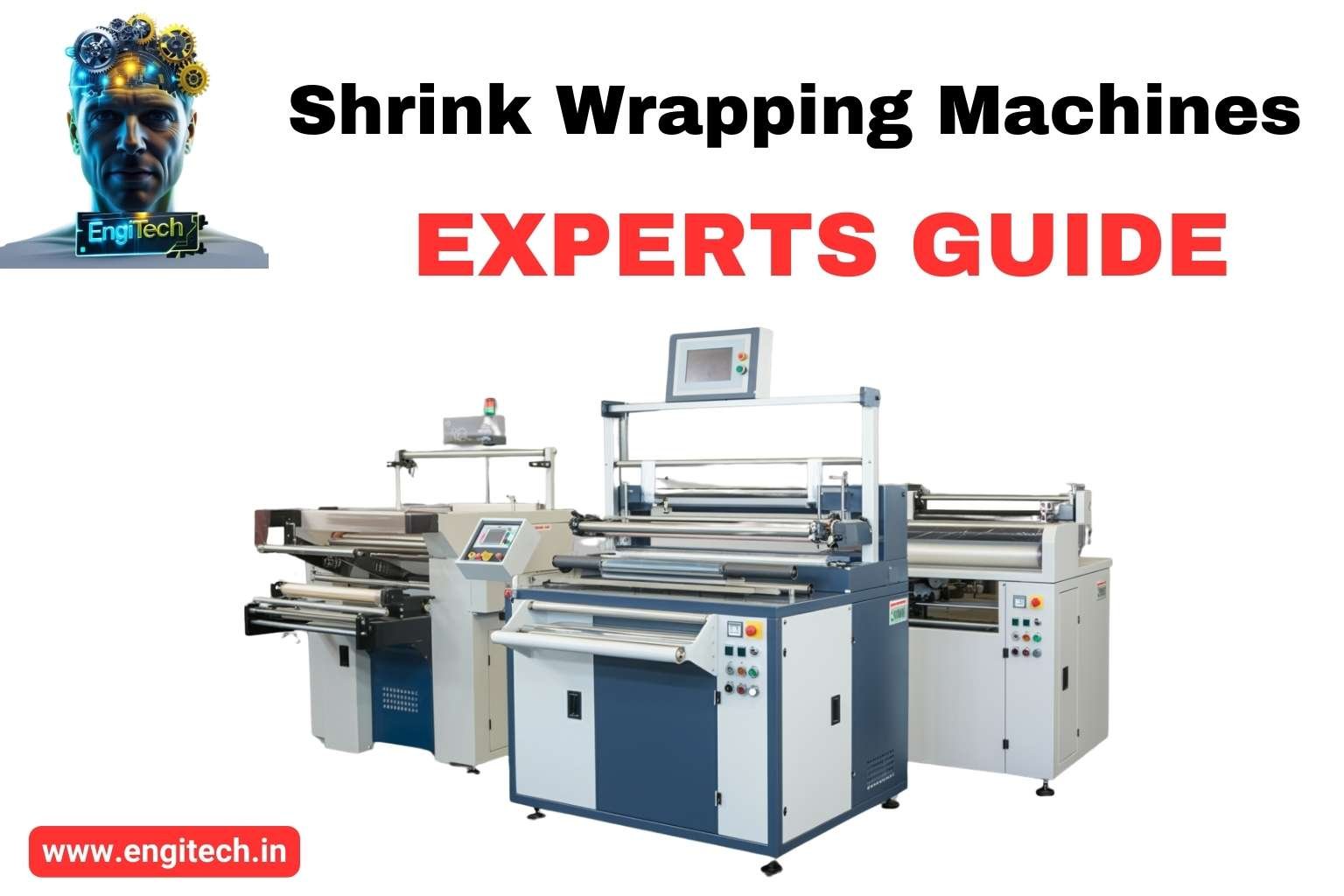
In today’s competitive marketplace, businesses across various industries are constantly seeking ways to protect and present their products in the most efficient, cost-effective manner possible. One solution that has rapidly gained popularity for its versatility and reliability is the shrink wrapping machine. This sophisticated equipment offers a secure, tamper-evident, and professional packaging method that can accommodate a wide range of items—from small bundles of stationery to large industrial components.
But what exactly is a shrink wrapping machine, and why is it so pivotal for modern packaging needs? In this comprehensive guide, we’ll dive deep into the inner workings of shrink wrapping technology, explore its benefits across different sectors, and provide actionable insights to help you determine which shrink wrapping machine is perfect for your specific operations. You’ll also learn best practices, frequently asked questions, and expert tips that will set you up for success.
Whether you’re completely new to packaging solutions or a seasoned professional looking to upgrade your processes, this article will serve as your one-stop resource. By the end, you’ll have a crystal-clear understanding of shrink wrapping machines, how they can enhance your packaging efficiency, and what you need to do to get started—ensuring you stay ahead of the competition in a rapidly evolving market.
Table of Contents
1. Introduction to Shrink Wrapping Machines
A shrink wrapping machine is specialized equipment designed to enclose a product within a shrink film—typically a polymer plastic—before applying heat to tighten the film snugly around the item. The result is a tamper-evident seal that provides both an appealing presentation and robust protection against dust, moisture, and other potential damage.
Why Shrink Wrapping?
- Professional Presentation: A well-shrunk wrap makes products look polished and store-ready.
- Cost Efficiency: The film used in shrink wrapping is generally affordable, and the process reduces the need for bulky packaging materials.
- Versatility: Shrink wrapping can handle an extensive range of product shapes and sizes.
- Security: The tight fit helps deter tampering and ensures products remain intact during transport.
The Rise of Shrink Wrapping Technology
Shrink wrapping technology has evolved significantly in the past few decades. Early machines were mostly manual, requiring operators to manually feed film and use handheld heat guns. Modern machinery now offers automated, semi-automated, or fully manual configurations, allowing businesses to choose a setup that aligns with their operational demands. With global packaging demands rising—especially in sectors like food and beverage, retail, and pharmaceuticals—shrink wrapping machines have become a mainstay for companies striving for efficient packaging solutions.
2. Core Benefits of Shrink Wrapping
Understanding the key advantages of shrink wrapping will help you appreciate why a shrink wrapping machine can be a game-changer for your packaging line.
- Enhanced Protection
Shrink film provides a protective barrier against dust, dirt, moisture, and even some forms of UV light. Once the film is heated and shrunk, it conforms tightly around the product, minimizing internal movement that could cause damage. - Cost Reduction
Unlike other packaging materials—such as cardboard boxes or large plastic clamshells—shrink film is relatively inexpensive. Additionally, it takes up less space in storage and reduces shipping volume. - Brand Visibility
Clear shrink film preserves visibility of the product’s design and labeling. Some industries opt for printed shrink film to bolster branding, but even using transparent film ensures the product itself remains the star attraction. - Tamper Evident
A shrink wrap serves as a clear indicator if the product has been tampered with. In industries like pharmaceuticals and food, this is a critical feature for consumer safety and brand integrity. - Versatility
You can shrink wrap virtually any shape or size. From small electronics to multi-packs of beverages, shrink wrapping machines can handle a diverse range of products efficiently.
3. Different Types of Shrink Wrapping Machines
While “shrink wrapping machine” is often used as a catch-all term, there are multiple categories to consider. Each type is suited to different production scales, product shapes, and packaging speeds. Below are some of the most common types:
- Manual Shrink Wrapping Machines
- Description: These machines require the operator to manually place products into the shrink film and use a heat source—like a heat gun—to shrink the film.
- Use Case: Low-volume operations or smaller businesses with budget constraints.
- Pros: Affordable initial cost, easy to operate.
- Cons: Lower throughput, higher labor involvement.
- Semi-Automatic Shrink Wrapping Machines
- Description: Semi-automatic machines use a conveyor system where the operator loads the product, and the machine automatically seals the film. A heat tunnel or similar heat chamber then shrinks the film.
- Use Case: Mid-volume production with moderate automation needs.
- Pros: Faster than manual systems, reduced human error, relatively cost-effective.
- Cons: Requires an operator for part of the process, might not meet extremely high-volume demands.
- Fully Automatic Shrink Wrapping Machines
- Description: Fully automated systems handle product feeding, film wrapping, sealing, and shrinking with minimal operator intervention.
- Use Case: High-volume operations that require constant, streamlined packaging. Common in large-scale manufacturing and distribution.
- Pros: Maximizes throughput, consistent packaging quality, minimal labor.
- Cons: Higher initial investment, more complex maintenance requirements.
- Specialty Shrink Wrapping Machines
- Description: Tailored to unique product configurations or specialized industries. Examples include machines for shrink-wrapping pallets or bundling irregularly shaped products.
- Use Case: Industries that require specialized packaging solutions, such as furniture, automotive parts, or large machinery components.
- Pros: Custom-fit for specific applications, high precision.
- Cons: Can be expensive and may require specialized technical support.
4. Key Components and How They Work
Regardless of whether you opt for a manual, semi-automatic, or fully automatic shrink wrapping machine, the core components remain fairly consistent:
- Film Roll Holder
- Holds the roll of shrink film (usually polyolefin, PVC, or polyethylene).
- Must allow easy changeovers and smooth film feeding.
- Sealing System
- Consists of a sealing bar or jaw that cuts and seals the film around the product.
- Often features adjustable temperature controls to accommodate different film types.
- Conveyor Belt
- Present in semi-automatic and fully automatic machines.
- Transports products from the sealing area to the heat tunnel.
- Heat Tunnel
- Applies hot air around the packaged product to shrink the film.
- Typically includes adjustable temperature settings, fan speeds, and conveyor speeds to optimize shrink quality.
- Cooling System
- Some machines include a cooling section after the heat tunnel, allowing the film to set quickly.
- Prevents products or the film from overheating.
- Operator Interface
- On automated machines, a control panel lets operators adjust temperature, conveyor speed, and sealing time.
- Modern interfaces may include touchscreens with advanced diagnostic features.
How It All Comes Together
- An operator (or automated mechanism) places the product on the infeed conveyor.
- The film is fed over or around the product.
- The sealing system trims and seals the film.
- The product moves through the heat tunnel, causing the film to shrink tightly.
- The product may pass through a cooling section before being discharged from the machine.
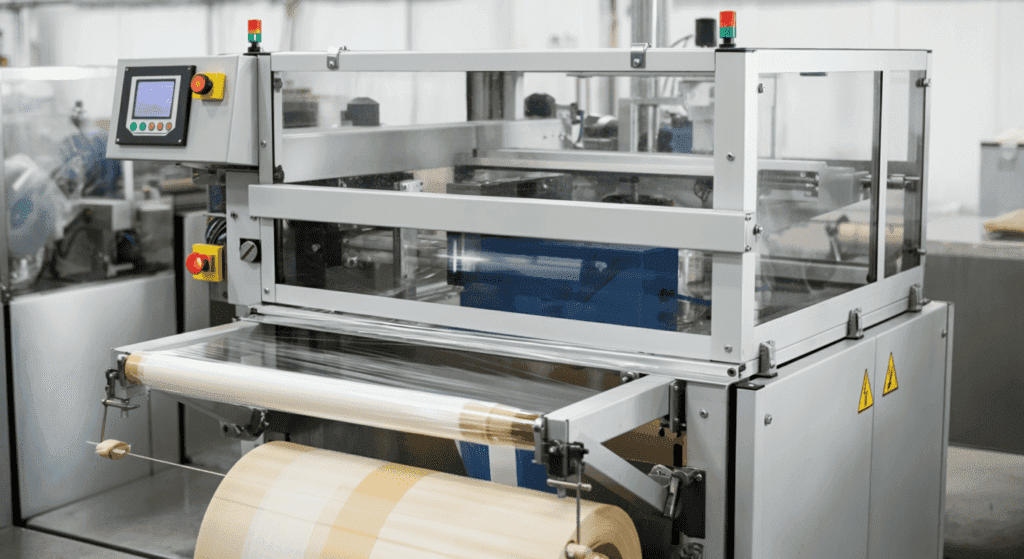
5. Step-by-Step: How to Use a Shrink Wrapping Machine
The exact steps vary depending on whether you have a manual, semi-automatic, or fully automatic system. Below is a general workflow for a semi-automatic shrink wrapping machine:
- Load the Film
- Select the appropriate shrink film (polyolefin, PVC, or polyethylene).
- Mount it onto the film holder, ensuring the film unwinds smoothly without wrinkles.
- Adjust Machine Settings
- Set the sealing bar temperature based on the film’s specifications.
- Configure conveyor speed according to product size and desired throughput.
- Preheat the heat tunnel.
- Position the Product
- Place the product on the infeed conveyor.
- For semi-automatic machines, you may need to manually position the product on the sealing area.
- Wrap & Seal
- Once the product is in the correct position, the machine seals the film around the item.
- Excess film is trimmed off, leaving a neat sealed package.
- Heat Tunnel
- The sealed product enters the heat tunnel.
- Hot air is circulated to shrink the film around the product.
- The conveyor moves the product through the tunnel at a controlled pace.
- Cooling & Discharge
- Some machines include a cooling chamber to quickly stabilize the shrink wrap.
- The product is then discharged onto an outfeed conveyor or collection point.
- Quality Check
- Visually inspect the wrapped product for holes, loose spots, or burn marks.
- If necessary, adjust machine settings for better results.
By following these steps and fine-tuning variables such as temperature and conveyor speed, operators can achieve professional, consistent shrink-wrapped packages.
6. Shrink Wrapping in Various Industries
A shrink wrapping machine can be a transformative asset across myriad industries:
- Food & Beverage
- Application: Multi-packs (soda cans, water bottles), meat products, produce, baked goods.
- Benefits: Sealed wrapping extends shelf life, offers tamper evidence, and supports bulk packaging for retail.
- Pharmaceuticals
- Application: Medication bottles, medical devices, and other sensitive items requiring strict hygiene standards.
- Benefits: Shrink wrap ensures tamper evidence and maintains cleanliness.
- Retail & Consumer Goods
- Application: Electronics, toys, cosmetics, household goods.
- Benefits: Professional appearance, product protection, and branding opportunities with printed film.
- Industrial & Manufacturing
- Application: Bundling machine parts, tools, and industrial components for transport.
- Benefits: Secure packaging that prevents dust and moisture damage, streamlined shipping.
- Publishing & Printing
- Application: Books, stationery, magazines, brochures, and multi-piece printed materials.
- Benefits: Maintains the pristine condition of printed items and protects them from tearing or dirt.
- E-commerce & Distribution
- Application: Bulk packaging of assorted goods to prepare them for shipping.
- Benefits: Lowers shipping costs by consolidating items, maintains product integrity during transport.
7. Materials Used in Shrink Wrapping
Choosing the right film type is essential to achieving optimal performance from your shrink wrapping machine. Each material has unique properties:
- Polyolefin (POF)
- Characteristics: Lightweight, puncture-resistant, clear presentation.
- Advantages: Food-safe, versatile, and relatively strong.
- Best For: Food items, consumer goods, products needing high clarity.
- Polyvinyl Chloride (PVC)
- Characteristics: High clarity, good seal strength.
- Advantages: Commonly used in retail, cost-effective, good film shrink ratio.
- Considerations: PVC emits fumes during sealing and shrinking, so proper ventilation is crucial.
- Polyethylene (PE)
- Characteristics: Very durable, ideal for heavier or larger objects.
- Advantages: Can be thicker and is often used for bundling multiple items or pallet wrapping.
- Best For: Industrial packaging, bulk goods.
- Cross-Linked Polyolefin
- Characteristics: Excellent strength, clarity, and higher seal temperature tolerance.
- Advantages: Strong resistance to punctures and tears.
- Best For: Items with sharp edges or irregular shapes.
Choosing the Right Film
- Product Requirements: Food-grade vs. industrial-grade.
- Clarity & Presentation: Consider how important transparency is for showcasing the product.
- Machine Compatibility: Check film thickness and sealing temperature requirements.
- Budget & Volume: Assess costs per roll, wastage, and output demands.
8. Factors to Consider Before Purchasing
Investing in a shrink wrapping machine can yield significant returns in efficiency and product quality. However, it’s crucial to evaluate several factors:
- Throughput Requirements
- Questions to Ask: How many products do you need to wrap per hour? Will demand increase soon?
- Implication: High-volume needs often justify a fully automatic system, whereas smaller operations may be better served by a semi-automatic or manual machine.
- Product Size & Shape
- Questions to Ask: Are your products uniform in shape? Do you need to wrap oversized items?
- Implication: Irregularly shaped items may require specialized machines or adjustable sealing bars.
- Available Space
- Questions to Ask: How much floor space can you allocate for the machine and associated equipment?
- Implication: Smaller facilities might need a compact semi-automatic system, while larger facilities can accommodate bigger, more robust machines.
- Budget
- Questions to Ask: What is your capital expenditure limit? Are you considering financing options?
- Implication: Automatic machines have higher upfront costs but may offer lower long-term labor costs.
- Film Compatibility
- Questions to Ask: Will you be using polyolefin, PVC, or polyethylene film most of the time?
- Implication: Ensure the machine’s seal bar temperature range and tunnel settings match the chosen film.
- Maintenance & Technical Support
- Questions to Ask: Does the manufacturer offer service contracts? Are replacement parts readily available?
- Implication: Reliable after-sales support can save you from costly downtime.
9. Cost Analysis: Is a Shrink Wrapping Machine Worth It?
The decision to invest in a shrink wrapping machine often boils down to a balance between upfront costs and the long-term benefits of automation. Let’s break it down:
- Upfront Investment
- Manual machines can cost a few hundred to a couple of thousand dollars.
- Semi-automatic machines might range from $5,000 to $25,000, depending on features.
- Fully automatic systems can start around $30,000 and go up to $100,000+ for high-end, specialized models.
- Ongoing Operational Costs
- Film Usage: Polyolefin or PVC film rolls can range from $50 to $200, depending on roll size and thickness.
- Labor: A fully automatic machine reduces labor costs, while manual systems rely heavily on operator input.
- Maintenance: Sealing bars, conveyor motors, and heat tunnels need periodic servicing.
- Potential Savings
- Reduced Packaging Material: Shrink film is generally less expensive than bulky boxes.
- Lower Shipping Expenses: Smaller, tight wraps reduce dimensional weight.
- Faster Turnaround: High-speed systems can package more products in less time.
- Minimized Product Damage: Proper wrapping reduces returns from damaged goods.
- Return on Investment (ROI)
- For mid to large-scale operations, the ROI can be realized quickly, often within 1–3 years, depending on production volume.
- Smaller businesses may need to weigh whether a semi-automatic or manual approach offers a better short-term payoff before scaling up.
Overall, if you foresee sustained or growing packaging demands, a shrink wrapping machine is likely a worthwhile investment that can streamline operations and improve product presentation.
10. How to Maintain Your Shrink Wrapping Machine
Even the best shrink wrapping machine requires regular maintenance to operate efficiently. Here’s what you need to keep in mind:
- Daily Checks
- Clean the sealing bar to remove excess film buildup.
- Inspect the heat tunnel for any debris.
- Check film roll tension and alignment.
- Weekly or Monthly Inspections
- Evaluate conveyor belts for wear and tear.
- Ensure heat tunnel temperature gauges remain accurate.
- Lubricate moving parts as recommended by the manufacturer.
- Electrical Components
- Inspect wiring and connections for signs of wear or burning.
- Replace faulty heating elements and sensors immediately to prevent downtime.
- Regular Calibration
- Heat tunnel and sealing temperatures must be calibrated to match the film specifications.
- Overheating can lead to film burn or product damage, while underheating causes loose wrapping.
- Service Contracts
- Many manufacturers offer periodic service contracts.
- Professional technicians can spot issues early, reducing costly breakdowns.
11. Advanced Tips and Techniques for Best Results
- Optimize Film Tension
- Too much tension leads to tears; too little tension causes loose wraps.
- Adjust your machine’s film guides and tension rollers for the perfect balance.
- Temperature Management
- Each film type has an optimal shrinking temperature range.
- Experiment with increments of 5–10 degrees Fahrenheit to find the sweet spot.
- Pre-Heating the Tunnel
- Let the tunnel reach the recommended temperature before you begin wrapping.
- Inconsistent heat can cause uneven shrink and weak seals.
- Use Quality Film
- Cheap, low-grade film can cause frequent jams and poor-quality wraps.
- Investing in reputable film ensures consistency and reduces waste.
- Bundle Multiple Products
- If you’re shipping items in sets, consider shrink wrapping them together.
- Reduces packaging complexity and shipping costs.
- Employee Training
- Even automated systems benefit from well-trained operators who can quickly adjust settings and troubleshoot.
- A small investment in training can drastically reduce downtime and enhance packaging quality.
12. Common Troubleshooting & FAQs
Below are some typical issues users encounter with a shrink wrapping machine, along with quick fixes:
12.1 Wrinkles in the Film
- Possible Causes: Temperature too high, conveyor speed too slow, or film tension too tight.
- Solutions: Lower the heat tunnel temperature, speed up the conveyor, or reduce film tension.
12.2 Burned or Holes in the Film
- Possible Causes: Excessive tunnel temperature or film dwelling in heat for too long.
- Solutions: Adjust temperature downward or speed up the conveyor to reduce exposure.
12.3 Loose Shrink
- Possible Causes: Underheated film, low tension, or improper sealing.
- Solutions: Increase tunnel temperature, adjust tension, and verify seal bar function.
12.4 Machine Jams
- Possible Causes: Misaligned film, worn out conveyor belts, or incorrect product placement.
- Solutions: Realign or replace belts, ensure product is placed consistently, and verify film roll orientation.
12.5 FAQs
- Which film is better—PVC or Polyolefin?
- Polyolefin is generally more versatile and food-safe, but PVC is often more cost-effective for certain retail applications.
- How often should I service my shrink wrapping machine?
- Basic daily and weekly checks should be standard. Major servicing may be needed every 6–12 months, depending on usage.
- Can I use the same machine for different film types?
- Often, yes. Just ensure you adjust the temperature and sealing settings according to each film’s requirements.
- Is it safe to shrink wrap food products?
- Yes, as long as you use a food-grade film (like polyolefin) and follow all relevant food safety guidelines.
13. Featured Q&A: Achieving the Perfect Shrink Wrap
Q: What are the top three things to keep in mind to consistently achieve a perfect, tight shrink wrap?
A: Based on expert insights, here’s what you need to remember:
- Temperature Control
- Monitor the heat tunnel temperature closely. An optimal, consistent heat is key for a uniform shrink.
- Film Quality
- Not all films are created equal. Choose a film that matches your product needs and keep it properly stored to avoid moisture damage.
- Machine Maintenance
- A well-maintained machine is less likely to produce faulty wraps. Ensure that the sealing bar, conveyor belt, and heat tunnel elements are inspected regularly.
Conclusion & Next Steps
The shrink wrapping machine stands as a cornerstone of modern packaging—delivering efficiency, security, and professional presentation for countless products across diverse industries. From small artisanal businesses to large-scale manufacturing plants, shrink wrapping has proven itself as an invaluable method to protect, bundle, and brand items for the marketplace.
Key Takeaways
- Shrink wrapping machines cater to a variety of volumes: from manual setups for small-scale operations to fully automated lines handling tens of thousands of products daily.
- Polyolefin, PVC, and polyethylene films each have their distinct advantages and use cases, making it vital to choose the right film for your specific needs.
- Proper machine settings—particularly temperature, conveyor speed, and film tension—are crucial to achieving consistently high-quality results.
- Regular maintenance and operator training can significantly minimize downtime, reduce waste, and ensure a long machine lifespan.
If you’re ready to elevate your packaging game:
- Assess Your Needs
- Calculate your approximate packaging volume.
- Determine your budget, floor space, and product requirements.
- Research & Compare
- Explore different machine models, read reviews, and consult with manufacturers to match your exact specifications.
- Don’t hesitate to request demonstrations or trial runs.
- Plan for Growth
- Consider how your production needs might evolve in the next few years.
- A slightly more advanced system now could save you from needing an upgrade later.
- Take Action
- Reach out to a reputable supplier or manufacturer to discuss the best shrink wrapping solution for your operation.
- Ask about after-sales support, training, and maintenance services to ensure a smooth transition.
Ready to transform your packaging process with a state-of-the-art shrink wrapping machine?
- Share this post with colleagues who might benefit from advanced packaging solutions.
- Leave a comment with any questions or experiences you’ve had with shrink wrapping technology. Our team is here to help you make the right decision for your business.
Interested in learning more about innovative packaging solutions or seeing how our machines can integrate seamlessly into your current workflow? Contact us or explore our comprehensive product range to discover the perfect system for your needs.
Stay Connected with EngiTech
EngiTech is your trusted source for in-depth knowledge on industrial mechanical engineering machines and technologies. Stay ahead with the latest innovations, expert insights, and practical guides designed to help you make informed decisions for your business and engineering needs. Join our growing community of professionals and industry leaders to stay updated and competitive in the ever-evolving world of industrial technology.