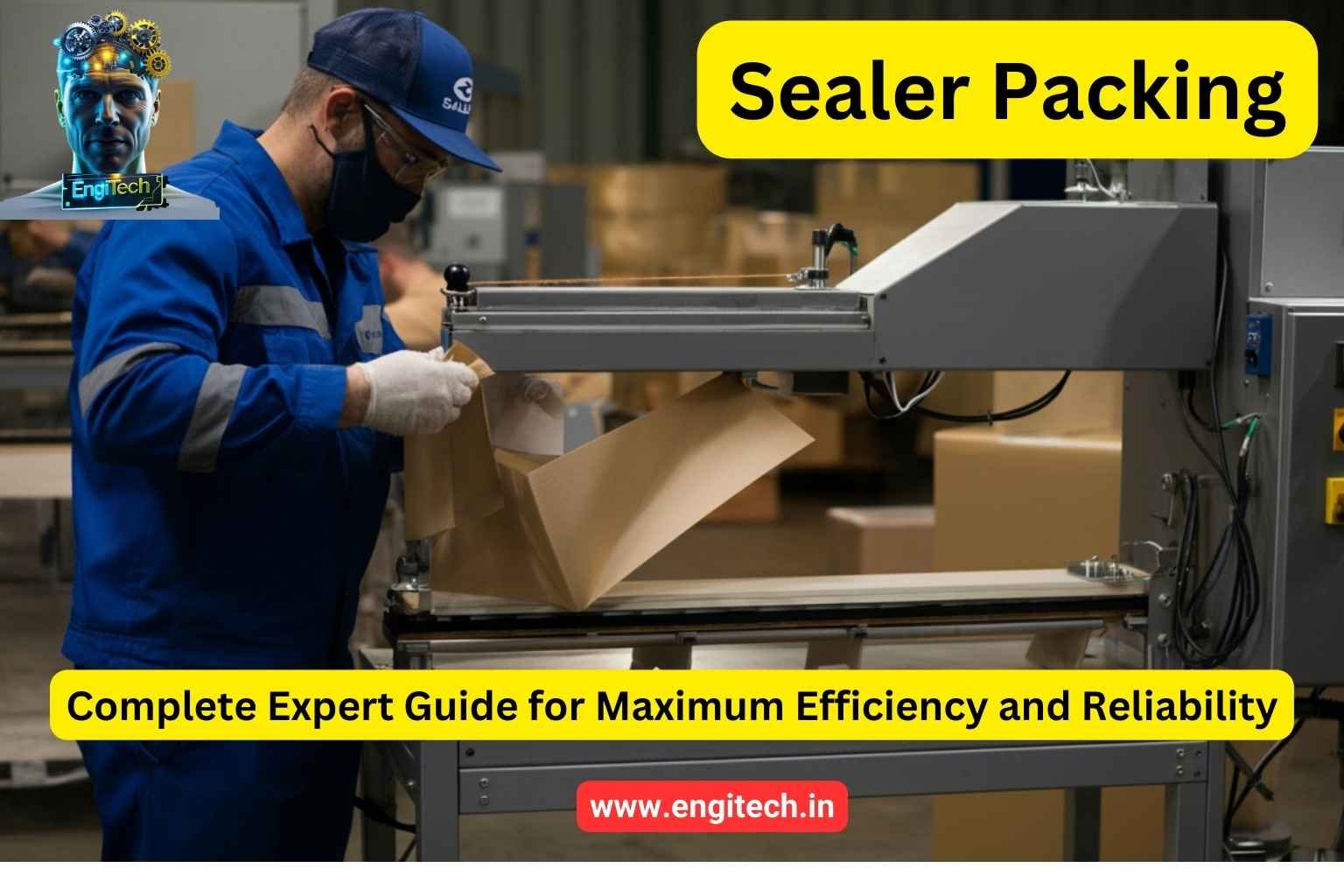
Sealer packing is an essential component across industries, ensuring machinery and equipment operate effectively and safely. Poor sealing leads to costly downtime, hazardous leaks, and inefficiencies. This guide delivers authoritative, expert-backed strategies to optimize your sealing performance, reduce operational costs, and enhance productivity.
Table of Contents
What is Sealer Packing?
Sealer packing is designed to create a secure, leak-proof barrier between moving parts, preventing fluid or gas leakage and contamination. Used extensively in pumps, compressors, valves, and rotary equipment, effective packing boosts efficiency and operational reliability.
Types of Sealer Packing Materials
Selecting the appropriate material is crucial. Key materials include:
- Graphite Packing: Excellent temperature and pressure resistance, ideal for demanding conditions.
- PTFE (Teflon) Packing: Highly chemical-resistant with low friction, great for aggressive chemical environments.
- Elastomer/Rubber Packing: Flexible and resilient, suited for moderate temperature applications.
- Metallic Packing: Durable, suited for extreme pressures and temperatures.
Importance of Effective Sealer Packing
Quality sealer packing provides numerous benefits:
- Energy Efficiency: Minimizes leaks, reducing power consumption.
- Reduced Maintenance Costs: Fewer repairs, reduced downtime.
- Enhanced Safety: Prevents hazardous leaks, protecting employees and the environment.
- Extended Equipment Lifespan: Lowers wear, increases service life.
Common industries benefiting significantly from effective packing:
- Chemical & Pharmaceutical
- Oil & Gas
- Food & Beverage
- Water Treatment & Wastewater Management
How to Select the Best Sealer Packing
When choosing packing, consider:
- Material Compatibility: Verify chemical and physical compatibility with operational fluids.
- Temperature & Pressure Requirements: Match seal material to your operational conditions.
- Chemical Resistance: Prioritize chemical resilience to avoid degradation or failure.
- Durability & Reliability: Choose materials proven to withstand harsh industrial environments.
Installation & Maintenance Best Practices
Proper installation and maintenance are vital for maximum performance.
Installation Tips:
- Clean and prepare sealing surfaces thoroughly.
- Carefully measure and align the packing accurately.
- Tighten seals gradually and evenly, avoiding over-tightening.
- Conduct immediate testing post-installation.
Maintenance Tips:
- Regular visual and performance inspections.
- Timely lubrication and cleaning.
- Scheduled replacement of worn-out seals.
- Proactive, preventive maintenance schedules.
Common Troubleshooting:
- Leakage due to incorrect installation: Reinstall correctly.
- Excessive wear from abrasion: Choose self-lubricating or abrasion-resistant materials.
- Temperature failure: Upgrade to high-temperature resistant packing.
Expert Insights and Case Studies
Expert Insights:
According to industrial sealing expert Dr. Emily Rogers, “High-quality sealer packing significantly reduces operational expenses and safety risks. Regular inspections and proactive maintenance save substantial costs in the long run.”
Industry veteran John Michaels adds, “Companies often overlook sealing performance, neglecting regular maintenance that ultimately leads to expensive downtime.”
Real-world Case Studies:
- Chemical Plant: Implemented PTFE packing, resulting in 40% energy cost reduction and 30% fewer maintenance interventions.
- Oil & Gas Company: Switched to metallic graphite seals, significantly enhancing operational reliability, safety, and equipment longevity.
Frequently Asked Questions (FAQs):
Q1. What exactly does sealer packing do?
A: Prevents leaks and contamination between moving equipment parts, ensuring safe and efficient operation.
Q2. Which sealer packing material is best?
A: Material depends on specific operational requirements. Graphite for high-pressure and temperature; PTFE for chemical resistance; Elastomers for flexibility.
Q3. How frequently should packing be replaced?
A: Typically every 6-12 months, depending on conditions and usage. Frequent inspections help predict maintenance needs.
Q4. Can improper packing be dangerous?
A: Yes, incorrect or failing seals can cause leaks, equipment failure, and significant safety hazards.
Q5. How to improve packing longevity?
A: Regular inspections, proper installation techniques, and preventative maintenance significantly enhance longevity.
Conclusion
Properly selected, installed, and maintained sealer packing significantly boosts industrial productivity, safety, and cost-efficiency. Understanding packing materials, effective installation practices, routine maintenance, and leveraging expert advice greatly enhance your operational success.
Ready to optimize your sealing performance?
- Share this article with colleagues.
- Comment below with your sealing challenges or experiences.
- Subscribe to our newsletter for the latest sealing industry insights.
- Contact our experts today for personalized recommendations.
Stay Connected with EngiTech
EngiTech is your trusted source for in-depth knowledge on industrial mechanical engineering machines and technologies. Stay ahead with the latest innovations, expert insights, and practical guides designed to help you make informed decisions for your business and engineering needs. Join our growing community of professionals and industry leaders to stay updated and competitive in the ever-evolving world of industrial technology.