitiveness.
11. Top Maintenance and Troubleshooting Tips
Even the best automatic pouch packing machine requires periodic upkeep. Proactive maintenance not only prolongs machine life but also ensures consistent, high-quality output. Here are some key tips:
- Follow Manufacturer Guidelines
- Adhere to recommended schedules for changing filters, lubricating bearings, or replacing sealing elements.
- Always use approved spare parts to maintain warranty coverage.
- Regular Cleaning
- Remove product residue to prevent contamination or mechanical jams.
- Pay attention to filling stations and seal bars where buildup is common.
- Inspect Seals and Sensors
- Loose or faulty seals lead to product leaks and compromised shelf life.
- Clean and calibrate sensors periodically to maintain accurate pouch detection.
- Temperature Calibration
- For heat-sealing machines, incorrect temperatures are a primary cause of faulty seals.
- Schedule weekly or monthly calibrations using specialized tools.
- Monitor Wear Parts
- Belts, knives, and seal bars degrade over time. Keep a log of replaced parts and track usage to anticipate replacements.
- Stock critical wear parts to avoid long downtime.
- Maintain Proper Tension
- For vertical form fill seal machines, the film roll tension is crucial for proper pouch formation.
- Excess tension causes film tearing; insufficient tension leads to wrinkled seals.
When issues arise, consult the machine’s troubleshooting guide before making drastic adjustments. Simple mistakes in diagnosing a problem can lead to extended downtime or damage to vital components.
FAQs about Automatic Pouch Packing Machines
Q1: Can I pack both solids and liquids on the same automatic pouch packing machine?
Yes, but you need interchangeable filling systems—such as a volumetric filler for solids and a liquid pump or piston filler for liquids. Many modern machines come with modular components, allowing you to switch easily.
Q2: What is the typical speed of an automatic pouch packing machine?
Speeds vary widely, from 30-60 pouches per minute for entry-level models up to 200+ pouches per minute for high-speed, advanced systems. The product type, pouch size, and sealing requirements also influence the throughput.
Q3: How do I know if my product is compatible with a vertical form fill seal machine?
Most dry, free-flowing products—like grains, snacks, or powders—are well-suited for vertical form fill seal (VFFS) machines. If your product is liquid or paste-like, you’ll need a specialized system with appropriate filler and sealing technology.
Q4: Are stand-up pouches always more expensive?
Stand-up pouches often require more complex film structures and sometimes gussets, which can be slightly more expensive. However, their visual impact and ability to stand on a shelf can significantly boost brand visibility, often outweighing the additional cost.
Q5: How critical is film quality for sealing success?
Film quality is extremely important. Inferior or inconsistent film thickness can lead to poor seals, product leakage, and machinery jams. Always source film from reputable suppliers and perform incoming quality checks.
Conclusion: Taking Your Packaging to the Next Level
Investing in an automatic pouch packing machine isn’t just a purchase—it’s a strategic decision that can set your brand apart. By embracing pouch packaging technology, you’ll enjoy faster production, fewer errors, and improved product presentation. Whether you’re packaging granola bars, powdered supplements, or household detergents, the flexibility, speed, and reliability of automated packaging systems can help you meet—and exceed—consumer expectations.
Remember to choose equipment that aligns with your specific production requirements, budget, and growth projections. Plan for continuous improvement by implementing strong maintenance procedures and staying informed about technological innovations. As you optimize your packaging line, you’ll reduce operational costs, enhance your brand image, and ultimately deliver a superior customer experience.
Ready to make the leap? Explore how an automatic pouch packing machine can transform your packaging processes, cut down on waste, and elevate your business to new heights. If you’re unsure which system suits your needs, consider reaching out to a trusted packaging specialist for a personalized evaluation. Don’t let outdated packaging methods hold you back—take the next step toward efficiency and success
If this guide helped you gain a better understanding of automatic pouch packing machines, share it with your network or leave a comment below. Interested in learning more about advanced packaging equipment and pouch packing solutions? Subscribe to our newsletter for insider tips, new product updates, and exclusive industry insights. Drive your business forward by embracing the future of packaging—starting today!
Stay Connected with EngiTech
EngiTech is your trusted source for in-depth knowledge on industrial mechanical engineering machines and technologies. Stay ahead with the latest innovations, expert insights, and practical guides designed to help you make informed decisions for your business and engineering needs. Join our growing community of professionals and industry leaders to stay updated and competitive in the ever-evolving world of industrial technology.