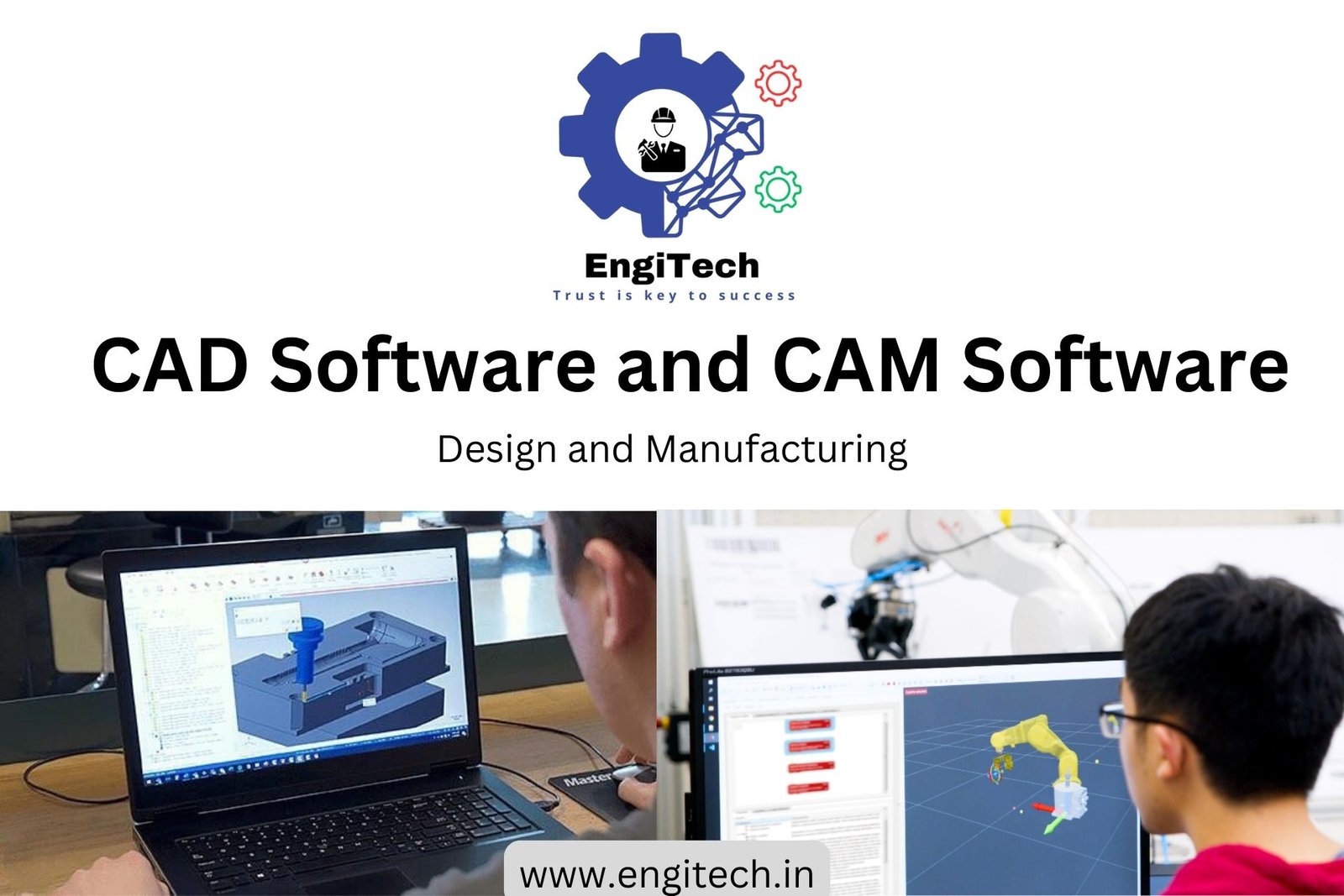
Have you ever wondered how modern products go from an idea to a manufactured reality so quickly? Behind every smartphone, car part, and even the chair you’re sitting on lies powerful technology that revolutionized design and manufacturing. CAD and CAM software are the unsung heroes of our modern world, enabling engineers and designers to create complex products with unprecedented speed and precision.
Whether you’re a seasoned professional looking to upgrade your toolset or a newcomer exploring these technologies for the first time, this comprehensive guide will walk you through everything you need to know about CAD and CAM software in 2025. We’ll explore how these technologies work together, the best options available today, and how to choose the right solution for your specific needs.
Table of Contents
What Are CAD and CAM Software?
Understanding CAD Software
Computer-Aided Design (CAD) software allows users to create precise 2D drawings or 3D models of physical objects. These digital blueprints serve as the foundation for product development across virtually every industry.
Modern CAD software has evolved significantly from its humble beginnings in the 1960s. Today’s programs offer intuitive interfaces, powerful modeling capabilities, and advanced simulation tools that can predict how designs will perform in real-world conditions.
Key capabilities of CAD software include:
- Creating detailed 2D technical drawings
- Developing complex 3D models
- Visualizing designs with photorealistic rendering
- Analyzing structural integrity through simulation
- Collaborating with team members in real-time
- Generating documentation for manufacturing
Understanding CAM Software
Computer-Aided Manufacturing (CAM) software takes those digital designs and transforms them into manufacturing instructions. This technology bridges the gap between design and production by generating tool paths and code that automated machinery can understand.
CAM software communicates with manufacturing equipment like CNC machines, 3D printers, and robotic systems to produce physical parts with exceptional accuracy and consistency.
Primary functions of CAM software include:
- Converting CAD models into machine-readable instructions
- Optimizing tool paths for efficient manufacturing
- Simulating machining processes to identify potential issues
- Supporting various manufacturing methods (milling, turning, 3D printing)
- Managing tool libraries and material specifications
- Reducing waste and production time
How CAD and CAM Work Together
The integration of CAD and CAM creates what industry professionals call the “digital thread” – a seamless flow of information from concept to finished product. This integration has become increasingly important as manufacturing has evolved toward greater automation and precision.
In an integrated CAD/CAM workflow:
- Designers create a digital model in CAD software
- The design is validated through simulations and analysis
- CAM software converts the design into machine instructions
- Manufacturing equipment produces the physical component
- Quality control compares the finished product against the original CAD model
This unified approach reduces errors, speeds up production, and enables more complex designs than would otherwise be possible.
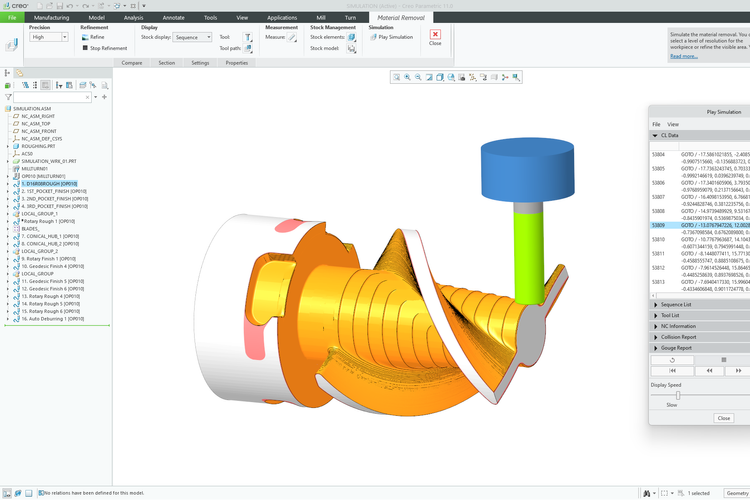
Evolution of CAD and CAM Technologies
Historical Development
The journey of CAD/CAM systems spans over six decades of technological innovation:
1960s: The first CAD systems emerge, primarily using 2D drafting techniques on mainframe computers. These early systems, like Sketchpad developed at MIT, laid the groundwork for modern digital design.
1970s: The introduction of 3D wireframe modeling marks a significant advancement. Companies like Auto-trol and Computervision release commercial CAD systems for industrial use.
1980s: Solid modeling capabilities appear, with software like CATIA and SolidWorks changing how engineers approach design. Personal computers start making CAD technology more accessible.
1990s-2000s: CAD/CAM integration accelerates, with software becoming more user-friendly and powerful. Cloud capabilities begin to emerge.
2010s: Mobile applications, cloud computing, and real-time collaboration transform CAD/CAM workflows. Generative design and AI-assisted features start appearing in premium software.
2020s: Full cloud integration, AI-driven design suggestion, advanced simulation capabilities, and seamless integration with additive manufacturing technologies define the current state of CAD/CAM systems.
Current Technological Landscape
Today’s CAD/CAM landscape is characterized by several key trends:
Cloud-Based Solutions: Software like Onshape, Fusion 360, and SolidWorks Cloud offer anywhere-access capabilities, facilitating remote work and collaboration.
AI Integration: Artificial intelligence now assists with design optimization, suggesting improvements and automating repetitive tasks.
Virtual and Augmented Reality: Designers can interact with their 3D models in immersive environments, making design reviews more intuitive.
Generative Design: AI algorithms can now produce optimized design alternatives based on specified constraints and goals.
Seamless Interoperability: Modern systems feature improved compatibility between different software packages and manufacturing equipment.
Types of CAD Software
2D CAD Software
Despite the rise of 3D modeling, 2D CAD software remains essential for many applications:
AutoCAD: The industry standard for 2D drafting, offering precision tools for creating technical drawings.
DraftSight: A cost-effective alternative to AutoCAD with a familiar interface and compatible file formats.
LibreCAD: An open-source option ideal for basic 2D drafting needs.
2D CAD is particularly valuable for:
- Architectural floor plans
- Electrical schematics
- Plumbing layouts
- Simple mechanical drawings
3D CAD Software
3D modeling software comes in several varieties, each with unique strengths:
Parametric Modeling Software:
- SolidWorks: Popular in manufacturing industries for its robust feature-based approach
- Autodesk Inventor: Excellent for mechanical design with strong simulation capabilities
- PTC Creo: Powerful for complex assembly modeling
Direct Modeling Software:
- SpaceClaim: Allows for quick modifications without concern for design history
- MoI 3D: Focused on fast, intuitive modeling for creative applications
Surface Modeling Software:
- Rhino: Excels at creating complex curved surfaces and organic shapes
- CATIA: Industry-leading surface modeling capabilities used in automotive and aerospace
Solid Modeling Software:
- Fusion 360: Combines solid modeling with integrated CAM and simulation
- Solid Edge: Offers a hybrid approach with both parametric and direct modeling
Specialized CAD Software
Many industries have CAD software tailored to their specific needs:
Architectural Design:
- Revit: Building Information Modeling (BIM) focused software
- ArchiCAD: Architectural-specific tools with strong visualization capabilities
Civil Engineering:
- Civil 3D: Specialized for infrastructure and land development projects
- Bentley MicroStation: Comprehensive solution for large infrastructure projects
Electronic Design:
- Altium Designer: PCB design and electronic system design
- Eagle: Entry-level PCB design software with professional capabilities
Industrial Design:
- Alias: Surface modeling software popular in automotive design
- SolidThinking: Combines industrial design with engineering functionality
Types of CAM Software
Entry-Level CAM Systems
These solutions provide basic manufacturing capabilities at an affordable price point:
Carbide Create: User-friendly software for simple CNC projects EstlCAM: Affordable option for small workshops and hobbyists FreeMill: Open-source solution for basic milling operations
These systems typically offer:
- Simple 2.5D machining operations
- Limited toolpath options
- Basic simulation capabilities
- Lower learning curve for beginners
Mid-Range CAM Systems
Mid-tier solutions balance capability and cost-effectiveness:
Fusion 360: Integrated CAD/CAM with cloud capabilities
MasterCAM Mill Express: Streamlined version of the industry-standard software
FeatureCAM: Automated toolpath generation with recognition of design features
These systems provide:
- 3-axis machining support
- More advanced toolpath strategies
- Better simulation and verification tools
- Support for a wider range of manufacturing equipment
High-End CAM Systems
Professional-grade solutions for complex manufacturing challenges:
Siemens NX CAM: Comprehensive manufacturing solution for advanced applications
CATIA Manufacturing: Part of the CATIA ecosystem with powerful integration capabilities
PowerMILL: Specialized in complex surface machining with advanced toolpath algorithms
These premium systems deliver:
- 5-axis simultaneous machining support
- Advanced toolpath optimization
- Comprehensive digital twin capabilities
- Enterprise-level data management
- Support for specialized manufacturing techniques
Industry-Specific CAM Solutions
Many CAM systems are tailored to specific manufacturing processes:
Sheet Metal Fabrication:
- Trumpf TruTops: Optimized for laser cutting and punching operations
- Bystronic BySoft: Specialized for sheet metal processing equipment
Woodworking:
- Alphacam: Features specific to wood machining requirements
- Cabinet Vision: Purpose-built for cabinet and furniture manufacturing
Dental/Medical:
- hyperDENT: Optimized for dental restoration manufacturing
- Materialise Magics: Focused on medical implant production
Electronics Manufacturing:
- Valor: Specialized for PCB manufacturing processes
- CircuitCAM: Focused on PCB prototyping
Key Features to Look for in CAD Software
Modeling Capabilities
The heart of any CAD system is its ability to create accurate digital representations:
Sketch Tools: Look for intuitive 2D sketch features with constraints and dimensions Feature Creation: Evaluate tools for extrusions, revolves, fillets, chamfers, and patterns Assembly Modeling: Check for efficient ways to bring parts together in assemblies Surface Modeling: Consider software with advanced surface creation and editing tools Large Assembly Handling: Assess performance with complex multi-part assemblies
Simulation and Analysis
Modern CAD tools should help validate designs before manufacturing:
Stress Analysis: Look for built-in FEA (Finite Element Analysis) capabilities Thermal Simulation: Evaluate tools for predicting heat transfer and thermal expansion Motion Studies: Check for kinematic and dynamic analysis of moving assemblies CFD (Computational Fluid Dynamics): Consider if fluid flow analysis is important for your applications Tolerance Analysis: Assess tools for understanding manufacturing variation impact
Collaboration Features
Team-based design requires robust collaboration capabilities:
Version Control: Look for history tracking and the ability to revert to previous versions Cloud Integration: Consider how the software enables remote team collaboration Markup and Review Tools: Evaluate features for design feedback and approval processes Data Management: Check for PDM (Product Data Management) integration Access Control: Assess security features for intellectual property protection
File Compatibility
Interoperability with other systems is crucial in modern workflows:
Native File Formats: Understand which CAD formats the software can create and edit Neutral Formats: Check support for STEP, IGES, and other universal formats Direct Translation: Evaluate how well the software handles files from competing systems Point Cloud Import: Consider if scanning data can be easily imported and referenced PMI and Annotations: Look for support of Product Manufacturing Information standards
Key Features to Look for in CAM Software
Tool Path Generation
The core functionality of CAM software lies in creating efficient machining instructions:
2D Operations: Evaluate features for facing, pocketing, contouring, and drilling 3D Operations: Look for complex surface machining capabilities Multi-Axis Support: Check the level of support for 4-axis and 5-axis machining Feature Recognition: Consider tools that automatically identify machining features Template Support: Assess the ability to save and reuse machining operations
Simulation and Verification
Virtual testing helps prevent costly mistakes:
Toolpath Visualization: Look for clear graphical representation of cutting paths Collision Detection: Evaluate tools that identify potential tool/fixture/machine collisions Material Removal Simulation: Check how accurately the software shows material being removed Machine Kinematics: Consider if the software simulates actual machine movements Cycle Time Estimation: Assess accuracy of manufacturing time predictions
Post-Processing Capabilities
The translation to machine-specific code is critical:
Post-Processor Library: Check for built-in support for your specific machines Custom Post Creation: Evaluate tools for creating or modifying post-processors G-Code Editing: Look for capabilities to review and modify generated code Multiple Machine Support: Consider if the software works with your entire equipment lineup Output Verification: Assess tools for validating the final machine code
Material and Tool Management
Comprehensive libraries improve efficiency:
Tool Libraries: Look for extensive databases of cutting tools Material Databases: Check for built-in materials with appropriate cutting parameters Tool Path Optimization: Evaluate features that minimize tool wear and maximize efficiency Tool Life Management: Consider tracking capabilities for tool usage and replacement Adaptive Machining: Assess support for dynamic feed and speed adjustments
Choosing the Right CAD/CAM Software
Assessing Your Needs
Before selecting software, carefully evaluate your requirements:
Industry Specifics: Consider the unique demands of your industry (aerospace, automotive, consumer products) Project Complexity: Assess the complexity of designs you typically create Team Size and Structure: Evaluate how many users need access and their locations Integration Requirements: Consider existing systems that need to connect with your CAD/CAM solution Budget Constraints: Determine both initial investment capacity and ongoing subscription costs
Popular Integrated CAD/CAM Solutions
Several platforms offer both design and manufacturing capabilities:
Autodesk Fusion 360:
- Strengths: Cloud-based collaboration, subscription pricing, integrated simulation
- Best for: Small to medium businesses, startups, educational use
SolidWorks:
- Strengths: Extensive user community, robust design tools, established industry standard
- Best for: Engineering-focused companies with complex design requirements
Siemens NX:
- Strengths: High-end capabilities, excellent large assembly handling, advanced manufacturing
- Best for: Enterprise users in automotive, aerospace, and heavy machinery
CATIA:
- Strengths: Surface modeling excellence, end-to-end product development
- Best for: Automotive, aerospace, and industrial design applications
OnShape:
- Strengths: Fully cloud-based, subscription model, excellent collaboration
- Best for: Remote teams, startups, companies needing accessibility from anywhere
Cost Considerations
CAD/CAM software pricing varies dramatically based on capabilities:
Licensing Models:
- Perpetual licenses: Higher upfront cost but potentially lower long-term expense
- Subscription: Lower initial investment with ongoing payments
- Floating licenses: Shared access among team members on an as-needed basis
Hidden Costs:
- Training: Budget for getting your team up to speed
- Hardware: Consider computing requirements for running software efficiently
- Maintenance: Annual support and update fees
- Implementation: Time and resources needed for deployment
Cost-Saving Strategies:
- Educational licenses for qualifying institutions
- Startup programs offered by major vendors
- Open-source alternatives for non-critical applications
- Cloud-based solutions to reduce hardware investment
Training and Support Resources
Consider the learning curve and available help:
Learning Resources:
- Official training programs from software vendors
- Third-party courses on platforms like Udemy and LinkedIn Learning
- YouTube tutorials and community forums
- Certification programs for professional development
Support Options:
- Technical support response times and availability
- User communities for peer assistance
- Consulting services for implementation
- Documentation quality and accessibility
Implementation and Best Practices
Setting Up an Effective CAD/CAM Workflow
Creating an efficient design-to-manufacturing process requires thoughtful planning:
Standard Operating Procedures:
- Establish naming conventions for files and features
- Create templates for common design tasks
- Develop a structured review and approval process
- Implement version control protocols
Hardware Considerations:
- Ensure workstations meet recommended specifications
- Consider dedicated rendering machines for visualization tasks
- Plan network infrastructure for data sharing
- Evaluate virtual desktop infrastructure for remote access
Integration Planning:
- Map data flows between systems
- Identify potential bottlenecks
- Test interoperability of different software packages
- Document integration points and required formats
Common Challenges and Solutions
Be prepared to overcome typical implementation hurdles:
Data Migration:
- Challenge: Transferring legacy designs to new systems
- Solution: Plan phased migration with careful validation of converted files
User Adoption:
- Challenge: Resistance to new workflows
- Solution: Involve end-users in selection process and provide adequate training
Performance Issues:
- Challenge: Slow processing of complex models
- Solution: Implement model simplification techniques and optimize hardware
Version Compatibility:
- Challenge: Maintaining file compatibility across versions
- Solution: Standardize on specific file formats or implement PDM systems
Future-Proofing Your CAD/CAM Investment
Prepare for evolving technology landscapes:
Scalability:
- Choose solutions that can grow with your business
- Consider cloud options for flexible capacity
Technology Trends:
- Stay informed about emerging capabilities like generative design
- Evaluate how AI and machine learning might impact your workflows
Skills Development:
- Invest in continuous training for your team
- Build internal expertise in customization and automation
Vendor Stability:
- Assess the financial health and market position of software providers
- Consider the ecosystem of third-party applications and add-ons
Industry Applications and Case Studies
Manufacturing and Product Design
CAD/CAM technology has transformed traditional manufacturing:
Automotive Industry:
- Reduced design cycle times by up to 50%
- Enabled complex surface modeling for aerodynamic optimization
- Facilitated weight reduction through advanced simulation and material optimization
Consumer Electronics:
- Accelerated product development for increasingly short market windows
- Enabled miniaturization through precise tolerance control
- Streamlined integration of mechanical and electronic components
Industrial Equipment:
- Improved machine performance through simulation-driven design
- Reduced material usage with optimized part design
- Enhanced serviceability through digital prototyping
Architecture and Construction
Building design and construction have been revolutionized:
BIM (Building Information Modeling):
- Enabled comprehensive digital representation of physical and functional building characteristics
- Facilitated better coordination between architectural, structural, and MEP systems
- Reduced construction errors and change orders by up to 40%
Prefabrication:
- Increased precision in factory-built components
- Improved on-site assembly efficiency
- Reduced construction waste by up to 60%
Infrastructure Projects:
- Enhanced large-scale coordination for transportation projects
- Improved earthwork calculations and site modeling
- Enabled better visualization for stakeholder communication
Medical and Dental Applications
Healthcare has embraced digital design and manufacturing:
Medical Device Development:
- Accelerated innovation in implantable devices
- Enabled patient-specific customization
- Reduced development costs through virtual testing
Dental Restoration:
- Transformed workflow from impression to final restoration
- Improved fit accuracy with digital scanning and design
- Reduced patient chair time through same-day manufacturing
Surgical Planning:
- Enhanced procedure preparation with patient-specific models
- Improved communication between surgical team members
- Reduced operating time for complex procedures
Emerging Trends in CAD/CAM Software
AI and Generative Design
Artificial intelligence is rapidly changing design approaches:
Design Suggestion:
- AI systems that propose alternative solutions based on requirements
- Machine learning algorithms that learn from previous designs
- Automated optimization for specific performance criteria
Generative Design:
- Creates multiple design alternatives based on constraints and goals
- Optimizes for weight, strength, material usage, and manufacturing method
- Often produces organic shapes difficult to conceive through traditional methods
Predictive Analytics:
- Anticipates potential design issues before they become problems
- Suggests improvements based on performance data
- Reduces iteration cycles through smarter starting points
Cloud Computing and Collaboration
The cloud continues to transform how teams work:
Real-Time Collaboration:
- Multiple users editing the same model simultaneously
- Cross-discipline teams working in integrated environments
- Global talent leveraged regardless of location
Computing Power on Demand:
- Complex simulations run on cloud servers rather than local workstations
- Rendering farms available without capital investment
- Scalable resources for varying project demands
Mobile Access:
- Design review and approval from tablets and smartphones
- Field data collection integrated with design systems
- Construction site verification against digital models
Integration with 3D Printing and Additive Manufacturing
The synergy between CAD/CAM and additive technologies continues to grow:
Design for Additive Manufacturing (DfAM):
- Tools specifically for creating designs that leverage 3D printing capabilities
- Topology optimization for parts that couldn’t be manufactured conventionally
- Lattice structure generation for lightweight, strong components
Direct Digital Manufacturing:
- Seamless workflow from design to printed part
- Automated preparation of print files with optimized support structures
- Quality control through comparison of scanned parts to original models
Hybrid Manufacturing:
- Combined additive and subtractive processes
- Restoration and repair of existing components
- Embedding of electronics and sensors during fabrication
Conclusion
CAD and CAM software have evolved from simple digital drafting tools to comprehensive design and manufacturing ecosystems that are transforming industries around the world. The integration of these technologies creates a digital thread that connects initial concept through final production, enabling unprecedented speed, precision, and innovation.
As we’ve explored in this guide, the right CAD/CAM solution depends on your specific needs, industry, and resources. By understanding the available options and carefully assessing your requirements, you can select software that will not only meet your current needs but also position your organization for future growth and technological advancement.
Whether you’re designing architectural marvels, life-saving medical devices, consumer electronics, or industrial machinery, CAD and CAM technologies provide the foundation for bringing your ideas to life. As artificial intelligence, cloud computing, and additive manufacturing continue to evolve, these tools will become even more powerful, accessible, and essential to competitive success.
The future of design and manufacturing is digital, connected, and intelligent. By embracing modern CAD/CAM solutions, you’re not just investing in software—you’re investing in your organization’s ability to innovate, collaborate, and create the products of tomorrow.
Stay Connected with EngiTech
EngiTech is your trusted source for in-depth knowledge on industrial mechanical engineering machines and technologies. Stay ahead with the latest innovations, expert insights, and practical guides designed to help you make informed decisions for your business and engineering needs. Join our growing community of professionals and industry leaders to stay updated and competitive in the ever-evolving world of industrial technology.
Further Reading and Resources
Recommended Books
- “Mastering CAD/CAM” by Ibrahim Zeid
- “The Design of Things to Come” by Craig M. Vogel, Jonathan Cagan, and Peter Boatwright
- “Additive Manufacturing Technologies” by Ian Gibson, David Rosen, and Brent Stucker
- “Digital Design and Manufacturing Technology” by Andreas Weber
Industry Publications and Websites
- Digital Engineering (digitalengineering247.com)
- Manufacturing Engineering Magazine (sme.org/me-magazine)
- Engineering.com CAD/CAM section
- Develop3D (develop3d.com)
Research Papers and Academic Resources
- “The Evolution of CAD/CAM Technologies: From Historical Perspectives to Future Trends” – Journal of Manufacturing Systems
- “Industry 4.0 and the Impact of Digital Twin Technology on Manufacturing” – International Journal of Production Research
- “Generative Design for Additive Manufacturing: Recent Advances and Opportunities” – Journal of Manufacturing Science and Engineering
Software Vendor Resources
- Autodesk University (autodesk.com/autodesk-university)
- SolidWorks World Proceedings (3ds.com/products/solidworks)
- Siemens Digital Industries Software Knowledge Base
- PTC Learning Exchange (ptc.com/en/support/learning-exchange)