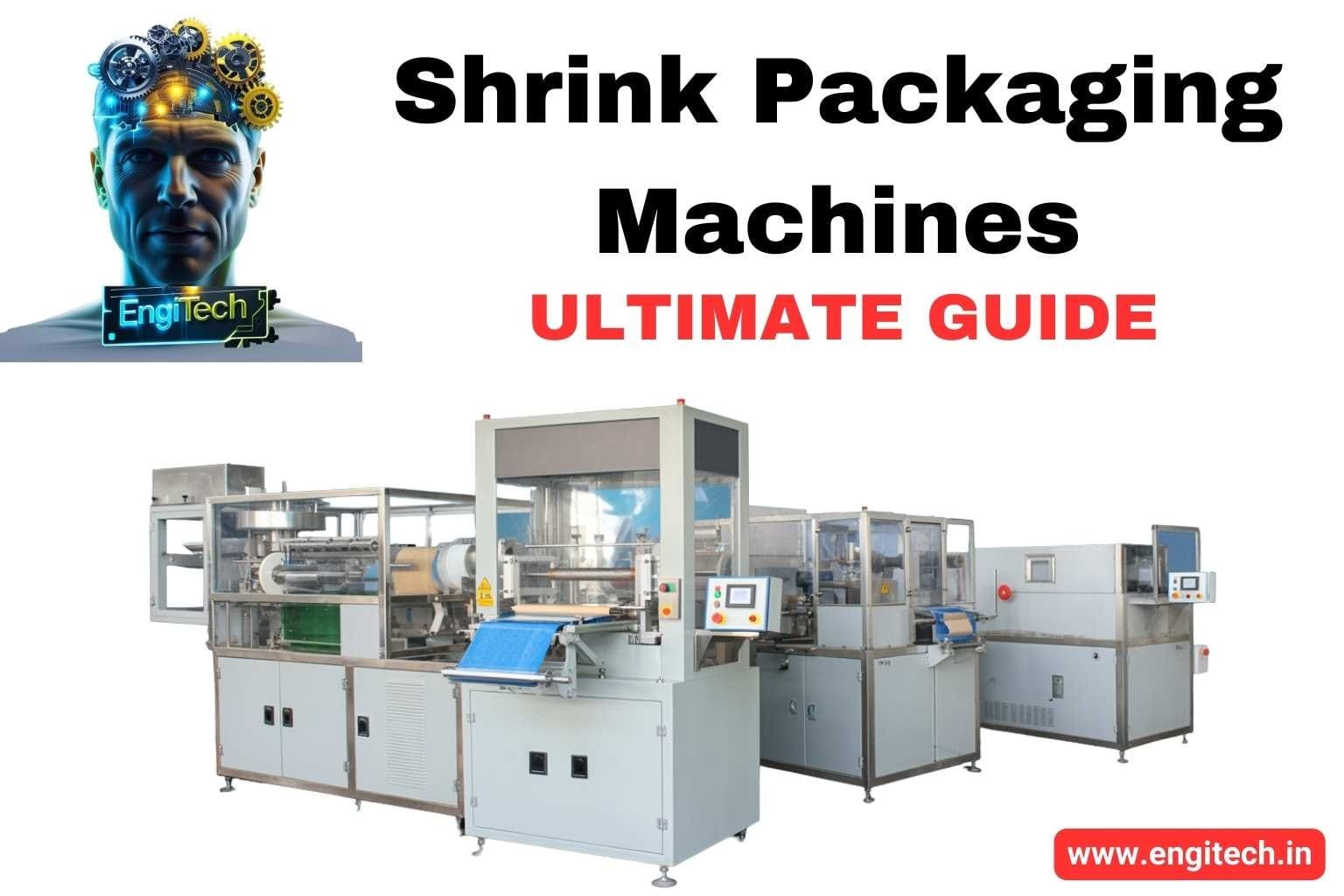
If you’ve ever picked up a tightly wrapped package that not only looked professional but also kept the product secure, chances are you’ve encountered the power of a shrink packaging machine. From food items on grocery shelves to electronics delivered right to your doorstep, shrink-wrapped packages have become a staple across industries for their neat appearance, cost-effectiveness, and protective capabilities.
In this comprehensive guide, you’ll learn everything you need to know about these indispensable packaging solutions—how they work, why they matter, and how to choose the right one for your business. By the end, you’ll be fully equipped to make an informed decision that can elevate your brand’s presentation and streamline your operations.
Table of Contents
Introduction: Why Shrink Packaging Matters
Imagine you’ve just purchased a high-end electronic gadget, and it arrives wrapped in loose, unprofessional-looking plastic. The initial impression may leave you questioning the product’s quality and the brand behind it. On the other hand, a product neatly enclosed in a perfectly contoured, tamper-evident film instills confidence in its quality and safety.
What you’ll learn in this guide:
- How shrink packaging works and the core components involved.
- The major types of shrink packaging machines and how each one can fit different business needs.
- Why shrink packaging is so popular across industries and how it can elevate your brand’s presentation.
- Insider tips on selecting and maintaining your machine for maximum durability and performance.
- Exciting new trends in shrink packaging technology that can give you an edge over competitors.
So if you’re a small business owner looking to enhance product appeal, or a production manager aiming to streamline operations with minimal fuss, read on. By understanding the ins and outs of shrink packaging machines, you’ll be empowered to make informed decisions that positively impact your bottom line.
Understanding Shrink Packaging Machines
A shrink packaging machine is a piece of equipment designed to wrap products in a special plastic film (often polyolefin, PVC, or polyethylene). After the film is applied, heat is used to shrink the film tightly around the product. This process offers several benefits:
- Enhanced Protection: The film shields your products from dust, moisture, and tampering.
- Improved Aesthetics: A tight, uniform wrap projects an air of professionalism, making your product stand out on crowded shelves.
- Cost-Effective: Shrink wrap film is relatively affordable, and the efficiency gained by using the machines can significantly cut labor costs.
At first glance, it might seem that a shrink packaging machine merely encloses items in plastic film. However, it’s more intricate than that. The machine involves careful temperature control, precise film feed mechanisms, and sometimes integration with conveyor systems to create a fully streamlined operation. These complexities ensure that the packaging not only looks good but also optimally safeguards the product.
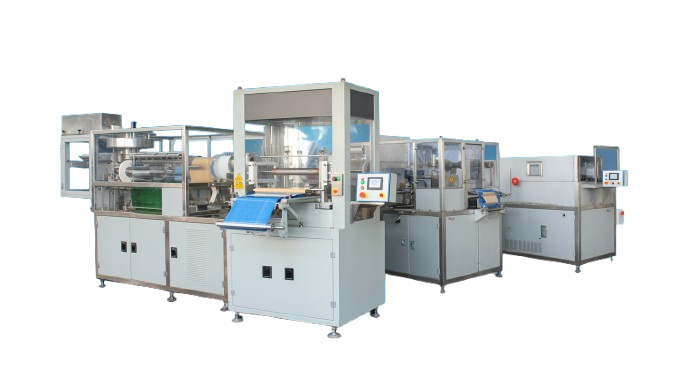
Key Components and Working Principles
Understanding the anatomy of a shrink packaging machine will help you appreciate its capabilities and decide which features matter most for your specific application. While designs vary, the fundamental components usually include:
- Film Dispenser
The film roll is mounted on a dispenser that feeds the plastic film into the wrapping zone. This setup often has tension control mechanisms to prevent wrinkles or uneven wrapping. - Sealing System
A sealing bar or jaw cuts and seals the plastic film around the product. Sealing quality is crucial for ensuring that the film won’t come undone, resulting in a loose or incomplete wrap. - Heat Tunnel or Chamber
This is where the magic happens. Once sealed, the product moves into a heat tunnel (in automatic systems) or a heat chamber (in manual or semi-automatic systems). The hot air in this chamber causes the film to shrink snugly around the product. - Cooling Zone
After heat is applied, some setups include a cooling phase to set the film. This helps prevent lingering heat from damaging the product and ensures the film remains tight. - Conveyor System (in fully automatic and some semi-automatic models)
A conveyor belt moves the products through the sealing and heating phases. It not only speeds up the process but also keeps operator intervention to a minimum. - Control Panel
Modern machines often come with digital control panels that let you adjust temperature, conveyor speed, and sealing time. This flexibility is especially helpful when handling multiple product sizes and materials.
How it works step by step:
- An operator (or an automated system) places the product in the film area.
- The sealing bar cuts and seals the film around the item.
- The wrapped item enters the heat tunnel.
- The film shrinks, conforming to the shape of the product.
- The product emerges, fully shrink-wrapped and ready for storage or distribution.
Types of Shrink Packaging Machines
Choosing the right machine is not always straightforward—each type comes with its own advantages, disadvantages, and best-use scenarios. Here’s a breakdown:
Manual Shrink Packaging Machines
- Overview: Perfect for low-volume operations or home-based businesses.
- Key Features:
- Hand-operated sealing bar.
- Often accompanied by a small heat gun or basic heat chamber.
- Advantages:
- Low initial cost.
- Easy to operate and maintain.
- Disadvantages:
- Limited throughput.
- Higher labor requirements per unit.
Semi-Automatic Shrink Packaging Machines
- Overview: Ideal for small to medium-sized businesses looking for higher speed without breaking the bank.
- Key Features:
- Automatic sealing system or L-bar sealer.
- Operator places items on the conveyor, but much of the process is automated.
- Advantages:
- Faster than manual machines.
- Reduced labor costs.
- More consistent sealing.
- Disadvantages:
- Higher investment than manual machines.
- Still requires an operator to position products.
Fully Automatic Shrink Packaging Machines
- Overview: Suited for large-scale operations where speed, precision, and minimal labor intervention are essential.
- Key Features:
- Automated infeed and outfeed conveyor.
- Advanced digital controls for temperature and speed.
- Advantages:
- High throughput and consistency.
- Minimal operator involvement.
- Advanced features like automated film feed and cutting.
- Disadvantages:
- Greater initial investment.
- More complex maintenance.
Advantages of Shrink Packaging
Shrink wrapping has gained immense popularity for good reason. Here are the standout benefits:
- Professional Appearance
A tight, wrinkle-free wrap gives products a polished look, improving shelf appeal and consumer confidence. - Tamper-Evident Packaging
When a product is wrapped in shrink film, any tampering becomes immediately noticeable. This adds an extra layer of protection against counterfeiting or mishandling. - Protection from Environmental Factors
Shrink-wrapped packages are resistant to dust, moisture, and sometimes UV light, depending on the film used. This helps maintain product integrity over longer periods. - Cost Efficiency
Shrink film is typically less expensive compared to other forms of protective packaging. Also, shrink packaging machines, especially automatic ones, reduce labor costs and speed up production. - Versatility
From small toys to large machinery parts, shrink film can conform to any shape. This is especially valuable in industries that package a wide variety of items. - Space-Saving Design
Unlike bulky boxes, shrink film adds minimal bulk. This efficient packaging can help reduce shipping and storage costs.
Common Applications Across Industries
Food and Beverage:
From bottled beverages to snack packs, shrink wrapping helps maintain hygiene and preserve product quality. It also bundles multi-packs together for promotions or warehouse storage.
Electronics:
Sensitive electronics benefit from dust and moisture protection. Some manufacturers also use anti-static shrink films to protect devices from electrostatic discharge.
Pharmaceuticals and Cosmetics:
When tamper-evidence is a top priority, shrink wrapping excels. Clear, tight packaging also showcases the product without removing it from its protective film.
Printing and Publishing:
Magazines, books, and promotional materials often come shrink-wrapped to preserve freshness and prevent pages from getting damaged.
Retail and Promotional Packs:
Bundling items—for example, “buy one get one free” promotions—becomes straightforward with shrink wrapping. This method keeps products together until they reach the consumer.
Industrial and Manufacturing:
Large machine parts or assemblies can be shrink-wrapped to protect them against environmental contaminants during transit or storage.
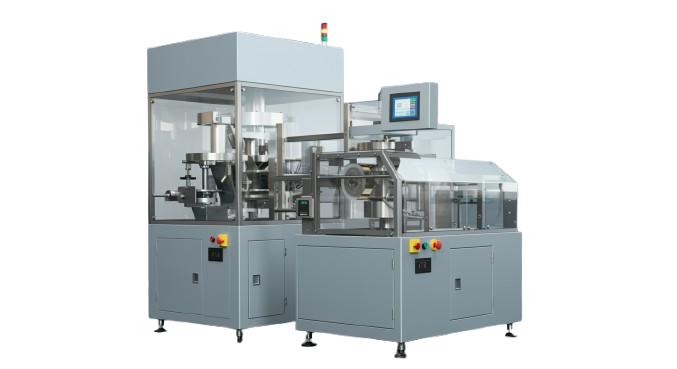
Selecting the Right Shrink Packaging Machine
Choosing a shrink packaging machine involves more than just budget considerations. Here’s what to keep in mind:
- Production Volume
- Low-volume businesses might do well with manual or semi-automatic machines.
- High-volume operations often need fully automatic systems to keep up with demand.
- Product Dimensions
- Ensure the machine can handle the largest items you intend to package.
- Consider if you need adjustable settings for handling products of varying sizes.
- Available Space
- Measure your production floor carefully. Automatic machines with conveyors can be sizable.
- Don’t forget to account for the space needed for a heat tunnel or shrink chamber.
- Budget and ROI
- Manual machines are cheaper but yield lower throughput.
- Automatic machines are more expensive but can pay off quickly in labor savings and increased productivity.
- Material Compatibility
- Consider the type of shrink film you plan to use (PVC, polyolefin, polyethylene).
- Each film has different sealing properties and shrink ratios.
- Maintenance and Support
- Look for a manufacturer or supplier known for robust customer support.
- Complexity of the machine often correlates with higher maintenance costs.
When in doubt, consult with reputable shrink wrapping machine manufacturers. Request demos, ask for references, and compare machine features carefully.
Maintenance and Best Practices
Keeping your shrink packaging machine in top shape is essential for consistent performance and longevity. Here are some tips:
- Regular Cleaning:
Dust and debris can accumulate in the sealing area and heat tunnel. A quick daily wipe-down can prevent buildup. - Scheduled Inspections:
Check belts, sealing elements, and heat controls periodically. Identifying wear and tear early can avert costly downtime. - Proper Film Handling:
Store shrink film rolls in a clean, dry area. Humidity and dust can affect film quality and sealing. - Temperature Calibration:
Heat tunnels need to be calibrated to the right temperature for the chosen film. Overheating can lead to film burn or product damage, while underheating results in loose wraps. - Operator Training:
Ensure operators know how to use and troubleshoot the machine properly. Misuse can lead to frequent breakdowns and subpar packaging.
Innovations and Trends in Shrink Packaging Technology
Shrink packaging technology has seen significant advancements in recent years. Here’s what’s trending:
- Eco-Friendly Films
With sustainability being a growing concern, many manufacturers now produce biodegradable or recyclable shrink films. - Automated Vision Systems
Some high-end machines incorporate vision systems to detect misaligned or faulty wraps and automatically stop the line for corrections. - Energy-Efficient Heat Tunnels
Newer designs focus on lower power consumption while still providing rapid heat-up and precise temperature control. - Integration with Smart Factory Systems
Machines can now communicate data like throughput rates, error logs, and maintenance alerts to central production management software. - Multi-Pack Flexibility
Advanced machines can handle varying batch sizes and multi-pack configurations on the fly, reducing downtime for retooling.
Staying informed about these trends can help you invest in a machine that remains competitive and meets evolving consumer expectations.
Step-by-Step Guide to Using a Shrink Packaging Machine
For those new to shrink wrapping, here’s a straightforward guide you can adapt to most machines:
- Choose the Right Film
- Select a film that suits your product’s weight, shape, and desired level of protection.
- Check compatibility with your machine’s sealing and tunnel specifications.
- Load the Film Roll
- Mount the roll onto the dispenser.
- Thread the film according to the manufacturer’s instructions.
- Adjust tension controls to avoid wrinkles.
- Set Machine Parameters
- Temperature: Calibrate for optimal shrink and sealing without overheating.
- Sealing Time: Too short might lead to incomplete seals; too long can melt the film.
- Conveyor Speed (if applicable): Align with the complexity and size of the product.
- Prepare the Products
- Ensure products are clean and free from loose attachments that might interfere with the wrap.
- Group items if you’re creating multi-packs or bundles.
- Position the Product
- Place the item on the film.
- If you’re using an automatic or semi-automatic machine, the conveyor will carry the product into the sealing area.
- Sealing
- The machine’s sealing bar or jaw will cut and seal the film.
- Check the seal visually. A complete, uniform seal is crucial to avoid loose wraps.
- Shrink Process
- The product enters the heat tunnel or chamber.
- Keep a close eye on initial runs to ensure the film shrinks evenly without overheating or wrinkles.
- Cooling
- If your machine includes a cooling section, let the film set before handling.
- In simpler setups, let the product rest momentarily on a staging table.
- Inspect & Store
- Examine the finished wrap for consistency and tightness.
- Store or box the product for shipping or retail display.
Following these steps diligently can result in professional-grade packaging that reflects well on your brand and keeps products safe.
Real-World Case Studies and Success Stories
Nothing cements the value of a shrink packaging machine like success stories from actual businesses. Here are a few brief examples to illustrate its impact:
- Gourmet Snack Startup
- Challenge: The startup needed a professional look to stand out in a highly competitive snack market.
- Solution: They invested in a semi-automatic shrink packaging machine.
- Results: Improved shelf appeal led to a 25% increase in retail orders. Labor costs also went down by 15%.
- Electronics Manufacturer
- Challenge: Shipping small circuit boards required dust and static protection.
- Solution: Incorporated an automated shrink line with anti-static film.
- Results: Reduced damage claims by 50% and sped up production by 30%.
- Pharmaceutical Company
- Challenge: Strict regulations required tamper-evident seals on multi-pack medications.
- Solution: Fully automatic machine with integrated quality checks.
- Results: The company passed audits with flying colors, and distribution efficiency improved significantly.
- Promotional Bundling for Retail
- Challenge: High volume of seasonal gift sets that needed secure, attractive bundling.
- Solution: Large-scale automatic shrink packaging machine with quick-change features.
- Results: Faster turnaround times, reducing the bottleneck during peak holiday seasons.
These examples highlight why more and more companies are turning to shrink packaging solutions: it’s not just a matter of looking good, but also about achieving real, quantifiable gains in operational efficiency.
FAQ: Your Top Shrink Packaging Questions Answered
Below are some common queries we often hear from businesses and production managers looking to integrate or upgrade to a shrink packaging machine.
- Q: What’s the difference between shrink wrapping and stretch wrapping?
A: While both use plastic films for packaging, shrink wrapping involves applying heat to tighten the film around the product, whereas stretch wrapping uses elastic film stretched around pallets or products without heat. - Q: Can I use any type of shrink film with my machine?
A: Not all films are universally compatible. Check your machine’s specifications. Some machines are better suited for polyolefin, while others work well with PVC or polyethylene. - Q: How do I prevent holes or burn marks in the film?
A: This usually occurs if the heat tunnel is set too high or the conveyor speed is too slow. Adjust temperature and speed settings, and always ensure the film is of good quality. - Q: Is shrink packaging eco-friendly?
A: Conventional plastics can raise environmental concerns. However, there are eco-friendly, recyclable shrink films available. Look for certifications and talk to manufacturers about biodegradable options. - Q: What kind of maintenance is typically required?
A: Routine cleaning, periodic checks of sealing bars and conveyor belts, and occasional part replacements are common. Some machines also require lubrication on moving parts.
Conclusion: Elevate Your Packaging Game
A shrink packaging machine is more than a piece of equipment—it’s an investment in the perception and security of your products. By embracing this technology, you stand to gain on multiple fronts: cost savings through lower labor and improved efficiency, enhanced product appeal that grabs consumer attention, and robust protection to reduce losses from environmental factors or tampering. As you’ve seen, businesses across various sectors—from food to electronics—are reaping tangible benefits by integrating shrink packaging into their operations.
If you’re aiming to boost efficiency, enhance brand presentation, and consistently deliver high-quality products, a shrink packaging machine may be the exact solution you need. The key is to choose wisely based on your production volume, budget, space constraints, and maintenance preferences. Once you’ve made that decision, commit to training your team, performing regular upkeep, and staying informed about the latest technological advancements.
Ready to take the next step?
- Ask Questions or Share Your Experiences: Drop a comment below to discuss your shrink packaging challenges or triumphs.
- Explore Our Advanced Packaging Solutions: If you’d like personalized guidance or want to request a quote, get in touch through our Contact Us page.
- Spread the Knowledge: Found this guide helpful? Share it on social media or forward it to a colleague who’s exploring packaging options.
With the right blend of knowledge, the right machine, and proper execution, you’ll be well on your way to dominating the market with top-tier, shrink-wrapped products that catch the eye and instill confidence in customers.
Stay Connected with EngiTech
EngiTech is your trusted source for in-depth knowledge on industrial mechanical engineering machines and technologies. Stay ahead with the latest innovations, expert insights, and practical guides designed to help you make informed decisions for your business and engineering needs. Join our growing community of professionals and industry leaders to stay updated and competitive in the ever-evolving world of industrial technology.