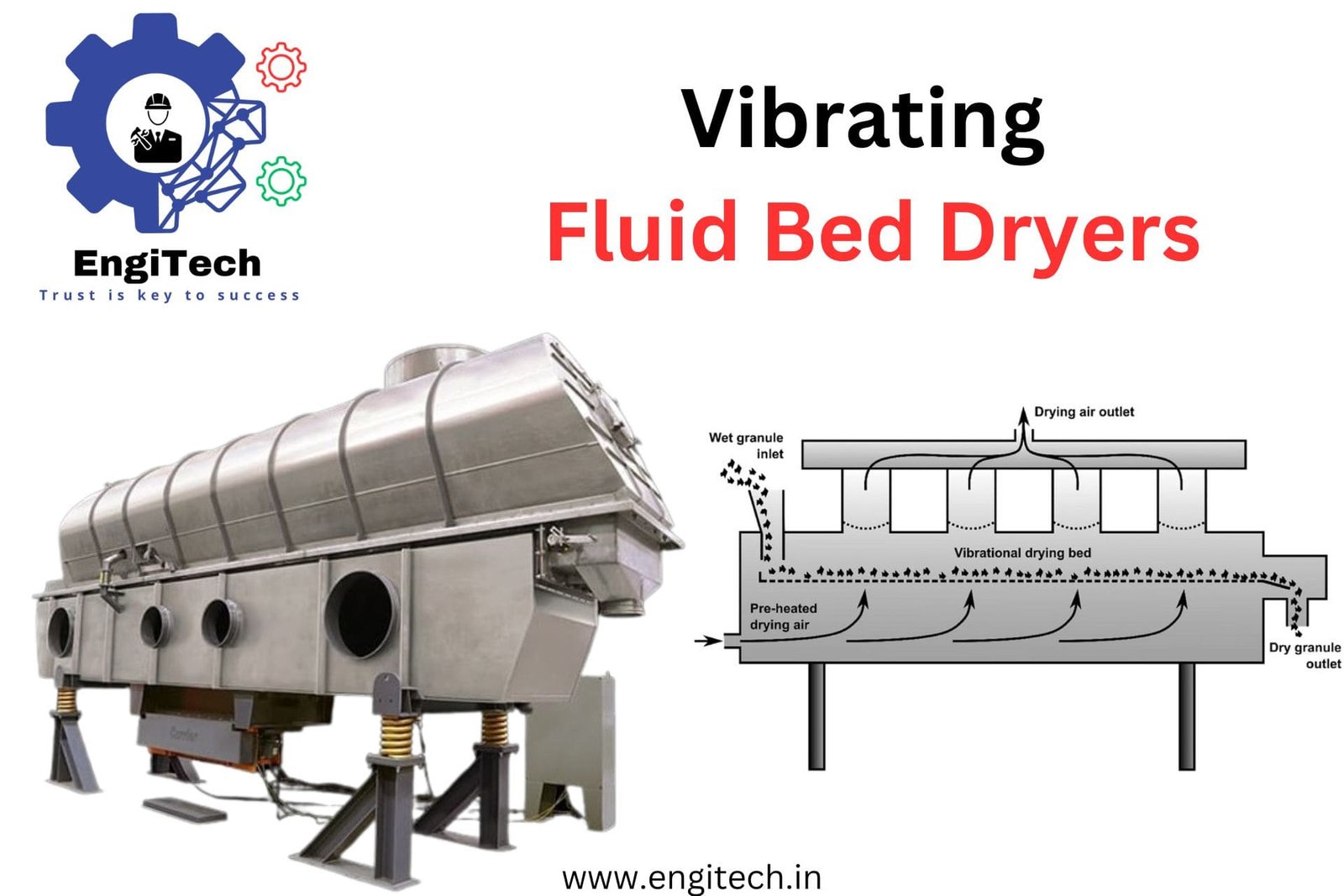
Vibrating fluid bed dryers (VFBDs) or vibratory fluidized bed dryers have become essential in various industries, offering efficient and uniform drying for particulate materials. These dryers utilize both air and mechanical vibrations to enhance the fluidization process, leading to improved drying performance. This guide delves into the concept, working principle, applications, benefits, and latest advancements in vibrating fluid bed dryer technology.
What is a Vibrating Fluid Bed Dryer?
A vibrating fluid bed dryer uses vibrations to assist in the fluidization of particles. By combining hot air and mechanical vibrations, VFBDs ensure efficient drying of materials, especially those that are sticky, cohesive, or difficult to fluidize using air alone.
How Vibrating Fluid Bed Dryers Work
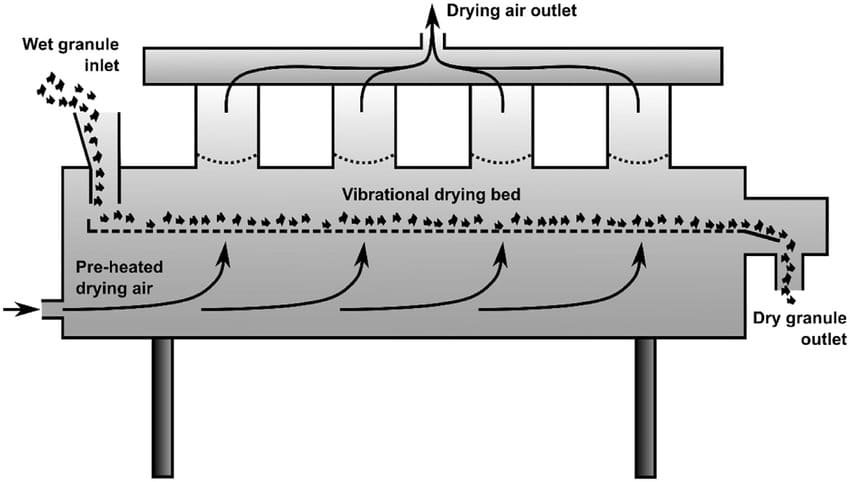
- Fluidization: Place the material in the drying chamber. Introduce a stream of hot air from below, fluidizing the particles. Simultaneously, apply mechanical vibrations to enhance the fluidization process.
- Heat Transfer: The fluidized and vibrated state of the particles ensures maximum contact with the hot air, promoting efficient heat transfer and rapid drying.
- Moisture Evaporation: As the hot air passes through the particles, it evaporates the moisture. The combination of fluidization and vibrations prevents particles from sticking together, ensuring uniform drying.
- Exhaust: Exhaust the moist air from the drying chamber through a filter system that removes fine particles, ensuring only clean air is released into the environment.
Types of Vibrating Fluid Bed Dryers
Batch Vibrating Fluid Bed Dryers:
- Process specific amounts of material in each cycle.
- Suitable for small-scale production and materials with varying properties.
Continuous Vibrating Fluid Bed Dryers:
- Process materials in a continuous flow.
- Ideal for large-scale production, ensuring consistent quality and efficiency.
Applications of Vibrating Fluid Bed Dryers
Pharmaceuticals:
- Dry granules, pellets, and powders.
- Essential for producing stable and effective tablets and capsules.
Food Processing:
- Dry grains, cereals, fruits, and vegetables.
- Preserve nutritional value and extend shelf life.
Chemicals:
- Dry powders, crystals, and granules.
- Suitable for heat-sensitive materials, ensuring consistent quality.
Minerals:
- Dry minerals and ores.
- Improve handling and processing efficiency.
Biotechnology:
- Dry biological materials like enzymes and proteins.
- Maintain the stability and activity of sensitive materials.
Benefits of Using Vibrating Fluid Bed Dryers
Enhanced Fluidization: Mechanical vibrations improve the fluidization process, ensuring uniform drying of materials that are difficult to fluidize with air alone.
Uniform Drying: VFBDs ensure consistent product quality by promoting maximum contact between hot air and particles.
High Efficiency: The combination of fluidization and vibrations results in rapid heat transfer and moisture evaporation, significantly reducing drying times.
Versatility: VFBDs can handle a wide range of materials, including sticky, cohesive, and heat-sensitive particles.
Scalability: Available in various sizes and configurations, VFBDs are suitable for both small-scale and large-scale production.
Gentle Drying: The fluidization process provides gentle drying, preserving the integrity and quality of delicate materials.
Reduced Agglomeration: Vibrations prevent particles from sticking together, reducing agglomeration and ensuring uniform particle size distribution.
Key Considerations in Selecting a Vibrating Fluid Bed Dryer
Material Properties: Understand the properties of the material to be dried, including particle size, moisture content, and heat sensitivity. This knowledge helps you choose the appropriate VFBD type and optimize the drying process.
Production Scale: Determine the production scale and select a VFBD that can handle the required throughput. Decide whether a batch or continuous VFBD is more suitable for your needs.
Energy Efficiency: Evaluate the energy efficiency of the VFBD. Look for features such as heat recovery systems and variable airflow control to minimize energy consumption and reduce operating costs.
Control Systems: Choose a VFBD with advanced control systems that allow precise monitoring and adjustment of process parameters. This capability ensures consistent product quality and optimizes the drying process.
Cleaning and Maintenance: Consider the ease of cleaning and maintenance when selecting a VFBD. Look for designs that facilitate quick and thorough cleaning to minimize downtime and ensure hygienic operation.
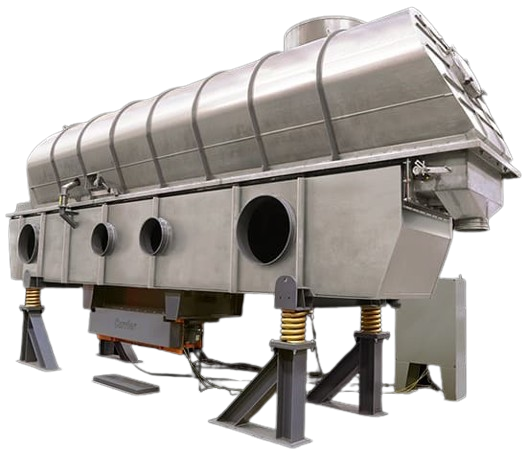
Advances in Vibrating Fluid Bed Dryer Technology
Advanced Control Systems: Modern VFBDs come equipped with advanced control systems that provide real-time monitoring and adjustment of process parameters, ensuring optimal drying conditions.
Energy Efficiency Innovations: New VFBD designs incorporate energy-efficient features such as heat recovery systems and variable airflow control, enhancing energy efficiency and reducing operating costs.
Multi-Stage Drying: Multi-stage VFBDs allow precise control over different drying stages within a single unit, improving efficiency and product quality.
Integration with Continuous Manufacturing: VFBDs are increasingly integrated with continuous manufacturing processes, boosting efficiency and scalability for large-scale production.
Customization: Advances in VFBD technology enable the customization of dryers to meet specific application requirements, optimizing drying processes for various materials.
Conclusion
Vibrating fluid bed dryers play a transformative role in industrial drying, offering uniform and efficient drying for particulate materials. By understanding their working principle, types, applications, and benefits, you can optimize the drying process. The latest advancements in VFBD technology continue to expand their capabilities and applications, making them indispensable in modern industrial processes.
For more in-depth articles and resources on industrial drying technologies and innovations, visit EngiTech.in. Stay updated on the latest advancements and applications in the industry!