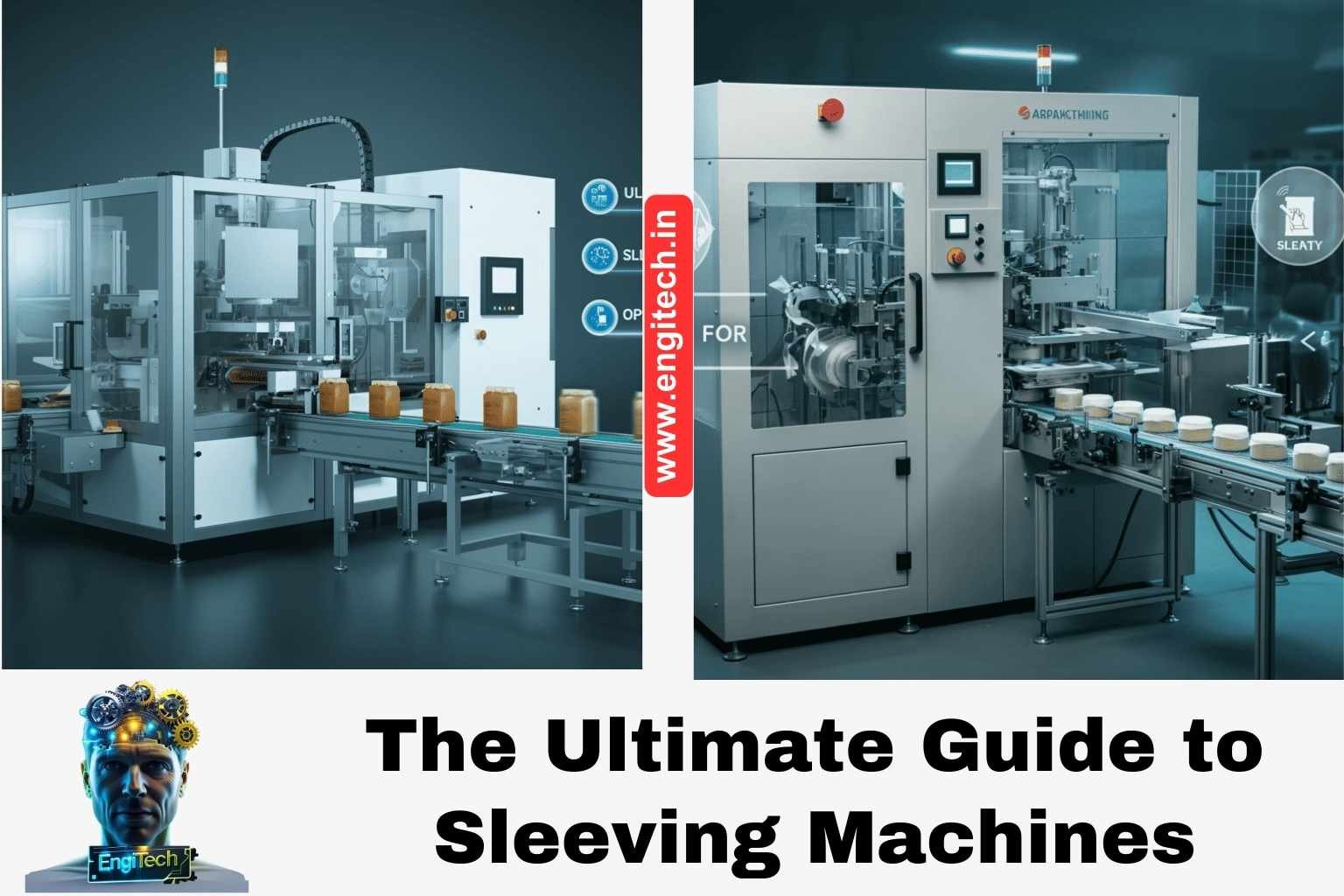
Imagine you’re walking down a supermarket aisle and your eyes land on a sleek bottle with a vibrant, full-body label that looks more like artwork than just product information. If you’ve ever wondered how these clean, uniform labels are applied so perfectly, you’re about to find out. The sleeving machine lies at the heart of this modern packaging marvel.
Over the next several sections, we’ll dive into every facet of this technology. From the basic mechanics behind sleeving to advanced features and maintenance routines, this comprehensive article will give you actionable insights to streamline your packaging line. By the time you finish, you’ll know exactly how to choose the right sleeving machine for your needs, optimize it for peak performance, and stay ahead of the competition. Buckle up—this is about to be the most thorough guide you’ll find online.
Table of Contents
What Is a Sleeving Machine?
Definition and Core Purpose
A sleeving machine is specialized equipment designed to apply a thin plastic or polymer “sleeve” around a container, product, or bundle of items. This sleeve often shrinks (via heat) or stretches to conform tightly to the shape it covers. In many cases, these sleeves are printed with brand logos, nutritional information, or eye-catching graphics. The result is a seamless, 360-degree label that enhances the product’s visual appeal and brand identity.
A Brief History of Sleeving Technology
While traditional labels have existed for centuries, full-body shrink-sleeve technology gained momentum in the late 20th century. Pioneered by innovations in polymer science and printing techniques, early sleeving machines were large, complex systems mostly reserved for high-end manufacturers. As technology advanced, these machines became more compact, versatile, and user-friendly, allowing smaller businesses to tap into their benefits. Today, sleeving is standard in a variety of industries, including food and beverage, cosmetics, pharmaceuticals, and household products.
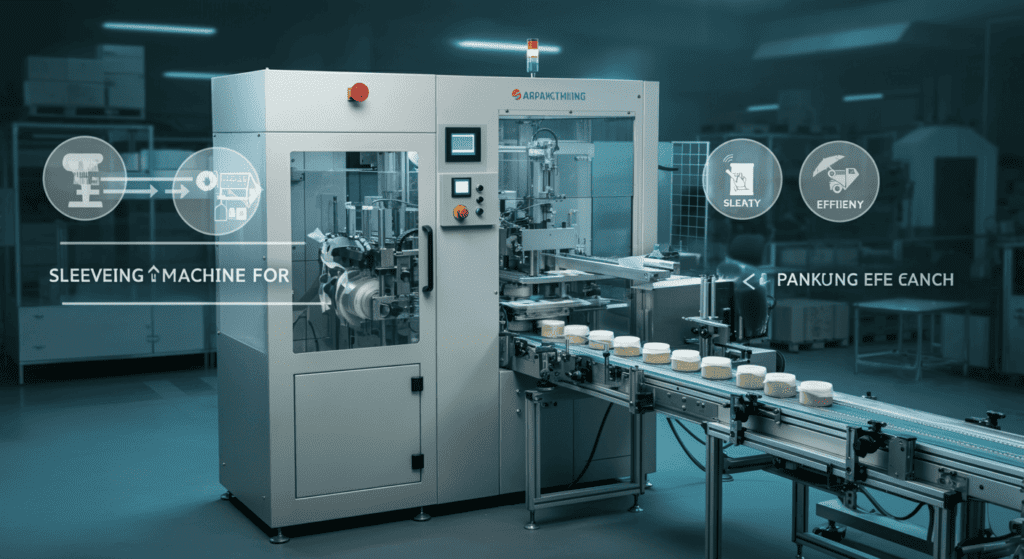
Why Sleeving Machines Are Essential in Modern Packaging
Enhanced Shelf Appeal
In a world saturated with product choices, the first impression on the shelf matters immensely. Sleeving machines create a polished, full-coverage appearance that helps products stand out in crowded retail environments. This visual “wow factor” can be the deciding factor for consumers making quick purchasing decisions.
Versatile Labeling Options
Sleeving machines accommodate different container shapes—cylindrical, rectangular, or contoured. Whether you’re packaging a straight-sided energy drink can or an hourglass-shaped shampoo bottle, a sleeving machine can handle it. With minimal adjustments, you can manage various product lines on the same piece of equipment.
Tamper-Evident Security
Safety and trustworthiness are crucial, especially for food, beverage, and pharmaceutical products. Full or partial shrink sleeves can also serve as tamper-evident seals. Any attempt to remove or break the sleeve becomes immediately noticeable. This feature boosts consumer confidence and meets strict regulatory guidelines.
Sustainability Potential
Many modern sleeve materials are recyclable or biodegradable. Coupled with decreasing material thickness and improved production efficiency, using a sleeving machine can help companies reduce waste and meet eco-friendly goals. Some manufacturers are even exploring PLA (polylactic acid) sleeves derived from renewable resources like corn starch.
Types of Sleeving Machines
Not all sleeving machines are built the same. They come in various configurations to handle specific production needs and packaging formats. Here are some of the most common types:
- Shrink Sleeve Applicators
- Uses heat tunnels to shrink the sleeve around a container.
- Ideal for a tight, contoured fit.
- Common in beverages and personal care items.
- Stretch Sleeve Applicators
- Relies on the elasticity of the film to wrap snugly around the product.
- No heat application needed.
- Popular for large containers or irregular shapes.
- Combo Applicators
- Offers both shrink and stretch capabilities in one machine.
- Useful for manufacturers handling multiple product types.
- Tamper-Evident Band Applicators
- Specially designed to apply a small band around a bottle cap or container opening.
- Common in pharmaceuticals and food packaging requiring sealed protection.
- Fully Automated Inline Systems
- Integrates seamlessly with conveyor lines for continuous high-speed operations.
- Best for large-scale manufacturers with significant output demands.
Key Components of a High-Performance Sleeving Machine
Film Unwind and Tension Control
In many designs, the sleeving film is stored on a roll. A smooth unwind system ensures the film isn’t stressed or creased before application. Tension control mechanisms keep the sleeve material taut yet flexible enough to be formed correctly.
Cutting or Perforation System
After the film is placed around the container, it often needs a precise cut or perforation. This operation demands accuracy to avoid misalignment that can ruin the final appearance or impede tamper-evident features.
Heat Tunnel or Steam Tunnel
In shrink-sleeve applications, a heat or steam tunnel applies controlled heat to shrink the film around the container. Temperature uniformity and dwell time are crucial: too little heat leaves wrinkles; too much can melt the film or distort printed graphics.
Conveyor and Container Handling
Most sleeving machines have integrated conveyors to move containers through different stations—film application, cutting, and heat tunnel. Some advanced machines use sensors and servo motors to adapt speed automatically, ensuring consistent sleeve placement even during rapid production changes.
Safety and Control Systems
A robust machine includes safety interlocks, emergency stops, and sensor-based controls. Touchscreen interfaces are common, allowing operators to adjust speed, temperature, and other parameters swiftly. Automated alerts let you know when the film roll is low or if a jam occurs, minimizing downtime.
How to Choose the Right Sleeving Machine
1. Production Speed Requirements
If your line runs thousands of units per hour, opt for a fully automated machine. For smaller or niche product lines, a semi-automated or manual system may suffice.
2. Container Shapes and Sizes
Evaluate the range of containers you need to sleeve. A versatile machine capable of handling various shapes and sizes prevents future limitations.
3. Type of Sleeve Material
Are you using shrink, stretch, or tamper-evident bands? Some machines are specialized for a particular sleeve type. Verify machine compatibility before purchasing.
4. Budget vs. ROI
Cost is always a factor, but consider the long-term return on investment. A cheaper machine might lead to higher maintenance costs and more frequent downtime. Sometimes, investing in a more advanced system pays off in the long run.
5. Maintenance and Technical Support
Reputable suppliers offer not just hardware but also after-sales service, training, and readily available spare parts. Investigate the supplier’s service record before committing.
Step-by-Step Process: How a Sleeving Machine Operates
Mastering the sleeving process can seem daunting at first. Here’s a simplified breakdown:
- Container Infeed
Containers arrive via conveyor. Sensors detect each container and trigger the sleeving cycle. - Film Forming
The film is unrolled, shaped into a tube, and cut or perforated to match the container’s height. - Sleeve Application
The container passes through a station where the sleeve is placed over it. Sometimes, an air-jet or mechanical device ensures the sleeve slides neatly over the container. - Heat or Stretch Process
- Shrink Sleeve: The container enters a heat tunnel, where hot air or steam shrinks the sleeve.
- Stretch Sleeve: The sleeve is stretched over the container without heat, relying on elastic properties.
- Output and Inspection
The newly sleeved container exits for quality checks—verifying sleeve alignment, checking for wrinkles or tears. Some lines use machine vision systems to automatically reject flawed items. - Labeling or Secondary Packaging
If additional labels or packaging steps are required (like placing products into boxes), these occur downstream.
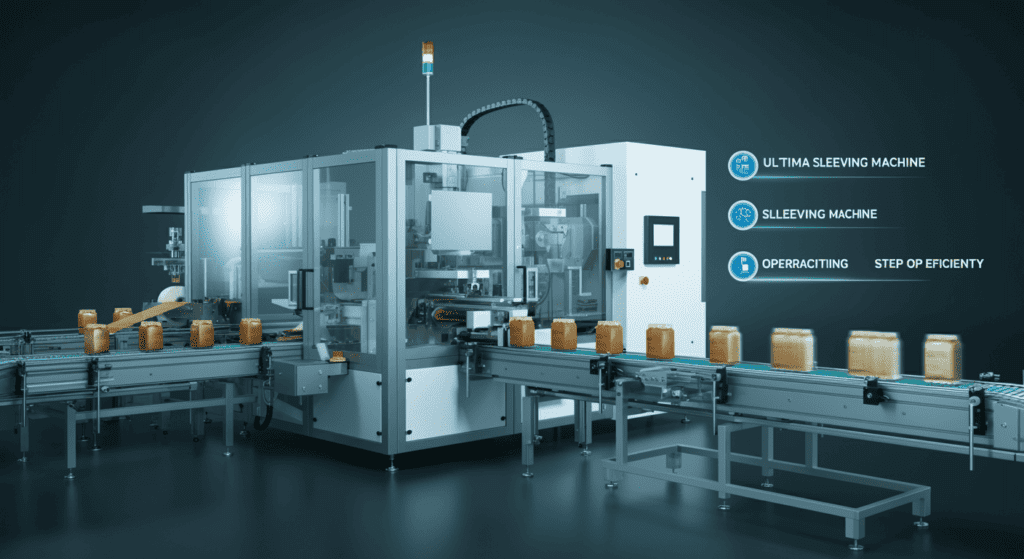
Maintenance and Best Practices for Longevity
Routine Inspections
Regularly inspect key components—belts, gears, blades, or heaters. Catching small issues early (like wear on a cutting blade) saves time and money down the line.
Proper Lubrication and Cleaning
Dirt buildup and friction can degrade performance. Implement a scheduled cleaning regimen with specialized detergents that don’t harm rubber or plastic parts.
Employee Training
No machine is foolproof without skilled operators. Regular training ensures staff can identify problems, perform routine checks, and optimize machine settings for maximum efficiency.
Calibration and Software Updates
Modern sleeving machines often include advanced electronics. Keep software and firmware updated to benefit from improvements in accuracy and reliability. Schedule periodic calibrations to maintain cutting-edge performance.
Emergency Preparedness
Things occasionally go wrong—a sudden jam or power outage can occur at any time. Ensure you have backup parts, accessible emergency stops, and a clear troubleshooting guide. A robust contingency plan minimizes production downtime and prevents accidents.
Sleeving Machine Innovations & Future Trends
1. Eco-Friendly Films
As consumer demand for sustainable packaging grows, manufacturers are developing thinner films and experimenting with biodegradable materials like PLA. The goal is to reduce plastic usage without compromising label durability or visual appeal.
2. Digital Printing Integration
Advancements in digital printing let companies produce full-color, custom sleeves on-demand. Personalized campaigns—like putting a customer’s name on a bottle—are more feasible and cost-effective than ever.
3. Automated Quality Control
State-of-the-art systems now incorporate cameras and sensors for real-time sleeve inspection. These detect misalignments, color inaccuracies, or tears, automatically ejecting defective products to maintain quality.
4. Augmented Reality (AR) Maintenance
Some machine manufacturers are experimenting with AR glasses and apps to guide technicians through repairs. This trend enhances troubleshooting efficiency, reducing operational downtime.
5. Industry 4.0 and IoT
With IoT (Internet of Things) integration, sleeving machines can send performance data to cloud-based dashboards, enabling remote monitoring and predictive maintenance. Machine learning algorithms analyze data to predict failures before they happen.
Real-World Case Studies: Sleeving Machines in Action
Beverage Industry Example
A mid-sized craft beverage company in the Pacific Northwest struggled to make its bottles stand out against national brands. They invested in a shrink-sleeve machine capable of applying full-body, high-definition sleeves. Within months, their eye-catching labels boosted brand recognition and sales jumped by nearly 20%. The cost-per-unit decreased, thanks to efficiency gains and fewer labeling errors.
Personal Care Products
An organic skincare startup wanted to highlight its eco-friendly ethos by using biodegradable films. They chose a stretch-sleeve machine that reduced energy consumption since it needed no heat tunnels. Despite initial skepticism about how well the sleeves would hold up, the brand reported zero tears or slippage during shipping and retail display. Customer feedback praised the packaging design, and retailers took note, offering prime shelf placement.
Pharmaceutical Applications
A pharmaceutical plant integrated tamper-evident band applicators into their existing line to meet stringent safety regulations. The bands also displayed dosage instructions. This single step improved consumer trust, and regulatory audits became smoother, as inspectors could clearly see tamper-evident measures in place.
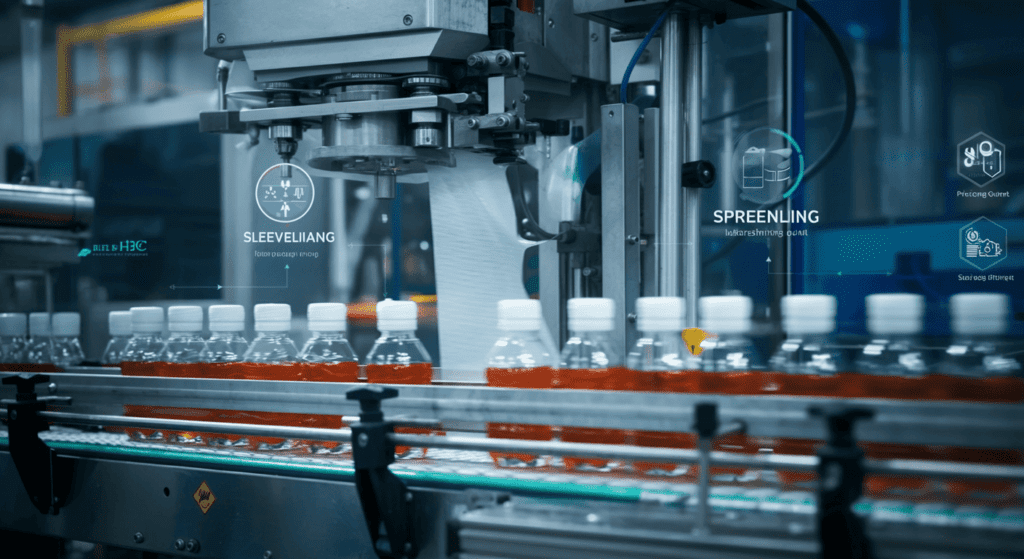
Frequently Asked Questions (FAQ)
Q1: What types of products can a sleeving machine handle?
A sleeving machine can handle a broad range of products, including food jars, beverage bottles, cosmetic containers, and even irregularly shaped pharmaceutical items. The key is choosing the right machine type—shrink, stretch, or tamper-evident—based on your product’s packaging needs.
Q2: Is a sleeving machine suitable for small-scale operations?
Absolutely. While some sleeving machines are designed for high-volume operations, there are smaller, semi-automated models perfect for limited runs or niche products. These machines can often be upgraded as your business grows.
Q3: How do I maintain quality control with sleeving?
Regular inspections, camera-based vision systems, and alignment sensors help maintain consistent quality. Training your staff to spot and rectify small issues early (like misalignments or film tension problems) can also go a long way.
Q4: Are sleeving materials environmentally friendly?
Many manufacturers offer recyclable or biodegradable options, and continuous innovations focus on reducing plastic usage. Always verify whether the material you choose aligns with local recycling regulations and your company’s sustainability goals.
Q5: What is the ROI timeline for investing in a sleeving machine?
Return on investment varies based on your production scale, the complexity of your machine, and your profit margins. Some companies recoup their investment within a year due to increased efficiency and reduced labeling waste, while others find the ROI timeline closer to two or three years.
External Reference Links:
- Packaging Machinery Manufacturers Institute (PMMI) – Industry insights, news, and technical data.
- Freedonia Group Research Reports – Data-driven packaging market forecasts and trends.
Conclusion
From bright, full-body wraps on energy drink cans to tamper-evident bands on pharmaceutical vials, sleeving machines are reshaping modern packaging—literally and figuratively. Throughout this comprehensive guide, we’ve covered the basics of what a sleeving machine is, examined the types and components, and even explored cutting-edge innovations like IoT integration and AR-based maintenance. By now, you should feel confident in your ability to make an informed decision that meets both your production needs and branding goals.
So, what’s your next step? If you’re eager to elevate your brand presence with professional, eye-catching sleeves, now’s the time to act. Talk to an industry expert, compare machine specifications, and request a live demonstration. You’ll quickly see how the right sleeving machine can transform your packaging line, reduce waste, and make your products stand out on the shelf. This is your chance to invest in a technology that not only appeals to consumers today but also sets you up for future success. Don’t let outdated labeling methods hold you back—start exploring your sleeving machine options now and watch your efficiency, brand image, and sales climb.
Stay Connected with EngiTech
EngiTech is your trusted source for in-depth knowledge on industrial mechanical engineering machines and technologies. Stay ahead with the latest innovations, expert insights, and practical guides designed to help you make informed decisions for your business and engineering needs. Join our growing community of professionals and industry leaders to stay updated and competitive in the ever-evolving world of industrial technology.