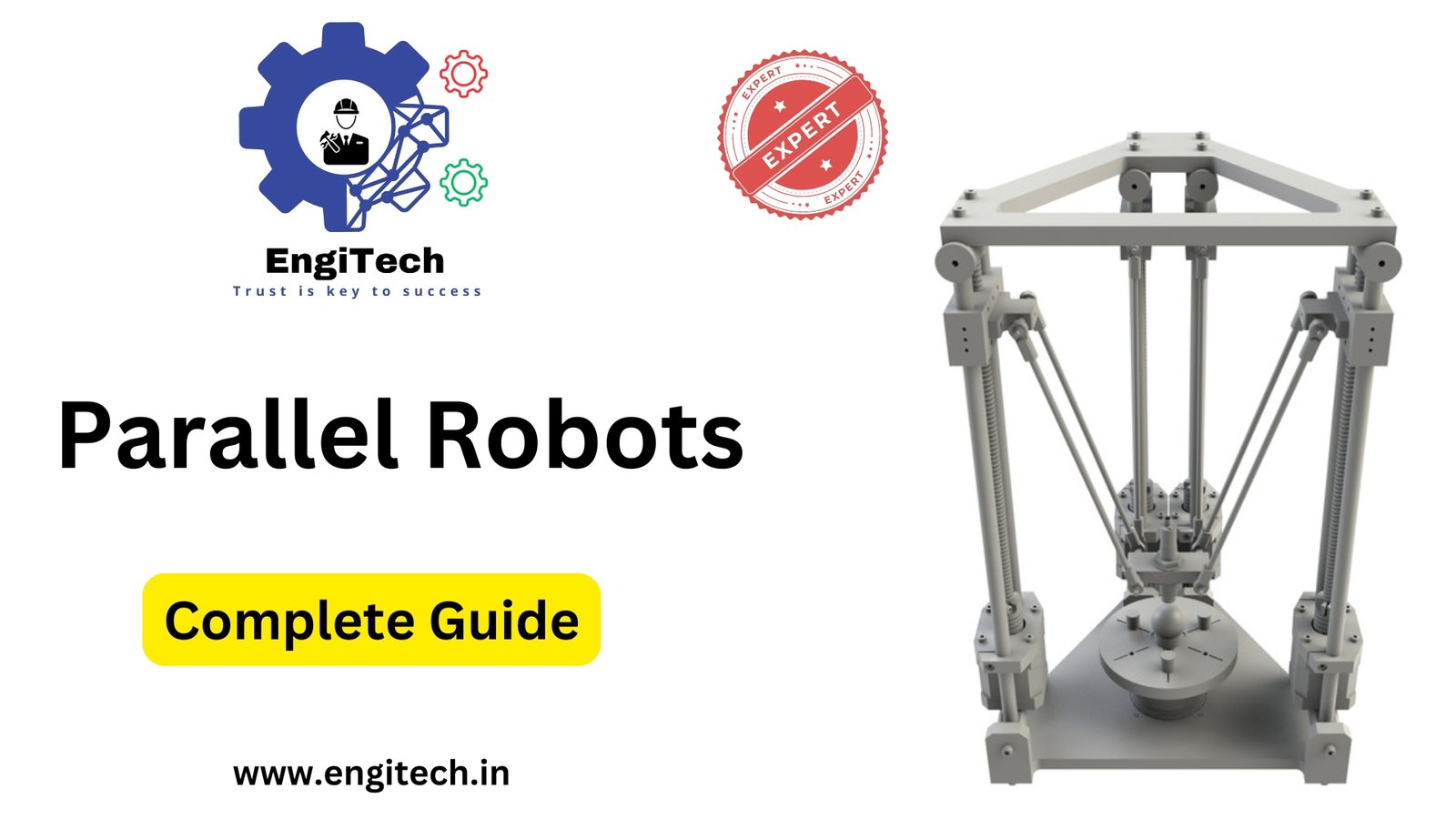
In the ever-evolving landscape of industrial automation, parallel robots are fast becoming a critical component in improving precision, speed, and flexibility in manufacturing processes. But what exactly are parallel robots, and how do they differ from the more common serial robots? More importantly, why should you care about parallel robots if you’re in industries such as automotive, aerospace, electronics, or pharmaceuticals?
In this guide, we will demystify the concept of parallel robots, explain how they work, and explore their numerous applications across various industries. By the end of this blog, you’ll have a comprehensive understanding of how parallel robots can enhance productivity and revolutionize modern manufacturing.
Table of Contents
What Are Parallel Robots?
At their core, parallel robots are mechanical systems where multiple arms are connected to a single platform or end effector. Unlike serial robots, which rely on a chain of linked joints and motors arranged in a series, parallel robots use several arms that operate simultaneously, giving them exceptional precision, speed, and strength.
One of the most iconic examples of parallel robots is the Delta robot, often seen in high-speed pick-and-place operations in food packaging and pharmaceutical industries. The unique design of parallel robots offers several advantages over their serial counterparts, making them ideal for tasks requiring high accuracy and quick movements.
Key Features and Advantages of Parallel Robots
- High Precision and Accuracy
Parallel robots excel in tasks requiring extreme precision, as multiple arms working together provide a more stable structure. This makes them ideal for industries like electronics and pharmaceuticals, where even a tiny margin of error can lead to significant issues. - Speed and Efficiency
Thanks to their structure, parallel robots are incredibly fast. They can carry out quick pick-and-place tasks or high-speed assembly operations without sacrificing accuracy. This efficiency is particularly useful in packaging, food production, and assembly lines. - Compact and Lightweight Design
Parallel robots are generally more compact than serial robots, meaning they take up less space on the factory floor. Their lightweight structure also makes them easier to install and maintain, providing companies with more flexibility in their production lines. - Stiffness and Load Distribution
The design of parallel robots offers excellent stiffness, which allows for higher payload capacities and better load distribution. This is crucial for applications that require strength, such as in aerospace and automotive manufacturing, where heavy parts need to be handled efficiently.
Types of Parallel Robots
There are several different types of parallel robots, each with its own unique applications and benefits. Here are the most common ones:
1. Delta Robots
Delta robots are perhaps the most well-known type of parallel robot. With a tripod-like structure, they are used primarily in high-speed operations such as picking, packing, and sorting. The design enables them to handle delicate and small items with ease.
2. Stewart Platform (Hexapod)
A Stewart platform, also known as a hexapod, features six degrees of freedom, providing motion in all directions (x, y, z axes, plus pitch, roll, and yaw). These robots are commonly used in flight simulators, motion platforms, and surgical applications due to their versatility and precision.
3. Parallel Kinematic Machines (PKM)
PKMs are used in applications that require heavy lifting or extreme precision, such as in machining and assembly. Their structure allows for very high stiffness, making them ideal for tasks requiring a stable platform.
Applications of Parallel Robots Across Industries
Parallel robots are used in a variety of industries, from electronics assembly to food processing. Here are some of the most notable applications:
1. Electronics and Semiconductor Manufacturing
In the electronics industry, precision is key. Parallel robots are commonly used for assembling small, delicate components like semiconductors, where their accuracy ensures that each part is placed perfectly.
2. Pharmaceuticals and Medical Devices
Parallel robots are instrumental in the manufacturing and packaging of pharmaceutical products. They are used in cleanroom environments where precision and speed are crucial, ensuring that medical devices and medications are produced and packaged with care.
3. Automotive Industry
The automotive industry has embraced parallel robots for various tasks, including assembly, welding, and material handling. Their ability to handle heavy payloads with precision makes them ideal for assembling complex car parts.
4. Food and Beverage Industry
From sorting to packaging, Delta robots (a type of parallel robot) are commonly seen in food production lines. Their speed and precision ensure that delicate food items like pastries or chocolates are handled without damage.
How Parallel Robots Work: A Technical Overview
Parallel robots operate using a system of arms connected to a common base and end-effector. The movement of the end-effector is controlled by the simultaneous operation of each arm, which allows for precise control in multiple directions.
Kinematics of Parallel Robots
The kinematic structure of a parallel robot is quite different from that of serial robots. In serial robots, each joint’s movement depends on the previous one, which can lead to a cumulative error. However, in a parallel robot, all actuators control the end-effector simultaneously, reducing the margin of error.
Actuators and Motors
Parallel robots rely on several actuators and motors, usually located at the base, to control the movement of the arms. These actuators work together, adjusting the arms’ angles and lengths to position the end-effector exactly where it needs to be.
Control Systems
Modern parallel robots use sophisticated control systems to ensure precise movement and operation. These systems continuously calculate the required movements and positions of each arm, ensuring smooth and accurate motion even at high speeds.
Parallel Robots vs. Serial Robots: Key Differences
When considering whether to use a parallel robot or a serial robot for your operations, it’s essential to understand the key differences between the two types.
- Precision and Accuracy
Parallel robots are more accurate due to their structure, which reduces cumulative errors found in serial robots. - Speed
Parallel robots are faster than serial robots, making them ideal for high-speed applications like pick-and-place tasks. - Payload Capacity
While parallel robots offer excellent precision, they may not always handle as heavy loads as some serial robots. However, they compensate for this with their superior load distribution. - Complexity of Movement
Serial robots can perform more complex movements than parallel robots due to their articulated design, but parallel robots outperform in terms of precision and speed.
The Future of Parallel Robots in Automation
As industries continue to evolve, so will the role of parallel robots in industrial automation. With advancements in AI and machine learning, the capabilities of parallel robots are expanding, enabling them to handle even more complex tasks.
Integration with Artificial Intelligence
One exciting future prospect is the integration of parallel robots with AI technologies. By combining real-time data processing with intelligent decision-making, parallel robots will be able to adapt to more complex environments and tasks without human intervention.
Collaborative Parallel Robots
In the near future, we can also expect to see collaborative parallel robots, or cobots, that work alongside humans. These cobots will be designed to assist with tasks that require both human intuition and robotic precision, offering the best of both worlds.
Conclusion: Why Invest in Parallel Robots?
Investing in parallel robots is a strategic decision that can dramatically improve the efficiency, accuracy, and speed of your production processes. Whether you’re in electronics, pharmaceuticals, automotive, or food processing, parallel robots provide the precision and reliability needed to stay competitive in today’s fast-paced industrial landscape.
As industrial automation continues to evolve, parallel robots are set to play an even more significant role. By embracing these robots now, you position your company to lead the way in efficiency, productivity, and innovation.
If you’re ready to revolutionize your manufacturing process with parallel robots, visit EngiTech today to explore more about the latest advancements in industrial automation and stay updated with expert insights. Let’s shape the future of automation together!