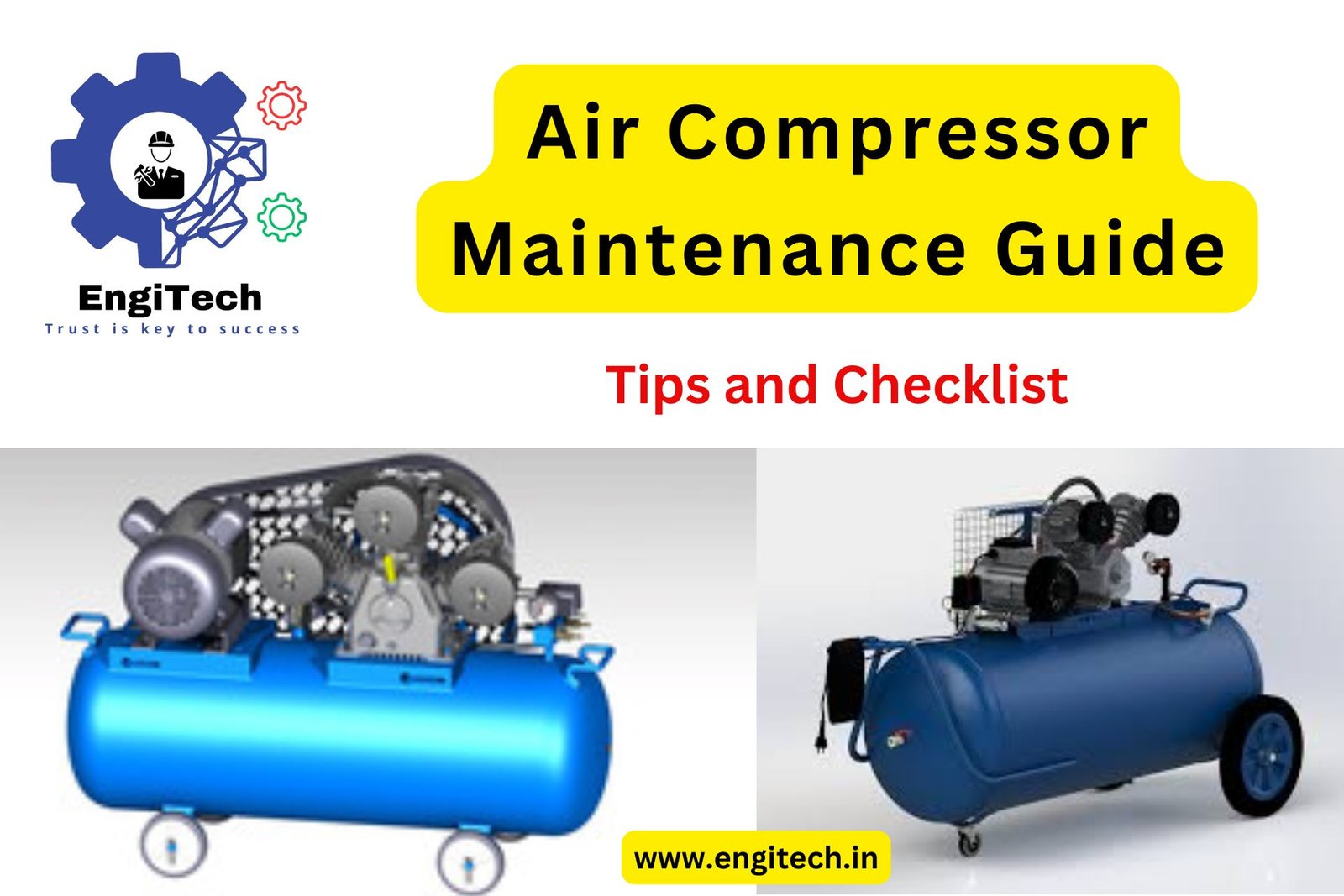
Air compressors are essential for many industries, ensuring seamless operations by powering tools, equipment, and processes. However, like any machinery, regular maintenance is crucial to keep them running efficiently and extend their lifespan. Neglecting maintenance can lead to increased energy costs, frequent breakdowns, and even complete failure.
In this guide, we will provide a detailed maintenance checklist, tips for troubleshooting common issues, and advice to optimize your air compressor’s performance. Whether you are a novice or an experienced operator, this blog equips you with all the necessary insights.
Table of Contents
Why Air Compressor Maintenance Is Important
Proper maintenance offers multiple benefits:
- Enhanced Efficiency: Prevents energy loss due to leaks and blockages.
- Longer Lifespan: Reduces wear and tear, prolonging operational life.
- Lower Costs: Minimizes repair expenses and downtime.
- Consistent Performance: Ensures reliable output for demanding applications.
1. Daily Maintenance Tasks
Regular daily checks keep your air compressor in optimal condition.
Tasks to Perform:
- Inspect Oil Levels:
- For oil-lubricated compressors, check and top off oil levels as needed.
- Use the recommended grade of oil.
- Drain Condensate:
- Remove moisture from the tank to prevent rust and contamination.
- Use an automatic drain valve for convenience.
- Visual Inspection:
- Check hoses and connections for signs of wear, damage, or leaks.
- Ensure all safety features are operational.
2. Weekly Maintenance Tasks
Tasks to Perform:
- Check for Air Leaks:
- Use soapy water to detect leaks in hoses, valves, and fittings.
- Repair leaks promptly to save energy.
- Clean or Replace Filters:
- Inspect air intake filters for dirt and debris.
- Clean reusable filters or replace disposable ones.
- Inspect Belts:
- Ensure belts are properly tensioned and free from cracks.
- Replace damaged or worn-out belts.
3. Monthly Maintenance Tasks
Tasks to Perform:
- Inspect Safety Relief Valve:
- Test the valve to ensure it operates correctly in overpressure situations.
- Check Pressure Levels:
- Verify the tank pressure aligns with manufacturer recommendations.
- Inspect Electrical Components:
- Check wiring and connections for any signs of damage or wear.
- Lubricate Bearings:
- Apply grease to motor and pump bearings if required.
4. Annual Maintenance Tasks
Tasks to Perform:
- Change Oil and Filters:
- Replace oil and filters in oil-lubricated compressors.
- Dispose of used oil responsibly.
- Inspect and Replace Seals:
- Check all seals for wear and replace as needed to prevent leaks.
- Tank Inspection:
- Inspect the interior of the tank for signs of rust or corrosion.
- Professional Service:
- Schedule a comprehensive inspection by a certified technician.
5. Common Issues and Troubleshooting Tips
1. Compressor Overheating
- Causes:
- Low oil levels, blocked filters, or insufficient ventilation.
- Solutions:
- Check and refill oil, clean or replace filters, and ensure adequate airflow.
2. Low Pressure Output
- Causes:
- Leaks, clogged hoses, or faulty valves.
- Solutions:
- Repair leaks, clean hoses, and inspect valves for damage.
3. Excessive Noise
- Causes:
- Loose components, worn-out bearings, or insufficient lubrication.
- Solutions:
- Tighten loose parts, replace bearings, and lubricate moving components.
4. Frequent Cycling
- Causes:
- Faulty pressure switch or undersized compressor.
- Solutions:
- Adjust or replace the pressure switch and evaluate compressor sizing.
6. Energy Efficiency Tips
Optimize Energy Use:
- Fix Air Leaks:
- Regularly inspect and seal leaks to prevent energy waste.
- Use Variable Speed Drives (VSD):
- Adjust motor speed to match demand.
- Monitor Usage Patterns:
- Avoid running compressors during non-peak hours.
Upgrade for Efficiency:
- Consider investing in energy-efficient models like rotary screw or centrifugal compressors.
7. Maintenance Tools and Equipment
Essential Tools:
- Wrenches and screwdrivers.
- Oil funnel and drain pan.
- Filter cleaning kits.
- Leak detection kits (soap solution or ultrasonic devices).
Recommended Accessories:
- Automatic drain valves.
- Pressure gauges.
- Maintenance logbooks.
8. Professional Maintenance Services
While regular in-house maintenance is crucial, professional services ensure deeper inspections.
What Professionals Offer:
- Advanced diagnostics for internal components.
- Calibration of pressure switches and valves.
- Replacement of critical parts like pistons and rotors.
When to Call a Professional:
- Persistent issues despite routine maintenance.
- Annual inspections for high-capacity compressors.
9. Maintenance Schedule Template
Task | Frequency | Notes |
---|---|---|
Check oil levels | Daily | Use recommended oil grade. |
Drain condensate | Daily | Install an auto-drain valve. |
Inspect filters | Weekly | Replace if clogged or damaged. |
Inspect belts | Weekly | Replace worn-out belts. |
Change oil and filters | Annually | Follow manufacturer guidelines. |
Professional servicing | Annually | Schedule with certified experts. |
10. Importance of a Maintenance Log
Keeping a maintenance log helps track:
- Tasks performed and their frequency.
- Replacement of parts and associated costs.
- Trends in compressor performance.
Pro Tip:
Use digital tools or apps for convenient log management and reminders.
Conclusion
Proper air compressor maintenance is essential for operational efficiency, cost savings, and equipment longevity. By following the daily, weekly, monthly, and annual maintenance tasks outlined in this guide, you can prevent costly repairs and ensure optimal performance.
Don’t wait for issues to arise—stay proactive with your maintenance routine. For more expert tips and insights on industrial equipment, explore the resources available on EngiTech.