
Have you ever wondered why some snack brands always deliver perfectly sealed and fresh-tasting chips, while others seem stale or poorly packaged? The answer often lies in one critical piece of equipment: a chips packing machine. This cutting-edge device plays a pivotal role in preserving product quality, extending shelf life, and ensuring customer satisfaction. In today’s fast-paced world, where consumers demand on-the-go convenience, getting snack packaging right has never been more important.
In this comprehensive guide, you’ll learn everything about chips packing machines—from how they work and why they matter to the food industry, to selecting the right model, mastering the maintenance process, and uncovering the latest technological innovations. By the end of this post, you’ll be well-equipped to streamline your packaging operations, minimize waste, and deliver consistently high-quality snacks to your market.
Whether you’re a small-scale snack producer or a high-volume manufacturer, understanding the ins and outs of a chips packing machine can transform your business.
Table of Contents
Why Chips Packaging Matters
Extending Shelf Life for Better Customer Satisfaction
At its core, snack packaging is about much more than aesthetics. When chips are exposed to air or moisture, they rapidly lose their crunch, flavor, and overall appeal. A high-quality chips packing machine uses proper sealing mechanisms and materials—often in combination with modified atmosphere packaging (MAP)—to keep the product fresh and crispy. This directly impacts customer satisfaction. After all, no one enjoys munching on stale chips. A properly packed snack will maintain taste, texture, and aroma for longer, reducing returns and boosting brand loyalty.
Protecting Against Contamination and Spoilage
Food safety is a non-negotiable priority in the snack industry. Chips can be particularly vulnerable to contamination, especially when oils and flavorings are involved. Proper packaging serves as a barrier against bacteria, mold, and other contaminants. The best chips packing machines are designed to minimize contact points and facilitate hygienic filling and sealing processes. According to the U.S. Food & Drug Administration, maintaining strict packaging standards is crucial for preventing foodborne illnesses, which could otherwise lead to costly recalls or even legal ramifications.

Enhancing Brand Image and Marketability
Packaging isn’t just about protecting the product; it’s also about showcasing your brand. Eye-catching bags or pouches with a secure seal and attractive labeling can make your snack stand out on crowded supermarket shelves. Advanced printing techniques allow you to display vivid graphics, barcodes, and nutritional information, all while maintaining the necessary barrier properties. Investing in a chips packing machine that can handle diverse packaging formats—like pillow pouches, gusseted bags, or stand-up pouches—means you have more creative freedom to market your snacks effectively.
Understanding the Key Components of a Chips Packing Machine
Overview of Core Parts
A chips packing machine typically includes several core components, each playing a distinct role in the packaging process:
- Product Hopper – Holds the chips before they are dispensed into packaging material.
- Weighing System – Ensures consistent portion sizes, often involving multi-head weighers for high accuracy.
- Film Unwinding Mechanism – Feeds packaging film (usually plastic or composite laminates) into the machine.
- Forming Tube – Shapes the film into a bag or pouch ready for filling.
- Filling and Sealing Station – Drops measured portions of chips into the formed pouch, then seals the top.
- Cutting Mechanism – Separates individual pouches from the continuous roll of packaging film.
Advanced Weighing Systems
Accuracy is paramount in snack packaging. Overfilling bags can lead to revenue losses, while underfilling can disappoint consumers or violate labeling regulations. Modern chips packing machines often feature multi-head weighers that use advanced load cells to ensure precise portioning. This not only helps maintain consistency in each pack but also boosts efficiency by reducing giveaway.
Sealing Mechanisms
Sealing technology can vary from machine to machine. Common sealing types include:
- Heat Sealing: Melts a thin layer of film to create a secure bond, often used in plastic-based packaging.
- Impulse Sealing: Uses short, precise bursts of heat to seal thermoplastic films.
- Ultrasonic Sealing: Employs high-frequency vibrations to bond packaging material, ideal for sensitive films.
The right sealing technology for your chips packing machine depends on factors like film thickness, packaging material, and production speed.
How a Chips Packing Machine Works: Step-by-Step Process
Simplifying the Packaging Workflow
While chips packing machines can be highly sophisticated, the overall workflow follows a logical sequence:
- Film Feeding
A roll of packaging film is mounted onto the machine. The film is then fed through tension rollers to ensure a smooth, wrinkle-free feed. - Bag Formation
The film wraps around a forming tube, shaping it into a cylindrical pouch. - Weighing and Dispensing
Chips stored in the hopper are weighed by a multi-head system. Once the target weight is reached, the weighed portion is discharged into the pouch. - Heat or Ultrasonic Sealing
The horizontal seal is created at the bottom of the pouch. After the chips are dispensed, the top seal is made, sealing the bag completely. - Cutting and Discharge
The machine separates the newly formed bag from the continuous film and discharges it onto a conveyor belt or collection bin.
Throughout these steps, sensors monitor factors like weight, film tension, and seal quality. If any irregularities occur, the machine can alert operators or even halt production to prevent large-scale waste.
Choosing the Right Chips Packing Machine
Identifying Production Needs
Before you invest in a machine, ask yourself the following:
- What is my daily or monthly production volume?
- What types of chips or snacks am I packaging (potato chips, tortilla chips, extruded snacks, etc.)?
- Do I require multi-pack capabilities for variety packs?
- What bag formats and sizes do I need?
A small-scale artisanal brand may only need a semi-automatic machine capable of packaging a few hundred bags per hour. Large snack manufacturers might require a fully automated system that can process several thousand bags per hour. Aligning your machine’s capacity with your actual production needs ensures you don’t overspend or risk bottlenecks.
Evaluating Machine Features and Specifications
When comparing various chips packing machine models, pay attention to:
- Speed and Accuracy: Measured in bags per minute (BPM) and how consistently each bag is weighed and sealed.
- Versatility: The ability to switch between different bag sizes and film types without extensive downtime.
- Ease of Use: Intuitive control panels, clear visual feedback, and straightforward maintenance procedures.
- Build Quality and Materials: Stainless steel frames are common in food processing settings due to their durability and easy-to-clean surfaces.
Secondary Keywords to Consider
When searching for or describing a chips packing machine, you’ll often encounter secondary terms like “snack packaging machine,” “potato chips packing line,” “vertical form fill seal (VFFS) machine,” or “flexible packaging solutions.” Familiarizing yourself with these terms can help you navigate industry jargon and find the best fit for your specific needs.
The Importance of Packaging Materials
Types of Films and Laminates
Not all packaging materials are created equal. For chips, the material must protect against:
- Oxygen Ingress: Oxygen accelerates rancidity and spoilage.
- Moisture: Even slight humidity can make chips soggy.
- Light: Exposure to UV light can degrade oils and flavors in the chips.
Common packaging materials for chips include metallized films (often PET-based) and multi-layer laminates. These materials provide excellent barrier properties while maintaining a lightweight profile.
Balancing Cost and Performance
Choosing the right packaging material is often a balancing act between performance and cost. Premium films may offer superior oxygen barrier properties but can be more expensive. On the other hand, lower-grade films might be cheaper but could compromise on freshness, leading to potential losses from returned or unsold goods. Working closely with packaging suppliers to test different film structures can help you find the sweet spot.
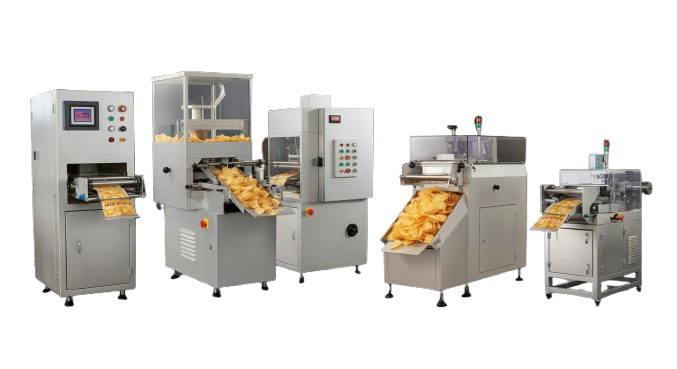
Maintenance and Operational Best Practices
Daily and Weekly Maintenance Routines
Once you’ve invested in a chips packing machine, keeping it in top condition is crucial:
- Cleaning
- Remove leftover chip fragments or oil residues to prevent contamination.
- Wipe down surfaces with food-grade sanitizers.
- Lubrication
- Apply lubricants to moving parts, gears, and bearings as recommended by the manufacturer.
- Inspection
- Check seals, gaskets, belts, and sensors for signs of wear or damage.
- Ensure the weighers are calibrated properly.
Troubleshooting Common Issues
- Inconsistent Seals
Could be due to improper temperature settings or worn-out sealing jaws. - Film Jams
Often caused by wrinkles or poor tension control. Regularly check the tension rollers and alignment. - Weight Variations
Ensure load cells are clean, and any accumulated debris is removed. Recalibrate regularly to maintain accuracy.
By following a structured maintenance plan, you not only prolong the life of your machine but also avoid costly downtime and production delays.
Automation and Emerging Technologies
The Rise of Smart Packaging Systems
Packaging technology is evolving at a rapid pace. Many chips packing machines now come with IoT (Internet of Things) capabilities. Sensors embedded in the machine collect real-time data—such as temperature, humidity, and production speed—and relay this information to a central dashboard. Operators can monitor the status of multiple lines remotely, troubleshoot potential issues, and even schedule predictive maintenance tasks before problems escalate.
AI-Driven Quality Control
Some advanced setups are integrating AI (Artificial Intelligence) and machine vision to enhance quality control. High-speed cameras capture images of each bag as it’s being sealed, while AI algorithms analyze seal quality, bag shape, and labeling accuracy in real-time. If an anomaly is detected—like a misprint or an uneven seal—the system can automatically divert the defective bag or pause production, reducing waste and ensuring consistent product quality.
Cost Considerations and Return on Investment (ROI)
Upfront vs. Long-Term Costs
It’s natural to focus on the purchase price of a chips packing machine, but your total cost of ownership extends far beyond that initial figure. Factors like energy consumption, maintenance costs, film waste, and spare part availability all impact your bottom line. A machine that is cheap upfront but prone to frequent breakdowns can become far more expensive in the long run compared to a higher-end model that boasts superior reliability and efficiency.
Calculating ROI
To determine whether an investment is worthwhile, consider the following:
- Production Efficiency
How much does the machine reduce labor costs or downtime? - Material Savings
If the machine can handle thinner films or reduce overfill, you’ll likely save on packaging materials and product giveaway. - Market Growth
Higher capacity and consistent quality can help you expand into new markets faster, leading to increased revenue.
By carefully analyzing these factors, you’ll be able to justify the investment in a chips packing machine and accurately forecast your payback period.
Frequently Asked Questions
Your Top Chips Packing Machine Queries Answered
1. What types of snacks can a chips packing machine handle?
A well-designed chips packing machine can pack a variety of snacks, including traditional potato chips, corn chips, popcorn, extruded snacks, and even nuts or dried fruit. The key is ensuring the machine’s configuration matches the product’s size, shape, and weight requirements.
2. How do I choose the right bag size and format?
Consider both your target market and the serving size you wish to offer. Single-serve snack packs often range from 20g to 40g, while family-size bags can exceed 200g. Your machine should accommodate your most common bag sizes as well as any seasonal or promotional packaging needs.
3. How often should I recalibrate the weighing system?
Calibration frequency depends on production volume, but a good rule of thumb is at least once a week. If you notice sudden weight deviations or have changed your packaging material, run a quick calibration to maintain accuracy.
4. Are chips packing machines compatible with sustainable packaging materials?
Yes. Many modern machines can work with biodegradable or compostable films. However, the sealing temperature and speed settings may need adjustment to accommodate these eco-friendly materials. It’s wise to consult both your equipment manufacturer and packaging supplier to identify the right parameters.
5. How much floor space do I need for a typical chips packing machine?
Machine footprints vary widely based on capacity and additional features like multiple weighers. Generally, you should allocate enough space for the machine itself, incoming film rolls, product hoppers, and areas for maintenance access. Factor in at least a few meters of clearance around the unit.
Expert Tips for Boosting Efficiency
Optimize Machine Settings
Every packaging line is unique, so don’t rely on default machine settings forever. Conduct regular tests and tweak parameters like seal temperature, dwell time, and fill speed to find the sweet spot between efficiency and quality.
Train Your Team
Even the most advanced chips packing machine is only as effective as the people operating it. Ensure your staff is well-trained in routine maintenance, troubleshooting, and standard operating procedures. Periodic refresher sessions can prevent knowledge gaps, reduce operator error, and keep your production running smoothly.
Leverage Data Analytics
If your machine has IoT or data-logging capabilities, use that data to make informed decisions. Track metrics like machine downtime, average seal strength, or product waste. Analyzing these trends can reveal opportunities for incremental improvements and cost savings, ultimately boosting your bottom line.
Real-World Case Study: Thriving with Automated Packaging
A Small Snack Brand’s Success Story
Consider the example of a small artisanal chip brand that made the leap from manually filling plastic bags to investing in a fully automated chips packing machine. Before automation, the company battled inaccurate fills, high labor costs, and inconsistent sealing. Within a few months of installing their new system:
- Labor costs dropped by 30% because fewer people were needed to operate the line.
- Bag consistency improved dramatically, reducing returns and complaints.
- Production capacity doubled, enabling the company to meet the demands of a growing customer base.
This transformation highlights the profound impact a well-chosen and well-managed chips packing machine can have on a business’s reputation, profitability, and overall growth potential.
Conclusion
When it comes down to it, a chips packing machine is far more than an industrial piece of equipment. It’s a linchpin that can make or break the success of your snack brand. From extending shelf life and preserving the crunchiness of your chips to enhancing brand image and operational efficiency, the right packaging solution is your gateway to higher customer satisfaction and sustainable growth.
As you evaluate different models and features, remember the importance of choosing materials wisely, maintaining the machine with care, and staying ahead of the curve with emerging technologies. By investing time and effort into understanding your production requirements, training your staff, and optimizing machine settings, you’ll set yourself up for consistent, quality-driven performance. Ready to take your snack packaging to the next level? Now is the perfect time to explore how a state-of-the-art chips packing machine can revolutionize the way you deliver your tasty creations to the world.
Ready to get started? Share this post with your colleagues, explore our additional resources, and leave a comment with your own experiences and questions. Let’s work together to make every chip a freshly sealed delight!
Stay Connected with EngiTech
EngiTech is your trusted source for in-depth knowledge on industrial mechanical engineering machines and technologies. Stay ahead with the latest innovations, expert insights, and practical guides designed to help you make informed decisions for your business and engineering needs. Join our growing community of professionals and industry leaders to stay updated and competitive in the ever-evolving world of industrial technology.