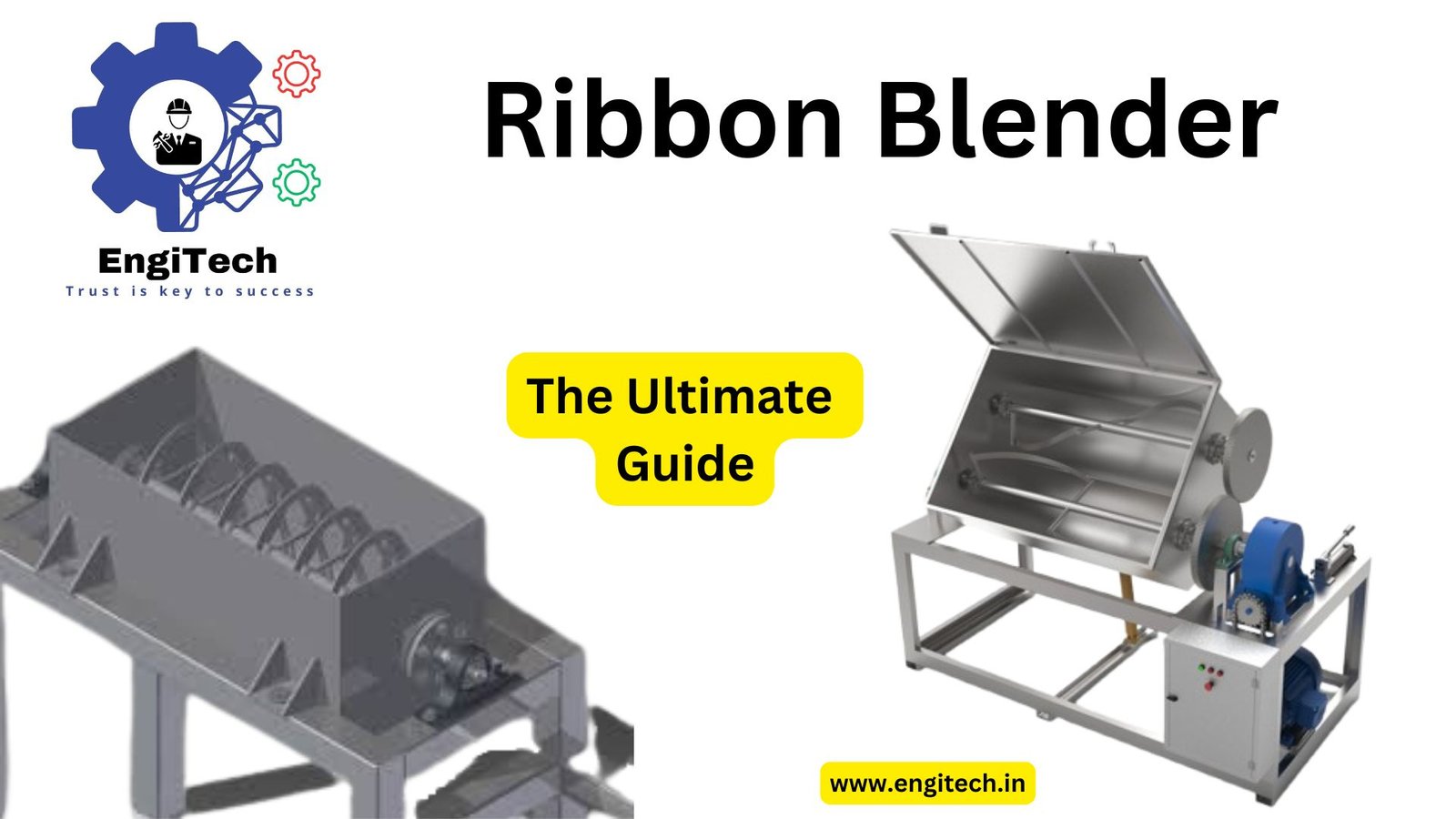
Ribbon blenders are versatile mixing machines essential across industries such as food, pharmaceuticals, and chemicals. This comprehensive guide explores their design, functionality, and advantages, helping you decide if a ribbon blender suits your application.
Table of Contents
What is a Ribbon Blender?
Overview of Ribbon Blenders
- Definition: A ribbon blender is an industrial mixing machine that uses counter-rotating ribbons to achieve uniform mixing.
- Key Features:
- Double or triple-layer ribbons for enhanced blending efficiency.
- Cylindrical drum design for consistent performance.
Primary Components
- Inner and Outer Ribbons: Counter-rotating for efficient mixing.
- Mixing Chamber: Designed for uniform distribution.
- Drive System: Powers the ribbons using a motor and gearbox.
- Discharge Mechanism: Ensures easy and quick unloading.
How Ribbon Blenders Work
Principles of Operation
Ribbon blenders mix materials by using helical ribbons that move the contents in opposing directions. This creates a shearing effect, perfect for dry and semi-wet ingredients.
Step-by-Step Process
- Load the materials into the mixing chamber.
- Activate the motor, which drives the ribbons.
- Inner and outer ribbons push materials in opposite directions, achieving uniformity.
- Discharge the mixed batch through the outlet.
Advantages of Ribbon Blenders
Efficiency and Versatility
- High mixing efficiency for both powders and semi-wet materials.
- Suitable for bulk production with consistent results.
Cost-Effectiveness
- Lower operational costs compared to other industrial mixers.
- Minimal energy consumption for high-volume operations.
Ease of Use
- Simple operation and maintenance.
- Quick material discharge with minimal residue.
Applications of Ribbon Blenders
Food Industry
- Mixing spices, flour, and baking ingredients.
- Preparing dry soup mixes and snacks.
Pharmaceuticals
- Blending active pharmaceutical ingredients (APIs).
- Homogenizing powders for tablet formulations.
Chemicals
- Mixing fertilizers, pesticides, and detergents.
- Creating uniform batches of powder coatings.
Selecting the Right Ribbon Blender
Key Considerations
- Capacity: Ensure the blender fits your production needs.
- Material Compatibility: Choose a design compatible with your ingredients (e.g., stainless steel for food).
- Motor Power: Opt for sufficient horsepower for your applications.
- Discharge Type: Pick between manual, pneumatic, or automatic discharge.
Maintenance and Best Practices
Routine Maintenance Tips
- Inspect ribbons regularly for wear and tear.
- Lubricate moving parts to reduce friction.
- Clean the mixing chamber thoroughly after each batch.
Ensuring Longevity
- Avoid overloading the machine.
- Use recommended cleaning agents to maintain material integrity.
Ribbon Blender vs. Other Industrial Mixers
Comparison with Paddle Mixers
- Mixing Time: Ribbon blenders are faster for dry blends.
- Material Handling: Better for free-flowing powders.
Comparison with V-Blenders
- Cost: Ribbon blenders are more affordable.
- Capacity: Higher capacity options available.
Optimizing Ribbon Blender Performance
Tips for Efficient Mixing
- Pre-weigh ingredients for precise formulations.
- Monitor mixing times to prevent over-processing.
- Use baffles for improved mixing of light materials.
Troubleshooting Common Issues
- Uneven Mixing: Check ribbon alignment.
- Motor Overheating: Reduce load or inspect the motor.
FAQs About Ribbon Blenders
1. What is a ribbon blender used for?
A ribbon blender is used for mixing dry powders, granules, and semi-wet ingredients in industries such as food, pharmaceuticals, chemicals, and construction.
2. How does a ribbon blender work?
A ribbon blender uses counter-rotating inner and outer helical ribbons to move materials in opposite directions, creating a shearing and mixing effect for uniform distribution.
3. What are the key components of a ribbon blender?
The main components include:
- Mixing chamber.
- Inner and outer ribbons.
- Motor and gearbox.
- Discharge outlet.
4. What industries commonly use ribbon blenders?
Industries like food processing, pharmaceuticals, chemicals, agriculture, and construction rely on ribbon blenders for consistent and efficient mixing.
5. Can ribbon blenders handle wet materials?
Yes, ribbon blenders can handle semi-wet materials, but they are primarily designed for dry blending applications.
6. How do I select the right ribbon blender?
Consider factors like:
- Capacity.
- Material compatibility.
- Power requirements.
- Discharge mechanism.
7. What are the advantages of a ribbon blender?
Key advantages include high mixing efficiency, cost-effectiveness, versatility, and ease of operation and maintenance.
8. What is the typical capacity of ribbon blenders?
Capacities range from small-scale models (50 liters) to large industrial blenders exceeding 10,000 liters.
9. What materials are used to construct ribbon blenders?
Ribbon blenders are commonly made of stainless steel or carbon steel, depending on the application and material being processed.
10. How long does it take to mix materials in a ribbon blender?
Mixing times vary depending on the material properties, but most operations are completed in 10 to 15 minutes.
11. How do you clean a ribbon blender?
- Remove residual material.
- Use a cleaning solution compatible with the materials handled.
- Rinse thoroughly and dry to prevent contamination.
12. Can ribbon blenders be customized?
Yes, manufacturers offer customization options like different ribbon designs, motors, discharge mechanisms, and materials for specific needs.
13. What safety features should a ribbon blender have?
Key safety features include overload protection, interlock systems, and safety covers for moving parts.
14. How do ribbon blenders compare to paddle mixers?
Ribbon blenders are more efficient for dry blending, while paddle mixers are better suited for wet and sticky materials.
15. What is the cost of a ribbon blender?
The cost varies based on size, materials, and customization but typically ranges from $5,000 to $50,000 or more for industrial models.
Conclusion
Ribbon blenders are indispensable for industries that prioritize efficiency and uniformity. By understanding their design, operation, and advantages, you can make informed decisions tailored to your production needs.
Explore more resources on industrial mixing solutions and innovations at EngiTech. Stay updated with the latest advancements in mechanical engineering!