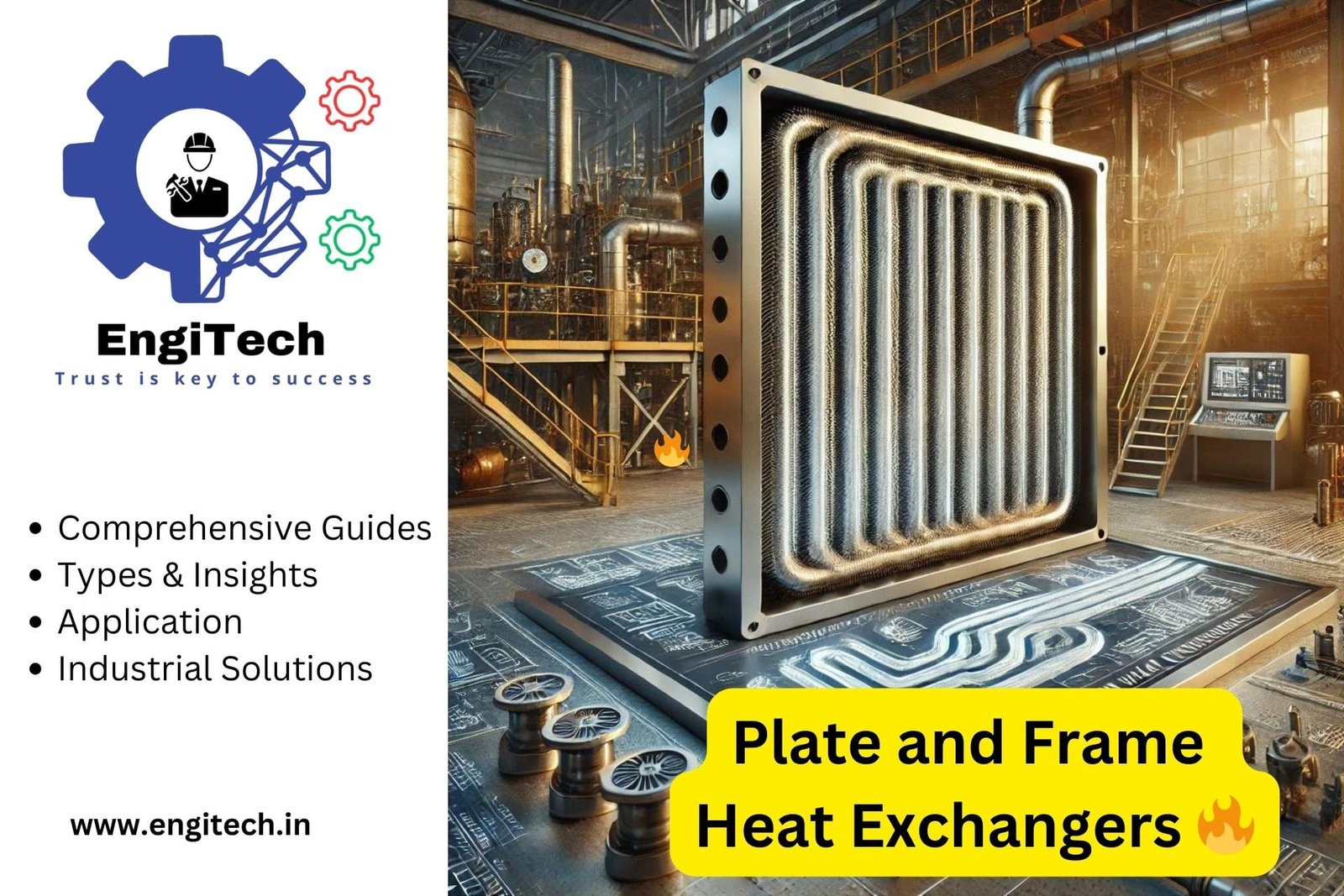
Plate and frame heat exchangers (PFHEs) are a critical component in numerous industrial processes, renowned for their efficiency and versatility in heat transfer applications. This type of heat exchanger offers a compact and cost-effective solution for transferring heat between fluids, making it ideal for a variety of industries, including chemical processing, food and beverage, pharmaceuticals, and HVAC systems.
In this detailed guide, we will explore the working principles, types, applications, advantages, maintenance, and advancements of plate and frame heat exchangers, providing valuable insights into their functionality and benefits.
Table of Contents
Introduction to Plate and Frame Heat Exchangers
Plate and frame heat exchangers consist of a series of thin, corrugated metal plates that are bolted together with gaskets between each plate. The plates create parallel channels for the fluids to flow through, with each fluid confined to alternate channels. The design allows for a large surface area, facilitating efficient heat transfer between the fluids without mixing them. The versatility of PFHEs allows them to be customized for specific applications, making them a popular choice across industries.
How Plate and Frame Heat Exchangers Work
The core principle behind plate and frame heat exchangers is maximizing the surface area available for heat transfer. The plates are arranged so that the hot and cold fluids flow in alternate channels. As the fluids flow across the corrugated surfaces, heat transfers from the hotter fluid to the cooler one through the metal plates. The corrugations create turbulence, enhancing the heat transfer rate by disrupting the boundary layer on the plate surfaces.
Flow Arrangements
There are three primary flow arrangements in plate and frame heat exchangers:
- Counter flow: The hot and cold fluids flow in opposite directions, which maximizes the temperature gradient along the length of the heat exchanger. This arrangement is the most efficient, allowing for the greatest heat transfer.
- Parallel Flow: The fluids flow in the same direction. This arrangement is less efficient than counter flow because the temperature difference between the fluids decreases along the flow path.
- Crossflow: The fluids flow perpendicular to each other. This configuration is often used when space constraints prevent the use of other arrangements. While less efficient than counter flow, crossflow can be effective in specific applications.
Types of Plate and Frame Heat Exchangers
Plate and frame heat exchangers come in various types, each designed for specific operational requirements and applications. The main types include:
1. Gasketed Plate and Frame Heat Exchangers
Gasketed PFHEs are the most common type, featuring plates with gaskets that seal the fluid channels and direct the flow. The gaskets are made from elastomeric materials, which allow for easy removal and reassembly of the plates for cleaning and maintenance. This design is flexible and can accommodate a wide range of applications by adjusting the number of plates.
2. Brazed Plate and Frame Heat Exchangers
In brazed PFHEs, the plates are permanently joined by brazing, eliminating the need for gaskets. This design is compact and leak-proof, making it suitable for applications involving high pressures and temperatures. Brazed PFHEs are often used in HVAC systems, refrigeration, and other industries where a compact design is critical.
3. Welded Plate and Frame Heat Exchangers
Welded PFHEs have plates welded together, providing a strong, durable seal that can handle aggressive fluids and high pressures. They are ideal for applications in the chemical and petrochemical industries, where the fluids can be highly corrosive. However, welded PFHEs are not as easy to maintain as gasketed ones, as they cannot be disassembled for cleaning.
4. Semi-Welded Plate and Frame Heat Exchangers
Semi-welded PFHEs combine welded and gasketed designs. Pairs of plates are welded together, and gaskets are used between these pairs. This design allows one fluid side to handle aggressive or hazardous fluids while the other side remains accessible for maintenance. Semi-welded PFHEs are used in applications requiring both high chemical resistance and ease of maintenance.
5. Fully Welded Plate and Frame Heat Exchangers
Fully welded PFHEs are similar to welded ones but with all plates welded together, forming a single block. This design is highly resistant to corrosion and can withstand very high pressures and temperatures. Fully welded PFHEs are commonly used in oil and gas, chemical processing, and power generation industries.
Applications of Plate and Frame Heat Exchangers
Plate and frame heat exchangers are versatile and find applications in a wide range of industries due to their efficient heat transfer capabilities and adaptability. Some common applications include:
1. Chemical Processing
In chemical processing, PFHEs are used for heating, cooling, and condensing chemical mixtures. They can handle corrosive fluids and high temperatures, making them suitable for various chemical reactions and processes.
2. Food and Beverage Industry
PFHEs are extensively used in the food and beverage industry for pasteurization, sterilization, and cooling of products. Their hygienic design, ease of cleaning, and precise temperature control make them ideal for handling food products.
3. HVAC Systems
In HVAC systems, PFHEs transfer heat between air and water or refrigerant, providing efficient heating and cooling solutions. They are used in heat recovery systems, air conditioning units, and district heating and cooling systems.
4. Pharmaceuticals
The pharmaceutical industry uses PFHEs for maintaining precise temperatures during processes like fermentation, crystallization, and purification. The ability to maintain sterile conditions and the easy cleaning of plates make PFHEs suitable for pharmaceutical applications.
5. Power Generation
In power plants, PFHEs are used for heat recovery, cooling, and condensing. They help improve the efficiency of power generation processes by transferring heat from one medium to another, often using waste heat for energy recovery.
6. Marine Applications
PFHEs are used in marine applications for cooling engines, lubricating oil, and other fluids. Their compact size and high efficiency make them suitable for use in confined spaces on ships and offshore platforms.
Advantages of Plate and Frame Heat Exchangers
Plate and frame heat exchangers offer several advantages that make them a preferred choice in many industries:
1. High Efficiency
The large surface area provided by the plates and the corrugated design enhances heat transfer efficiency. The high turbulence created by the design increases the heat transfer rate, making PFHEs highly efficient.
2. Compact Design
PFHEs are more compact than shell and tube heat exchangers, making them suitable for installations with space constraints. Their modular design also allows for easy expansion or modification.
3. Ease of Maintenance
Gasketed PFHEs can be easily disassembled for cleaning, inspection, and maintenance. The plates can be individually cleaned, and gaskets can be replaced, reducing downtime and maintenance costs.
4. Flexibility
The modular nature of PFHEs allows for easy reconfiguration and customization. The number of plates can be adjusted to meet specific capacity requirements, making them adaptable to changing process conditions.
5. Low Fouling Risk
The high turbulence created by the corrugated plates reduces the risk of fouling, ensuring efficient operation over a longer period. This is particularly beneficial in applications involving fluids with suspended solids.
6. Cost-Effectiveness
PFHEs are cost-effective due to their high efficiency, compact design, and lower maintenance requirements. They offer a lower total cost of ownership compared to other heat exchanger types.
7. Hygienic Design
In industries where hygiene is critical, such as food and beverage and pharmaceuticals, PFHEs provide a clean and sanitary solution. The smooth surfaces and easy-to-clean design help maintain high hygiene standards.
Maintenance and Troubleshooting of Plate and Frame Heat Exchangers
Proper maintenance of plate and frame heat exchangers is essential to ensure optimal performance and longevity. Regular inspections, cleaning, and monitoring can prevent common issues and extend the life of the equipment.
1. Inspection
Routine inspections help identify signs of wear, corrosion, or damage. Operators should check for leaks, gasket integrity, and the condition of the plates. Early detection of issues can prevent more significant problems and costly downtime.
2. Cleaning
Cleaning is crucial to prevent fouling and maintain heat transfer efficiency. Depending on the application, operators can use chemical cleaning, mechanical cleaning, or a combination of both. Gasketed PFHEs can be easily disassembled for thorough cleaning.
3. Gasket Replacement
Gaskets are crucial components that seal the fluid channels in gasketed PFHEs. Over time, gaskets may degrade due to chemical exposure, temperature fluctuations, or mechanical stress. Regular replacement ensures a proper seal and prevents leaks.
4. Plate Replacement
In cases where plates are damaged or corroded, replacing them is necessary to maintain performance. Operators should ensure that replacement plates are compatible with the existing system and materials of construction.
5. Troubleshooting Common Issues
Operators may encounter common issues such as leaks, reduced heat transfer efficiency, or pressure drops. Addressing these issues promptly requires identifying the root cause, which could involve inspecting gaskets, cleaning the plates, or checking for mechanical damage.
Technological Advancements in Plate and Frame Heat Exchangers
Advancements in technology continue to enhance the performance and capabilities of plate and frame heat exchangers. Innovations in materials, design, and manufacturing processes have led to the development of more efficient and reliable PFHEs.
1. Advanced Materials
The use of advanced materials such as titanium, nickel alloys, and specialized coatings has improved the corrosion resistance and durability of PFHEs. These materials are particularly beneficial in applications involving aggressive chemicals or high temperatures.
2. Enhanced Plate Designs
Innovations in plate design, such as optimized corrugation patterns and microchannel structures, have increased heat transfer efficiency and reduced pressure drops. These designs promote better fluid distribution and minimize dead zones.
3. Compact and Lightweight Designs
Efforts to reduce the size and weight of PFHEs have resulted in more compact and lightweight models. These designs are ideal for applications with space constraints or where weight is a critical factor.
4. Automation and Control
The integration of automation and control systems allows for real-time monitoring and optimization of PFHE performance. Advanced sensors and control algorithms help maintain optimal operating conditions, improving efficiency and reducing energy consumption.
5. 3D Printing and Additive Manufacturing
3D printing and additive manufacturing technologies have enabled the production of complex plate designs with high precision. These technologies allow for customized solutions and rapid prototyping, accelerating the development of new PFHE models.
Conclusion
Plate and frame heat exchangers are essential components in various industries, offering efficient heat transfer solutions in a compact and versatile design. Their ability to handle a wide range of fluids, pressures, and temperatures makes them ideal for applications in chemical processing, food and beverage, HVAC systems, pharmaceuticals, and more.
With ongoing technological advancements and a growing focus on energy efficiency and sustainability, plate and frame heat exchangers will continue to play a vital role in industrial processes. As industries evolve and new challenges arise, PFHEs will adapt and innovate, providing reliable and efficient solutions for years to come.
FAQs about plate and frame heat exchangers:
1. What is a plate and frame heat exchanger, and how does it work?
- A plate and frame heat exchanger is a type of heat exchanger that uses thin, corrugated plates arranged in a frame to transfer heat between two fluids. The fluids flow through alternate channels created by the plates, allowing heat transfer through the plate surfaces without mixing the fluids.
2. What are the advantages of plate and frame heat exchangers?
- Plate and frame heat exchangers offer high heat transfer efficiency, compact design, ease of maintenance, flexibility in capacity adjustments, low fouling risk, and cost-effectiveness. They are also suitable for applications requiring hygienic conditions.
3. What are the different types of plate and frame heat exchangers?
- The main types include gasketed plate and frame heat exchangers, brazed plate and frame heat exchangers, welded plate and frame heat exchangers, semi-welded plate and frame heat exchangers, and fully welded plate and frame heat exchangers. Each type has specific features suited for different applications.
4. In which industries are plate and frame heat exchangers commonly used?
- Plate and frame heat exchangers are used in a variety of industries, including chemical processing, food and beverage, pharmaceuticals, HVAC systems, power generation, and marine applications. They are versatile and can handle various fluids and temperatures.
5. How do I select the right plate and frame heat exchanger for my application?
- Selection depends on factors such as the type of fluids, temperature and pressure requirements, flow rates, and the desired heat transfer efficiency. Consulting with a heat exchanger specialist or using selection software can help determine the best option for specific needs.
6. What materials are used in plate and frame heat exchangers?
- Common materials include stainless steel, titanium, nickel alloys, and other high-performance materials. The choice of material depends on the chemical compatibility with the fluids, temperature, pressure conditions, and corrosion resistance requirements.
7. How often should plate and frame heat exchangers be cleaned?
- The frequency of cleaning depends on the application and the nature of the fluids. Regular inspections and cleaning are necessary to prevent fouling and maintain heat transfer efficiency. Gasketed PFHEs can be easily disassembled for thorough cleaning.
8. What is the difference between gasketed and brazed plate and frame heat exchangers?
- Gasketed plate and frame heat exchangers use removable gaskets to seal the plates and direct fluid flow, allowing for easy disassembly and cleaning. Brazed plate and frame heat exchangers have plates permanently joined by brazing, providing a compact, leak-proof design suitable for high-pressure and high-temperature applications.
9. Can plate and frame heat exchangers handle high-pressure applications?
- Yes, certain types of plate and frame heat exchangers, such as brazed and welded PFHEs, are designed to handle high-pressure applications. They are suitable for demanding environments, including chemical processing and power generation.
10. How do I maintain a plate and frame heat exchanger?
- Regular maintenance includes inspections for leaks, gasket integrity checks, cleaning, and replacing damaged plates or gaskets. Preventive maintenance helps ensure efficient operation and extends the life of the heat exchanger.
11. What are the common issues faced with plate and frame heat exchangers?
- Common issues include fouling, gasket degradation, leaks, and pressure drops. Addressing these issues promptly through regular maintenance and proper operation can prevent significant performance losses.
12. Are plate and frame heat exchangers suitable for hygienic applications?
- Yes, plate and frame heat exchangers are widely used in the food and beverage and pharmaceutical industries due to their hygienic design. They allow for easy cleaning and sterilization, ensuring compliance with stringent hygiene standards.
These FAQs provide essential information and address common queries about plate and frame heat exchangers, helping users understand their functionality, applications, and maintenance requirements.
At EngiTech, we are your trusted source for expert knowledge and detailed insights into industrial engineering solutions, specializing in essential equipment like plate and frame heat exchangers, shell and tube heat exchangers, and more. Our website offers a wealth of information, from comprehensive guides and technical articles to the latest industry trends and innovations. Whether you’re in chemical processing, food and beverage, pharmaceuticals, or any other industry, we provide the expertise you need to optimize your processes, improve efficiency, and stay ahead of the competition.
Explore our resources to find the best solutions for your engineering challenges and elevate your business to new heights with EngiTech.in. Join our community of industry professionals and discover how our knowledge can drive your success.