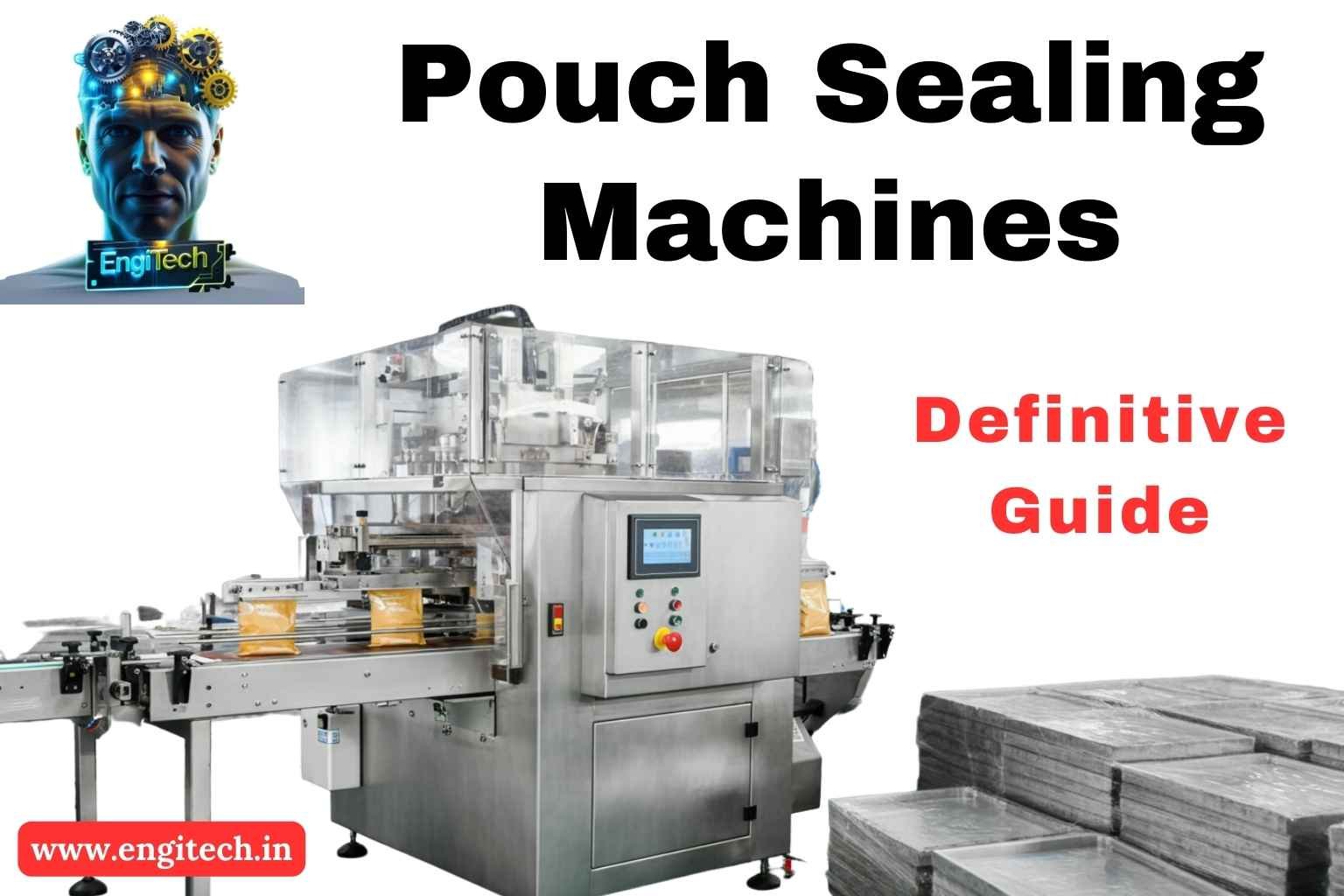
If you’re searching for a way to streamline your packaging process and enhance product preservation, look no further than the pouch sealing machine—a crucial innovation that’s reshaping industrial and small-scale packaging alike. Within this comprehensive guide, you’ll learn exactly how these machines work, why they’re indispensable across industries, and how to select the perfect model for your unique needs. Whether you’re a small business owner who’s tired of manual sealing methods or a production manager who’s aiming to ramp up packaging volumes, you’ll find actionable strategies to simplify your workflow, maintain product freshness, and ensure you’re giving your customers the quality they deserve.
Modern consumers demand freshness, durability, and visual appeal in the products they buy, whether it’s artisanal coffee beans or high-end electronics. Traditional sealing methods can be time-consuming, prone to human error, and unreliable over the long haul. Enter the pouch sealing machine, an essential piece of equipment that delivers airtight, tamper-evident seals in seconds.
But why do pouch sealers matter so much in today’s market? It’s all about efficiency and consistency. In an era where online reviews can make or break a brand, having a reliable packaging system can significantly impact your business reputation. Mistakes like leaky seals, contaminated products, and damaged goods can all be avoided by using a machine that’s designed for precision. By the end of this guide, you’ll understand exactly how pouch sealing machines function, which type fits your specific needs, and how to operate and maintain them for maximum ROI.
Table of Contents
Understanding the Basics of Pouch Sealing Technology
The fundamental principle behind any pouch sealing machine is heat—applied in just the right way, at the correct temperature, and for the ideal duration. Modern sealers use a combination of heated bars or continuous bands that press against the pouch material, effectively melting and fusing the layers together. Some machines even employ ultrasonic technology, which uses high-frequency vibrations to bond packaging material. Regardless of the mechanism, the goal is the same: create a secure, leak-proof seal that preserves and protects the product inside.
Key Points
- Heat Application: The core mechanism involves consistent heating elements that melt the pouch’s inner layers.
- Pressure & Cooling: Right after heating, pressure is applied, followed by a quick cooling phase to finalize the seal.
- Material Compatibility: Machines are built to handle various packaging materials like polyethylene, polypropylene, and laminated foils.
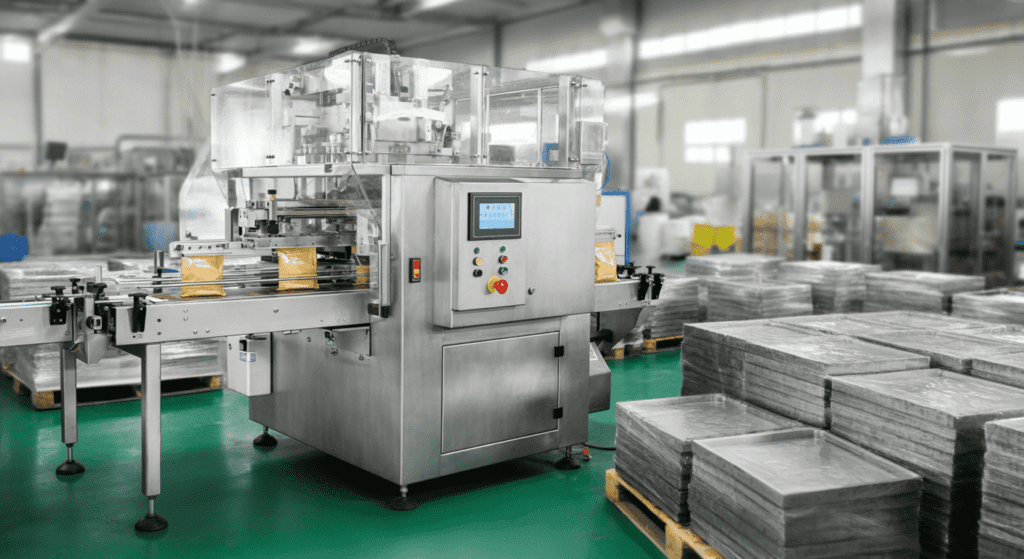
Types of Pouch Sealing Machines
Not all pouch sealing machines are created equal. Depending on the volume of production, budget constraints, and product specifications, you may find one type more suitable than another. Let’s break down the four major categories of pouch sealers.
1. Manual Pouch Sealing Machines
Manual sealers are straightforward, compact, and often the most cost-effective option. They usually require an operator to position the pouch under the sealing element and press down a lever. These machines are popular among home-based businesses or small-scale operations, especially those dealing with modest order volumes.
- Advantages:
- Affordable upfront cost
- Simple to operate
- Minimal maintenance required
- Disadvantages:
- Limited sealing speed
- Heavily reliant on operator consistency
- Not ideal for large-scale production
Real-World Example: A small pastry shop might use a manual sealer to package cookies in custom pouches. This helps maintain freshness while adding a professional finish without breaking the bank.
2. Semi-Automatic Pouch Sealing Machines
Semi-automatic machines strike a balance between manual effort and automated processes. The operator typically loads the pouch into the machine, but the sealing process—temperature control, timing, and pressure—is handled automatically.
- Advantages:
- Faster and more consistent than manual sealers
- Reduces the margin of human error
- Great for medium-volume production
- Disadvantages:
- Higher initial investment compared to manual sealers
- Requires some operator interaction, though less than manual models
Real-World Example: An organic snack brand that packages nuts, dried fruits, and other health foods might leverage a semi-automatic system to keep up with moderate demand and ensure each pouch is sealed to perfection.
3. Automatic & Continuous Band Sealers
Automatic pouch sealing machines—often referred to as continuous band sealers—are built for high throughput. They can operate nonstop on a conveyor belt, sealing hundreds or even thousands of pouches per hour, depending on the model.
- Advantages:
- Significantly higher output
- Consistent seal quality with minimal operator intervention
- Suitable for large-scale manufacturing
- Disadvantages:
- Larger footprint and higher cost
- Requires routine maintenance to keep up with heavy usage
Real-World Example: A commercial coffee roastery distributing products to grocery stores nationwide will often rely on an automatic band sealer, enabling them to process high volumes quickly while maintaining product quality.
4. Vacuum Pouch Sealers
Vacuum sealers remove air from the pouch before sealing, dramatically extending shelf life and preserving product freshness. These machines are commonly used for perishable items such as meats, cheeses, and other food products susceptible to spoilage.
- Advantages:
- Maximized shelf life and freshness
- Protects against oxidation and freezer burn
- Presents a professional, vacuum-packed appearance
- Disadvantages:
- Typically more expensive than standard heat sealers
- Slower operation due to the vacuum process
Real-World Example: A small butcher shop packaging marinated steaks for direct consumer sales will use a vacuum pouch sealer to keep the product fresh longer while offering a professional look.
How to Choose the Right Machine for Your Needs
Selecting the perfect pouch sealing machine is more than a simple matter of budget. You’ll need to consider:
- Production Volume: How many pouches do you expect to seal daily, weekly, or monthly?
- Material Compatibility: Different machines excel at sealing specific materials, be it foil laminates, plastic films, or paper laminates.
- Product Type: Food products often require vacuum sealing or modified-atmosphere packaging, while non-food items might only need a basic heat seal.
- Scalability: Are you looking to expand your production capacity in the near future? A semi-automatic machine may serve as a stepping stone before you invest in a fully automatic system.
- Maintenance and Support: Factor in the availability of spare parts, technician support, and service agreements.
Pro Tip: Before purchasing, request sample tests from your prospective supplier. Most reputable manufacturers will seal your sample pouches to demonstrate the machine’s capabilities, ensuring it meets your standards.
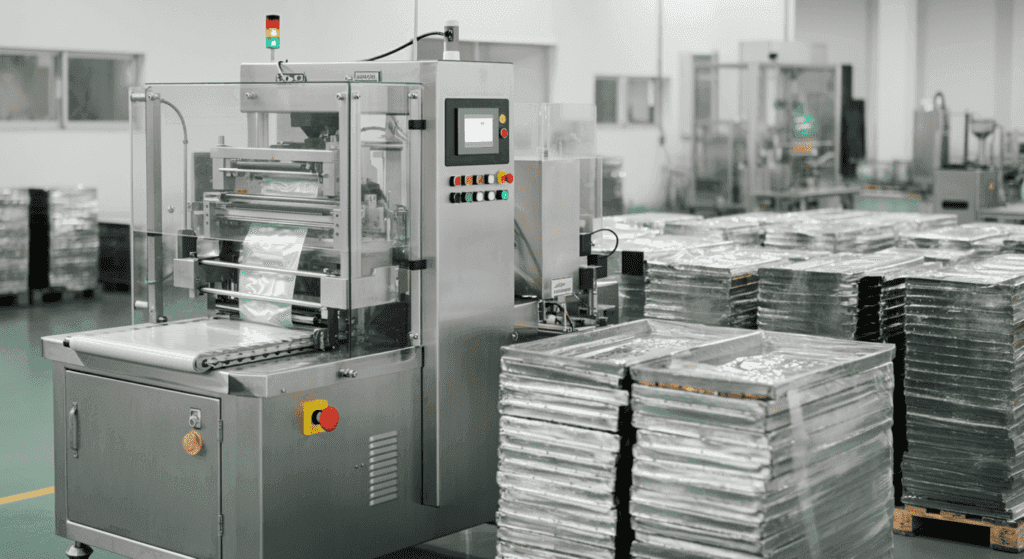
Key Features to Look For
While each business has its own set of priorities, the following features stand out in any decision-making process:
- Adjustable Temperature Controls: This ensures a secure seal across various pouch materials.
- Integrated Cooling System: A built-in cooling bar or fan helps set the seal quickly and consistently.
- Digital Displays & Timers: Provides real-time feedback on sealing time, temperature, and production count.
- Conveyor Speed Regulation (For Automatic Machines): Adjusting the belt speed can accommodate different pouch sizes and fill levels.
- Stainless Steel Construction: Durable and easy to sanitize, especially crucial for food packaging environments.
- Safety Mechanisms: Emergency stops, protective covers, and temperature alarms can prevent accidents and product waste.
- Versatility: Some machines come with attachments to print batch codes, best-before dates, or barcodes directly on the seal.
Bonus Consideration: If your product line includes varying pouch thicknesses, look for a machine with adjustable seal pressure or multiple sealing modes.
Step-by-Step Guide: Operating a Pouch Sealing Machine
Although each model has its own unique operating steps, here’s a high-level process that applies to most pouch sealing machines:
- Power On & Preheat
Turn on the machine and wait until the sealing elements reach the desired temperature. Many machines have indicator lights or digital displays to show when they’re ready. - Adjust Settings
Set your sealing time, temperature, and pressure (if applicable) according to the pouch material you’re using. For thicker materials, you’ll generally need a higher temperature and longer seal time. - Position Your Pouch
Place the pouch carefully under the sealing bar (manual or semi-automatic) or on the conveyor belt for continuous sealers. Make sure the product is adequately positioned inside, with enough space at the top for sealing. - Activate the Machine
Engage the lever (manual), press the start button (semi-automatic), or simply guide the pouch on the conveyor belt (automatic). The machine will apply heat and pressure to fuse the pouch layers. - Cool & Inspect
After sealing, remove the pouch and let the seal cool for a brief moment. Inspect the seal for any irregularities—such as wrinkles or incomplete bonding. - Package & Store
If you’re sealing food items, follow your standard hygiene and labeling protocols. For non-food products, ensure the packaging is tamper-proof and visually appealing.
Maintenance and Care
Regular upkeep is vital to extend the life of your pouch sealing machine and maintain optimal performance.
- Daily Cleaning: Wipe down the sealing bars, conveyor belts, and surrounding areas with a soft cloth or brush to remove debris.
- Weekly Inspection: Check heating elements, rubber pads, and Teflon covers for wear. Replace if they show signs of damage.
- Lubrication: Some machines require periodic lubrication of moving parts. Refer to the manufacturer’s instructions.
- Calibration: Over time, temperature sensors and digital controls may drift. Regular calibration ensures consistent heat application.
- Professional Servicing: Schedule an annual or bi-annual service check, especially for high-capacity machines.
Tip: Keep a logbook of your maintenance activities. Documenting every cleaning, part replacement, and calibration session helps in future troubleshooting and warranty claims.
Common Troubleshooting Tips
Even the best machines encounter hiccups from time to time. Here are common problems and quick fixes:
- Uneven Seal or Wrinkles
- Cause: Improper alignment or inconsistent pressure.
- Fix: Readjust the pouch placement or check if the sealing bar needs recalibration.
- Weak or Leaky Seal
- Cause: Inadequate temperature or a worn-out heating element.
- Fix: Increase the temperature or replace damaged sealing components. Make sure the machine has time to preheat thoroughly.
- Machine Jamming
- Cause: Debris or product remnants caught in the moving parts.
- Fix: Power down the machine and clean it. Ensure no fragments are blocking the conveyor belt or sealing area.
- Excessive Heat Damage
- Cause: Temperature set too high for the pouch material.
- Fix: Lower the seal temperature or reduce the sealing time. Some delicate materials require lower heat and gentler pressure.
- Electrical Issues
- Cause: Blown fuses or faulty wiring.
- Fix: Always consult a professional electrician or authorized service technician. Electrical components can be dangerous to handle.
Industry Applications and Real-World Use Cases
A pouch sealing machine is a versatile solution spanning numerous sectors:
- Food & Beverage: From potato chips to frozen vegetables, these machines preserve flavor and extend shelf life.
- Pharmaceuticals & Supplements: Sealed pouches ensure product integrity, dosage accuracy, and tamper resistance.
- Cosmetics & Personal Care: Shampoos, lotions, and face masks can all be hygienically packaged.
- Industrial & Chemical: Cleaning agents, hardware components, and even small electronic parts benefit from secure, moisture-resistant packaging.
- Agriculture & Gardening: Seeds, fertilizers, and soil additives can be neatly packed for both retail and wholesale markets.
Case Study: A pet food manufacturer upgraded from manual sealing to a continuous band sealer. This shift nearly doubled their daily output and drastically reduced packaging inconsistencies. The investment paid for itself within a year due to reduced labor costs and fewer product returns.
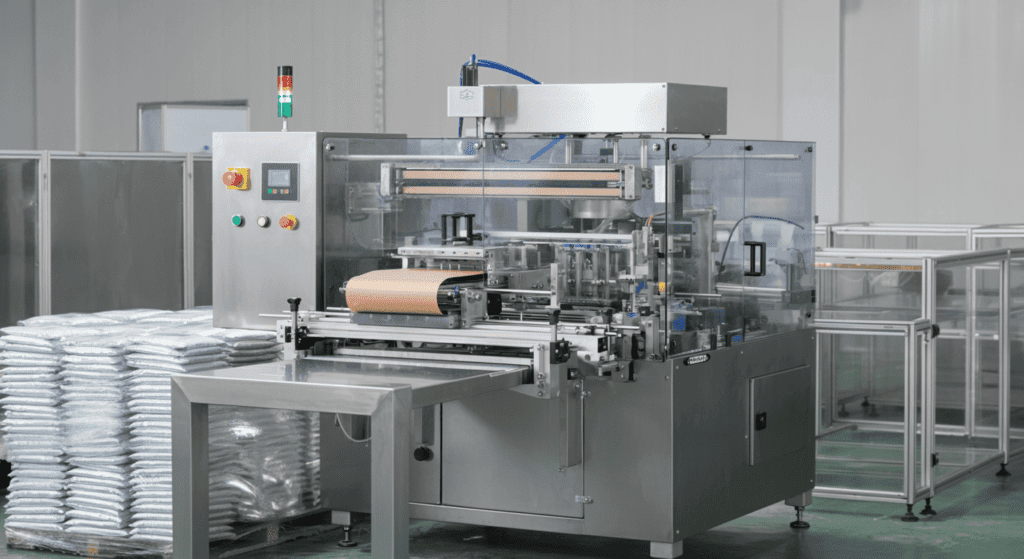
Advanced Packaging Solutions and Innovations
As technology progresses, so do packaging solutions. Modern innovations include:
- Modified Atmosphere Packaging (MAP): Introduces gases like nitrogen to preserve freshness in snack foods and baked items.
- Ultrasonic Sealing: Generates friction and heat using high-frequency vibrations, resulting in a clean, strong seal with minimal material deformation.
- Smart Packaging Sensors: Some pouches feature embedded sensors that indicate temperature exposure or product freshness.
- Eco-Friendly Materials: With rising consumer demand for sustainability, biodegradable and compostable pouch materials are increasingly common.
Looking Ahead: Robotics and AI-driven systems are on the horizon, capable of adaptive sealing techniques based on real-time feedback. This will further reduce human error and boost production efficiency in large-scale operations.
FAQs: Your Most Pressing Questions Answered
1. Can a pouch sealing machine handle different types of pouches?
Yes. Most modern machines have adjustable settings for temperature, pressure, and time, enabling them to seal various materials—from plastic films to foil laminates.
2. How do I know which sealing temperature is right for my pouch?
Check the manufacturer’s specifications for your pouch material. Start with the recommended range, then fine-tune by performing test seals until you achieve a strong, wrinkle-free seal.
3. Is a vacuum sealer always better than a standard heat sealer?
Not necessarily. Vacuum sealers are optimal for perishable goods that need an oxygen-free environment. Standard heat sealers are often sufficient for products that don’t require extended shelf life or specialized storage conditions.
4. Can I integrate a printer or labeler with my pouch sealing machine?
Many automatic and semi-automatic machines have optional attachments for date coding, batch numbering, and labeling, making it easy to comply with regulatory requirements and brand guidelines.
5. How frequently should I service my pouch sealing machine?
For most machines running at moderate capacity, an annual professional check is recommended. High-capacity operations might schedule servicing every six months. Regular daily or weekly cleaning remains essential for all users.
Conclusion and Next Steps
A pouch sealing machine is far more than just a tool for closing bags—it’s a strategic investment in product quality, brand reputation, and operational efficiency. From manual sealers perfect for artisanal batches to fully automated systems tackling industrial-scale packaging, there’s a machine tailored for every business model. By now, you should have a clear understanding of how pouch sealing machines work, the different types available, and the key considerations to keep in mind when making a purchase.
Remember, consistent maintenance is critical. Whether you choose a semi-automatic machine or a top-of-the-line continuous band sealer, proper care ensures that your packaging lines continue to run smoothly, keeping your products fresh and consumers satisfied. If you’re ready to make the switch or upgrade your current setup, start by defining your specific requirements—production volume, pouch materials, and budget—and use the insights from this guide to find a machine that fits like a glove.
Ready to boost efficiency, cut costs, and deliver impeccable packaging every time? Take the next step today by exploring trusted manufacturers, reading user reviews, and even requesting trial runs to confirm a machine’s performance. Feel free to share your experiences or ask any questions in the comments section below. Let’s elevate your packaging game and ensure that every product you seal meets the highest standards of quality and freshness.
Stay Connected with EngiTech
EngiTech is your trusted source for in-depth knowledge on industrial mechanical engineering machines and technologies. Stay ahead with the latest innovations, expert insights, and practical guides designed to help you make informed decisions for your business and engineering needs. Join our growing community of professionals and industry leaders to stay updated and competitive in the ever-evolving world of industrial technology.