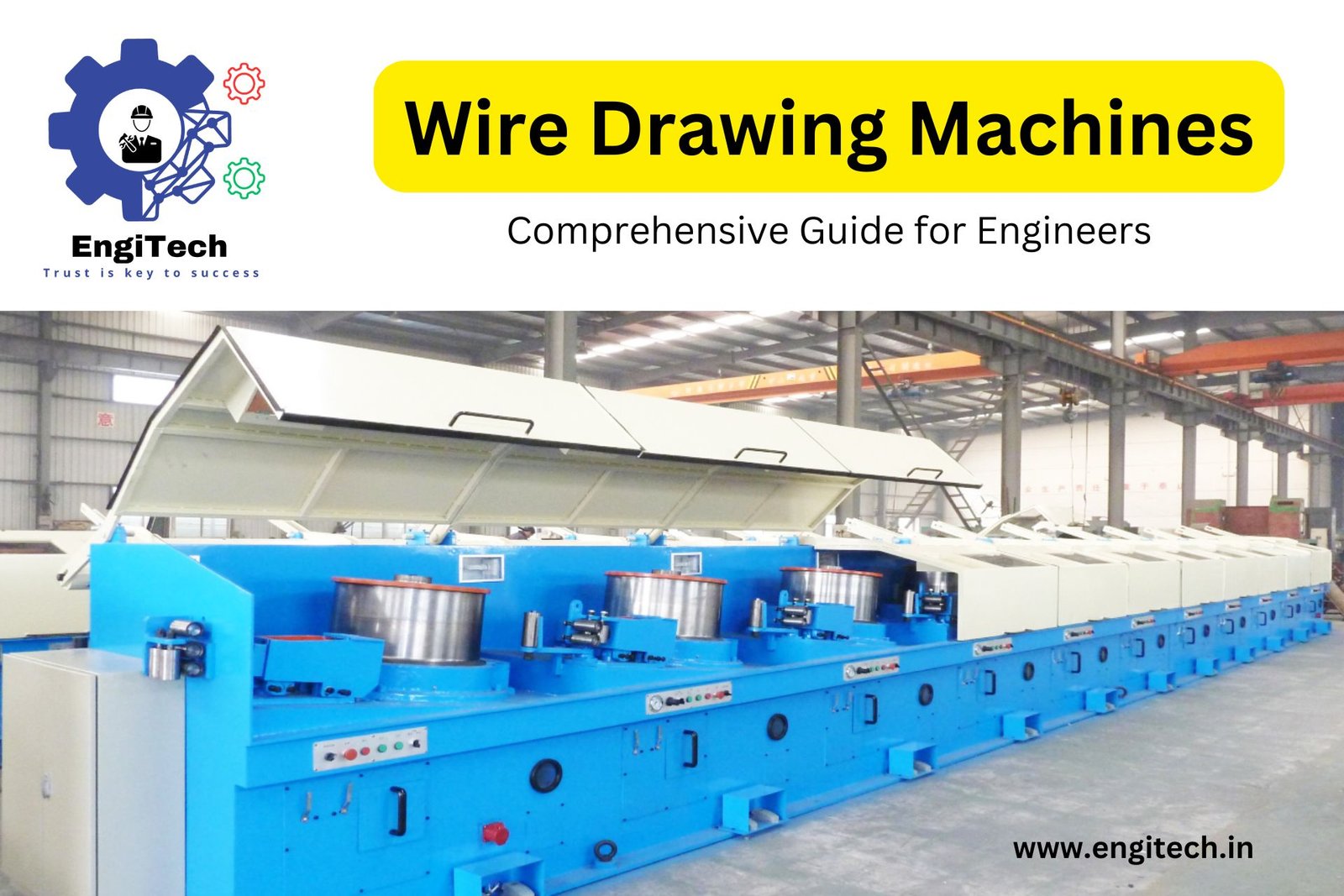
In the vast domain of manufacturing and metallurgy, wire drawing machines play a crucial role. These machines transform raw wire rods into precise and uniform wire products, essential in various industries, including construction, automotive, electronics, and telecommunications.
This detailed guide will provide valuable insights into wire drawing machines, their working principles, types, applications, and maintenance, tailored to the needs of knowledge seekers, students, and working professionals.
Table of Contents
What Are Wire Drawing Machines?
Wire drawing machines are mechanical devices used to reduce the diameter of a wire by pulling it through a series of drawing dies. The process involves stretching the wire, which results in a decrease in its cross-sectional area while maintaining its length. This method allows the production of wires with specific diameters and mechanical properties, essential for various industrial applications.
Key Components of Wire Drawing Machines
- Drawing Die: The heart of the wire drawing process, the drawing die is typically made of tungsten carbide or diamond, depending on the material and precision required. It reduces the wire’s diameter and shapes it into the desired cross-section.
- Capstan: The capstan pulls the wire through the drawing die. It is usually driven by an electric motor and controls the speed and tension of the wire during the drawing process.
- Wire Guide: This component ensures the wire is correctly aligned with the drawing die, preventing damage or uneven drawing.
- Lubrication System: Lubrication is critical in wire drawing to reduce friction and heat generation. The lubrication system ensures a continuous supply of lubricant to the wire and die during the drawing process.
- Coiling Mechanism: After the wire has been drawn, it is coiled for easy handling and transportation. The coiling mechanism ensures the wire is neatly wound onto spools or drums.
Working Principle of Wire Drawing Machines
The wire drawing process begins with a wire rod, typically made of steel, copper, aluminum, or other metals, depending on the final application. The wire rod is first cleaned to remove any surface impurities that could damage the drawing die. Once cleaned, the rod is fed into the wire drawing machine.
As the wire passes through the drawing die, it undergoes plastic deformation, which reduces its diameter while increasing its length. The capstan pulls the wire through the die at a controlled speed, ensuring uniformity in diameter and mechanical properties. The drawn wire is then passed through successive dies, each reducing the diameter further until the desired size is achieved.
Importance of Lubrication in Wire Drawing
Lubrication is essential in wire drawing to minimize friction between the wire and the drawing die. Without adequate lubrication, the wire could overheat, leading to surface defects, breakage, or damage to the drawing die. Lubricants also help dissipate heat, ensuring the wire remains at a stable temperature during the drawing process.
Types of Wire Drawing Machines
Wire drawing machines come in various types, each designed for specific applications and materials. Understanding the different types will help you select the right machine for your needs.
- Single-Block Wire Drawing MachinesThese machines are designed for drawing wires in a single pass. They are typically used for producing wires with large diameters or when high precision is required. Single-block machines are often used in industries where the final product must meet strict tolerances.
- Multi-Block Wire Drawing MachinesMulti-block wire drawing machines consist of several drawing dies arranged in series. The wire passes through each die sequentially, gradually reducing its diameter. These machines are ideal for producing wires with smaller diameters and are commonly used in the production of electrical wires, cables, and fine metal wires.
- Wet Wire Drawing MachinesIn wet wire drawing machines, the entire drawing process occurs under a continuous flow of lubricant. This type of machine is particularly effective in reducing friction and heat, making it suitable for drawing wires made from materials that are prone to surface damage, such as copper or aluminum.
- Dry Wire Drawing MachinesDry wire drawing machines use a powdered lubricant that is applied to the wire before it enters the drawing die. These machines are typically used for drawing steel wires and other hard materials. The dry lubricant forms a thin film on the wire surface, reducing friction and wear on the die.
- Fine Wire Drawing MachinesFine wire drawing machines are specialized for producing extremely thin wires, often used in electronics and telecommunications. These machines require precise control and high-quality dies to achieve the desired wire thickness and properties.
- Coarse Wire Drawing MachinesCoarse wire drawing machines are designed for drawing thicker wires, often used in construction, automotive, and heavy industry applications. These machines are built to handle the higher forces required to draw large-diameter wires.
Applications of Wire Drawing Machines
Wire drawing machines are indispensable in various industries, each requiring wires of specific diameters and properties. Here are some key applications:
- Electrical and Electronics IndustryWires drawn from copper and aluminum are widely used in the electrical and electronics industry. These wires are essential for manufacturing cables, connectors, and other components that require high conductivity and precise dimensions.
- Automotive IndustryThe automotive industry relies on wire drawing machines to produce wires used in vehicle wiring harnesses, brake cables, and control cables. These wires must meet stringent quality standards to ensure safety and reliability.
- Construction IndustrySteel wires drawn using wire drawing machines are used in construction for reinforcing concrete structures, manufacturing mesh, and creating suspension cables for bridges. The strength and durability of these wires are critical for structural integrity.
- Telecommunications IndustryThe telecommunications industry uses fine wires drawn from copper, aluminum, and fiber-optic materials for transmitting data and signals. These wires must have excellent conductivity and minimal signal loss.
- Jewelry MakingWire drawing machines are also used in the jewelry industry to produce fine wires for creating intricate designs. These wires are typically made from precious metals such as gold, silver, and platinum.
Advantages of Using Wire Drawing Machines
Wire drawing machines offer several advantages, making them an essential tool in manufacturing and industrial processes:
- Precision and UniformityWire drawing machines provide precise control over wire dimensions, ensuring uniform diameter and mechanical properties. This precision is crucial in industries where tolerance is critical.
- Cost-Effective ProductionWire drawing is a cost-effective method for producing wires with specific dimensions and properties. The process minimizes material waste and allows for high-volume production, reducing overall manufacturing costs.
- VersatilityWire drawing machines can handle a wide range of materials, including steel, copper, aluminum, and precious metals. This versatility makes them suitable for various applications across different industries.
- Improved Mechanical PropertiesThe wire drawing process enhances the mechanical properties of the wire, such as tensile strength and hardness. These improved properties make the wire more suitable for demanding applications.
- Surface FinishWire drawing machines produce wires with a smooth surface finish, reducing the need for additional processing. This is particularly important in industries where surface quality is critical, such as electronics and telecommunications.
Maintenance of Wire Drawing Machines
Regular maintenance of wire drawing machines is essential to ensure their optimal performance and longevity. Proper maintenance also reduces the risk of unexpected breakdowns, which can lead to costly downtime.
Routine Maintenance Tasks
- Inspection of Drawing DiesThe drawing dies are subjected to significant wear and tear during the wire drawing process. Regular inspection and replacement of worn dies are essential to maintain the quality of the drawn wire.
- Lubrication System MaintenanceThe lubrication system must be regularly checked to ensure it is functioning correctly. Proper lubrication is crucial for reducing friction and heat, preventing damage to the wire and drawing die.
- Capstan and Motor InspectionThe capstan and motor drive the wire through the drawing die. Regular inspection of these components ensures they are functioning correctly and maintaining the required tension on the wire.
- Cleaning and Debris RemovalAccumulated debris and metal particles can affect the performance of the wire drawing machine. Regular cleaning of the machine and its components is necessary to prevent blockages and maintain smooth operation.
- Electrical System ChecksThe electrical system of the wire drawing machine should be regularly checked for any issues, such as loose connections or worn cables. Ensuring the electrical system is in good condition helps prevent malfunctions.
Expert Insights on Wire Drawing Machines
Our expert engineers have extensive experience working with wire drawing machines in various industrial settings. Here are some insights they share:
- Selecting the Right Drawing Die Material“Choosing the right drawing die material is critical for achieving the desired wire quality. Tungsten carbide dies are durable and suitable for most materials, but for ultra-fine wires or materials that require exceptional surface finish, diamond dies are the best choice.” – John Doe, Senior Engineer
- Importance of Consistent Lubrication“Lubrication is often overlooked, but it plays a vital role in wire drawing. Consistent and adequate lubrication not only reduces friction but also extends the life of the drawing die and improves the wire’s surface quality.” – Jane Smith, Process Engineer
- Monitoring Wire Tension“Maintaining the correct tension on the wire is essential to prevent breakage and ensure uniform drawing. Operators should regularly check and adjust the capstan speed to match the wire’s drawing speed.” – Michael Brown, Mechanical Engineer
Troubleshooting Common Issues in Wire Drawing
Even with proper maintenance, wire drawing machines can encounter issues. Here are some common problems and their solutions:
- Wire Breakage Solution: Wire breakage can occur due to excessive tension, poor lubrication, or worn drawing dies. To prevent breakage, ensure the wire tension is properly regulated, the lubrication system is functioning correctly, and the drawing dies are in good condition. Regular inspections and adjustments can help prevent this issue.
- Surface Defects on WireSolution: Surface defects, such as scratches or grooves, can result from debris on the wire or drawing die, insufficient lubrication, or improper die alignment. To resolve this issue, clean the wire and die thoroughly before starting the drawing process, ensure the lubrication system is delivering sufficient lubricant, and check that the wire is aligned correctly with the die.
- Inconsistent Wire DiameterSolution: Variations in wire diameter can be caused by worn dies, fluctuations in wire tension, or uneven drawing speed. To maintain consistent diameter, regularly inspect and replace drawing dies as needed, monitor and adjust the capstan speed to ensure uniform tension, and ensure the wire drawing machine operates at a stable speed.
- Overheating of WireSolution: Overheating can occur if the wire drawing speed is too high, the lubrication is inadequate, or the wire material is not suitable for the chosen drawing process. To prevent overheating, reduce the drawing speed, ensure the lubrication system is functioning correctly, and consider using a material more suited to the wire drawing process.
- Die WearSolution: Die wear is inevitable but can be minimized by using high-quality dies and ensuring proper lubrication. Regularly inspect the dies for wear and replace them as needed to maintain wire quality. Implementing a routine maintenance schedule will help prolong the life of the drawing dies.
Future Trends in Wire Drawing Technology
The wire drawing industry continues to evolve, with new technologies and techniques emerging to improve efficiency, quality, and sustainability. Here are some trends to watch:
- Automation and DigitalizationThe integration of automation and digital technologies in wire drawing machines is on the rise. Automated systems can monitor and adjust machine parameters in real-time, ensuring optimal performance and reducing the risk of human error. Digitalization enables predictive maintenance, where sensors collect data to predict when components will need maintenance, minimizing downtime.
- Sustainable PracticesAs industries move towards sustainability, the wire drawing sector is also adopting eco-friendly practices. These include the development of biodegradable lubricants, energy-efficient machines, and recycling systems for waste materials generated during the drawing process.
- Advanced MaterialsThe demand for advanced materials, such as high-strength alloys and composites, is driving innovation in wire drawing technology. New die materials and coatings are being developed to handle these challenging materials, ensuring precision and durability in the wire drawing process.
- High-Speed Wire DrawingAdvances in machine design and materials are enabling higher drawing speeds, increasing production efficiency. High-speed wire drawing machines are particularly beneficial for industries that require large volumes of wire, such as automotive and construction.
Conclusion
Wire drawing machines are indispensable tools in the manufacturing industry, enabling the production of wires with precise dimensions and mechanical properties. Understanding the working principles, types, and applications of these machines is essential for knowledge seekers, students, and working professionals in the field.
This guide has provided an in-depth overview of wire drawing machines, covering everything from their key components and working principles to maintenance practices and future trends. By following the expert insights and troubleshooting tips shared in this article, you can ensure the optimal performance and longevity of wire drawing machines in your operations.
Whether you’re a student looking to deepen your understanding of wire drawing technology or a professional seeking practical knowledge for your work, this guide offers valuable information that will enhance your expertise and help you achieve your goals in the field.
From EngiTech Team
At EngiTech, we empower engineers, professionals, and knowledge seekers with cutting-edge information and expert insights into the world of industrial machinery. Whether you’re exploring the latest advancements in wire drawing machines or diving deep into the complexities of industrial dryers, our comprehensive guides and resources are designed to enhance your expertise and drive your success. Stay ahead of the curve with EngiTech, where precision meets innovation in industrial engineering.