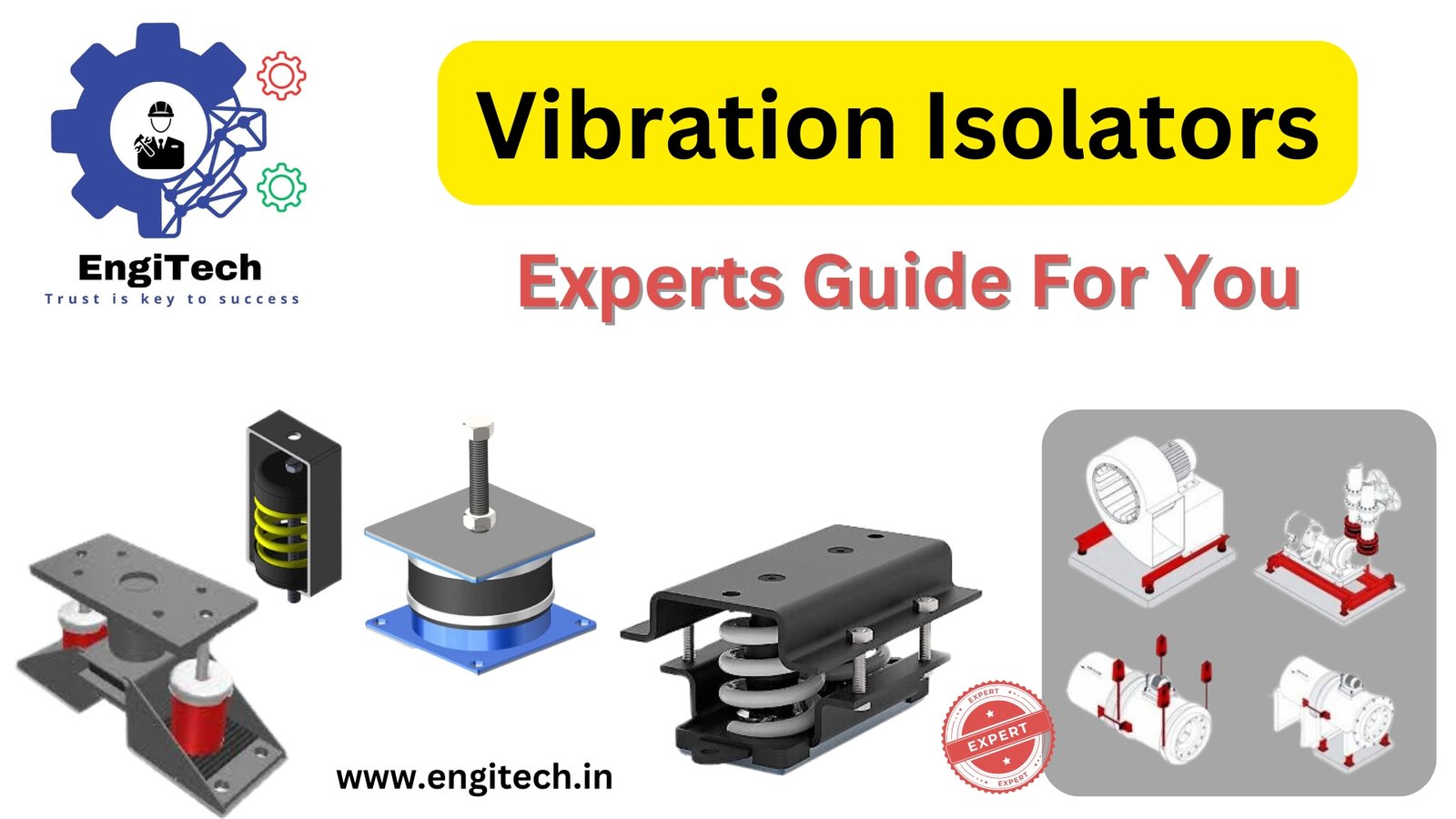
In the world of industrial and mechanical applications, vibration isolators play a critical role in ensuring the smooth and efficient operation of machinery. Whether you’re managing sensitive equipment or large industrial machines, dealing with unwanted vibrations is a common challenge that can lead to equipment wear, reduced accuracy, and potential failures. This comprehensive guide will take you through everything you need to know about vibration isolators, from understanding what they are and how they work, to selecting the right type for your specific needs.
By the end of this guide, you’ll have a clear understanding of how to optimize your equipment’s performance, extend its lifespan, and reduce downtime by effectively managing vibrations.
Table of Contents
What Are Vibration Isolators?
Vibration isolators are devices designed to minimize or eliminate the transmission of vibration from one area or object to another. They are essential for protecting both machinery and the environment from the adverse effects of vibrations. Isolators work by absorbing and dissipating the energy created by vibrating systems, ensuring that sensitive equipment remains unaffected by external vibrations and that machines operate at peak efficiency.
Common applications for vibration isolators include:
- Industrial machinery: Reducing wear and tear on components.
- Automotive industry: Protecting vehicle components from road-induced vibrations.
- Electronics: Preventing damage to sensitive components.
- Building structures: Mitigating the effects of environmental vibrations.
How Do Vibration Isolators Work?
Vibration isolators operate on the principle of energy absorption and dissipation. When a machine or system vibrates, the isolator absorbs the vibration energy and prevents it from transferring to nearby structures or equipment. The effectiveness of an isolator depends on its ability to reduce the vibration transmission ratio, which measures how much vibration is being passed through.
There are two main types of isolators:
- Passive isolators: These rely on materials such as rubber, springs, or elastomers to absorb vibrations.
- Active isolators: These use sensors and actuators to counteract vibrations in real-time, offering higher precision.
Types of Vibration Isolators
Selecting the right type of vibration isolator is crucial to achieving optimal performance. Below, we outline the most common types:
1. Rubber Vibration Isolators
Rubber isolators are widely used due to their elasticity and ability to absorb a wide range of frequencies. They are cost-effective and ideal for light to medium-duty applications. Rubber isolators are typically used in the automotive and electronics industries to minimize vibrations from engines, motors, or small components.
Advantages:
- Cost-effective
- Easy to install
- Available in various shapes and sizes
Disadvantages:
- Limited durability in extreme temperatures
- Not suitable for very high-frequency vibrations
2. Spring Vibration Isolators
Spring isolators are mechanical devices that use metal springs to absorb vibrations. They are often used for heavy machinery and equipment that operates in low-frequency vibration environments. Spring isolators can handle significant loads, making them ideal for industrial applications.
Advantages:
- High load capacity
- Effective in low-frequency environments
- Durable and long-lasting
Disadvantages:
- Larger in size compared to rubber isolators
- More expensive
3. Air Vibration Isolators
Air isolators use compressed air to create a cushioning effect that absorbs vibrations. These isolators are commonly found in precision equipment where even the smallest vibration can affect performance, such as laboratory instruments or high-precision manufacturing tools.
Advantages:
- Excellent at absorbing low-frequency vibrations
- Adjustable damping capacity
- Ideal for precision applications
Disadvantages:
- Expensive
- Requires a constant supply of air
4. Polymer Vibration Isolators
Polymers like neoprene and silicone are also popular materials for vibration isolators. They offer a good balance between flexibility, durability, and vibration dampening.
Advantages:
- Resistant to extreme temperatures
- Long-lasting
- Can be molded into various shapes
Disadvantages:
- Higher cost than rubber isolators
- Limited load capacity
Factors to Consider When Choosing Vibration Isolators
Choosing the right vibration isolator involves understanding several factors that can influence its effectiveness:
1. Load Capacity
It’s crucial to select an isolator that can handle the weight of your equipment. Overloading an isolator can result in poor performance and a shorter lifespan.
2. Frequency Range
Different isolators are designed to handle specific frequency ranges. It’s essential to match the isolator’s frequency response to the vibrations produced by your machinery.
3. Environmental Conditions
Consider the operational environment of your equipment. Temperature extremes, exposure to chemicals, and moisture can affect the durability of certain isolator materials like rubber or polymers.
4. Space Constraints
Vibration isolators come in various sizes and shapes, so it’s essential to select one that fits within the spatial limits of your equipment setup.
5. Durability
If your equipment operates in harsh conditions, such as high temperatures or exposure to chemicals, choose an isolator made from durable materials like metal or specialized polymers.
Benefits of Using Vibration Isolators
The use of vibration isolators offers several advantages, both for machinery and the environment it operates in:
- Extended Equipment Lifespan: By reducing wear and tear caused by vibrations, isolators help to prolong the life of your equipment, leading to cost savings on maintenance and replacement parts.
- Increased Precision: For sensitive equipment, such as measuring instruments, reducing vibrations can significantly improve accuracy and performance.
- Improved Safety: Machinery that vibrates excessively can pose safety risks to operators and surrounding structures. Isolators help minimize these risks by stabilizing equipment.
- Reduced Noise Levels: Vibration is often accompanied by noise, which can create an uncomfortable work environment. Vibration isolators help to reduce noise pollution by dampening the source of the vibration.
Installation Tips for Vibration Isolators
To maximize the benefits of vibration isolators, proper installation is key. Here are some expert tips:
- Ensure Correct Alignment: Misalignment can reduce the effectiveness of an isolator. Always ensure that the isolator is properly aligned with the equipment.
- Distribute Load Evenly: If using multiple isolators, ensure the weight of the equipment is distributed evenly across all isolators to prevent overloading.
- Regular Maintenance: Periodically check isolators for signs of wear and tear. Damaged isolators should be replaced immediately to maintain performance.
- Follow Manufacturer Guidelines: Always adhere to the manufacturer’s installation and maintenance recommendations for best results.
Troubleshooting Common Issues with Vibration Isolators
While vibration isolators are highly effective, issues can arise if they are not selected or installed properly. Here are some common problems and how to address them:
1. Insufficient Vibration Damping
If your isolator isn’t reducing vibrations effectively, check if it’s suitable for the frequency range of your equipment. Consider switching to an isolator designed for lower or higher frequency vibrations.
2. Isolator Overloading
If the isolator is deformed or compressed, it may be overloaded. Upgrade to a model with a higher load capacity or distribute the weight more evenly.
3. Material Degradation
Rubber and polymer isolators can degrade over time, especially in harsh environments. If you notice cracks, hardening, or other signs of wear, replace the isolators with more durable options like metal springs or air isolators.
FAQs about vibration isolators:
1. What are vibration isolators?
Vibration isolators are devices designed to reduce or eliminate the transmission of vibrations from one structure or object to another, protecting machinery and equipment from the negative effects of vibration.
2. How do vibration isolators work?
Vibration isolators work by absorbing and dissipating the energy created by vibrations, preventing it from transferring to sensitive equipment or surrounding structures. This helps in improving performance, accuracy, and safety.
3. What are the types of vibration isolators?
Common types include rubber isolators, spring isolators, air isolators, and polymer isolators. Each type is suited for different applications, depending on load capacity, vibration frequency, and environmental factors.
4. Why are vibration isolators important in industrial applications?
Vibration isolators are crucial in industries because they prevent excessive vibration, which can lead to equipment wear, reduced precision, and operational failures. They also contribute to noise reduction and improved safety.
5. How do I choose the right vibration isolator for my equipment?
To choose the right vibration isolator, consider factors such as load capacity, frequency range, environmental conditions, size constraints, and the specific type of vibration your equipment experiences.
6. What materials are used for vibration isolators?
Common materials include rubber, metal springs, air-filled bags, and polymers like silicone or neoprene, depending on the vibration frequency and application requirements.
7. Can vibration isolators reduce noise as well?
Yes, many vibration isolators also help reduce noise levels. Since vibration and noise are often related, isolators that dampen vibrations can also reduce the sound produced by equipment.
8. What is the difference between active and passive vibration isolators?
Active isolators use sensors and actuators to counteract vibrations in real-time, while passive isolators rely on materials like rubber or springs to absorb and dampen vibrations without active intervention.
9. How often should vibration isolators be replaced?
The replacement frequency depends on the operational environment and material durability. Regular inspection for wear and tear is recommended, and isolators should be replaced when signs of damage or performance decline are noticed.
10. Can vibration isolators improve the lifespan of my machinery?
Yes, by reducing wear and tear caused by vibrations, vibration isolators can significantly extend the lifespan of machinery and reduce maintenance costs.
Conclusion
Investing in the right vibration isolators can dramatically improve the performance, precision, and longevity of your equipment. By absorbing and dissipating unwanted vibrations, isolators protect both your machinery and its surrounding environment. Whether you’re dealing with industrial-grade machinery or sensitive laboratory equipment, understanding how vibration isolators work and selecting the right type for your specific needs is crucial.
Are you looking to enhance the efficiency and durability of your industrial equipment? At EngiTech, we provide a wide range of expert resources and the latest insights on industrial solutions like vibration isolators. Explore our comprehensive resources on EngiTech and stay updated on the latest innovations in vibration isolation technologies.
For more in-depth guides and expert advice on industrial equipment, visit EngiTech today. Stay ahead of the competition with our cutting-edge resources and solutions tailored to your needs.