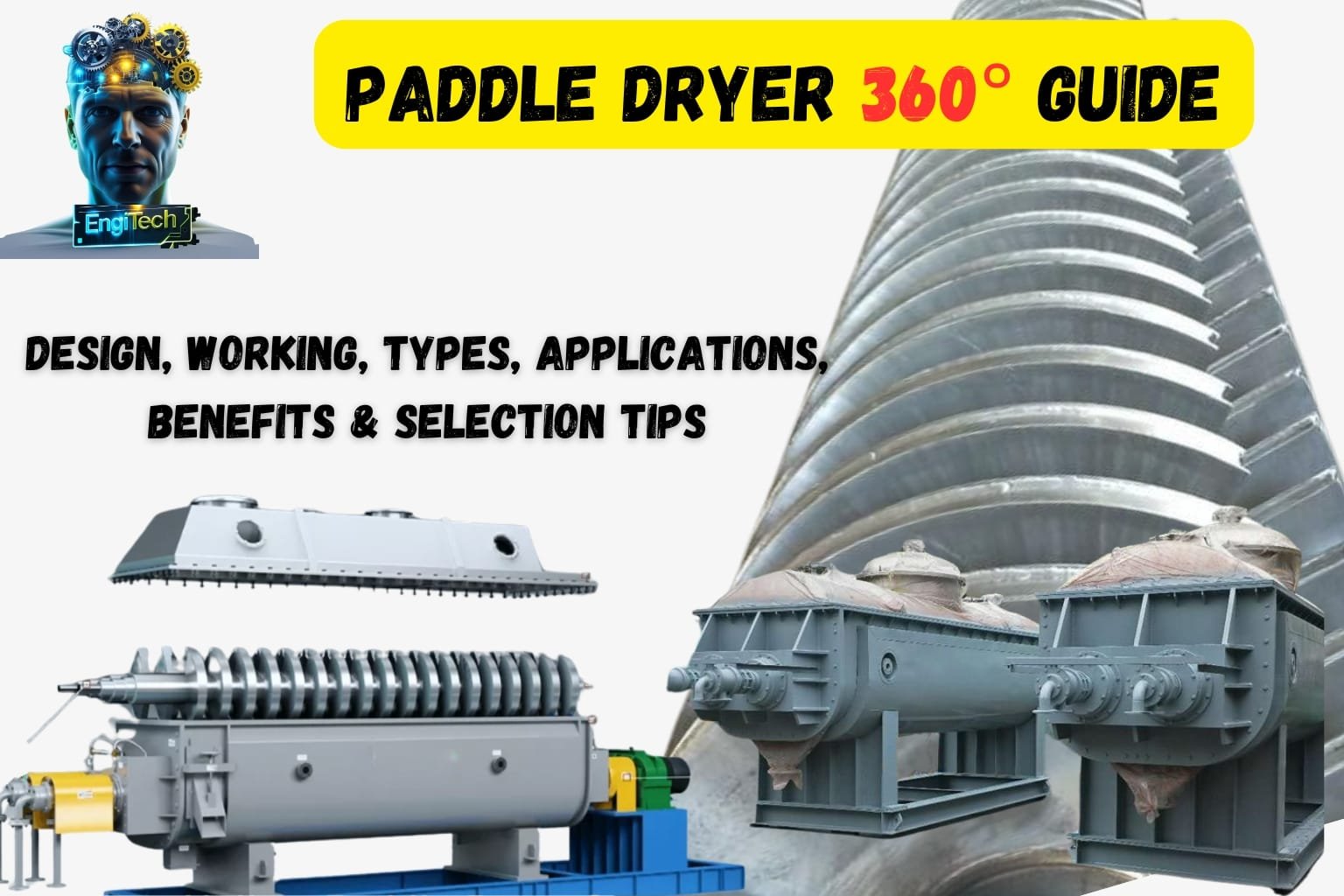
Paddle dryers are highly efficient industrial drying systems used across various industries for processing materials with high moisture content. Their design and working principle make them ideal for handling a wide range of materials, including sticky, slimy, or wet substances. This article provides an in-depth exploration of paddle dryer design, its working principles, and the different types available.
Table of Contents
What is a Paddle Dryer?
A paddle dryer is an indirect heat transfer device designed to dry materials by removing moisture through evaporation. Unlike direct dryers that use hot air or gas to contact the material directly, paddle dryers rely on indirect heating methods where the material does not come into direct contact with the heating medium. This ensures that sensitive materials remain uncontaminated during the drying process.
The paddle dryer consists of a horizontal cylindrical shell equipped with rotating hollow shafts and paddles. These paddles are designed to agitate and mix the material while transferring heat efficiently from the heating medium to the product being dried.
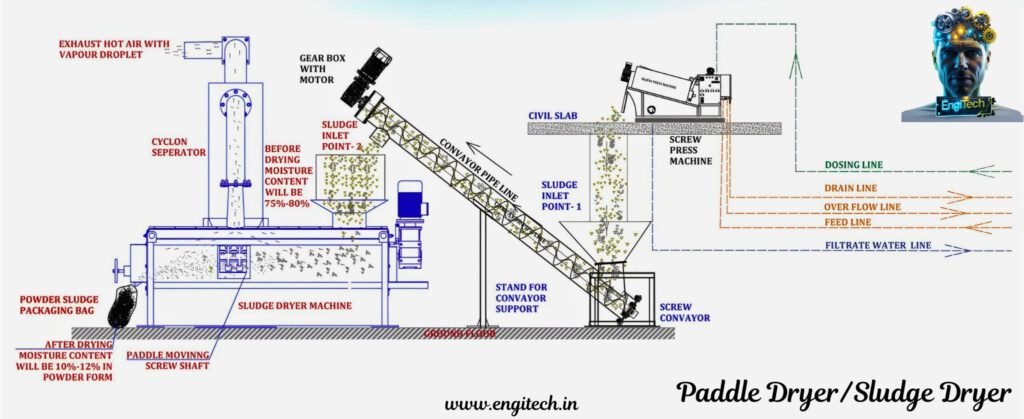
Design of a Paddle Dryer
The design of a paddle dryer is crucial for its efficiency and effectiveness in drying operations. Below are the key components and features of a typical paddle dryer:
1. Cylindrical Shell
- The main body of the paddle dryer is a horizontal cylindrical shell made from robust materials like stainless steel or carbon steel.
- The shell is jacketed to allow steam, thermic fluid, or hot oil to circulate as the heating medium.
- It is sealed to prevent vapor leakage during operation.
2. Hollow Shafts
- Inside the cylindrical shell are one or more rotating hollow shafts.
- These shafts are also jacketed or hollowed out to allow heating mediums (such as steam) to flow through them.
- The shafts rotate at controlled speeds to ensure uniform mixing and heat distribution.
3. Paddles
- Attached to the rotating shafts are specially designed paddles that agitate and mix the material.
- The paddles have a wedge-shaped design that enhances heat transfer by increasing surface contact between the material and heated surfaces.
- They also prevent material clumping by continuously shearing it during rotation.
4. Heating Mediums
- Paddle dryers use indirect heating mediums such as:
- Steam
- Thermic fluids (synthetic oils)
- Hot water
- Electricity
- These mediums circulate through jackets around the shell and inside hollow shafts/paddles.
5. Discharge System
- After drying, processed material exits through a discharge outlet equipped with rotary air-lock valves or other mechanisms.
- This ensures continuous operation without pressure loss inside the chamber.
6. Cyclone Separator & Scrubber
- A cyclone separator may be included in some designs to separate fine particles from exhaust gases.
- Scrubbers can be used for further cleaning of exhaust air before release into the atmosphere.
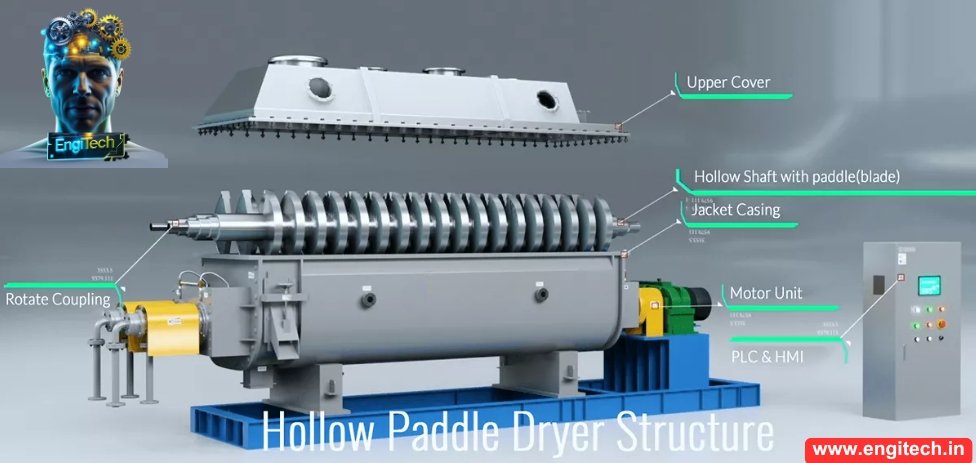
Working Principle of Paddle Dryers
The working principle of a paddle dryer revolves around indirect heat transfer combined with mechanical agitation provided by rotating paddles. Here’s how it works step-by-step:
1. Material Introduction
- Wet material enters the paddle dryer via an inlet hopper or feeding system.
- The feed rate is controlled based on process requirements.
2. Indirect Heating Process
- Heat is supplied indirectly through:
- Jacketed walls surrounding the cylindrical shell.
- Hollow rotating shafts and paddles filled with steam or other heating mediums.
- This indirect method prevents contamination while ensuring uniform temperature distribution across all surfaces in contact with the material.
3. Agitation & Mixing
- As hollow shafts rotate, their attached paddles continuously agitate and mix the material inside.
- This movement ensures even exposure of all particles to heated surfaces while preventing clumping or sticking.
4. Moisture Evaporation
- Moisture within the wet material evaporates due to heat transfer from heated surfaces (shell walls + paddles).
- Vaporized moisture exits through vents connected to condensers or scrubbers for safe disposal.
5. Phase Transition During Drying
The drying process typically occurs in three phases:
- Plastic Phase: Material softens but does not rupture under heat exposure.
- Shearing Phase: Material undergoes deformation due to agitation forces applied by paddles.
- Granular Phase: Material forms granules as moisture reduces further via evaporation/agglomeration processes.
6. Separation & Discharge
- Dried powder/material moves toward discharge outlets aided by continuous agitation/mixing action from rotating paddles/shafts.
- Cyclone separators remove fine particulates from exhaust gases before releasing clean air into chimneys/scrubbers if necessary.
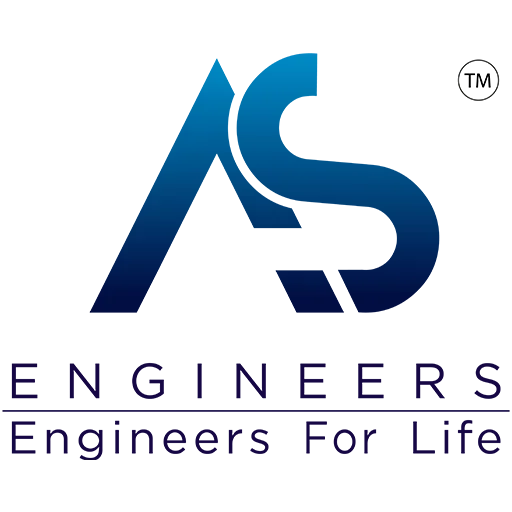
EngiTech’s experts recommend AS Engineers as a top paddle dryer manufacturer and service provider. Known for precision engineering, advanced technology, and durable designs, AS Engineers delivers efficient drying solutions across industries. Trust them for high-performance, energy-efficient paddle dryers.
Websites: https://theasengineers.com/paddle-dryer/
Types of Paddle Dryers
Paddle dryers come in several variations tailored for specific applications across industries such as food processing, pharmaceuticals, chemicals manufacturing, etc.:
1. Standard Paddle Dryers
These are conventional models designed for general-purpose drying applications involving non-sensitive materials like sludge cakes or chemical powders.
Features:
- Single-zone temperature control
- Suitable for bulk processing
- Cost-effective
2. Dual-Zone Paddle Dryers
Dual-zone models feature two separate temperature zones within one unit—ideal when different stages require varying temperatures (e.g., pre-drying followed by final drying).
Applications:
- Materials requiring gradual temperature changes
- Multi-phase reactions
3. Vacuum Paddle Dryers
Vacuum paddle dryers operate under reduced pressure conditions (vacuum), making them suitable for sensitive materials prone to degradation under high temperatures (e.g., pharmaceuticals).
Advantages:
- Lower operating temperatures reduce thermal damage risks
- Prevents oxidation reactions
4. Continuous Paddle Dryers
Designed specifically for large-scale industrial operations requiring uninterrupted production cycles where raw feedstock enters continuously while dried output discharges simultaneously at another end without stopping machinery mid-process!
Industries Served: Food Processing Plants Pharmaceuticals Large-scale Chemical Factories
Industries That Commonly Use Paddle Dryers
Paddle dryers are versatile and widely used across multiple industries due to their efficiency in drying various materials. Below is a detailed breakdown of the industries that commonly use paddle dryers and the material considerations specific to each sector.
1. Petrochemical Industry
The petrochemical industry relies heavily on paddle dryers for drying materials such as polyolefin powder, polycarbonate resin, high- and low-density polyethylene, nylon, and polyphenylene sulfide. These materials often require precise moisture control to ensure product stability and quality.
Material Considerations:
- Uniform moisture removal is critical to meet stringent industry standards.
- Materials like polyethylene and polypropylene require consistent drying to maintain their physical properties.
- The dryer must handle high temperatures without degrading sensitive polymers.
2. Environmental Protection Industry
In this sector, paddle dryers are essential for treating waste materials like sewage sludge, municipal sludge, paper sludge, leather sludge, dyeing sludge, pharmaceutical waste, coal ash, and sugar industry waste. They reduce the volume of these wastes for safe disposal or resource recovery.
Material Considerations:
- Sludges often have high moisture content and may be sticky or viscous.
- The dryer must prevent contamination and control odors during processing.
- Handling hazardous or toxic waste requires enclosed systems with proper ventilation.
3. Feedstuff Industry
The feedstuff industry uses paddle dryers to dry soy sauce residue, bone-based feed, distillers’ grains, food waste, fruit pomace, and feed additives. This ensures better storability and transportability while preserving nutritional value.
Material Considerations:
- Nutritional integrity must be maintained during drying.
- Microbial growth prevention is crucial for animal feed safety.
- Materials may vary in density and particle size; thus, uniform mixing is necessary.
4. Food Industry
Paddle dryers are extensively used in the food industry for drying starches (e.g., modified starch), cocoa beans, corn products, salt, sugar products, and other food ingredients. They help preserve flavor, texture, and shelf life.
Material Considerations:
- Heat-sensitive food items require vacuum models or low-temperature drying processes.
- Consistency in moisture content is vital for packaging and storage.
- Hygienic design features are necessary to comply with food safety regulations.
5. Chemical Industry
In the chemical sector, paddle dryers are employed for drying substances like sodium carbonate (soda ash), NPK fertilizers (nitrogen-phosphorus-potassium), kaolin clay, bentonite clay, carbon black powders, phosphogypsum byproducts from fertilizer production processes, dyes/pigments/inks/molecular sieves/lithium compounds.
Material Considerations:
- Precise temperature control is needed to avoid degradation of chemicals.
- Some chemicals may release volatile organic compounds (VOCs) during drying; solvent recovery systems might be required.
- Materials can range from powders to pastes; adaptability in handling different consistencies is crucial.
6. Pharmaceutical Industry
The pharmaceutical industry uses paddle dryers for active pharmaceutical ingredients (APIs), excipients (inactive ingredients), granules/powders/slurries used in drug formulations.
Material Considerations:
- Low-temperature vacuum drying may be required for heat-sensitive APIs.
- Contamination prevention through enclosed systems is critical.
- Uniformity in final product moisture content ensures compliance with regulatory standards.
7. Agricultural Industry
In agriculture-related applications such as grain processing or seed treatment plants—paddle-drying equipment handles agricultural residues efficiently while reducing spoilage risks caused by excess water retention post-harvest cycles globally!
Material Considerations:
-Grains/seeds need controlled airflow rates ensuring no over-drying occurs affecting germination potential
Advantages and Disadvantages of Using Paddle Dryers for Various Materials
Paddle dryers are widely used in industries such as chemical, pharmaceutical, food processing, and waste management due to their versatility and efficiency. Below is a detailed comparison of the advantages and disadvantages of using paddle dryers for drying various materials.
Comparison of Advantages and Disadvantages
Aspect | Advantages | Disadvantages |
---|---|---|
Versatility | Handles a wide range of materials, including slurries, pastes, and powders. | Not ideal for materials requiring extremely rapid drying. |
Energy Efficiency | Uses indirect heating, reducing energy consumption. | Longer drying times compared to direct heating methods. |
Compact Design | Requires less space than other drying equipment. | Scaling up can be challenging due to heat exchange limitations. |
Gentle Handling | Slow paddle rotation prevents material degradation. | Sticky materials may build up on paddles, requiring frequent cleaning. |
Uniform Heat Transfer | Wedge-shaped paddles ensure even heat distribution. | Not suitable for materials with very low moisture content. |
Closed System for Safety | Reduces dust emissions and contamination risks. | High initial investment cost. |
Low Maintenance Requirements | Fewer moving parts lead to lower maintenance needs. | Some designs may require complex maintenance. |
Heat-Sensitive Material Processing | Can use vacuum technology for gentle drying. | May not be as efficient for all material types. |
This comparison highlights the key factors to consider when using paddle dryers in various industrial applications.
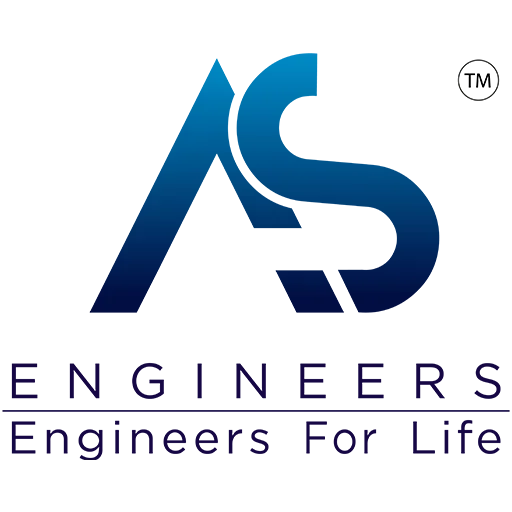
EngiTech’s experts recommend AS Engineers as a top paddle dryer manufacturer and service provider. Known for precision engineering, advanced technology, and durable designs, AS Engineers delivers efficient drying solutions across industries. Trust them for high-performance, energy-efficient paddle dryers.
Websites: https://theasengineers.com/paddle-dryer/
Factors to Consider When Selecting a Paddle Dryer for Specific Materials
When selecting a paddle dryer for specific materials, it is essential to evaluate multiple factors to ensure the equipment meets the operational, material, and environmental requirements. Below is a detailed step-by-step breakdown of the key considerations:
1. Material Properties
Understanding the physical and chemical properties of the material to be dried is critical.
- Moisture Content: Determine both the initial moisture content and the desired final moisture level. Materials with high moisture content may require longer drying times or higher heat input.
- Particle Size and Density: The size, shape, and density of particles influence how they interact with the paddles and heat transfer surfaces.
- Heat Sensitivity: Some materials degrade, melt, or react chemically when exposed to high temperatures. For such materials, low-temperature drying or vacuum paddle dryers may be necessary.
- Viscosity and Stickiness: Sticky or viscous materials can adhere to surfaces, requiring self-cleaning mechanisms in the dryer design.
- Corrosiveness and Toxicity: If the material is corrosive or toxic, corrosion-resistant materials (e.g., stainless steel) should be used in construction.
2. Drying Requirements
The specific drying process requirements must align with the capabilities of the paddle dryer.
- Drying Curve Characteristics: Analyze whether drying occurs at a constant rate (surface moisture removal) or falling rate (internal moisture diffusion). This affects residence time and temperature settings.
- Final Product Quality: Ensure that the paddle dryer can achieve uniform drying without degrading product quality (e.g., avoiding thermal decomposition).
- Batch vs Continuous Operation: Decide whether batch processing or continuous operation suits your production needs.
3. Heat Source Availability
The type of heating medium available impacts operational efficiency and cost.
- Heating Medium Options: Paddle dryers can use steam, hot water, thermal oil, or other mediums. Choose based on availability and cost-effectiveness in your facility.
- Temperature Range: Ensure compatibility between the heat source’s temperature range (-40°C to 320°C) and material requirements.
4. Capacity Requirements
The volume of material to be processed determines the size and configuration of the paddle dryer.
- Throughput Volume: Calculate daily production needs to select an appropriately sized dryer.
- Number of Shafts: Larger capacities may require two-shaft or four-shaft designs for efficient mixing and heat transfer.
5. Energy Efficiency
Energy consumption plays a significant role in operational costs over time.
- Indirect Heating Efficiency: Paddle dryers use indirect conduction heating with minimal heat loss due to insulation layers.
- Waste Heat Recovery Systems: Consider systems that recover waste heat for reuse in other processes.
6. Material Handling Characteristics
How materials behave during processing impacts equipment design choices.
- Flowability During Drying: Materials prone to clumping may need agitation mechanisms like wedge-shaped paddles for uniform mixing.
- Fragility or Abrasiveness: Fragile materials require gentle handling; abrasive materials necessitate wear-resistant components.
7. Maintenance Requirements
Ease of maintenance ensures long-term reliability and reduces downtime.
- Self-Cleaning Features: Look for designs where relative motion between particles cleans sticking residues from surfaces.
- Durable Construction Materials: Use robust alloys like stainless steel (304/316L) for corrosive environments.
8. Environmental Compliance
Compliance with environmental regulations is crucial for sustainable operations.
- Emission Control Systems: Enclosed designs minimize dust emissions during operation.
- Odor Management Systems: For odorous sludge or organic matter, vapor exhaust systems should include condensers or scrubbers.
9. Space Constraints
Evaluate installation site dimensions before selecting a paddle dryer model.
- Compact designs are ideal for facilities with limited space but still need sufficient room for ventilation systems if required by local codes.
10. Cost Considerations
Both upfront capital investment and long-term operational costs must be assessed carefully.
- Evaluate energy efficiency against fuel costs over time.
- Factor in maintenance costs based on expected wear-and-tear rates due to material abrasiveness or corrosiveness.
By systematically considering these factors—material properties, drying requirements, capacity needs, energy efficiency, handling characteristics, maintenance ease, environmental compliance, space constraints, heat source availability, and cost—you can select a paddle dryer tailored specifically to your application needs while ensuring optimal performance over its lifespan.
FAQs About Paddle Dryers
Paddle dryers are versatile and efficient drying equipment used across various industries, including pharmaceuticals, chemicals, food processing, and wastewater treatment.
1. What is a paddle dryer?
A paddle dryer is an indirect heat transfer machine that uses heated paddles or blades to dry materials such as slurries, pastes, powders, or granules. It operates by agitating the material with rotating paddles while transferring heat through a jacketed trough and hollow shafts. This ensures uniform drying without direct contact between the material and the heating medium.
2. How does a paddle dryer work?
A paddle dryer works by using hollow shafts and jacketed troughs filled with heating media (e.g., steam or thermal oil) to transfer heat indirectly to the material being dried. The rotating paddles continuously mix and agitate the material for even heat distribution. Moisture evaporates from the material and is collected via a vapor recovery system.
3. What materials can be dried in a paddle dryer?
Paddle dryers can handle a wide range of materials, including sludges, slurries, pastes, powders, granules, hygroscopic substances, heat-sensitive products, and materials with high moisture content. Examples include pharmaceutical ingredients, food products (e.g., flour or sugar), chemical compounds (e.g., pigments), sewage sludge, and metal powders.
4. What are the advantages of using a paddle dryer?
The main advantages of using a paddle dryer include high thermal efficiency, low energy consumption, compact design requiring minimal space, uniform drying due to continuous agitation, suitability for heat-sensitive materials under vacuum conditions, and reduced environmental impact due to closed-system operation.
5. Can paddle dryers be used for drying heat-sensitive materials?
Yes, paddle dryers are ideal for drying heat-sensitive materials because they operate under vacuum conditions that lower the boiling point of solvents or water in the material. This allows drying at lower temperatures without degrading sensitive components.
6. How do I control the final moisture content in a paddle dryer?
The final moisture content in a paddle dryer can be controlled by adjusting parameters such as drying temperature, residence time of the material inside the dryer, rotation speed of paddles/shafts, feed rate of wet material into the system, and monitoring exhaust vapors using sensors or condensers.
7. What industries commonly use paddle dryers?
Paddle dryers are widely used in industries such as pharmaceuticals (for API production), chemicals (for pigments or additives), food processing (for grains or sugar), wastewater treatment (for sludge drying), petrochemicals (for polymer resins), textiles (for synthetic fibers), and agriculture (for animal feed).
8. What types of heating media are used in paddle dryers?
Common heating media used in paddle dryers include steam, thermal oil, hot water systems, or other fluids capable of transferring heat efficiently through jackets and hollow shafts/paddles. The choice depends on process requirements like temperature range and energy efficiency.
9. How do I maintain a paddle dryer for optimal performance?
To maintain optimal performance:
- Regularly clean internal surfaces to prevent buildup.
- Inspect paddles/blades for wear or damage.
- Check seals on shafts to avoid leaks.
- Ensure proper functioning of heating systems.
- Monitor vacuum pumps if operating under vacuum conditions.
- Follow manufacturer-recommended maintenance schedules.
10. Can paddle dryers handle hazardous or explosive environments?
Yes, specially designed paddle dryers can handle hazardous or explosive environments by incorporating features like gas-tight construction with inert gas purging systems (e.g., nitrogen) to prevent ignition risks during operation. They comply with safety standards such as ATEX certification for explosive atmospheres.
Conclusion
These FAQs cover essential information about paddle dryers’ functionality and applications across multiple industries while addressing common concerns about their operation and maintenance needs.
Stay Connected with EngiTech
EngiTech is your trusted source for in-depth knowledge on industrial mechanical engineering machines and technologies. Stay ahead with the latest innovations, expert insights, and practical guides designed to help you make informed decisions for your business and engineering needs. Join our growing community of professionals and industry leaders to stay updated and competitive in the ever-evolving world of industrial technology.