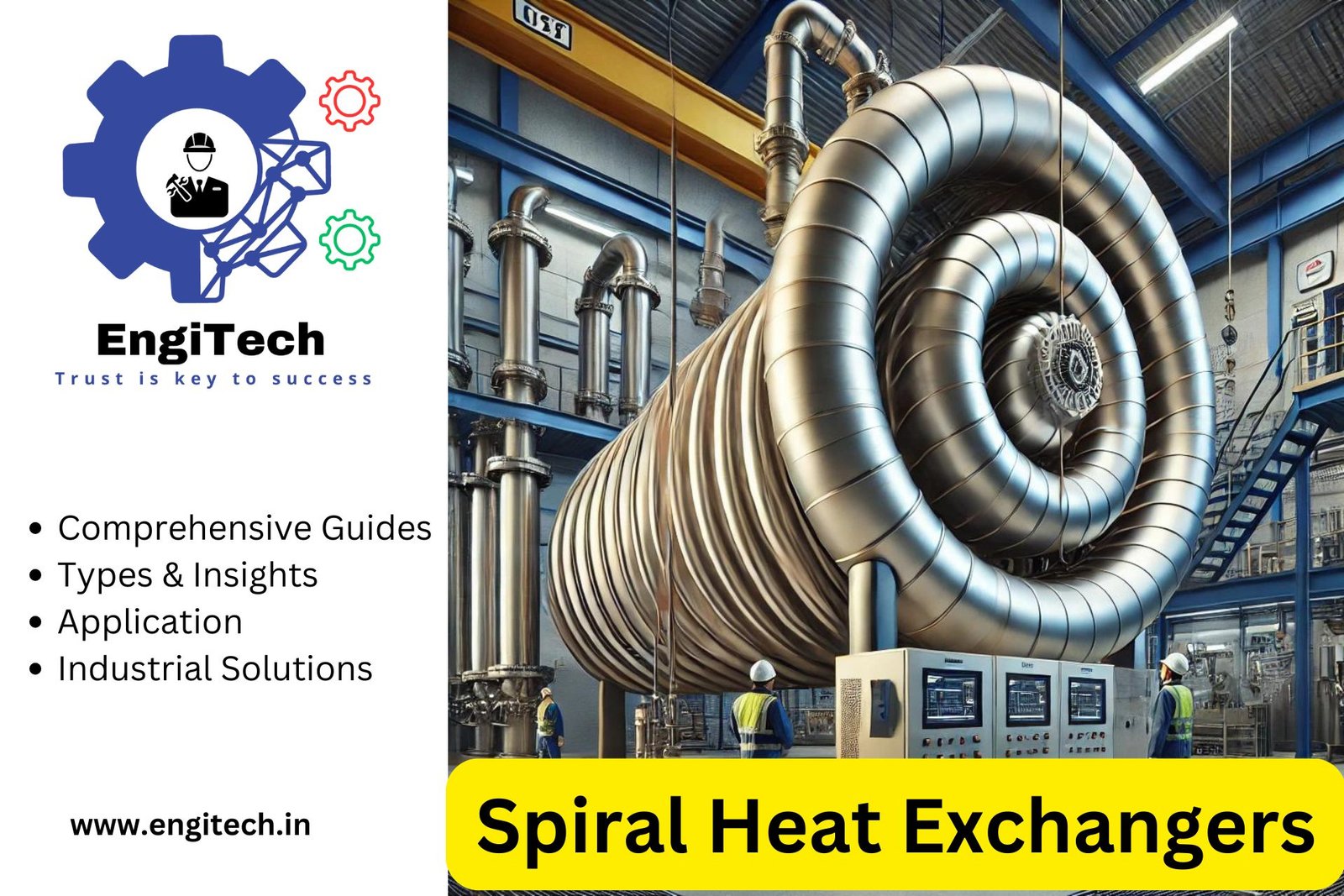
Spiral heat exchangers are innovative devices designed for efficient heat transfer in various industrial applications. Their unique spiral design offers numerous advantages over traditional heat exchangers, making them an excellent choice for industries seeking to optimize their thermal processes.
This comprehensive guide delves into the design, working principles, types, applications, advantages, and maintenance of spiral heat exchangers. By understanding these aspects, industry professionals and knowledge seekers can better appreciate the role spiral heat exchangers play in enhancing process efficiency.
Table of Contents
Introduction to Spiral Heat Exchangers
Spiral heat exchangers are characterized by their unique construction, which consists of two flat surfaces wound into a spiral shape. This design creates a continuous flow channel for each fluid, allowing for efficient heat transfer between the two streams. The spiral configuration promotes turbulence and minimizes fouling, enhancing the overall performance of the heat exchanger.
Design and Components of Spiral Heat Exchangers
The typical design of a spiral heat exchanger includes several key components:
- Spiral Channels: Two metal strips are wound around a central core, forming two separate spiral flow channels. Each channel carries one of the fluids, ensuring efficient heat exchange between the two streams.
- Core and Shell: The spiral channels are enclosed within a cylindrical shell, which provides structural support and protects the heat exchanger from external damage.
- Inlet and Outlet Ports: These ports are located at the ends of the spiral channels, allowing the fluids to enter and exit the heat exchanger.
- Baffles and Spacers: Baffles and spacers are used to maintain the spacing between the spiral channels, ensuring uniform flow distribution and preventing channel collapse.
Working Principles of Spiral Heat Exchangers
The working principle of a spiral heat exchanger is based on the counterflow arrangement of the fluids. In a counterflow setup, the hot and cold fluids flow in opposite directions, maximizing the temperature gradient and enhancing heat transfer efficiency. This arrangement ensures that the temperature difference between the fluids is maintained along the entire length of the spiral channels.
Heat Transfer Mechanism
The heat transfer process in a spiral heat exchanger involves three key mechanisms:
- Conduction: Heat is transferred through the walls of the spiral channels as the hot fluid flows along one side and the cold fluid flows along the other side.
- Convection: Both fluids transfer heat to and from the channel walls through convective heat transfer, driven by fluid motion.
- Overall Heat Transfer: The combined effect of conduction and convection results in the overall heat transfer, which depends on the thermal properties of the fluids, flow rates, and temperature differences.
Types of Spiral Heat Exchangers
Spiral heat exchangers come in various types, each designed for specific operational requirements and applications. The main types include:
Type 1: Both Fluids in Spiral Flow
In this configuration, both fluids flow through the spiral channels. This type of spiral heat exchanger is suitable for applications where both fluids need to be heated or cooled simultaneously. The counterflow arrangement ensures maximum heat transfer efficiency.
Applications:
- Chemical processing
- Wastewater treatment
- Food and beverage industry
Type 2: One Fluid in Spiral Flow, One in Cross Flow
In this setup, one fluid flows through the spiral channels while the other fluid flows perpendicularly (cross flow) to the spiral flow. This configuration is ideal for applications where one fluid needs to be heated or cooled more efficiently than the other.
Applications:
- Heat recovery systems
- HVAC systems
- Oil and gas industry
Type 3: One Fluid in Spiral Flow, One in Shell Flow
In this configuration, one fluid flows through the spiral channels while the other fluid flows through the shell surrounding the spiral. This design is suitable for applications involving fluids with significantly different flow rates or thermal properties.
Applications:
- Power generation
- Petrochemical industry
- Pharmaceuticals
Applications of Spiral Heat Exchangers
Spiral heat exchangers are versatile and find applications in a wide range of industries due to their efficient heat transfer capabilities and adaptability. Some common applications include:
1. Chemical Processing
In chemical processing, spiral heat exchangers are used for heating, cooling, and condensing chemical mixtures. Their ability to handle high viscosities and fouling fluids makes them suitable for various chemical reactions and processes.
2. Wastewater Treatment
The wastewater treatment industry utilizes spiral heat exchangers for recovering heat from effluents and treating sludge. Their compact design and high efficiency make them ideal for treating large volumes of wastewater.
3. Food and Beverage Industry
Spiral heat exchangers are extensively used in the food and beverage industry for pasteurization, sterilization, and cooling of products. Their hygienic design and ease of cleaning make them ideal for handling food products.
4. HVAC Systems
In HVAC systems, spiral heat exchangers are used for heating and cooling air and water. They provide efficient heat transfer solutions for air conditioning units, heat pumps, and other HVAC applications.
5. Oil and Gas Industry
The oil and gas industry uses spiral heat exchangers for cooling and heating process fluids, recovering heat from flue gases, and condensing vapors. Their robust design and high-pressure handling capabilities make them ideal for harsh operating conditions.
6. Power Generation
In power plants, spiral heat exchangers are used for heat recovery, cooling, and condensing. They help improve the efficiency of power generation processes by transferring heat from one medium to another, often using waste heat for energy recovery.
Advantages of Spiral Heat Exchangers
Spiral heat exchangers offer several advantages that make them a preferred choice in many industries:
1. High Efficiency
The counterflow design in spiral heat exchangers maximizes the temperature gradient, leading to high heat transfer efficiency. This design ensures that the fluids are effectively heated or cooled as they pass through the exchanger.
2. Compact Design
Spiral heat exchangers have a compact and space-saving design, making them suitable for installations with limited space. Their spiral configuration allows for a larger heat transfer area within a smaller footprint.
3. Fouling Resistance
The spiral design promotes turbulence, which minimizes fouling and reduces the need for frequent cleaning. This feature is particularly beneficial for applications involving dirty or viscous fluids.
4. Ease of Maintenance
The straightforward design of spiral heat exchangers makes them easy to maintain. The channels can be easily accessed for cleaning, inspection, and maintenance, reducing downtime and maintenance costs.
5. Versatility
Spiral heat exchangers are versatile and can handle a wide range of fluids, including corrosive, viscous, and fouling fluids. Their adaptability makes them suitable for various industrial applications.
6. Cost-Effectiveness
Spiral heat exchangers are cost-effective due to their high efficiency, compact design, and lower maintenance requirements. They offer a lower total cost of ownership compared to other heat exchanger types.
Maintenance and Troubleshooting of Spiral Heat Exchangers
Proper maintenance of spiral heat exchangers is essential to ensure optimal performance and longevity. Regular inspections, cleaning, and monitoring can prevent common issues and extend the life of the equipment.
1. Inspection
Routine inspections help identify signs of wear, corrosion, or damage. Operators should check for leaks, inspect the condition of the channels, and ensure that the inlet and outlet ports are secure. Early detection of issues can prevent more significant problems and costly downtime.
2. Cleaning
Cleaning is crucial to prevent fouling and maintain heat transfer efficiency. Depending on the application, operators can use chemical cleaning, mechanical cleaning, or a combination of both. The channels should be regularly cleaned to remove any deposits or contaminants that may impede heat transfer.
3. Gasket Replacement
For spiral heat exchangers with gaskets, regular inspection and replacement of gaskets are necessary to ensure a proper seal and prevent leaks. Gaskets may degrade over time due to chemical exposure, temperature fluctuations, or mechanical stress.
4. Channel Replacement
In cases where the channels are damaged or corroded, replacing them is necessary to maintain performance. Operators should ensure that replacement channels are compatible with the existing system and materials of construction.
5. Troubleshooting Common Issues
Operators may encounter common issues such as leaks, reduced heat transfer efficiency, or pressure drops. Addressing these issues promptly requires identifying the root cause, which could involve inspecting gaskets, cleaning the channels, or checking for mechanical damage.
Technological Advancements in Spiral Heat Exchangers
Technological advancements continue to enhance the performance and capabilities of spiral heat exchangers. Innovations in materials, design, and manufacturing processes have led to the development of more efficient and reliable spiral heat exchangers.
1. Advanced Materials
The use of advanced materials such as high-performance alloys and specialized coatings has improved the corrosion resistance and durability of spiral heat exchangers. These materials are particularly beneficial in applications involving aggressive chemicals or high temperatures.
2. Enhanced Channel Designs
Innovations in channel design, such as optimized corrugation patterns and microchannel structures, have increased heat transfer efficiency and reduced pressure drops. These designs promote better fluid distribution and minimize dead zones.
3. Compact and Lightweight Designs
Efforts to reduce the size and weight of spiral heat exchangers have resulted in more compact and lightweight models. These designs are ideal for applications with space constraints or where weight is a critical factor.
4. Automation and Control
The integration of automation and control systems allows for real-time monitoring and optimization of spiral heat exchanger performance. Advanced sensors and control algorithms help maintain optimal operating conditions, improving efficiency and reducing energy consumption.
5. 3D Printing and Additive Manufacturing
3D printing and additive manufacturing technologies have enabled the production of complex channel designs with high precision. These technologies allow for customized solutions and rapid prototyping, accelerating the development of new spiral heat exchanger models.
Conclusion
Spiral heat exchangers are essential components in various industries, offering efficient heat transfer solutions in a compact and versatile design. Their ability to handle high viscosities, fouling fluids, and wide temperature ranges makes them ideal for applications in chemical processing, wastewater treatment, food and beverage, HVAC systems, oil and gas, and power generation.
With ongoing technological advancements and a growing focus on energy efficiency and sustainability, spiral heat exchangers will continue to play a vital role in industrial processes. As industries evolve and new challenges arise, spiral heat exchangers will adapt and innovate, providing reliable and efficient solutions for years to come.
FAQs About Spiral Heat Exchangers
1. What is a spiral heat exchanger?
A spiral heat exchanger is a type of heat exchanger that uses two metal strips wound into a spiral shape, creating two separate flow channels. This design allows efficient heat transfer between two fluids, promoting turbulence and minimizing fouling.
2. How does a spiral heat exchanger work?
A spiral heat exchanger works by directing two fluids through separate spiral channels in a counterflow arrangement. The fluids flow in opposite directions, maximizing the temperature gradient and enhancing heat transfer efficiency.
3. What are the advantages of using a spiral heat exchanger?
Spiral heat exchangers offer high efficiency, compact design, fouling resistance, ease of maintenance, versatility, and cost-effectiveness. Their spiral configuration allows for efficient heat transfer and reduces the need for frequent cleaning.
4. Where are spiral heat exchangers commonly used?
Spiral heat exchangers are used in various industries, including chemical processing, wastewater treatment, food and beverage, HVAC systems, oil and gas, and power generation. They are ideal for applications requiring efficient heat transfer and handling of fouling fluids.
5. What are the different types of spiral heat exchangers?
The main types of spiral heat exchangers include:
- Type 1: Both fluids in spiral flow
- Type 2: One fluid in spiral flow, one in cross flow
- Type 3: One fluid in spiral flow, one in shell flow
Each type is designed for specific operational requirements and applications.
6. How do you maintain a spiral heat exchanger?
Maintenance of a spiral heat exchanger involves regular inspection, cleaning, gasket replacement, and troubleshooting. Routine maintenance ensures optimal performance and longevity, preventing issues such as fouling, leaks, and reduced efficiency.
7. What materials are used in spiral heat exchangers?
Manufacturers typically use metals like stainless steel, high-performance alloys, and specialized coatings for spiral heat exchangers. These materials offer excellent thermal conductivity, corrosion resistance, and durability.
8. How does the spiral design improve heat transfer efficiency?
The spiral design promotes turbulence, which enhances heat transfer by maintaining a high-temperature gradient along the channels. This design also reduces the likelihood of fouling, ensuring consistent performance.
9. Can spiral heat exchangers handle high-pressure fluids?
Yes, spiral heat exchangers are designed to handle high-pressure fluids. Their robust construction makes them suitable for applications involving high-pressure processes and aggressive chemicals.
10. Why choose a spiral heat exchanger over other types?
Spiral heat exchangers are preferred for their high efficiency, compact design, fouling resistance, ease of maintenance, and versatility. They are particularly suitable for applications involving dirty or viscous fluids.
11. What technological advancements have improved spiral heat exchangers?
Technological advancements include the use of advanced materials, enhanced channel designs, compact and lightweight models, automation and control systems, and 3D printing for complex channel designs. These innovations improve efficiency, durability, and customization.
12. How do spiral heat exchangers contribute to energy efficiency and sustainability?
Spiral heat exchangers improve energy efficiency by maximizing heat transfer and reducing energy consumption. They can be integrated with renewable energy systems, offering sustainable heating and cooling solutions.
These FAQs address common queries and provide essential information about spiral heat exchangers, helping users understand their functionality, benefits, and maintenance requirements.
Welcome to EngiTech, your premier resource for cutting-edge industrial engineering solutions. At EngiTech.in, we are committed to empowering professionals with expert insights and the latest advancements in industrial technologies. Our comprehensive guides and articles cover a wide range of topics, including heat exchangers, HVAC systems, renewable energy solutions, and advanced manufacturing techniques.
Our team of industry experts and seasoned engineers ensures that every piece of content is accurate, practical, and designed to enhance your operational efficiency. Join our growing community of industry leaders and stay ahead of the curve with EngiTech.in—where innovation meets expertise. Explore our content today and transform your industrial processes with knowledge-driven solutions.