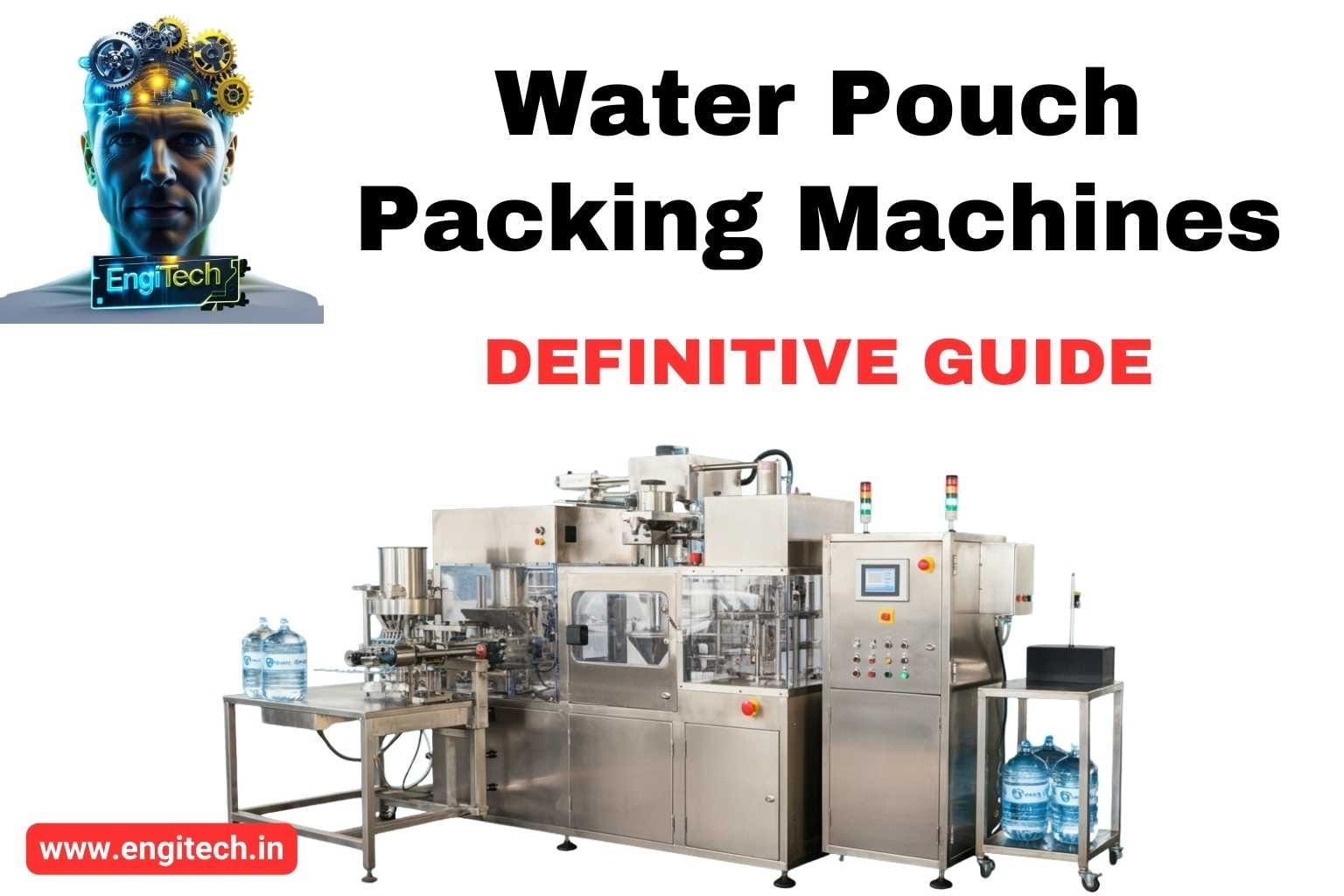
Water is not just a basic necessity—it’s a cornerstone of health and well-being. As the demand for convenient, hygienic, and cost-effective water packaging continues to soar, the water pouch packing machine has emerged as a pivotal solution.
This comprehensive guide delves into everything you need to know about water pouch packing machines, from foundational concepts and operational best practices to expert insights that will help you optimize efficiency and maintain top-notch quality. Whether you’re just venturing into the packaged water business or you’re looking to upgrade your current system, this article will equip you with the knowledge and confidence to make an informed decision.
In the sections that follow, we’ll explore how a water pouch packing machine works, why it’s become an industry standard, and how you can select and maintain the right model for your specific needs. You’ll discover the common pitfalls, the must-have features, and how to stay compliant with industry regulations. By the end, you’ll not only understand the ins and outs of these machines but also be ready to integrate them seamlessly into your operations.
Table of Contents
Understanding the Basics of Water Pouch Packing
When it comes to delivering safe, clean drinking water in an easily transportable and cost-effective format, water pouch packing offers a compelling solution. At the most fundamental level, these machines automate the process of filling, sealing, and cutting pouches that contain water.
Why Pouches, and Not Bottles?
- Cost Efficiency: Pouches generally require less material than bottles, and the packaging material (often a specialized polyethylene film) can be more affordable.
- Space Optimization: Pouches are more compact, making shipping and storage more efficient.
- Eco-Friendly Footprint: Many pouch materials are recyclable. Moreover, the reduced bulk means lower transportation emissions.
Consumer Demand and Market Trends
The rising preference for on-the-go hydration solutions has expanded the market for small, single-serving water pouches. Retailers and suppliers see significant savings in logistics, and consumers appreciate the convenience. All of this underscores why a robust water pouch packing machine is key for businesses aiming to meet modern consumer expectations.
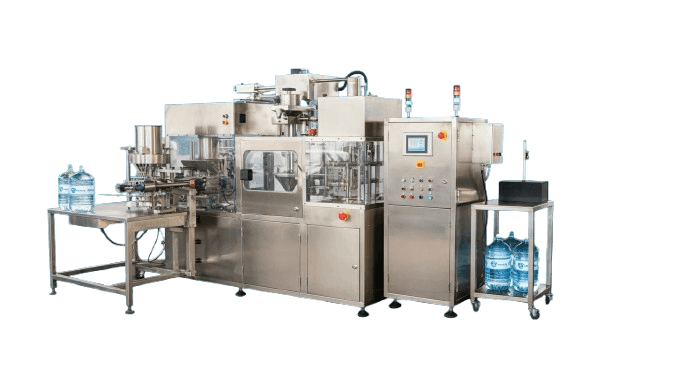
Key Components of a Water Pouch Packing Machine
A water pouch packing machine might look complex at first glance, but understanding its main components can help you operate it more effectively and troubleshoot issues. Here are the critical parts:
- Film Roll Holder
- Holds the roll of packaging film used to create each pouch.
- Equipped with tension control to ensure smooth film feed.
- Forming Tube
- Shapes the film into the cylindrical or rectangular form that becomes the pouch.
- Often adjustable to accommodate different pouch sizes.
- Filling Nozzle
- Dispenses water into the formed pouch with precision.
- In advanced models, can be outfitted with flow meters or volumetric controls for high accuracy.
- Sealing Jaws
- Heat-seal or ultrasonic-seal the film to create a secure enclosure.
- Responsible for both vertical and horizontal seals.
- Cutting Mechanism
- Slices individual pouches from the continuous roll.
- May be servo-driven for precise cut length and minimal wastage.
- Control Panel
- Houses the electronics and user interface.
- Allows operators to input settings like filling volume, sealing temperature, and production speed.
Each of these components plays a vital role. When selecting a machine, pay close attention to how they’re built and the quality of their materials.
How Does a Water Pouch Packing Machine Work?
A water pouch packing machine typically follows a straightforward, linear process. Once you load the roll of film at the start, the machine automates almost every subsequent step:
- Film Unwinding
- The machine unwinds the film from the roll.
- Sensors detect any tension issues or misalignment.
- Forming the Pouch
- The film travels around a forming tube.
- Heat or ultrasonic sealers attach the edges, creating a tube shape.
- Water Filling
- The formed tube passes beneath a filling nozzle.
- The machine dispenses a pre-measured amount of water.
- Sealing and Cutting
- Sealing jaws seal the top of the pouch.
- Simultaneously, the machine seals the bottom of the next pouch.
- A cutting mechanism separates individual pouches.
- Output and Collection
- The finished water pouch is dispensed onto a collection area or conveyor.
- Operators or automated systems then pack these pouches for distribution.
Modern machines often incorporate sensors and microcontrollers to monitor temperature, fill levels, and seal integrity. This ensures a consistent, high-quality final product with minimal operator intervention.
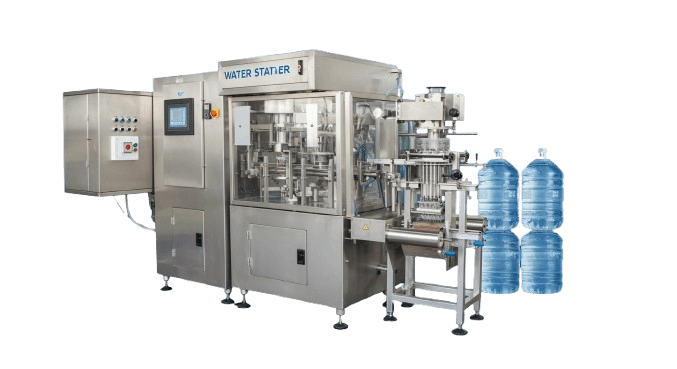
Advantages of Using a Water Pouch Packing Machine
Investing in a water pouch packing machine can offer a host of advantages, whether you’re a small startup looking to break into the packaged water market or a large-scale operation that needs to improve efficiency.
- Scalability
- Machines come in various capacities, ranging from small-scale units to high-speed industrial models.
- As your production needs grow, you can scale up by choosing a more advanced machine or adding additional units.
- Consistency and Quality Control
- Automated processes ensure each pouch is filled to the exact volume specified.
- Seals remain uniform across all pouches, reducing leakage risks.
- Reduced Labor Costs
- The automated nature of these machines cuts down on manual labor.
- Operators mainly focus on loading film, changing settings, and basic oversight.
- Enhanced Hygiene
- Many machines operate within enclosed systems, reducing contamination risks.
- Some models incorporate UV sterilization or other features to maintain water purity.
- Versatility
- Modern water pouch packing machines can often handle different pouch sizes.
- Some are also adaptable to package beverages like juices or liquid food products.
- Eco-Friendly Solutions
- Pouches typically require less plastic material than bottles of the same volume.
- Reduced packaging weight can lead to fewer carbon emissions during transport.
When evaluated holistically—time savings, cost reductions, improved quality—a water pouch packing machine quickly proves its worth.
Different Types of Water Pouch Packing Machines
Not all water pouch packing machines are created equal. Manufacturers design them for different operational speeds, fill volumes, sealing technologies, and automation levels. Below are some common types:
- Manual Machines
- Require an operator for several steps, including pouch positioning and sealing.
- Ideal for very small operations or places with limited electricity access.
- Semi-Automatic Machines
- Automate some stages (like sealing and cutting) but might need manual intervention for water filling or pouch placement.
- Offer a balance between affordability and improved productivity.
- Automatic Machines
- Fully automate forming, filling, sealing, and cutting processes.
- Controlled via a PLC (Programmable Logic Controller) or similar systems.
- Best suited for medium to large-scale production environments.
- High-Speed Machines
- Feature multiple lanes or advanced mechanics to produce thousands of pouches per hour.
- Often used by large beverage companies or factories aiming for mass distribution.
- Ultrasonic Sealing Machines
- Use ultrasonic vibrations instead of heat to fuse the plastic layers.
- May reduce the risk of damaging the film and allow for faster sealing in some cases.
- Vertical Form-Fill-Seal (VFFS) Machines
- Integrate the entire process vertically, making them compact.
- Popular in diverse industries for packaging snacks, powders, and liquids—including water.
Matching Your Needs to a Machine
- Production Volume: Estimate how many pouches you plan to produce per day, week, or month.
- Budget Constraints: Balance between upfront costs and long-term operational savings.
- Film Compatibility: Ensure the machine supports the material grade suitable for water.
- Additional Features: Look for integrated sterilization, data logging, or customizable pouch sizes.
By aligning machine specifications with your production goals, you can optimize efficiency and ensure a steady return on investment.
Steps to Choose the Right Water Pouch Packing Machine
Selecting the best water pouch packing machine can make or break your packaging line’s profitability and reliability. Below is a systematic approach to guide your decision:
- Define Production Goals
- How many pouches per hour or per shift do you need?
- Are you aiming for incremental growth or preparing for massive distribution?
- Set a Realistic Budget
- Factor in both the initial cost of the machine and ongoing maintenance.
- Don’t forget ancillary costs like packaging film, spare parts, and labor.
- Evaluate Key Features
- Look for advanced sealing techniques, built-in sensors, and user-friendly control panels.
- Check for proven track records on consistency and minimal downtime.
- Assess Film Compatibility
- Ensure that the machine can handle the thickness and type of film you intend to use.
- If you plan to switch between different films or incorporate recyclable materials, confirm that the machine can adapt.
- Consider After-Sales Support
- Warranty length and coverage can be crucial.
- Technical support availability—both remote and on-site—is essential.
- Look for comprehensive training packages, especially if your team is new to automated packaging.
- Inspect or Request a Demo
- Whenever possible, see the machine in action.
- If visiting a showroom or factory is not feasible, request video demos or references from existing users.
By following these steps, you’ll be well on your way to finding a water pouch packing machine that aligns perfectly with your operational needs and growth strategy.
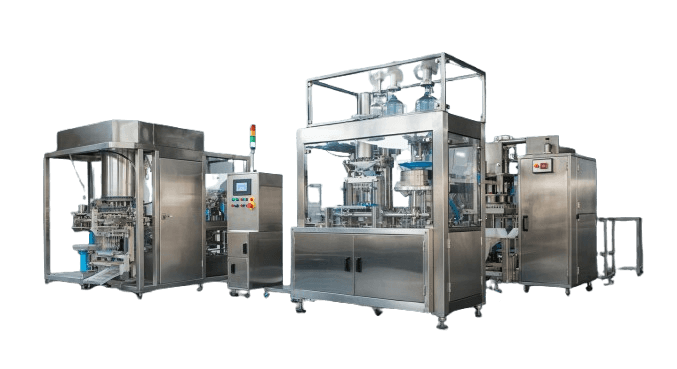
Installation and Operational Best Practices
Even the best water pouch packing machine can’t deliver optimal results without proper installation and operation. Below are best practices to ensure smooth functioning:
- Site Preparation
- Allocate sufficient floor space for the machine, film storage, and operator movement.
- Maintain a clean, dust-free environment to reduce contamination risks.
- Ensure stable flooring—vibrations can interfere with sensitive filling and sealing mechanisms.
- Electrical & Water Supply
- Confirm voltage requirements and ensure a stable power source.
- For direct water supply machines, use purified or pre-treated water to avoid clogging and contamination.
- Follow Manufacturer Guidelines
- Adhere to recommended settings for temperature, pressure, and speed.
- Use approved spare parts and consumables.
- Operator Training
- Train all operators thoroughly on startup, shutdown, emergency stops, and cleaning procedures.
- Familiarize them with the control panel interfaces and typical error messages.
- Quality Checks
- Regularly inspect seals to ensure no leaks.
- Conduct random sampling of pouches to test volume accuracy and seal integrity.
- Sanitation Protocols
- Clean the machine at regular intervals to prevent bacterial growth.
- If possible, perform CIP (Cleaning-In-Place) for the filling lines to maintain water purity.
A correct installation coupled with well-trained personnel sets the stage for maximum uptime, reduced waste, and high-quality pouch output.
Maintenance Tips for Longevity
Your water pouch packing machine is a significant investment, and proper maintenance can extend its service life by years. Below are key tips for keeping your machine in top shape:
- Daily Inspections
- Check the forming tube and sealing jaws for residue or film buildup.
- Verify all sensors are functioning correctly.
- Weekly Cleaning
- Remove any film scraps that might block the cutting mechanism.
- Wipe down external and internal surfaces with a food-grade cleaning solution.
- Lubrication Schedules
- Certain moving parts (e.g., gears, chains, bearings) need regular lubrication.
- Always use lubricants recommended by the manufacturer.
- Replace Worn Parts Promptly
- Worn-out belts, seals, or cutting blades can cause uneven pouches or leaks.
- Keep essential spare parts on hand for quick replacements.
- Software Updates & Calibration
- If your machine has a PLC or microcontroller, stay updated with the latest firmware.
- Schedule periodic calibrations for filling accuracy.
- Professional Servicing
- Arrange annual or bi-annual visits from authorized technicians.
- Regular professional checkups can catch issues that might not be evident in day-to-day inspections.
By prioritizing maintenance, you safeguard not only the machine’s efficiency but also the consistency and safety of your packaged water.
Common Troubleshooting and Problem-Solving
Even the most advanced water pouch packing machine can run into hiccups. Knowing how to diagnose and solve these quickly can save you from significant downtime:
- Leaking Pouches
- Possible Causes: Improper sealing temperature, misalignment of sealing jaws, contaminated film.
- Solutions: Check the heat settings, ensure the forming tube is aligned, and clean sealing surfaces.
- Inconsistent Fill Volume
- Possible Causes: Fluctuating water pressure, faulty flow meter, or air bubbles in the filling line.
- Solutions: Stabilize water supply, calibrate flow meter, and purge air from the filling system.
- Film Jams
- Possible Causes: Incorrect film tension, damaged film roll, or debris in the film path.
- Solutions: Adjust tension settings, remove and inspect film roll, clear any obstructions.
- Machine Overheating
- Possible Causes: Excessive production speed, failing cooling fans, or clogged ventilation.
- Solutions: Reduce the operational pace, clean or replace fans, and ensure adequate airflow around the machine.
- Control Panel Errors
- Possible Causes: Software bugs, loose wiring, or sensor failures.
- Solutions: Reboot the system, secure any loose connections, or consult the manufacturer for a software update.
Performing regular checkups and adhering to the recommended maintenance schedule can prevent most of these issues from escalating.
Industry Regulations and Compliance
Packaging drinking water comes with a responsibility to meet high safety and quality standards. Regulatory bodies often have stringent guidelines in place. Understanding these will help you choose and operate a water pouch packing machine ethically and legally.
- Food-Grade Materials
- Ensure the packaging film meets food-contact regulations.
- In many countries, polypropylene (PP) or polyethylene (PE) must comply with FDA or similar local standards.
- Sanitation Protocols
- Periodic machine cleaning and water testing are often mandatory.
- Keep detailed records to demonstrate compliance.
- Labeling Requirements
- Depending on your region, you may need to list nutritional information, source of water, and expiry dates.
- Ensure your printing or labeling method is clear and non-toxic.
- Facility Inspection
- Government agencies may inspect your facility to ensure hygienic conditions.
- Keep all operational and cleaning logs up-to-date.
- Traceability
- Some markets require batch coding or QR codes for product tracking.
- Integrate your water pouch packing machine with a labeling system if this is a regulatory requirement.
Staying informed about local and international food safety guidelines is crucial. Not only does it help avoid legal complications, but it also fosters consumer trust.
Frequently Asked Questions (FAQ)
Below are some of the most common questions people have when exploring the world of water pouch packing machines:
1. How much does a water pouch packing machine cost?
Costs can vary widely based on automation level, brand reputation, and added features. Entry-level manual or semi-automatic models might range from a few thousand dollars, while fully automatic high-speed lines can reach well into the tens of thousands.
2. Can these machines handle other liquids besides water?
Yes. Many water pouch packing machines can also handle beverages like fruit juices, flavored drinks, and even liquid condiments—provided the machine’s material compatibility and filling mechanisms are suitable.
3. What is the average production speed?
Production speed can range from 500 pouches per hour for smaller semi-automatic models to several thousand pouches per hour for industrial-scale automatic machines.
4. How often should I clean the machine?
Daily wipe-downs and weekly deeper cleans are recommended. If you’re switching from one product to another or if your water supply is prone to contamination, more frequent cleaning may be necessary.
5. Do I need any special permits to operate a water pouch packing machine?
That depends on your local regulations. Typically, you will need a license or permit to package and sell drinking water. The facility may require inspections to ensure compliance with health and safety standards.
Conclusion
The water pouch packing machine stands as a game-changer in modern beverage packaging. From its cost efficiency and scalability to the environmental benefits of reduced plastic usage, this packaging method satisfies both business goals and evolving consumer expectations. By selecting the right machine for your production levels, maintaining it diligently, and staying compliant with regulations, you pave the way for a profitable and sustainable operation.
Whether you’re an emerging entrepreneur or an established bottling facility, now is the perfect time to leverage the advantages of a water pouch packing machine. You’ve learned about different machine types, core components, maintenance protocols, and even troubleshooting tactics. The next step is to translate this knowledge into concrete action.
Ready to optimize your packaging process and elevate your brand’s reputation for quality and convenience?
- Explore Our In-Depth Resource Library: Dive deeper into related topics like [efficient water filtration systems], [high-speed pouch sealing solutions], and [food-grade packaging material innovations].
- Schedule a Demo: Reach out to trusted machine suppliers to see a live demonstration of a water pouch packing machine that meets your specifications.
- Consult with Experts: Speak to packaging consultants or equipment specialists to tailor the best solution for your facility size and budget.
- Stay Updated: Subscribe to industry newsletters and forums. Continuous learning is essential for staying ahead in a competitive market.
By embracing the potential of a water pouch packing machine, you’re not just improving operational efficiencies—you’re making a statement to your customers that you value sustainability, convenience, and reliability. Implement these insights, take decisive action, and watch your production line transform for the better. And remember: in the final analysis, how effectively you package water can be just as important as the quality of the water itself. Here’s to more efficient packaging, satisfied consumers, and a robust future in the water distribution industry!
(Note: This article is intended for informational purposes. Always consult local regulations and machine-specific guidelines before installing or operating any water pouch packing machine.)
Stay Connected with EngiTech
EngiTech is your trusted source for in-depth knowledge on industrial mechanical engineering machines and technologies. Stay ahead with the latest innovations, expert insights, and practical guides designed to help you make informed decisions for your business and engineering needs. Join our growing community of professionals and industry leaders to stay updated and competitive in the ever-evolving world of industrial technology.