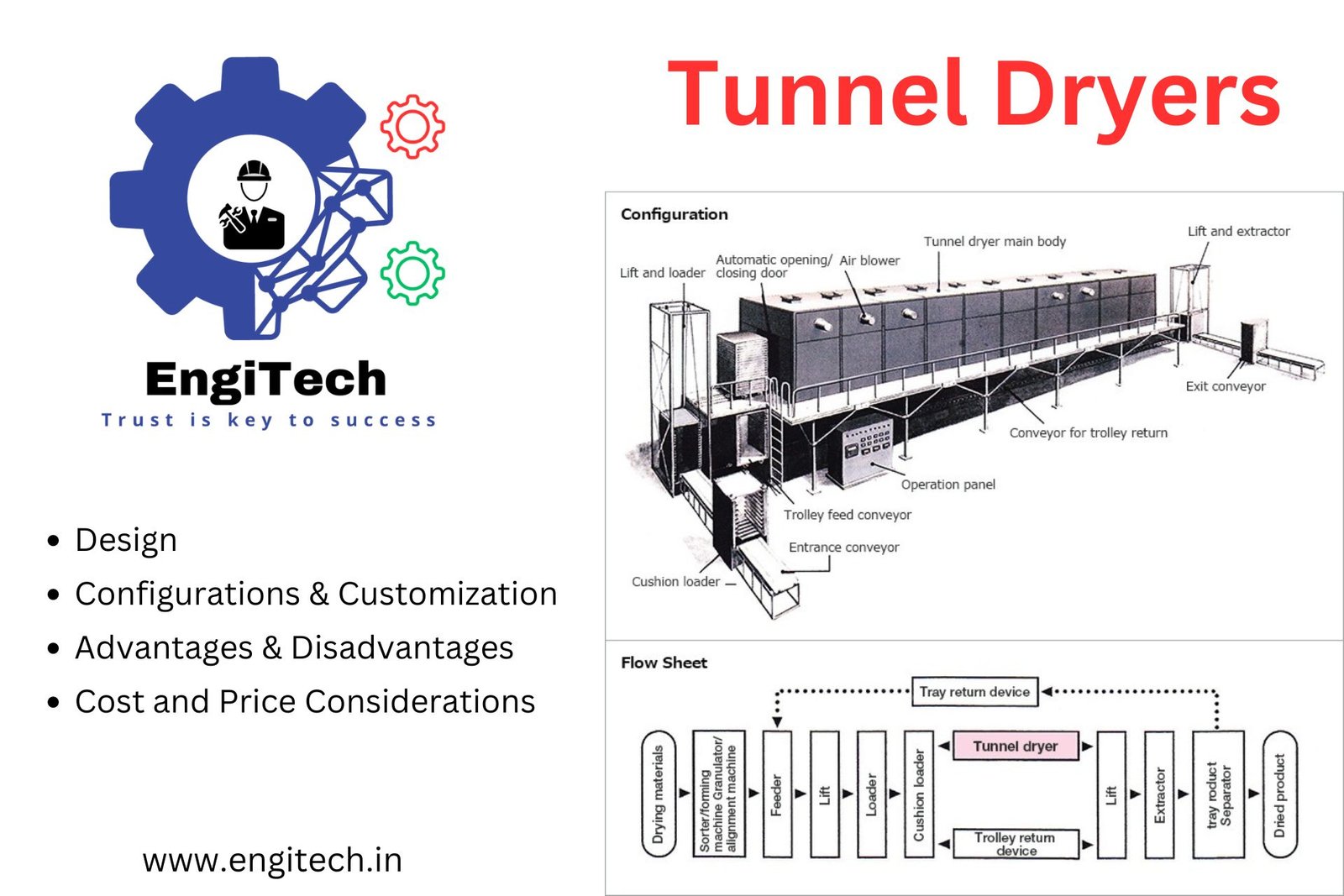
Tunnel dryers are versatile drying systems widely used in various industries for drying bulk materials. Their design, configurations, and customization options make them suitable for a broad range of applications. In this blog, we will explore the design aspects, configurations, customization possibilities, cost considerations, and the advantages and disadvantages of tunnel dryers.
Questions This Blog Will Answer:
- What are the design aspects of tunnel dryers?
- What configurations are available for tunnel dryers?
- How can tunnel dryers be customized for specific needs?
- What are the cost factors associated with tunnel dryers?
- What are the advantages and disadvantages of tunnel dryers?
Tunnel Dryer Design
Tunnel dryers are designed to provide efficient and uniform drying of materials. Key design aspects include:
- Construction Material:
- Typically made from stainless steel or other corrosion-resistant materials to withstand high temperatures and moisture.
- Insulated inner surfaces to minimize energy loss and enhance efficiency.
- Heating Systems:
- Utilize various heating methods such as hot air, microwave, RF (radio frequency), or infrared.
- Equipped with high-quality heat exchangers to ensure consistent heating and low air moisture.
- Air Circulation:
- Designed with an efficient air circulation system to improve airflow and decrease drying time.
- Air patterns can be counterflow, parallel flow, or combined flow to suit different drying requirements.
- Transport Mechanism:
- Use roller or belt conveyors to move materials through the tunnel.
- Conveyor speed and temperature settings can be controlled via a touchscreen panel for precise drying conditions.
- Control Systems:
- Feature advanced control mechanisms for accurate temperature and airflow management.
- Available in automated or semi-automated configurations for ease of operation.
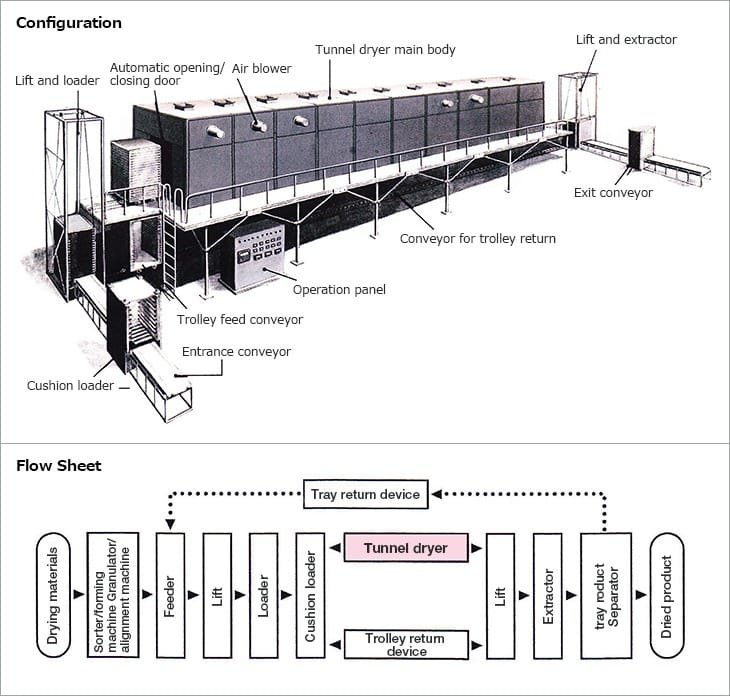
Configurations of Tunnel Dryers
Tunnel dryers come in various configurations to meet different industrial needs. Common configurations include:
- Batch Tunnel Dryers:
- Designed for drying materials in batches. Ideal for small to medium-scale operations.
- Continuous Tunnel Dryers:
- Allow for continuous feeding and discharge of materials, suitable for large-scale operations and consistent production lines.
- Modular Tunnel Dryers:
- Comprised of modular sections that can be added or removed as needed, offering flexibility in length and capacity.
- Multi-Zone Tunnel Dryers:
- Feature multiple drying zones with independent temperature and airflow controls, enabling customized drying processes within the same tunnel.
Customization of Tunnel Dryers
Tunnel dryers can be customized to meet specific requirements of different industries. Customization options include:
- Size and Capacity:
- Customizable length, width, and height to accommodate various production scales.
- Heating Methods:
- Choice of heating technologies (hot air, microwave, RF, infrared) based on the material and desired drying speed.
- Material Handling:
- Customizable transport mechanisms such as rollers, belts, or trolleys based on material properties and handling needs.
- Control Systems:
- Advanced control systems with programmable settings for precise temperature, humidity, and conveyor speed management.
- Additional Features:
- Options for additional features like air filtration systems, moisture sensors, and data logging for process monitoring and optimization.
Cost and Price of Tunnel Dryers
The cost of tunnel dryers varies widely based on several factors:
- Size and Capacity:
- Larger and higher-capacity dryers typically cost more due to increased material and construction costs.
- Heating Technology:
- Advanced heating technologies like microwave or RF can significantly increase the cost compared to traditional hot air systems.
- Customization:
- Customization options and additional features add to the overall cost.
- Automation Level:
- Fully automated systems with advanced control mechanisms are more expensive than semi-automated or manual systems.
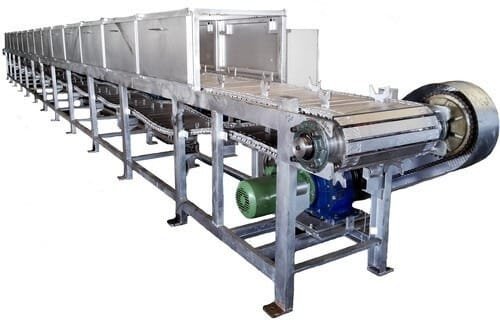
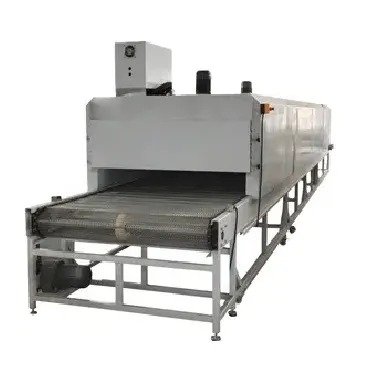
Advantages of Tunnel Dryers
- Efficiency:
- High drying efficiency with uniform heat distribution and controlled airflow.
- Versatility:
- Suitable for drying a wide range of materials across different industries.
- Scalability:
- Available in various sizes and configurations to match production scales.
- Customization:
- Highly customizable to meet specific processing needs and material properties.
- Energy Efficiency:
- Designed to minimize energy loss and maximize drying efficiency.
Disadvantages of Tunnel Dryers
- Initial Cost:
- High initial capital investment, especially for large-scale or highly customized systems.
- Maintenance:
- Regular maintenance required to ensure optimal performance and longevity.
- Complexity:
- Complex systems with advanced controls may require skilled operators and maintenance personnel.
- Space Requirement:
- Tunnel dryers can occupy significant floor space, which may be a limitation for some facilities.
Conclusion
Tunnel dryers are essential in various industries for their efficient and versatile drying capabilities. By understanding their design, configurations, customization options, and cost factors, businesses can make informed decisions to optimize their drying processes. While they offer numerous advantages, it is important to consider the initial investment and maintenance requirements. As technology advances, tunnel dryers will continue to evolve, providing even greater efficiency and adaptability to meet the diverse needs of modern industries.
For more in-depth articles and resources on industrial drying technologies and innovations, visit EngiTech.in. Stay updated on the latest advancements and applications in the industry!