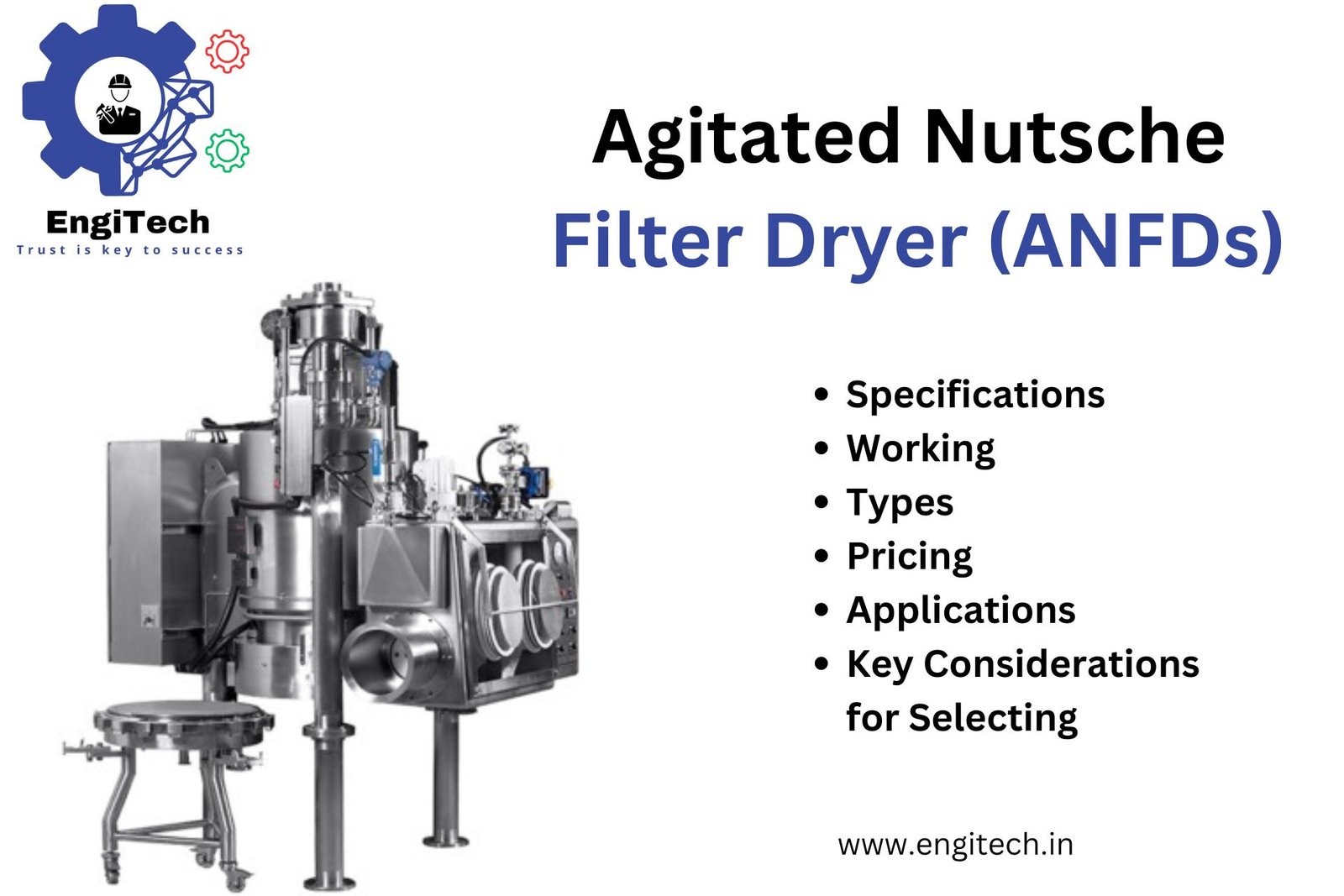
Agitated Nutsche Filter Dryers (ANFDs) serve as versatile equipment in the pharmaceutical, chemical, and food industries, enabling efficient solid-liquid separation processes. By integrating filtration, washing, and drying in a single unit, ANFDs enhance efficiency, cost-effectiveness, and safety. This guide explores the working principles, applications, advantages, and key considerations for selecting and maintaining agitated nutsche filter dryers.
What is an Agitated Nutsche Filter Dryer?
An agitated nutsche filter dryer is a multipurpose unit used for solid-liquid separation. It integrates filtration, washing, and drying into a single system, making it highly efficient and versatile for various industrial applications.
Specifications of Agitated Nutsche Filter Dryers
Construction and Materials
- Material of Construction: Manufacturers typically construct ANFDs from stainless steel, Hastelloy, or glass-lined steel to ensure durability and resistance to corrosion.
- Size and Capacity: ANFDs come in sizes ranging from laboratory-scale (a few liters) to industrial-scale (several thousand liters).
- Design Pressure and Temperature: ANFDs operate under varying pressure conditions (up to 6 bar) and temperatures (up to 200°C), making them suitable for various processes.
Key Components
- Agitator: A motor-driven mechanism stirs the contents, ensuring even distribution and efficient mixing.
- Filter Media: A porous material allows liquid to pass through while retaining solid particles.
- Heating System: This system ensures efficient drying of the filtered solids.
- Control System: The control system manages operation, including temperature, pressure, and agitation speed.
- Inspection Ports: These ports facilitate visual inspection and sampling.
Working Principle of Agitated Nutsche Filter Dryers
The working principle of an ANFD involves several stages:
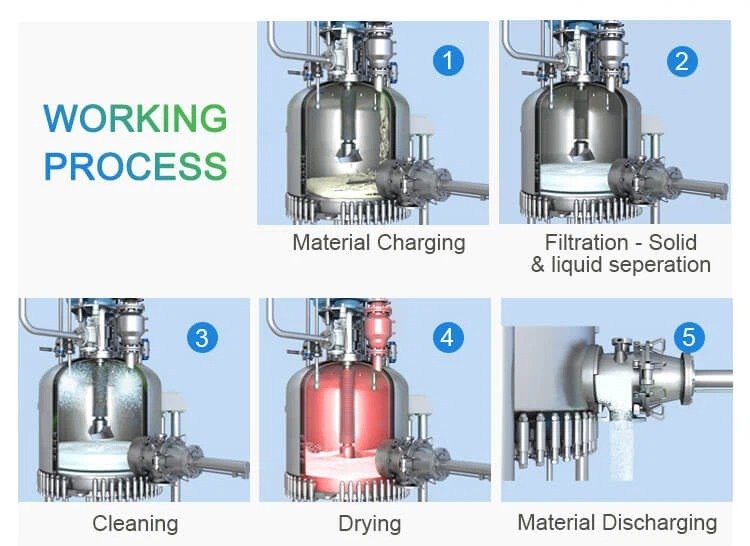
Filtration
- Slurry Feeding: Feed the slurry, a mixture of solid and liquid, into the filter.
- Filtration: Apply pressure or vacuum to separate the liquid from the solids. The agitator ensures even distribution of the slurry over the filter media.
- Cake Formation: The solids form a cake on the filter media, while the liquid passes through.
Washing
- Washing Liquor Addition: Add a washing liquid to remove impurities from the cake.
- Agitation: The agitator ensures thorough mixing, enhancing the washing efficiency.
- Washing Filtration: Filter out the washing liquid, leaving a purified cake.
Drying
- Heating: Heat the filtered cake to evaporate the remaining liquid.
- Agitation: Continuous agitation improves heat transfer and drying efficiency.
- Vacuum Application: Apply a vacuum to expedite the drying process.
Types of Agitated Nutsche Filter Dryers
Glass-Lined Agitated Nutsche Filter Dryer
Glass-lined agitated nutsche filter dryers are particularly suited for processes involving highly corrosive substances. The glass lining provides excellent chemical resistance and ensures product purity by preventing contamination.
- Applications: Ideal for pharmaceuticals, chemicals, and food processing industries where contamination must be avoided.
- Advantages: High chemical resistance, easy to clean, and maintain product purity.
Agitated Pressure Nutsche Filter Dryer
Agitated pressure nutsche filter dryers can operate under high pressure, enhancing filtration efficiency and reducing processing time.
- Applications: Suitable for processes requiring rapid filtration and drying, such as pharmaceuticals and specialty chemicals.
- Advantages: Faster processing times, higher throughput, and improved filtration efficiency.
Pharma Application of Agitated Nutsche Filter Dryers
Agitated Nutsche Filter Dryers (ANFDs) play a crucial role in various industries due to their versatility and efficiency in solid-liquid separation, washing, and drying processes.
Pharmaceuticals
In the pharmaceutical industry, ANFDs are essential for producing high-purity active pharmaceutical ingredients (APIs) and intermediates. Their ability to handle sensitive materials under controlled conditions ensures the quality and safety of pharmaceutical products.
- API Production: ANFDs facilitate the filtration, washing, and drying of APIs, ensuring they meet strict purity standards.
- Intermediate Processing: These dryers handle the intermediate stages of drug production, maintaining product integrity and consistency.
- Sterile Processing: ANFDs can operate in sterile environments, essential for producing injectable drugs and other sterile products.
- High Potency Compounds: They are particularly useful for high-potency compounds that require precise handling to avoid contamination and ensure worker safety.
- Continuous Processing: ANFDs support continuous processing, enhancing efficiency and reducing batch-to-batch variations.
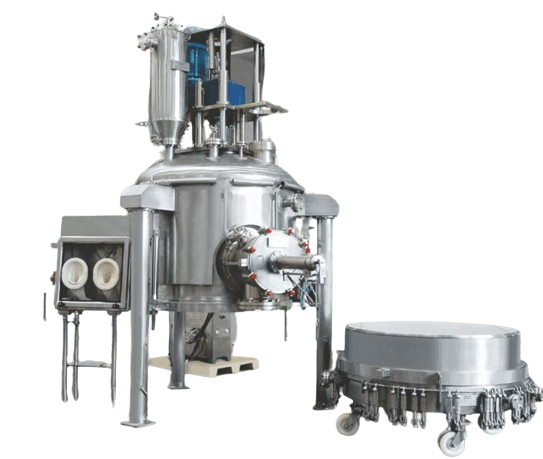
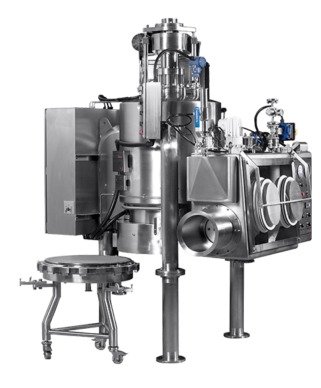
Advantages of Agitated Nutsche Filter Dryers
Efficiency
ANFDs combine multiple process steps into one unit, reducing the need for additional equipment and handling. This integration improves process efficiency and reduces operational costs.
Versatility
ANFDs can handle a wide range of materials, from fine powders to coarse crystals. Their adaptable design makes them suitable for various applications across different industries.
Quality Control
The closed system of ANFDs minimizes contamination risks, ensuring high product purity. The controlled environment allows precise adjustments to process parameters, improving product quality.
Safety
ANFDs operate in a closed system, reducing exposure to hazardous substances. This design enhances worker safety and complies with stringent industrial safety regulations.
Pricing of Agitated Nutsche Filter Dryers
The cost of agitated nutsche filter dryers varies based on several factors:
- Size and Capacity: Larger units with higher capacities typically cost more.
- Material of Construction: Stainless steel, Hastelloy, and glass-lined options have different price points.
- Customization: Custom features and advanced control systems can increase the overall cost.
Key Considerations for Selecting an Agitated Nutsche Filter Dryer
When selecting an agitated nutsche filter dryer, consider the following factors:
- Process Requirements: Evaluate the specific needs of your process, including the type of materials, pressure, temperature, and purity requirements.
- Material Compatibility: Ensure the construction materials of the ANFD are compatible with the substances being processed to avoid corrosion and contamination.
- Capacity and Size: Choose a size that matches your production volume while allowing for scalability.
- Automation and Control: Look for advanced control systems that offer real-time monitoring and adjustments to optimize performance.
- Maintenance and Support: Consider the availability of maintenance services and spare parts to ensure the longevity and reliability of the equipment.
Conclusion
Agitated nutsche filter dryers (ANFDs) are essential equipment in various industries, offering efficient solid-liquid separation, washing, and drying processes. Their versatility, efficiency, and safety make them a preferred choice for pharmaceutical, chemical, and food applications. By understanding the working principles, key components, applications, and maintenance of ANFDs, industries can optimize their processes and improve product quality. As technology advances, ANFDs will continue to evolve, offering even greater efficiency and sustainability.
For more in-depth articles and resources on agitated nutsche filter dryers and related technologies, visit EngiTech.in. Stay updated on the latest advancements and applications in the field!