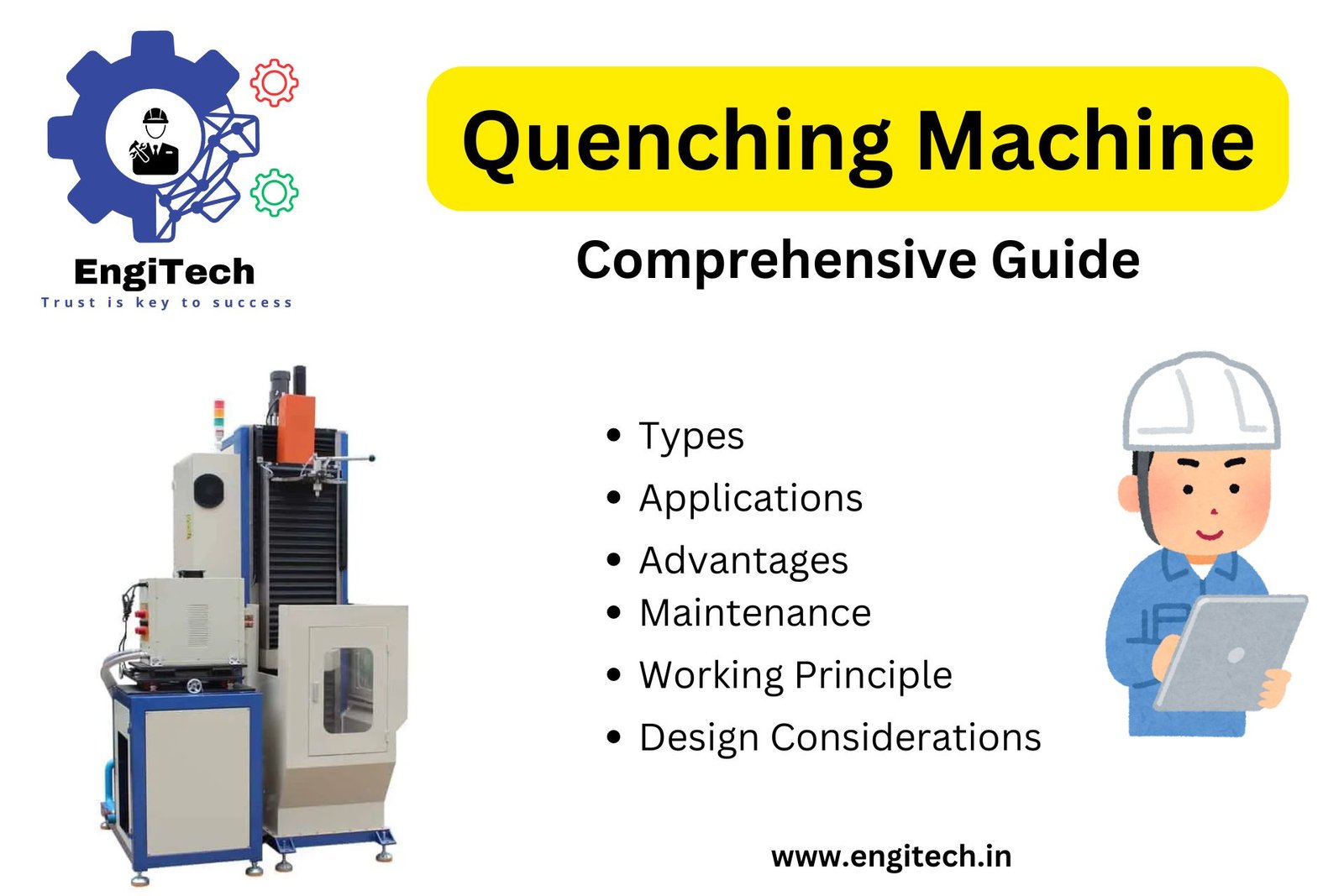
In the world of metallurgy and material science, the quenching process plays a pivotal role in enhancing the mechanical properties of metals. Central to this process is the quenching machine, an essential tool that facilitates controlled cooling, thereby imparting desired hardness and strength to various metal components.
This blog post aims to provide a thorough understanding of quenching machines, their types, working principles, applications, and the significance they hold in modern industries. Whether you are a student, a professional engineer, or simply someone interested in metallurgy, this guide will offer valuable insights into the intricate world of quenching machines.
Table of Contents
What is a Quenching Machine?
A quenching machine is a specialized piece of equipment used in the heat treatment process of metals. It is designed to rapidly cool heated metal components by immersing them in a quenching medium, typically water, oil, or air. This rapid cooling process alters the metal’s microstructure, resulting in increased hardness and improved mechanical properties. The quenching machine ensures uniform cooling, minimizing the risk of distortions or cracks in the metal.
The Importance of Quenching in Metallurgy
Quenching is a critical step in the heat treatment process, especially for steel and other ferrous alloys. The primary purpose of quenching is to enhance the hardness and strength of the metal by forming a martensitic microstructure. Without proper quenching, metals would retain their ductile properties, making them unsuitable for applications requiring high wear resistance and durability. The quenching machine ensures that this process is controlled and consistent, leading to high-quality end products.
Types of Quenching Machines
Quenching machines come in various types, each suited for specific applications and quenching mediums. Understanding the different types of quenching machines is crucial for selecting the right equipment for your specific needs.
1. Immersion Quenching Machines
Immersion quenching machines are the most common type, where the metal component is fully immersed in a quenching medium such as water, oil, or a polymer solution. The immersion process ensures rapid and uniform cooling, which is essential for achieving the desired hardness and mechanical properties.
Key Features:
- Uniform Cooling: The entire surface of the metal is exposed to the quenching medium, ensuring uniform cooling.
- Controlled Process: The immersion time and temperature can be precisely controlled, allowing for consistent results.
- Versatility: Suitable for a wide range of metal components, including gears, shafts, and tools.
2. Spray Quenching Machines
Spray quenching machines use high-pressure nozzles to spray the quenching medium onto the heated metal surface. This method is particularly effective for components with complex geometries, where immersion may not provide uniform cooling.
Key Features:
- Targeted Cooling: Allows for selective cooling of specific areas of the metal component.
- Reduced Distortion: Minimizes the risk of warping or cracking, especially in components with varying thicknesses.
- Efficient Use of Quenching Medium: Reduces the amount of quenching medium required compared to immersion quenching.
3. Gas Quenching Machines
Gas quenching machines utilize an inert gas, such as nitrogen or helium, as the quenching medium. This method is often employed in vacuum heat treatment processes, where the absence of liquid quenching mediums is necessary to avoid contamination.
Key Features:
- Clean Process: No risk of contamination from liquids, making it ideal for precision components.
- Controlled Cooling Rate: The cooling rate can be adjusted by varying the gas pressure and flow rate.
- Applications: Commonly used for aerospace and medical components where cleanliness is critical.
4. Selective Quenching Machines
Selective quenching machines are designed to cool only specific areas of a metal component, leaving other areas unaffected. This method is used when only certain parts of the component require hardening.
Key Features:
- Customizable Process: Allows for precise control over which areas are quenched.
- Reduced Material Stress: Prevents unnecessary stress and distortion in non-quenched areas.
- Applications: Ideal for components such as camshafts and crankshafts.
Working Principle of a Quenching Machine
The working principle of a quenching machine revolves around the rapid cooling of a heated metal component to alter its microstructure. The process typically involves the following steps:
1. Heating
The metal component is first heated to a specific temperature, often above its critical temperature, in a furnace. This heating process transforms the metal’s microstructure into austenite, a phase that is essential for achieving the desired hardness through quenching.
2. Immersion or Spraying
Once the metal reaches the desired temperature, it is either immersed in a quenching medium or subjected to a high-pressure spray. The rapid cooling caused by the quenching medium transforms the austenite into martensite, a hard and brittle microstructure.
3. Cooling
The quenching medium absorbs the heat from the metal, cooling it down to room temperature. The cooling rate is critical and must be controlled to avoid defects such as cracks or warping.
4. Post-Quenching Treatment
After quenching, the metal component may undergo further heat treatment processes such as tempering to reduce brittleness and improve toughness. This step is essential for achieving the final mechanical properties required for the specific application.
Applications of Quenching Machines
Quenching machines are used across a wide range of industries, where the mechanical properties of metal components are of paramount importance. Some of the key applications include:
1. Automotive Industry
In the automotive industry, quenching machines are used to harden components such as gears, crankshafts, camshafts, and axles. The increased hardness and wear resistance provided by quenching are essential for ensuring the longevity and reliability of these critical parts.
2. Aerospace Industry
The aerospace industry demands high-strength, lightweight components that can withstand extreme conditions. Quenching machines play a vital role in the production of aircraft components such as turbine blades, landing gear, and structural parts, where material properties are critical for safety and performance.
3. Tool and Die Industry
Tools and dies used in manufacturing processes must possess exceptional hardness and wear resistance to endure repeated use. Quenching machines are employed to harden cutting tools, punches, molds, and dies, ensuring they maintain their sharpness and dimensional accuracy.
4. Heavy Machinery
Components used in heavy machinery, such as excavators, bulldozers, and mining equipment, are subjected to harsh conditions. Quenching machines are used to enhance the durability and toughness of these components, reducing downtime and maintenance costs.
5. Power Generation
In the power generation industry, quenching machines are used to treat components such as turbine shafts, generator rotors, and boiler tubes. The improved mechanical properties resulting from quenching ensure these components can withstand the demanding operating conditions of power plants.
Choosing the Right Quenching Machine
Selecting the right quenching machine for your specific application involves considering several factors. These include the type of metal, the desired mechanical properties, the size and geometry of the component, and the quenching medium. Here are some key considerations:
1. Material Compatibility
Different metals require different quenching methods and mediums. For example, steel alloys typically use water or oil quenching, while non-ferrous metals may require air or gas quenching. Understanding the material properties is essential for choosing the right quenching machine.
2. Component Geometry
The shape and size of the metal component play a significant role in determining the appropriate quenching machine. Complex geometries may benefit from spray quenching, while simpler shapes may be better suited for immersion quenching.
3. Quenching Medium
The choice of quenching medium affects the cooling rate and the final properties of the metal. Water provides the fastest cooling rate, but it may cause distortion or cracking in some alloys. Oil offers a slower cooling rate, reducing the risk of defects but may require additional cleaning steps.
4. Production Volume
For high-volume production, automated quenching machines with conveyor systems may be more suitable, ensuring consistent results and reducing labor costs. For smaller batches or specialized components, manual or semi-automated machines may offer greater flexibility.
Common Challenges in Quenching and How to Overcome Them
Quenching is a complex process that presents several challenges. Understanding these challenges and how to overcome them is crucial for achieving optimal results.
1. Distortion and Warping
Rapid cooling can cause uneven contraction of the metal, leading to distortion or warping. To minimize this risk, it is essential to control the cooling rate and ensure uniform exposure to the quenching medium. Using appropriate fixtures and jigs during quenching can also help maintain the component’s shape.
2. Cracking
Cracking is a common issue in quenching, particularly in high-carbon steels and large components. To prevent cracking, it is important to preheat the metal before quenching and to select a quenching medium that provides a controlled cooling rate. Post-quenching tempering can also relieve stresses and reduce the risk of cracking.
3. Residual Stresses
Quenching can introduce residual stresses into the metal, which may lead to premature failure or reduced fatigue life. To mitigate this, a combination of quenching and tempering is often used to balance hardness and toughness. Additionally, stress-relief annealing can be performed after quenching to reduce residual stresses.
4. Non-Uniform Hardness
Achieving uniform hardness across the entire component is a challenge, especially in complex geometries. Careful selection of the quenching method and medium, along with proper agitation of the quenching bath, can help ensure uniform cooling and hardness distribution.
Maintenance and Care of Quenching Machines
Proper maintenance of quenching machines is essential for ensuring their longevity and consistent performance. Regular maintenance routines should include:
1. Quenching Medium Maintenance
The quenching medium should be regularly filtered and replaced to remove contaminants and maintain its effectiveness. Monitoring the temperature and agitation of the quenching medium is also crucial for consistent results.
2. Machine Calibration
Regular calibration of the quenching machine ensures that the immersion time, spray pressure, and cooling rates are within the desired parameters. This helps maintain the quality and consistency of the quenched components.
3. Inspection and Repair
Periodic inspection of the machine’s components, such as nozzles, pumps, and control systems, is essential for identifying and addressing any wear or damage. Prompt repair or replacement of faulty parts helps prevent downtime and ensures the machine operates at peak efficiency.
Expert Insights: Best Practices for Quenching
Our team of expert engineers has compiled a list of best practices for optimizing the quenching process:
1. Preheat the Quenching Medium
Preheating the quenching medium can help reduce the thermal shock experienced by the metal, minimizing the risk of cracking and distortion. This is particularly important for large or complex components.
2. Use Agitation for Uniform Cooling
Agitating the quenching medium ensures that the heat is evenly distributed, preventing hot spots and ensuring uniform cooling. This can be achieved through mechanical stirring or by circulating the quenching medium.
3. Control the Cooling Rate
The cooling rate should be carefully controlled based on the material and desired properties. For high-carbon steels, a slower cooling rate is recommended to prevent cracking, while low-carbon steels may benefit from faster cooling.
4. Perform Post-Quenching Tempering
Tempering after quenching is essential for reducing brittleness and improving toughness. The tempering temperature and duration should be selected based on the specific material and application requirements.
FAQs related to quenching machines:
1. What is a quenching machine used for?
- A quenching machine is used to rapidly cool heated metal components, typically after they have been heated to a critical temperature. This process alters the metal’s microstructure, increasing its hardness and strength, which is essential for applications that require wear resistance and durability.
2. What are the different types of quenching machines?
- The main types of quenching machines include immersion quenching machines, spray quenching machines, gas quenching machines, and selective quenching machines. Each type is suited to different applications and cooling mediums.
3. How does a quenching machine work?
- A quenching machine works by immersing or spraying a quenching medium (such as water, oil, or gas) onto a heated metal component. The rapid cooling transforms the metal’s microstructure, typically into martensite, which enhances its hardness and strength.
4. What are the benefits of using a quenching machine?
- The primary benefits of using a quenching machine include increased hardness, improved mechanical properties, reduced risk of warping or cracking, and consistent, controlled cooling.
5. What is the difference between oil quenching and water quenching?
- Oil quenching provides a slower cooling rate compared to water quenching, which reduces the risk of distortion and cracking. Water quenching, on the other hand, cools the metal faster, which can be beneficial for achieving higher hardness but may increase the risk of defects.
6. Can quenching cause metal to crack?
- Yes, quenching can cause metal to crack, especially if the cooling rate is too fast or if the metal has high carbon content. To minimize the risk of cracking, it is important to control the cooling rate and use appropriate quenching mediums and methods.
7. What is selective quenching?
- Selective quenching is a process where only specific areas of a metal component are cooled, leaving other areas unaffected. This technique is used when only certain parts of the component require hardening, such as in camshafts or crankshafts.
8. Why is tempering necessary after quenching?
- Tempering is necessary after quenching to reduce the brittleness introduced by the rapid cooling process. It helps to improve the toughness and ductility of the metal while maintaining the hardness achieved during quenching.
9. What are the common challenges in the quenching process?
- Common challenges in the quenching process include distortion and warping, cracking, non-uniform hardness, and residual stresses. These challenges can be mitigated by controlling the cooling rate, using appropriate fixtures, and performing post-quenching treatments like tempering.
10. How do I choose the right quenching machine for my application?
- To choose the right quenching machine, consider factors such as the type of metal, the desired mechanical properties, the size and geometry of the component, the quenching medium, and the production volume. Consulting with experts and understanding the specific requirements of your application are essential steps in making the right choice.
11. What maintenance is required for quenching machines?
- Regular maintenance for quenching machines includes monitoring and replacing the quenching medium, calibrating the machine to ensure consistent cooling rates, and inspecting and repairing components such as nozzles, pumps, and control systems.
12. What industries commonly use quenching machines?
- Quenching machines are commonly used in industries such as automotive, aerospace, tool and die manufacturing, heavy machinery, and power generation. These industries require components with high hardness, wear resistance, and durability.
These FAQs are written to address the most common queries related to quenching machines, making them valuable for knowledge seekers, students, and professionals alike.
Conclusion
Quenching machines are indispensable tools in the heat treatment process, enabling the precise control of cooling rates to achieve the desired mechanical properties in metals. Whether you are a student exploring the fundamentals of metallurgy, a professional engineer seeking to enhance your understanding of quenching processes, or an industry expert looking for advanced insights, this guide provides comprehensive information on quenching machines and their applications.
By following best practices and understanding the various types of quenching machines, you can optimize the quenching process, ensuring high-quality, durable components for a wide range of industries. As technology continues to evolve, quenching machines will remain a critical part of manufacturing, contributing to the advancement of materials science and engineering.
From EngiTech Team
EngiTech is your trusted resource for in-depth knowledge and expert insights into the world of industrial mechanical engineering. Whether you’re a seasoned professional, an engineering student, or simply passionate about innovative technology, our comprehensive guides and expertly crafted content empower you to stay ahead in the industry. Dive into detailed analyses, cutting-edge developments, and practical advice on a wide range of topics, from advanced machinery to essential engineering processes. Join us at EngiTech and discover how you can elevate your expertise and make informed decisions with confidence.