
Imagine spending hours perfecting your product, only to fall short on presentation because your labels are crooked, partially peeling off, or just don’t look professional. A sticker labeling machine can be the transformative piece of equipment your business needs to ensure consistent, high-quality labeling every single time. Within the first few months of integrating an automated labeling system into a production line, many businesses report improved efficiency, reduced waste, and significantly better brand presentation.
In this comprehensive guide, we’ll uncover exactly what a sticker labeling machine is, why it’s indispensable in modern manufacturing, and how you can choose the right one to give your business an unshakable competitive edge.
Table of Contents
Understanding the Role of Modern Labeling
Labeling is not just about slapping a piece of paper with your brand name onto a product—it’s about conveying crucial information in a visually appealing, accurate, and regulatory-compliant manner. Consumers today are more discerning than ever, scrutinizing labels for details such as product ingredients, usage instructions, safety warnings, and environmental claims. Meanwhile, businesses rely on labels to establish brand identity, share barcodes or QR codes, and comply with local and international regulations.
- Brand Identity: A label can instantly communicate the essence of your product. Whether it’s bold, eco-friendly, or luxurious, the design and quality of the label set the tone for how consumers perceive your brand.
- Regulatory Compliance: Different industries—such as food, cosmetics, or pharmaceuticals—have strict guidelines on what information must be displayed. Improper labeling can lead to legal complications and product recalls.
- Operational Efficiency: When labeling is automated, products move seamlessly from one stage of production to another. This efficiency frees up staff time, reduces errors, and speeds up the entire manufacturing process.
Given these stakes, it’s no wonder that the method and quality of labeling can make or break your product’s success. Enter the sticker labeling machine—a specialized piece of equipment designed to handle these challenges and more.

What Is a Sticker Labeling Machine?
A sticker labeling machine is an automated (or semi-automated) device engineered to apply self-adhesive labels, often called “stickers,” onto product containers or surfaces. These labels may include brand logos, nutritional facts, barcodes, compliance data, and marketing slogans. The machine ensures that each label is placed with uniform precision, drastically reducing the possibility of misaligned or wrinkled labels.
Key Attributes
- Speed & Efficiency
Most modern machines can label hundreds or even thousands of products per hour, depending on their configuration and the type of product surface. - Consistency
Labels are applied at the same spot and angle every time, creating a professional and uniform look across all products. - Versatility
Many sticker labeling machines can handle various container shapes—cylindrical, flat, conical, or otherwise. They can also accommodate multiple label sizes and materials.
No matter which industry you operate in—be it food and beverages, pharmaceuticals, chemicals, or cosmetics—chances are you can benefit from the reliability and professionalism offered by a high-quality sticker labeling machine.
Key Components and Features
Although the specifics can vary from model to model, most sticker labeling machines share several core components and features that significantly impact their performance and durability.
Conveyor System
- Role: Moves the product containers through the labeling station.
- Importance: A smooth and efficient conveyor prevents bottlenecks and ensures that each product arrives at the labeling station in the correct orientation.
Label Dispenser
- Role: Holds the roll of self-adhesive labels and feeds them to the application point.
- Importance: The dispenser’s tension control and feed system must be finely tuned to avoid label tears, misfeeds, or jams.
Applicator or Peel Plate
- Role: Strips the label from its backing and places it onto the product.
- Importance: The applicator must align and position the label accurately, adhering it smoothly without wrinkles or bubbles.
Sensor Technology
- Role: Detects the presence of a product and signals the machine to apply the label.
- Importance: Correct sensor calibration prevents misplacements such as labeling air gaps or labeling multiple products at once.
Control Panel and PLC (Programmable Logic Controller)
- Role: Provides an interface for operators to configure speed, labeling placement, and other parameters.
- Importance: A user-friendly control panel with advanced PLC helps in customizing the process for different product shapes or label sizes, and also stores preset configurations for quick changeovers.
Frame and Build Quality
- Role: Provides overall stability and durability to the machine structure.
- Importance: Materials like stainless steel not only offer longevity but also comply with hygiene standards in food and pharmaceutical industries.
How Sticker Labeling Machines Work: A Step-by-Step Breakdown
A well-orchestrated dance occurs behind the scenes every time a label is applied to your product. Here’s a simplified step-by-step walkthrough:
- Product Placement
Products either manually or automatically enter the machine via the infeed conveyor. - Sensing the Product
Once the product crosses an electronic eye or sensor, the machine prepares to dispense a label. - Label Dispensing
The label dispenser feeds the correct length of the label, partially peeling it off its liner. - Application
As the product passes the peel plate or applicator head, the label is pressed firmly onto the surface. Some machines use an air-blow mechanism, while others use a brush or roller to ensure adhesion. - Wrapping or Rolling (if needed)
For cylindrical products, wrap-around rollers may further secure the label around the circumference. - Outfeed
After labeling, the product continues along the conveyor, making room for the next item in the queue. - Real-Time Adjustments
Advanced machines track any misalignment or jams and can pause the line or self-correct automatically.
From start to finish, the entire sequence is timed to perfection, coordinating sensors, mechanical parts, and PLC logic to ensure the highest level of consistency.
Types of Sticker Labeling Machines
Choosing the right type of sticker labeling machine depends on various factors: your production volume, packaging style, budget, and specific labeling requirements. Below are some popular types, each designed to cater to different operational needs.
Automatic vs. Semi-Automatic Machines
- Automatic Machines
These are integrated into a fully automated production line. They handle large volumes without requiring an operator to position or guide each product. If you’re aiming to label thousands of items daily, an automatic machine is often your best bet. - Semi-Automatic Machines
In these systems, an operator typically loads the product manually, and the machine handles the label application. They’re suitable for smaller batches or specialty products. Although slower than automatic machines, they offer flexibility and cost savings for lower production scales.
Inline vs. Rotary Machines
- Inline Machines
Products move in a straight line along a conveyor. Ideal for standard-sized products and moderate to high production volumes. - Rotary Machines
These machines use rotating platforms or turrets to position products for labeling. Rotary models can achieve higher speeds and handle complex label placements (like front-and-back or wrap-around labels).
Wrap-Around vs. Front-and-Back vs. Multi-Sided
- Wrap-Around Machines
Commonly used for bottles and cylindrical containers. Labels wrap around the circumference, ensuring 360° coverage. - Front-and-Back Machines
Ideal for products requiring two separate labels (one on the front, one on the back). These machines apply both labels in a single pass. - Multi-Sided Machines
Used for rectangular or uniquely shaped containers that need multiple labels (e.g., top, bottom, side). Often found in industries with elaborate packaging requirements, such as electronics or premium cosmetics.
Industries That Rely on Sticker Labeling Machines
Sticker labeling machines aren’t limited to a single market segment. Their adaptability and efficiency have made them an invaluable resource across a wide range of industries:
- Food & Beverage
From water bottles to canned goods, labeling machines ensure nutritional facts, barcodes, and branding are consistently displayed. - Pharmaceuticals & Healthcare
Labels often contain critical data such as dosage instructions, batch numbers, and expiration dates—precision and compliance are paramount. - Cosmetics & Personal Care
Eye-catching labels reflect a product’s brand identity, while clear ingredient lists meet regulatory requirements. - Chemical & Industrial
Durable labels that withstand harsh conditions—heat, moisture, chemicals—are essential for safety and regulatory compliance. - Logistics & Warehousing
Shipping labels, barcodes, and tracking IDs are critical for inventory management and supply chain tracking.
Each industry has its unique compliance standards and consumer expectations, but the universal need is for a reliable, high-throughput system that maintains top-notch accuracy.

Crucial Factors to Consider Before Buying
Investing in a sticker labeling machine is a big decision—one that can yield massive long-term rewards if you choose wisely. Here are key considerations to guide you:
- Production Volume
- Why it matters: Machines are often rated for specific speeds. Overloading a slower machine can lead to frequent downtime or mechanical issues.
- Pro Tip: Calculate peak production needs and add a buffer for future growth.
- Labeling Requirements
- Why it matters: Different products require various label placements (front, back, wrap-around) or specialized adhesives.
- Pro Tip: Make a list of all container shapes and label specifications you might use.
- Available Floor Space
- Why it matters: Some high-speed or multi-function machines have a large footprint.
- Pro Tip: Measure not just the space for the machine but also the loading/unloading areas.
- Budget & ROI
- Why it matters: Sticker labeling machines range from affordable semi-automatic units to high-end rotary systems that cost significantly more.
- Pro Tip: Estimate how quickly improved speed and accuracy will offset the investment cost.
- Ease of Use & Maintenance
- Why it matters: Complex machines with steep learning curves can require more staff training and risk operational errors.
- Pro Tip: Opt for user-friendly controls and request demonstration or training sessions from the manufacturer.
- Integration with Existing Line
- Why it matters: If you have other automated equipment (fillers, cappers, etc.), check compatibility to avoid production bottlenecks.
- Pro Tip: Involve your production engineers early to confirm the new machine can seamlessly tie into existing workflows.
- Reputation & Support
- Why it matters: Reputable manufacturers offer strong warranties, better customer support, and reliable spare parts availability.
- Pro Tip: Consult industry peers and online reviews, and consider scheduling a factory acceptance test (FAT).
Selecting the right equipment from the start can save you from headaches, extra costs, and production delays further down the line.
Maintenance & Best Practices for Longevity
Once you’ve chosen your sticker labeling machine, preserving its performance is largely about diligent upkeep. A well-maintained machine can remain productive for years, significantly boosting your return on investment.
- Regular Cleaning
- What to do: Clear any adhesive residue on rollers, brushes, or conveyor belts.
- Why it helps: Residue buildup can cause uneven label application or mechanical wear.
- Lubrication of Moving Parts
- What to do: Follow the manufacturer’s guidelines for lubrication schedules and oil specifications.
- Why it helps: Proper lubrication minimizes friction, reducing machine stress and breakdowns.
- Routine Checks on Sensors & Electronics
- What to do: Inspect sensors for dust or misalignment, and ensure cables are intact.
- Why it helps: Faulty sensors lead to misfeeds, double labeling, or halts in production.
- Replace Worn Parts Promptly
- What to do: Keep spare rollers, belts, or labeling heads on hand.
- Why it helps: Prompt part replacement avoids extended downtime, which can be costly in high-production settings.
- Document & Schedule Maintenance
- What to do: Keep a log of all maintenance activities, including cleaning, checks, and part replacements.
- Why it helps: An organized record helps identify recurring issues and ensures routine tasks aren’t overlooked.
- Operator Training
- What to do: Provide continuous education on new settings or updates.
- Why it helps: Skilled operators can quickly spot irregularities and handle minor adjustments without requiring a service call.
Combining these best practices with a well-thought-out maintenance schedule is the easiest way to keep your sticker labeling machine running smoothly at optimal capacity.
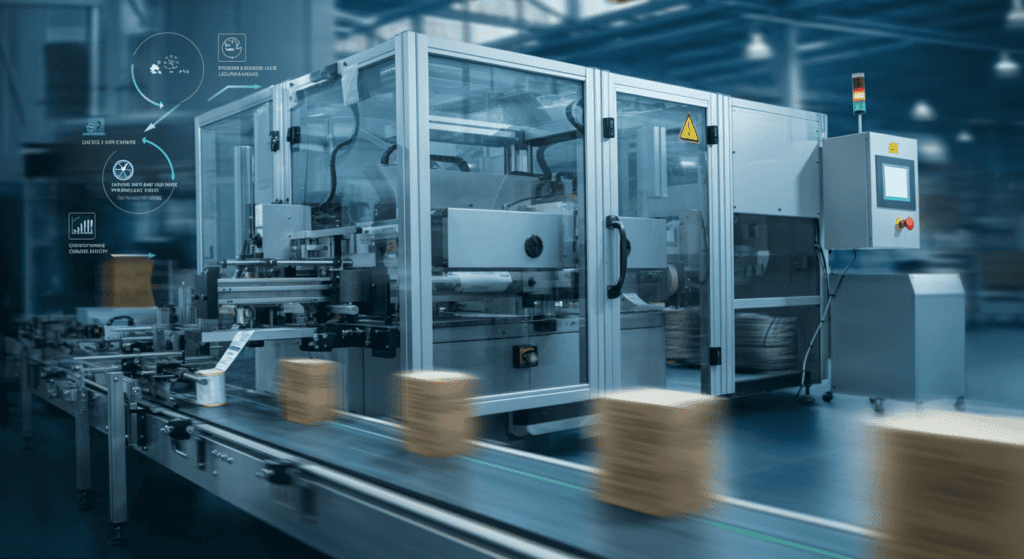
Troubleshooting Common Issues
Even the most advanced equipment can face hiccups. Below are some common issues you might encounter and quick solutions to get back on track:
- Label Misalignment
- Possible Cause: Sensor miscalibration or conveyor speed mismatch.
- Solution: Recalibrate sensors according to the manufacturer’s manual and ensure conveyor speed settings match label feed rate.
- Wrinkled or Bubbled Labels
- Possible Cause: Inconsistent tension on label roll or dirty rollers.
- Solution: Check tension control settings and clean any adhesive residue from rollers.
- Labels Not Sticking
- Possible Cause: Low-quality adhesive or dirty product surface.
- Solution: Switch to a better-quality label stock or ensure product surfaces are dry and free of dust or oil.
- Frequent Jams
- Possible Cause: Improper label roll placement or alignment issues.
- Solution: Reload the label roll carefully and check for correct alignment. Inspect sensors for dirt or obstruction.
- Machine Stopping Abruptly
- Possible Cause: Sensor or PLC error triggered by a product jam or misfeed.
- Solution: Identify the jammed product, remove it safely, and reset the system. If errors persist, consult the manufacturer.
A routine approach to maintenance, paired with an understanding of common fixes, can drastically reduce downtime and ensure your labeling line functions at peak efficiency.
FAQs on Sticker Labeling Machines
Below are some frequently asked questions to help you navigate any uncertainties about sticker labeling machines:
Q1: Can a sticker labeling machine handle multiple product shapes?
Absolutely. Many machines feature adjustable settings and modular parts like wrap belts, stabilizing plates, or rollers that can adapt to different shapes—cylindrical, rectangular, tapered, and more. Always confirm these capabilities before purchase.
Q2: Is a sticker labeling machine difficult to operate?
Most modern machines feature intuitive control panels and pre-programmed settings for various label types. With a brief training session, most operators can handle daily tasks like label roll changes, sensor adjustments, and minor troubleshooting.
Q3: What kind of labels can I use?
Sticker labeling machines generally work with pressure-sensitive labels, including paper, film, foil, or clear labels. Make sure the machine’s specifications match the thickness, width, and core diameter of the label rolls you plan to use.
Q4: How often should I perform maintenance?
While this can vary based on production volumes and environmental conditions, a weekly light cleaning and a more comprehensive monthly check can be a good baseline. Refer to your machine’s manual for specific intervals.
Q5: How do I ensure compliance with international labeling regulations?
Research the regulatory requirements for your target market—such as FDA guidelines, EU regulations, or country-specific mandates—and design your labels accordingly. Many businesses consult labeling experts or legal advisors for specialized guidance, especially when dealing with multiple international markets.
Conclusion
From faster turnarounds to flawless product presentation, the sticker labeling machine has emerged as an essential tool for businesses aiming to scale efficiently and maintain a polished brand image. By automating the label application process, companies can minimize human error, meet regulatory demands, and ultimately enhance overall production performance. Whether you’re in the food, pharmaceutical, cosmetic, or industrial sector, investing in the right machine can pay off in spades—through improved product consistency, higher output, and a stronger brand presence.
If you’ve been on the fence about upgrading your labeling process, now is the perfect time to explore the sticker labeling machine options that best align with your production needs. Ready to elevate your labeling game and set your products apart? We invite you to take the next step—explore reputable manufacturers, read in-depth reviews, and consult with industry experts. Don’t hesitate to drop a comment below with your questions or share your experiences. Spread the word on social media if you found this article helpful, and feel free to check out our other resources for more insights on optimizing your packaging and production line.
External References
- U.S. Food & Drug Administration (FDA) – Labeling & Nutrition
- ISO – Label Standards
- Packaging World Magazine
Stay Connected with EngiTech
EngiTech is your trusted source for in-depth knowledge on industrial mechanical engineering machines and technologies. Stay ahead with the latest innovations, expert insights, and practical guides designed to help you make informed decisions for your business and engineering needs. Join our growing community of professionals and industry leaders to stay updated and competitive in the ever-evolving world of industrial technology.