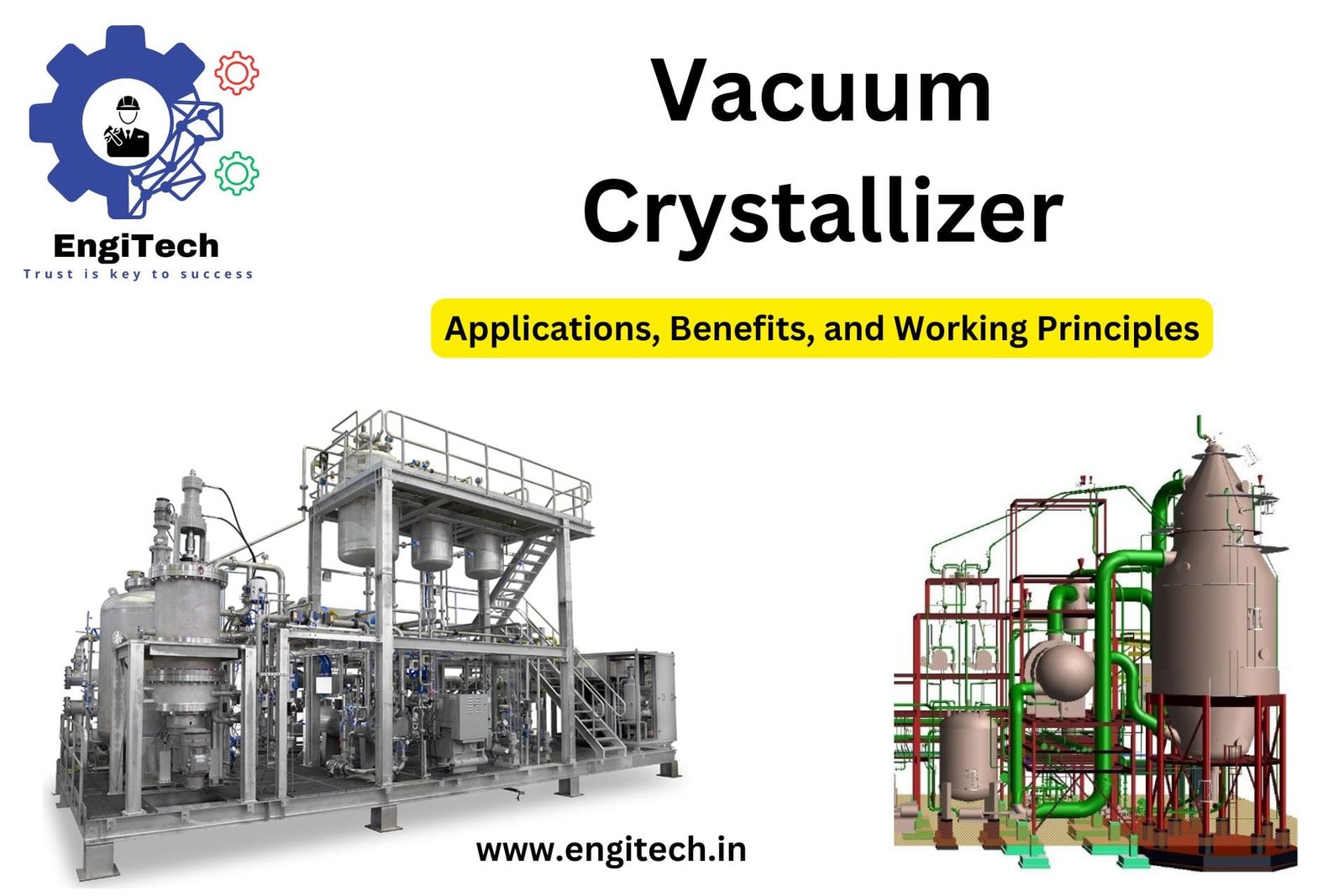
In the realm of industrial chemical processes, vacuum crystallizers stand as one of the most efficient and effective methods for purifying and producing high-quality crystals. Whether you’re involved in the chemical, pharmaceutical, or food processing industry, understanding vacuum crystallization can unlock immense operational and financial benefits.
This guide delves deep into the workings of vacuum crystallizers, their applications, advantages, and why they are essential for modern industries. By the end of this post, you’ll gain actionable insights into leveraging this technology for your processes.
Table of Contents
What Is Vacuum Crystallization?
Vacuum crystallization is a process where the pressure inside a crystallizer is reduced to below atmospheric levels to induce crystallization. By lowering the pressure, the boiling point of the solvent decreases, allowing the solution to evaporate at lower temperatures.
This technology is ideal for handling heat-sensitive materials and ensuring high-purity crystal production. Industries requiring precision and efficiency often rely on this method.
How Vacuum Crystallizers Work
Vacuum crystallizers operate on the principle of controlled evaporation. Here’s a step-by-step overview:
- Preparation: A saturated solution of the desired material is prepared.
- Vacuum Creation: A vacuum pump reduces the pressure inside the crystallizer.
- Boiling Point Reduction: Lower pressure decreases the boiling point of the solvent.
- Evaporation: Solvent evaporates, concentrating the solution.
- Crystallization: As the solution cools, crystals begin to form.
- Collection: Crystals are separated from the mother liquor for further processing.
This method ensures precise control over crystal size, purity, and consistency.
Key Components of a Vacuum Crystallizer
Understanding the components of a vacuum crystallizer is essential for optimal operation. The main components include:
- Vacuum Pump: Reduces the pressure to facilitate crystallization.
- Heat Exchanger: Manages temperature during evaporation.
- Crystallization Chamber: Where the crystals form.
- Agitator: Ensures uniform distribution of solutes.
- Discharge System: Collects and separates crystals from the solution.
Each component plays a critical role in maintaining the efficiency and quality of the crystallization process.
Advantages of Using Vacuum Crystallizers
a. Energy Efficiency
Operating at lower temperatures reduces energy consumption, making the process cost-effective.
b. High Purity Crystals
Controlled conditions ensure the production of uniform, high-purity crystals.
c. Ideal for Heat-Sensitive Materials
Vacuum crystallizers prevent thermal degradation of sensitive compounds by working at lower temperatures.
d. Scalability
From small-scale labs to large industrial setups, vacuum crystallizers can be tailored to suit varying production needs.
Applications Across Industries
Vacuum crystallizers are indispensable in several industries:
a. Pharmaceuticals
Used for purifying active pharmaceutical ingredients (APIs).
b. Food and Beverage
Essential for producing high-purity sugar and other crystalline food additives.
c. Chemicals
Facilitates the crystallization of salts, fertilizers, and specialty chemicals.
d. Water Treatment
Helps in recovering salts from brine solutions.
Their versatility makes them a preferred choice for processes requiring precision and quality.
Factors to Consider When Choosing a Vacuum Crystallizer
To ensure optimal performance, consider the following:
- Capacity Requirements: Match the crystallizer size to your production needs.
- Material Compatibility: Ensure the equipment is made from materials resistant to corrosion or wear from the chemicals used.
- Automation Features: Look for systems with advanced controls for better precision.
- Energy Efficiency: Prioritize models that minimize operational costs.
Maintenance Tips for Prolonging Equipment Life
Proper maintenance ensures the longevity and efficiency of vacuum crystallizers. Follow these tips:
- Regular Inspections: Check for wear and tear in components like pumps and agitators.
- Cleaning: Remove residues after each batch to prevent contamination.
- Lubrication: Ensure moving parts are well-lubricated to avoid friction damage.
- Calibration: Regularly calibrate sensors and controls for accurate operation.
Future Trends in Vacuum Crystallization Technology
The future of vacuum crystallization is geared toward greater efficiency and sustainability. Emerging trends include:
- AI and IoT Integration: For predictive maintenance and process optimization.
- Green Energy Solutions: Utilizing renewable energy sources for operations.
- Advanced Materials: Development of corrosion-resistant alloys for longer equipment life.
These advancements aim to make vacuum crystallizers even more efficient and eco-friendly.
FAQs About Vacuum Crystallizers
1. What is the purpose of a vacuum crystallizer?
A vacuum crystallizer is used to produce high-purity crystals by lowering the boiling point of solvents through reduced pressure. It is ideal for processing heat-sensitive materials and ensuring precise crystal size and quality.
2. How does vacuum crystallization differ from conventional crystallization?
Vacuum crystallization operates under reduced pressure, enabling solvent evaporation at lower temperatures. This contrasts with conventional methods that rely on high temperatures, making vacuum crystallization more energy-efficient and suitable for temperature-sensitive compounds.
3. What industries commonly use vacuum crystallizers?
Industries like pharmaceuticals, food and beverage, chemicals, and water treatment extensively use vacuum crystallizers for applications such as purifying APIs, producing sugar, crystallizing salts, and recovering materials from waste streams.
4. What factors affect the efficiency of a vacuum crystallizer?
Key factors include the quality of the vacuum system, temperature control, solution concentration, and the design of the crystallization chamber. Proper maintenance also plays a significant role in ensuring consistent performance.
5. What materials are suitable for vacuum crystallization?
Vacuum crystallizers can handle a wide range of materials, including salts, sugars, pharmaceuticals, fertilizers, and specialty chemicals. However, the choice of equipment material should be compatible with the chemical properties of the solution to prevent corrosion or degradation.
6. How do you maintain a vacuum crystallizer?
Maintenance includes regular inspections, cleaning after each use, lubricating moving parts, calibrating sensors, and ensuring the vacuum pump is functioning correctly. Proper maintenance extends the equipment’s life and ensures efficient operation.
7. What are the advantages of using vacuum crystallizers in production?
Vacuum crystallizers offer multiple benefits, such as energy efficiency, production of high-purity crystals, suitability for heat-sensitive materials, and scalability for different production volumes.
These FAQs address common concerns and provide insights into the operation, benefits, and applications of vacuum crystallizers.
Conclusion
Vacuum crystallization is a transformative technology for industries that demand precision, efficiency, and high-quality output. From pharmaceuticals to water treatment, its applications are vast and impactful.
By understanding the principles, components, and maintenance requirements of vacuum crystallizers, businesses can achieve superior results while optimizing costs.
Explore more about cutting-edge industrial drying and crystallization technologies on EngiTech. Stay ahead with the latest innovations and resources!