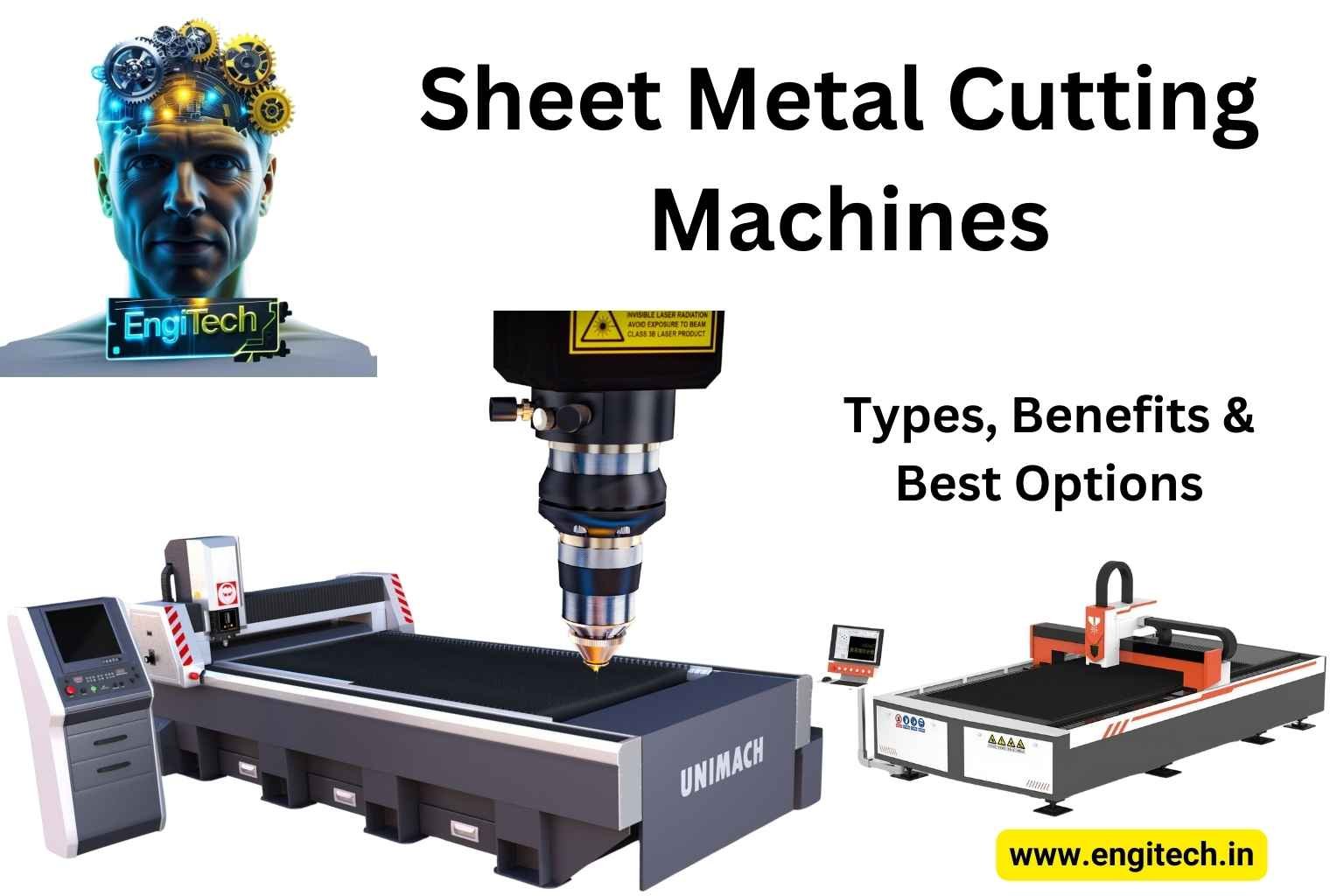
Sheet metal cutting is a cornerstone of modern manufacturing, influencing industries from automotive and aerospace to construction and electronics. As businesses push for higher efficiency, precision, and cost-effectiveness, selecting the right sheet metal cutting machine becomes critical.
This guide explores the various types of sheet metal cutting machines, their working principles, advantages, and key factors to consider when choosing the right machine for your needs. Whether you’re a manufacturer, engineer, or decision-maker, this in-depth guide will equip you with valuable insights to optimize your metal fabrication process.
Table of Contents
1. Understanding Sheet Metal Cutting: The Basics
Sheet metal cutting is the process of separating metal into desired shapes and sizes using specialized machines. It is categorized into two main types:
- Thermal Cutting: Uses heat sources like plasma, laser, or oxy-fuel to melt and cut metal.
- Mechanical Cutting: Uses physical force through shearing, punching, or sawing to create precise cuts.
Each method has its advantages and is suited for specific applications depending on material type, thickness, and required precision.
2. Types of Sheet Metal Cutting Machines
2.1 Laser Cutting Machines
How They Work:
Laser cutting machines use a high-powered laser beam to melt, burn, or vaporize metal, creating precise cuts. The laser is controlled by CNC (Computer Numerical Control) for extreme accuracy.
Advantages:
- High precision with minimal material waste
- Can cut intricate designs with clean edges
- Works on various metals including stainless steel, aluminum, and mild steel
Disadvantages:
- Higher initial investment and maintenance costs
- Not ideal for very thick metals compared to plasma cutting
Best For:
Industries requiring high precision, such as aerospace, medical device manufacturing, and custom fabrication.
2.2 Plasma Cutting Machines
How They Work:
Plasma cutters use ionized gas (plasma) to generate extreme heat, melting the metal while a high-speed jet of gas blows away the molten material.
Advantages:
- Cuts thick metals efficiently
- Faster than laser cutting for medium to thick materials
- More affordable than laser cutting systems
Disadvantages:
- Not as precise as laser cutting
- Produces rougher edges requiring additional finishing
Best For:
Heavy fabrication industries, automotive repair, and shipbuilding where speed and thickness are priorities over ultra-fine precision.
2.3 Water Jet Cutting Machines
How They Work:
Water jet cutting machines use a high-pressure stream of water, often mixed with abrasive particles, to cut through metal without heat.
Advantages:
- No heat-affected zones (HAZ), preserving metal properties
- Can cut a wide range of materials, including composites and stone
- High precision with minimal material distortion
Disadvantages:
- Slower cutting speed compared to plasma and laser cutting
- Requires high water consumption and waste disposal considerations
Best For:
Industries requiring precision without heat damage, such as aerospace, defense, and high-value component manufacturing.
2.4 Oxy-Fuel Cutting Machines
How They Work:
Oxy-fuel cutters use a combination of oxygen and fuel gas (such as acetylene) to create a flame hot enough to oxidize and cut through metal.
Advantages:
- Low-cost setup and operation
- Effective for cutting thick steel (above 1 inch)
- Portable and suitable for fieldwork
Disadvantages:
- Not suitable for non-ferrous metals like aluminum or stainless steel
- Produces significant heat distortion
Best For:
Construction, shipbuilding, and metal recycling applications where affordability and portability are key.
2.5 Mechanical Cutting Machines (Shearing, Punching, Sawing)
How They Work:
Mechanical cutting uses physical force to cut sheet metal through:
- Shearing: A straight blade cuts through metal with force.
- Punching: A tool punches out shapes from metal sheets.
- Sawing: Bandsaws or circular saws cut metal using toothed blades.
Advantages:
- No heat distortion
- Suitable for high-volume production
- Cost-effective for simpler cuts
Disadvantages:
- Limited to straight or predefined shapes
- Not ideal for intricate designs
Best For:
Mass production, structural steel fabrication, and simple metal cutting applications.
3. Choosing the Right Sheet Metal Cutting Machine
When selecting a sheet metal cutting machine, consider the following factors:
3.1 Material Type and Thickness
- Thin Metals (0.5mm – 5mm): Laser cutting or water jet cutting for precision.
- Medium Thickness (5mm – 25mm): Plasma cutting for speed and cost-effectiveness.
- Thick Metals (Above 25mm): Oxy-fuel cutting for affordability.
3.2 Precision Requirements
- High precision: Laser or water jet cutting
- Moderate precision: Plasma cutting
- Low precision: Oxy-fuel or mechanical shearing
3.3 Production Speed
- High-speed production: Plasma and mechanical shearing
- Moderate speed: Laser cutting
- Slower but precise: Water jet cutting
3.4 Cost Considerations
- Upfront Investment: Laser cutting machines are expensive, while oxy-fuel and plasma cutters have lower initial costs.
- Operational Costs: Plasma and oxy-fuel cutting have lower running costs than laser or water jet cutting.
- Maintenance & Consumables: Water jet cutting has higher maintenance due to abrasive material usage.
3.5 Safety and Environmental Factors
- Heat-Affected Zones (HAZ): Water jet cutting eliminates heat distortion.
- Fume & Gas Emissions: Plasma and oxy-fuel cutting generate more fumes.
- Noise Levels: Water jet and laser cutting are quieter than mechanical and plasma cutting.
4. Latest Trends and Innovations in Sheet Metal Cutting
4.1 Automation and Industry 4.0 Integration
- CNC and AI-powered cutting machines improve efficiency and accuracy.
- Smart sensors monitor cutting performance and reduce errors.
4.2 Hybrid Cutting Machines
- Machines combining laser and mechanical cutting are emerging for flexibility.
- Hybrid solutions reduce costs while maintaining precision.
4.3 Eco-Friendly Cutting Technologies
- Water jet cutting is gaining popularity due to its minimal environmental impact.
- Advances in laser cutting reduce energy consumption and improve sustainability.
FAQs About Sheet Metal Cutting Machines
1. What is the best machine for cutting sheet metal?
The best machine depends on your specific needs:
- Laser cutting for high precision and intricate designs.
- Plasma cutting for fast cutting of thick metals.
- Water jet cutting for precision without heat distortion.
- Oxy-fuel cutting for cost-effective thick metal cutting.
- Mechanical shearing or punching for high-volume production of simple shapes.
2. What is the difference between laser, plasma, and water jet cutting?
- Laser cutting: High precision, minimal waste, best for thin to medium metals.
- Plasma cutting: Faster than laser for thick metals but less precise.
- Water jet cutting: No heat-affected zones, suitable for various materials but slower.
3. How thick can a laser cutter cut sheet metal?
Laser cutters can cut:
- CO₂ lasers: Up to 20mm (mild steel)
- Fiber lasers: Up to 50mm (stainless steel & aluminum)
- The cutting capacity depends on laser power (e.g., 1kW to 12kW+).
4. Is plasma cutting better than laser cutting?
It depends on the application:
- Plasma cutting is better for speed and cutting thick metals (above 10mm).
- Laser cutting is superior for precision, intricate designs, and thin metals.
5. Which sheet metal cutting method is the most cost-effective?
- For thick steel (above 25mm): Oxy-fuel cutting is the most economical.
- For mid-range thickness (5mm – 25mm): Plasma cutting offers the best balance.
- For thin sheet metal: Mechanical shearing or punching is cost-effective.
6. What are the main disadvantages of laser cutting?
- High initial investment for laser cutting machines.
- Not ideal for very thick metals (plasma or oxy-fuel is better).
- Reflective materials like copper and brass can be challenging for CO₂ lasers.
7. How do I choose the right sheet metal cutting machine?
Consider:
- Material Type & Thickness: Laser for thin, plasma for medium, oxy-fuel for thick.
- Precision Needs: Laser or water jet for high accuracy.
- Budget & Operating Costs: Oxy-fuel is the cheapest, laser has high upfront costs.
- Speed Requirements: Plasma and laser are the fastest.
8. What are the safety precautions for sheet metal cutting?
- Wear proper PPE (gloves, goggles, fire-resistant clothing).
- Ensure proper ventilation for plasma and oxy-fuel cutting to prevent fumes.
- Avoid direct laser exposure to prevent burns and eye injuries.
- Secure the material properly to prevent shifting during cutting.
9. How does CNC technology improve sheet metal cutting?
CNC (Computer Numerical Control) ensures:
- Higher precision and repeatability
- Faster production speeds with minimal errors
- Automated cutting for complex designs
- Reduced material wastage and increased efficiency
10. What are the latest trends in sheet metal cutting technology?
- Fiber laser cutting is becoming more dominant due to higher efficiency.
- Automated & AI-powered cutting improves speed and accuracy.
- Eco-friendly cutting methods like water jet cutting are gaining popularity.
- Hybrid cutting systems combine laser and mechanical methods for flexibility.
These FAQs provide insights into the most common questions about sheet metal cutting machines, helping businesses and manufacturers make informed decisions.
Conclusion: Optimizing Your Metal Fabrication Process
Choosing the right sheet metal cutting machine depends on your specific needs, including material type, thickness, precision requirements, and budget.
- For high precision: Laser or water jet cutting is ideal.
- For speed and affordability: Plasma or oxy-fuel cutting works best.
- For high-volume production: Mechanical shearing and punching provide cost-effective solutions.
By understanding the strengths and limitations of each cutting method, you can invest in the most suitable technology to optimize productivity, reduce waste, and improve overall manufacturing efficiency.
Take Action
- Need expert advice on choosing the right cutting machine? Contact us for a consultation.
- Looking for top-quality cutting solutions? Explore our range of cutting machines tailored for diverse industrial applications.
- Stay updated on the latest trends in metal fabrication! Subscribe to our newsletter.
This guide ensures that you make an informed decision, maximizing efficiency and precision in your metalworking operations.
Stay Connected with EngiTech
EngiTech is your trusted source for in-depth knowledge on industrial mechanical engineering machines and technologies. Stay ahead with the latest innovations, expert insights, and practical guides designed to help you make informed decisions for your business and engineering needs. Join our growing community of professionals and industry leaders to stay updated and competitive in the ever-evolving world of industrial technology.