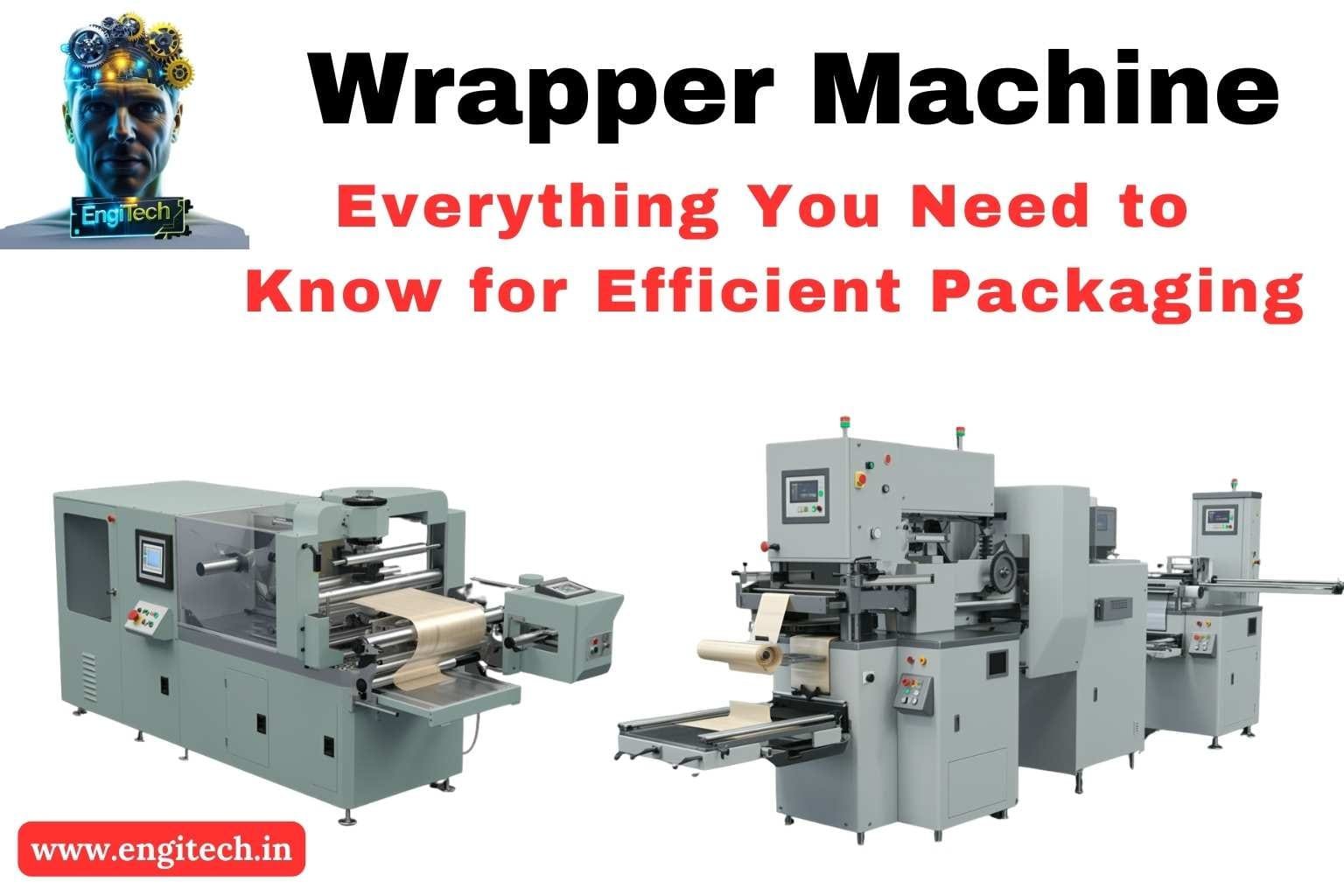
In today’s fast-paced manufacturing and retail environments, businesses are constantly searching for ways to optimize their packaging lines. One of the most effective investments a company can make is in a wrapper machine. From boosting output and reducing labor costs to maintaining the integrity of products during transit, a wrapper machine can transform your operations in a very tangible way.
In this comprehensive guide, you’ll discover everything you need to know about wrapper machines. We’ll explore the technology behind them, the various types available, best practices for operation, key maintenance tips, as well as a deep dive into how to choose the right solution for your specific industry needs. Whether you’re a small-scale startup or a global manufacturing powerhouse, you’ll walk away with actionable insights that will immediately translate into improved packaging efficiency and product safety.
Table of Contents
1. What Is a Wrapper Machine?
A wrapper machine is a specialized piece of packaging technology designed to wrap products or packages efficiently, securely, and consistently. In a typical scenario, it applies a flexible film, paper, or other wrapping material around a product to protect it from external elements, improve its shelf life, and enhance its presentation. This can be seen in a wide variety of settings, from food packaging lines and consumer goods manufacturing to pharmaceutical applications and industrial settings.
The wrapper machine usually integrates into a larger packaging system, working alongside conveyors, labelers, fillers, and sealers to form a cohesive operation. Depending on the model and type, it can handle diverse product shapes and sizes—from small candy bars to large pallets containing multiple boxes.
Why Is It Important?
- Efficiency: Automated wrapping solutions significantly reduce manual labor, speeding up the packaging process.
- Consistency: Machines ensure uniform wrapping tension, material usage, and sealing for each product.
- Safety and Hygiene: A well-wrapped product is less prone to contamination or tampering.
- Cost Savings: By optimizing film usage and reducing labor costs, businesses can see a noticeable return on their investment.
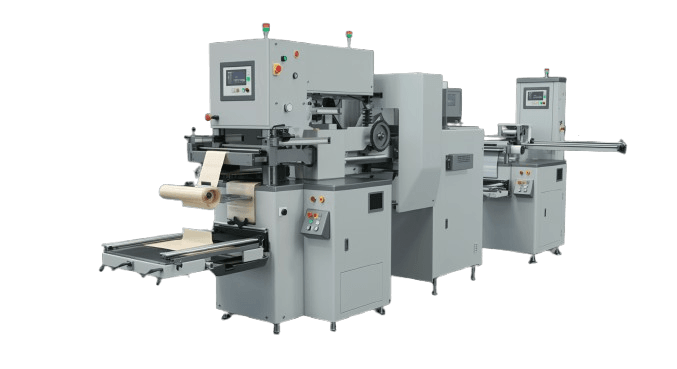
2. The Evolution of Wrapper Machines
Packaging technology has evolved dramatically over the last century. What began as manual processes reliant on human labor gradually transitioned into semi-automated systems. By the late 20th century, fully automated machines became mainstream, incorporating robotics, sensors, and digital controls.
Key Milestones
- 1920s–1930s: Manual wrapping methods become standardized in certain industries, especially confectionery.
- 1950s–1960s: Emergence of semi-automated machines with mechanical levers and basic motors.
- 1980s: Introduction of programmable logic controllers (PLCs) for more precise control over wrapping speed and tension.
- 21st Century: Adoption of advanced sensors, data analytics, and robotic arms. Modern systems can adapt to varying product shapes and sizes in real-time.
According to a 2019 study by the Packaging Machinery Manufacturers Institute (PMMI), automated packaging solutions, including wrapper machines, have shown an annual growth rate of roughly 6.5%. This trend is fueled by consumer demand for speed, consistency, and eco-friendly solutions in the packaging sector.
3. Key Components and Mechanisms
While wrapper machines vary by design and purpose, most share a core set of components:
- Film Dispenser: Holds and dispenses the wrapping material (e.g., plastic film, paper).
- Conveyor System: Transports products into the wrapping zone.
- Cutting & Sealing Mechanism: Cuts the wrapping material to size and seals it around the product.
- Control Panel & Sensors: Regulates temperature, film tension, and wrapping speed, ensuring precision and consistency.
- Motor & Drive Systems: Powers the conveyor and the film roll, enabling high-speed wrapping.
- Safety Guards & Emergency Stops: Protect operators and products from hazards.
4. Types of Wrapper Machines
The wrapper machine category encompasses a wide range of models, each specialized for different packaging needs. Here are some of the most common types:
4.1 Flow Wrappers
- How It Works: Products are fed into a horizontal or vertical conveyor that continuously wraps the product in a tube of film, sealing the edges and ends.
- Best For: Individually wrapped items like candy bars, cookies, and snack packs.
- Advantages: High-speed operation and consistent sealing.
4.2 Overwrappers
- How It Works: Material is folded over the product manually or automatically, often with a heat seal to secure flaps.
- Best For: Cosmetic boxes, DVD cases, and certain food trays.
- Advantages: Crisp, professional-looking wraps that showcase branding.
4.3 Stretch Wrappers
- How It Works: A stretchable film is pulled around a product (often a pallet), and the film’s elasticity holds the load together.
- Best For: Pallets and bulk loads in warehouse or distribution settings.
- Advantages: Stabilizes large shipments, reducing damage during transit.
4.4 Shrink Wrappers
- How It Works: Film is applied around the product, then exposed to heat so it shrinks tightly around the product’s contours.
- Best For: Bottled beverages, multipacks, and irregularly shaped items.
- Advantages: Tamper-evident, protective layer that also offers excellent shelf appeal.
4.5 Band Wrappers
- How It Works: A band of paper or film is wrapped around the center or a specific segment of the product.
- Best For: Booklets, brochures, or smaller items requiring minimal coverage.
- Advantages: Reduces material usage and allows partial product visibility.
4.6 Robotic and Customized Solutions
- How It Works: Incorporates robotic arms and sensor-based controls for versatile, high-speed applications.
- Best For: Complex assembly lines with diverse product types.
- Advantages: Flexible, scalable, and easily integrated into fully automated packaging lines.
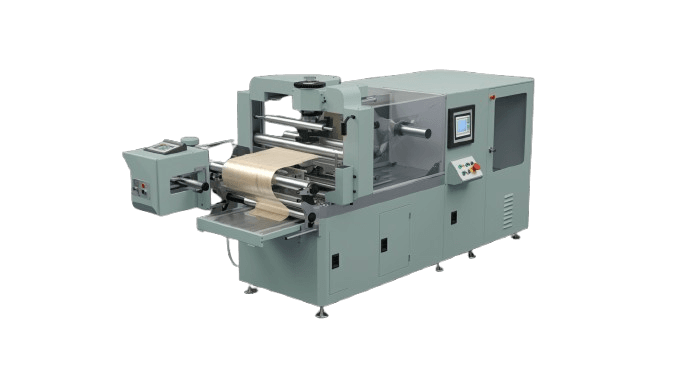
5. Primary Industries and Applications
Almost every sector that requires packaging can benefit from a wrapper machine:
- Food & Beverage: Snacks, baked goods, frozen items, and beverages often rely on flow or shrink wrappers to maintain freshness and prevent contamination.
- Consumer Goods: Cosmetics, electronics, and home care products utilize overwrappers for tamper-evident and visually appealing packaging.
- Pharmaceuticals: Shrink wrapping and band wrapping provide secure, sealed products that meet regulatory standards.
- E-commerce & Retail: Stretch wrappers are invaluable in stabilizing bulk shipments and protecting products through the supply chain.
- Industrial & Automotive: Parts and components benefit from stretch or shrink wrapping to maintain integrity during storage and transport.
6. How to Choose the Right Wrapper Machine
Selecting the ideal wrapper machine for your operation is a strategic decision that can significantly impact your bottom line. Consider these important factors:
6.1 Production Volume and Speed
- Throughput: Estimate how many units per hour or day need to be wrapped.
- Scalability: Choose a machine that can handle your projected growth to avoid future bottlenecks.
6.2 Product Dimensions and Complexity
- Shape & Size: Some wrappers handle irregular shapes better than others.
- Fragility: Delicate products might need gentler wrapping methods and specialized materials.
6.3 Material Compatibility
- Film Types: Polyethylene (PE), Polypropylene (PP), or biodegradable films.
- Thickness: Ensure the machine is optimized for the thickness and type of film you intend to use.
6.4 Space & Facility Layout
- Footprint: Measure available floor space, considering operator access and safety clearance.
- Integration: If you already have conveyor lines or robotic systems, confirm compatibility.
6.5 Budget and ROI
- Initial Costs: Budget not just for the machine, but also for installation, training, and maintenance.
- Long-Term Savings: Factor in reduced labor, faster throughput, and film efficiency for a clear ROI picture.
6.6 Regulatory and Quality Requirements
- Safety Standards: Machines should comply with relevant local and international safety regulations.
- Industry-Specific Rules: Food, pharmaceutical, and other sensitive industries may have additional requirements like GMP (Good Manufacturing Practices) and FDA guidelines.
7. Best Practices for Efficient Operation
A wrapper machine is only as good as the processes and people behind it. Following certain best practices can maximize uptime, efficiency, and product quality.
- Train Operators Thoroughly
Ensure every team member understands how to start, stop, and adjust the machine. Proper training reduces errors and extends machine life. - Regular Calibration
Periodically check film tension, conveyor speeds, and heat seal temperatures. Even minor deviations can lead to inconsistent wraps or wasted material. - Use High-Quality Materials
Cheap or incompatible films may save money in the short term but can lead to frequent breakdowns or subpar packaging. - Implement Preventive Maintenance Schedules
Don’t wait for a breakdown. Consistently replace or repair parts like sealing jaws, belts, and motors before they fail. - Record and Analyze Data
Many modern wrapper machines come equipped with data logging. Track performance metrics like downtime, wrapping speed, and material usage to identify bottlenecks and inefficiencies. - Keep It Clean
In industries like food and pharmaceuticals, cleanliness is paramount. Regular cleaning prevents contamination and extends the machine’s lifespan.
8. Maintenance, Troubleshooting, and Safety
Proper maintenance of your wrapper machine goes hand-in-hand with safe and efficient operations. Here’s what you need to know:
8.1 Maintenance Essentials
- Daily Checks: Inspect belts, seals, and film rollers before each shift.
- Weekly Routine: Lubricate moving parts and tighten loose bolts or connections.
- Monthly & Quarterly: Conduct detailed inspections, replace worn components, and update any software or firmware.
8.2 Common Troubleshooting Tips
- Film Tearing or Jamming
- Possible Cause: Incorrect tension or misaligned rollers.
- Solution: Adjust tension settings and inspect rollers for wear.
- Uneven Heat Seals
- Possible Cause: Temperature fluctuations or dirty sealing jaws.
- Solution: Clean sealing surfaces and verify temperature settings.
- Machine Stoppages
- Possible Cause: Sensor malfunction or software glitch.
- Solution: Reset the system, check for sensor misalignment, and run diagnostics.
- Wrinkles or Air Pockets
- Possible Cause: Film feed rate mismatched with conveyor speed.
- Solution: Adjust machine settings to synchronize speeds.
8.3 Safety Measures
- Emergency Stops: Ensure all operators know the location and proper usage of emergency stop buttons.
- Guarding & Fences: Prevent accidental contact with moving parts.
- Lockout/Tagout Procedures: Vital when cleaning or repairing machinery.
- Personal Protective Equipment (PPE): Depending on the environment, operators may require gloves, hairnets, safety goggles, or ear protection.
9. Emerging Trends in Wrapper Machine Technology
The packaging industry continues to innovate rapidly. Several cutting-edge trends are shaping the next generation of wrapper machines:
9.1 Sustainability and Eco-Friendly Films
- Biodegradable and Compostable Films: Gaining popularity as consumers demand reduced plastic waste.
- Material Reduction: Advanced machines that optimize film usage without compromising package integrity.
9.2 Smart Sensors and IoT Integration
- Real-Time Monitoring: Sensors track temperature, tension, and machine health, sending alerts for immediate intervention.
- Predictive Maintenance: AI-driven data analysis identifies wear patterns so parts can be replaced before failure.
9.3 Robotics and Collaborative Systems
- Cobots (Collaborative Robots): Work alongside humans on the packaging line, reducing manual load and increasing accuracy.
- High-Speed Vision Systems: Cameras detect product orientation, defects, or label alignment with minimal downtime.
9.4 Flexibility and Customization
- Modular Systems: Easily scalable or reconfigurable for different product lines.
- On-the-Fly Adjustments: Operators can change machine settings digitally, adapting quickly to new packaging requirements.
9.5 Sustainability in Machine Manufacturing
- Energy Efficiency: Motors and controls are designed for lower energy consumption.
- Carbon Footprint Reduction: Manufacturers aim to use more recyclable parts and processes in machine production.
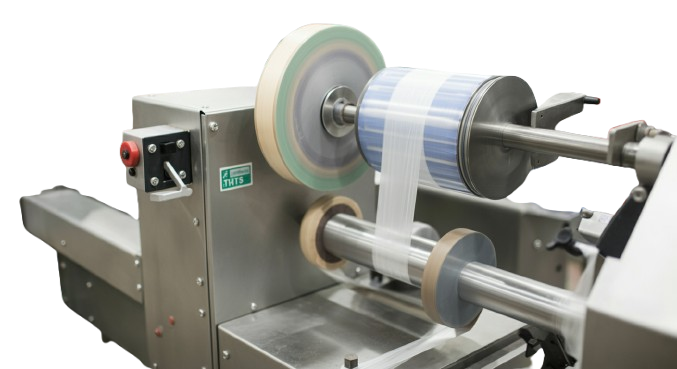
10. Cost Analysis and ROI of Investing in a Wrapper Machine
While a wrapper machine can be a significant initial outlay, the long-term financial benefits are often substantial. Here’s how to evaluate the return on investment:
- Initial Capital Expenditure (CAPEX)
This includes the machine’s purchase cost, installation, and any necessary facility upgrades. - Operational Expenditure (OPEX)
- Maintenance & Repair: Routine servicing plus occasional part replacements.
- Labor: Automated systems reduce the need for manual labor.
- Materials: Some machines optimize film usage, lowering material costs.
- Throughput Increase
The ability to wrap more products in less time translates into higher productivity and revenue. - Reduced Waste and Returns
Properly wrapped products are less likely to be damaged, lowering returns and boosting customer satisfaction. - Long-Term Scalability
Investing in a modular or upgradable system can save money as production demands rise.
By calculating these factors, you can estimate a payback period—commonly ranging from 6 months to 3 years depending on production scale. Larger firms often see quicker returns due to higher volume, while smaller businesses can still benefit by expanding their operational capacity without extensive additional labor.
11. Frequently Asked Questions (FAQs)
Q1: How do I decide whether a flow wrapper or a stretch wrapper is better for my business?
Answer: It depends on the product type and packaging goals. Flow wrappers are ideal for individual or small packaged goods like snacks. Stretch wrappers are geared toward stabilizing large loads like pallets. Assess your daily throughput, product fragility, and shipping needs before making a decision.
Q2: Can I use eco-friendly film on my existing wrapper machine?
Answer: Most modern machines support a range of films, including biodegradable or compostable types. However, always verify compatibility with the machine manufacturer to prevent issues like tearing or poor seals.
Q3: What routine maintenance steps can I perform to keep my wrapper machine running smoothly?
Answer: Daily checks, cleaning of sealing jaws, and tension adjustments are essential. A weekly or monthly preventive maintenance schedule that includes lubrication, parts inspection, and software updates also helps avoid unplanned downtime.
Q4: How critical is operator training for wrapper machine efficiency?
Answer: Training is extremely important. Well-trained operators not only maintain higher throughput but also catch potential problems early, reducing downtime and waste.
Q5: Is a wrapper machine suitable for small startups or only large-scale manufacturers?
Answer: Wrapper machines come in various sizes and price ranges. Even small businesses can benefit from semi-automated or compact models, especially if they plan to scale production in the future.
Conclusion
A wrapper machine is much more than just a piece of equipment—it can revolutionize your packaging process, ensuring quality, consistency, and cost-efficiency across multiple product lines. By understanding the different types of wrapper machines, their core components, and best operational practices, you are better prepared to make an informed decision that aligns with your production goals.
Whether you’re in food and beverage, consumer goods, or industrial manufacturing, there’s a wrapper machine solution out there tailored to your needs. Remember to weigh factors like product dimensions, desired throughput, budget, and compliance requirements as you explore various models.
Stay Connected with EngiTech
EngiTech is your trusted source for in-depth knowledge on industrial mechanical engineering machines and technologies. Stay ahead with the latest innovations, expert insights, and practical guides designed to help you make informed decisions for your business and engineering needs. Join our growing community of professionals and industry leaders to stay updated and competitive in the ever-evolving world of industrial technology.