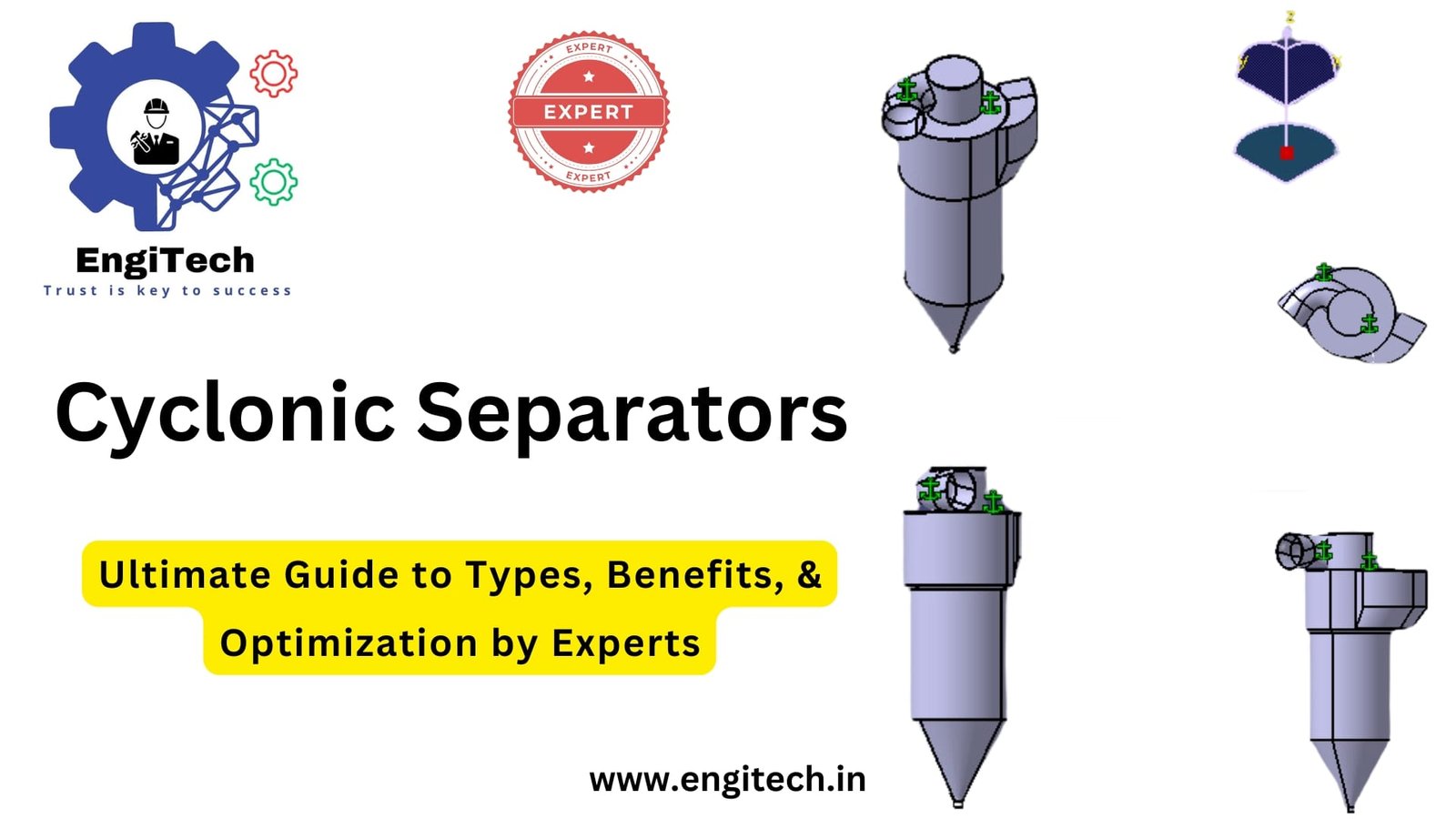
Cyclonic separators play a crucial role in various industrial applications by efficiently separating particulates from gases or liquids. From enhancing air quality to ensuring smoother manufacturing processes, cyclonic separators offer a cost-effective and maintenance-free solution. In this comprehensive guide, we’ll delve deep into what cyclonic separators are, their working principles, types, benefits, and tips for optimizing their performance.
This guide is crafted to educate knowledge seekers and provide in-depth information on the applications, selection criteria, and best practices for cyclonic separators.
Table of Contents
What are Cyclonic Separators?
A cyclonic separator is a device that uses centrifugal force to remove particles from air, gas, or liquid without the use of filters. These separators are highly efficient and often used in industrial environments to remove dust, debris, and other solid particulates from air or fluids. The cyclonic separators, is a critical tool for ensuring operational efficiency in industries like oil and gas, power plants, food processing, and more.
In essence, cyclonic separators work by forcing the fluid (whether air or liquid) into a circular motion. This motion pushes heavier particles to the outside, where they are collected, allowing clean air or liquid to pass through the center.
How Do Cyclonic Separators Work?
The working principle of a cyclonic separator is simple but highly effective. Here’s a step-by-step breakdown of the process:
- Inlet of Gas or Liquid: The contaminated fluid (air or liquid) enters the cyclonic separator tangentially, creating a spiral or vortex inside the separator.
- Centrifugal Force: As the fluid swirls, centrifugal force pushes the denser particulate matter outward toward the walls of the cyclone chamber.
- Separation: The clean air or liquid is drawn up through the vortex and exits the separator, while the heavier particles settle at the bottom for collection or disposal.
This mechanism allows cyclonic separators to operate without needing filters or regular maintenance, making them ideal for industries that require high efficiency with low operational costs.
Pro Tip: For optimal performance, ensure the cyclonic separator is designed to handle the specific particle size and density of the contaminants in your application.
Types of Cyclonic Separators
There are several types of cyclonic separators, each designed for specific applications and operational requirements. Let’s look at the most common types:
a) Reverse Flow Cyclonic Separator
In reverse flow cyclones, gas or liquid enters tangentially and spins in a downward spiral. The clean gas or liquid is then drawn upward through the center, while particulates fall to the bottom.
b) Axial Flow Cyclonic Separator
In this design, the fluid flows parallel to the axis of the cyclone, with the clean fluid exiting from one end and the particulates being collected at the other. This type of separator is typically used in situations where space constraints require a more compact design.
c) High-Efficiency Cyclonic Separator
These separators are specifically designed to maximize the separation of fine particles. By creating stronger vortexes, high-efficiency separators can remove smaller particulates that other types may struggle to capture.
d) Multicyclones
For processes that require even more precision, multicyclones combine multiple smaller cyclones in a single unit, each handling a portion of the airflow. This increases efficiency and is ideal for applications requiring the removal of very fine particles.
Advantages of Using Cyclonic Separators
Cyclonic separators offer numerous benefits, making them a preferred choice in various industrial applications. Some of the key advantages include:
- Cost-Effective Operation: Cyclonic separators do not require moving parts or filters, reducing maintenance and operating costs.
- Durable and Long-Lasting: Their robust design ensures a long lifespan with minimal wear and tear.
- High Efficiency: Cyclonic separators can remove up to 99% of particulates in certain applications, ensuring cleaner air or liquid.
- Environmentally Friendly: These separators contribute to reducing emissions and improving air quality in industrial settings.
- Versatility: Cyclonic separators can handle a wide range of particulate sizes and are suitable for various gases and liquids.
Applications of Cyclonic Separators
The versatility of cyclonic separators makes them useful across various industries. Here are some common applications:
a) Oil and Gas Industry
In the oil and gas industry, cyclonic separators are used to remove solids and liquids from natural gas and crude oil, improving processing efficiency and reducing equipment wear.
b) Power Plants
Power plants often use cyclonic separators to remove dust and other particulates from exhaust gases, helping to meet environmental regulations and improve air quality.
c) Food Processing
Cyclonic separators help in ensuring the purity of products by removing dust and debris from the air during the production process.
d) Mining and Quarrying
In mining operations, cyclonic separators are used to separate dust from the air in extraction and crushing processes.
e) Chemical Processing
Cyclonic separators ensure that particulates are removed from gases and liquids in chemical processing, preventing contamination and ensuring product purity.
Factors to Consider When Choosing Cyclonic Separators
When selecting a cyclonic separator, it is crucial to consider specific factors to ensure it meets your operational requirements. Here’s what to keep in mind:
a) Particle Size and Density
The efficiency of a cyclonic separator depends largely on the size and density of the particles being separated. High-density particles are easier to separate than low-density ones, and finer particles require more precise designs.
b) Flow Rate
The rate at which the fluid (air or liquid) flows through the separator affects its performance. Selecting the right separator for your flow rate ensures optimal separation efficiency.
c) Pressure Drop
Cyclonic separators cause a pressure drop as the fluid flows through them. It is important to choose a design that minimizes pressure drop to avoid affecting the overall system performance.
d) Material of Construction
Since cyclonic separators are used in harsh industrial environments, their construction materials should be selected based on the type of fluid and particulates being handled. Stainless steel, carbon steel, and specialized alloys are commonly used materials.
How to Optimize Cyclonic Separator Performance
To get the most out of your cyclonic separator, here are some tips for optimizing its performance:
- Correct Sizing: Ensure that the separator is correctly sized for the flow rate and particulate load in your application. Oversized or undersized separators can result in suboptimal performance.
- Regular Inspections: Periodically inspect the separator for wear and tear, especially in high-dust environments.
- Maintain Inlet Velocity: The inlet velocity directly impacts the separation efficiency. Ensure the separator is designed to operate at the recommended velocity for your specific application.
- Control Pressure Drop: Excessive pressure drops can reduce separation efficiency. Monitor and control pressure drops to ensure smooth operation.
Cyclonic Separator Maintenance Tips
While cyclonic separators are generally low-maintenance, proper upkeep can significantly extend their lifespan and maintain efficiency. Here are some maintenance tips:
- Monitor Particle Buildup: Check for any accumulation of particles in the cyclone chamber, as this can reduce separation efficiency.
- Inspect for Erosion: High-velocity particles can erode the separator walls. Regular inspections will help you catch any early signs of erosion.
- Check Seals and Connections: Ensure all seals and connections are intact to prevent leakage and maintain efficiency.
- Clean Discharge Systems: Keep the discharge system clean and clear of any obstructions to ensure proper collection of separated particles.
Cyclonic Separators vs. Other Separation Methods
While cyclonic separators are a popular choice, other separation methods may be more suitable depending on the application. Here’s a quick comparison:
- Cyclonic Separators vs. Bag Filters: Bag filters are more effective for removing extremely fine particles but require regular maintenance and filter changes. Cyclonic separators, on the other hand, are low-maintenance and better for larger particles.
- Cyclonic Separators vs. Electrostatic Precipitators: Electrostatic precipitators use an electric charge to remove particulates from the air, making them ideal for applications with fine particles. However, they are more expensive to operate and maintain compared to cyclonic separators.
- Cyclonic Separators vs. Scrubbers: Scrubbers use liquid to remove particulates from gases, which makes them suitable for applications involving both solids and liquids. However, they are typically more complex and expensive to maintain than cyclonic separators.
FAQs related to cyclonic separators:
1. What is a cyclonic separator?
A cyclonic separator is a device that uses centrifugal force to separate particles from a gas or liquid stream without the need for filters. It is commonly used in industrial applications to remove dust, debris, and solid particulates from fluids.
2. How does a cyclonic separator work?
Cyclonic separators work by forcing the fluid into a circular motion, creating a vortex. Heavier particles are pushed outward to the walls, while clean air or liquid is drawn up through the center, allowing the separated particulates to collect at the bottom.
3. What industries use cyclonic separators?
Cyclonic separators are widely used in industries like oil and gas, power generation, food processing, chemical processing, mining, and HVAC systems for air purification and filtration.
4. What is the efficiency of a cyclonic separator?
The efficiency of a cyclonic separator can range from 70% to over 99%, depending on the design, operating conditions, and particle size being separated.
5. What types of materials can cyclonic separators handle?
Cyclonic separators can handle a wide range of materials, including dust, sand, metal shavings, liquid droplets, and solid particulates, depending on the design and industrial application.
6. What is the difference between a single-stage and a multistage cyclonic separator?
A single-stage cyclonic separator has one separation chamber, while a multistage separator uses multiple smaller cyclones to improve efficiency and capture finer particles.
7. What are the main advantages of using cyclonic separators?
Cyclonic separators are cost-effective, low-maintenance, durable, and efficient at removing particulates. They do not require filters, making them suitable for applications with high dust loads.
8. How do I choose the right cyclonic separator for my application?
When selecting a cyclonic separator, consider factors like particle size and density, flow rate, pressure drop, and the material of construction. It’s important to choose one that meets your specific operational needs.
9. What maintenance is required for cyclonic separators?
Cyclonic separators require minimal maintenance. Regular inspection of the collection chamber and discharge outlets to ensure there is no blockage is recommended. Periodic cleaning may be needed depending on the application.
10. Can cyclonic separators be used for both air and liquid applications?
Yes, cyclonic separators can be used to separate solid particles from both air (as in dust collection systems) and liquids (such as in oil-water separation).
11. How much pressure drop occurs in a cyclonic separator?
The pressure drop across a cyclonic separator varies based on its design, flow rate, and particle load, but it generally ranges from 2 to 10 inches of water column. Lower pressure drop designs are more energy-efficient.
12. What particle sizes can cyclonic separators remove?
Cyclonic separators are most efficient at removing medium to large particles, typically ranging from 10 microns to 100 microns, though high-efficiency designs can capture smaller particulates.
13. What are the limitations of cyclonic separators?
Cyclonic separators may struggle to remove very fine particles (below 5 microns) without additional filtration stages. They may also have high pressure drops in some designs, which can affect energy efficiency.
14. What is the typical lifespan of a cyclonic separator?
With proper maintenance, cyclonic separators can last for many years. Their lifespan is influenced by factors like operating conditions, material of construction, and the types of particulates being processed.
15. How do cyclonic separators compare to other dust collection methods?
Compared to baghouse filters or electrostatic precipitators, cyclonic separators offer a maintenance-free solution without the need for filters or electricity. However, they may not be as efficient in removing ultra-fine particles.
Conclusion
Cyclonic separators are indispensable tools in many industries, offering a low-maintenance, cost-effective solution for separating particulates from gases and liquids. Whether you’re in the oil and gas, chemical, or food processing industry, selecting the right cyclonic separator and optimizing its performance is crucial for efficient operation.
By following the best practices outlined in this guide, you can ensure your cyclonic separator operates at peak performance, reducing downtime and enhancing overall efficiency.
EngiTech dedicated to providing cutting-edge solutions and expert insights for the industrial mechanical engineering sector. Our platform offers in-depth resources on advanced machinery, including blowers, dryers, and cyclonic separators, designed to help engineers, manufacturers, and industry professionals enhance efficiency and performance. Whether you’re looking for detailed technical guides, optimization tips, or the latest innovations in industrial technology, EngiTech is your go-to source for reliable, up-to-date information. Join us to stay ahead in the rapidly evolving world of engineering and unlock the full potential of your industrial processes.