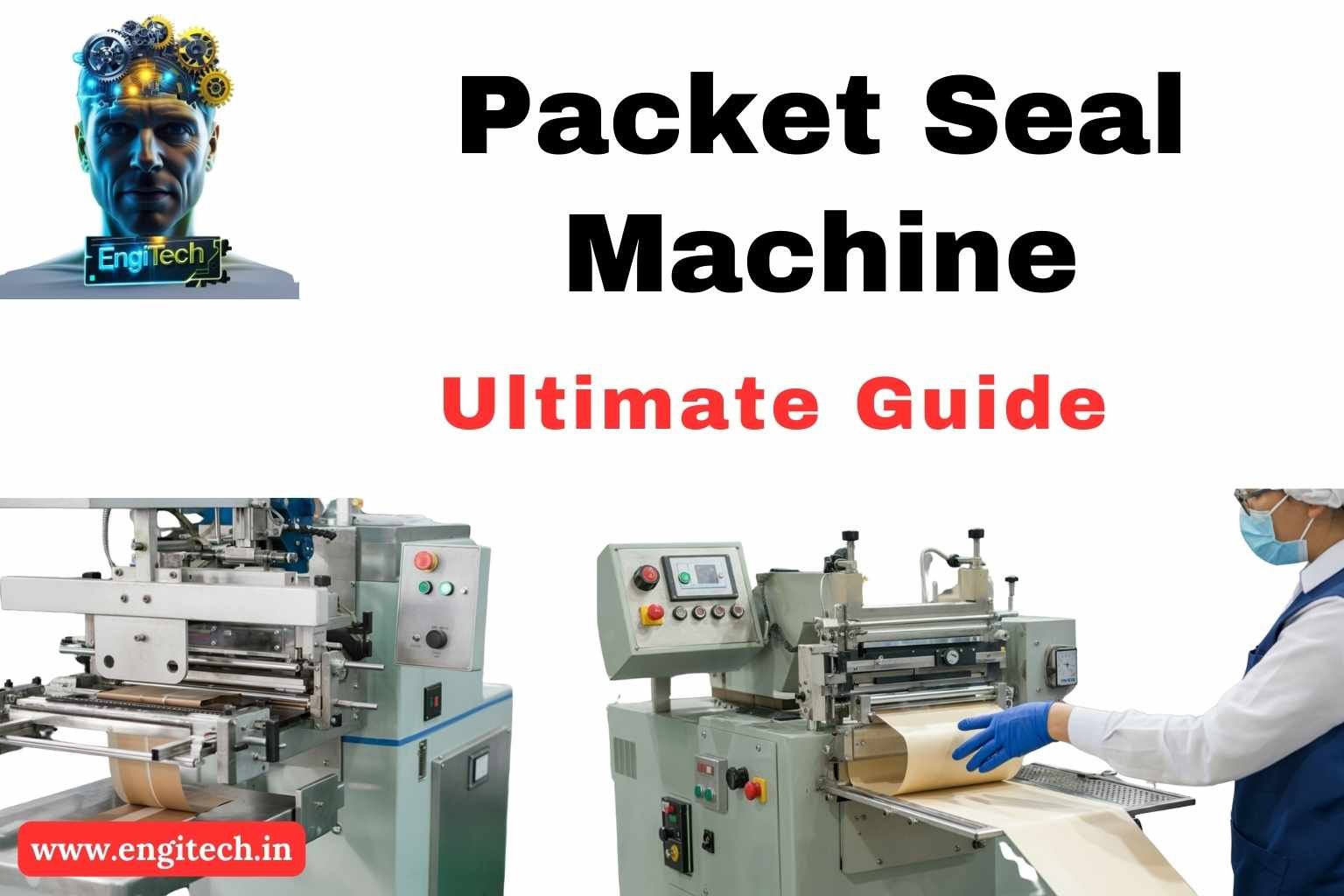
Have you ever wondered how those perfectly sealed packets of chips, spices, or small hardware items make it from the factory to store shelves without spilling a single crumb or screw? The answer often lies in a packet seal machine, a piece of automated packaging technology responsible for preserving product freshness, safety, and overall quality.
In today’s rapidly evolving market, consumers demand efficient packaging that looks great, guards against contaminants, and extends shelf life. If you’re looking to optimize your packaging process—whether you’re a budding entrepreneur or a seasoned industry professional—this in-depth guide will arm you with all the insights you need.
In the next few thousand words, you’ll discover everything about packet seal machines, including how they work, what features to look for, the different types available, and even some lesser-known tips to help you master the art of packaging. By the end of this guide, you’ll have a solid grasp of the technology, allowing you to make well-informed decisions for your business or personal projects.
Table of Contents
1. What Is a Packet Seal Machine?
A packet seal machine—also known in some circles as a pouch sealing machine or bag sealing equipment—is a specialized piece of industrial or commercial machinery designed to close (or seal) packets, pouches, or bags securely. The goal is to protect the product inside from external contaminants like moisture, dust, or bacteria while maintaining the integrity of the contents for an extended shelf life. These machines utilize heat, pressure, or specialized adhesives to form airtight seals that prevent leaks and preserve freshness.
Packet seal machines come in various shapes, sizes, and functionalities. Some are stand-alone devices designed for smaller businesses and home-based operations, while others are large, fully automated systems integrated into high-volume packaging lines.
2. Why Packet Seal Machines Matter
Imagine walking through a grocery store. Notice the countless products—from snack foods and spices to coffee and pet treats—neatly displayed in secure, sealed bags. These items rely on packet seal machines to deliver quality and freshness to consumers.
- Product Safety and Freshness: Proper sealing prevents spoilage, contamination, and waste.
- Extended Shelf Life: Many food products can stay fresh longer when sealed properly.
- Professional Presentation: A well-sealed package looks high-quality and consistent, boosting consumer trust.
- Reduced Costs: Minimizing product loss and extending shelf life can help companies save money over time.
- Eco-Friendly Options: Many modern machines support biodegradable or eco-friendly packaging materials, appealing to environmentally conscious consumers.
In a world where customer satisfaction and brand reputation hinge on product quality, investing in the right packet seal machine can significantly impact your bottom line and consumer perception.
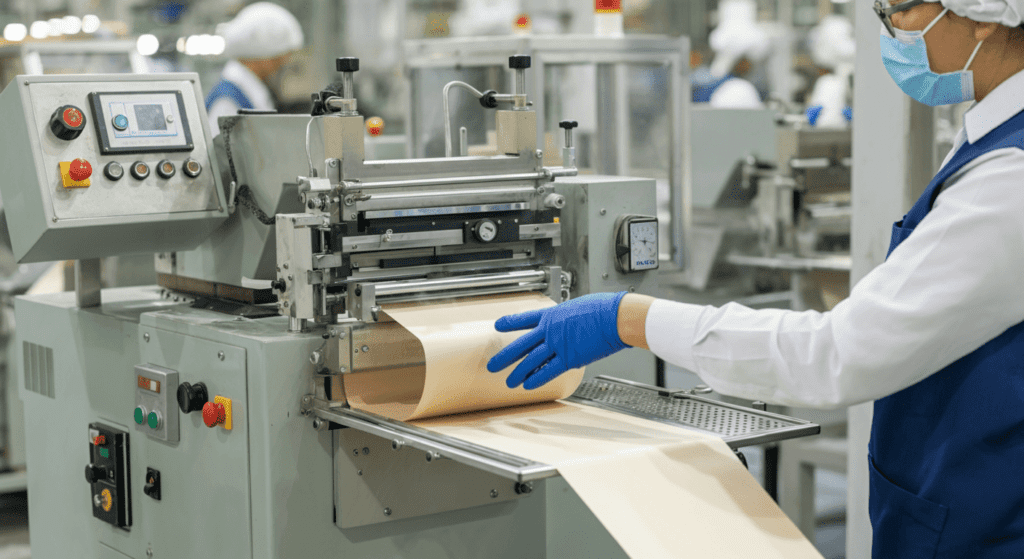
3. How a Packet Seal Machine Works
While models vary, most packet seal machines operate under similar principles. Understanding these fundamentals will help you troubleshoot issues or optimize efficiency.
3.1 Heating or Bonding Elements
Most machines use a heating element or bonding component to fuse the layers of plastic or specialized packaging materials. When heat is applied at just the right temperature, the materials melt together at the seam, forming an airtight seal.
3.2 Pressure and Cooling
Pressure is often applied to ensure the seam fuses completely. Once sealed, a cooling mechanism helps the newly formed seal set, preventing it from reopening or weakening.
3.3 Automated or Manual Feeding
In large-scale operations, bags or pouches often flow along a conveyor, and the machine detects the bag’s position using sensors. In smaller operations, an operator might manually place each pouch in the sealing area.
3.4 Quality Control
Many advanced systems come equipped with sensors or vision systems that check for incomplete seals, wrinkles, or air leaks. If a defect is detected, the bag may be automatically rejected to maintain quality standards.
Expert Insight:
Modern technologies, like ultrasonic sealing, offer minimal energy consumption and can handle an array of packaging materials. While slightly more expensive initially, these technologies can yield long-term cost savings through reduced material wastage and downtime.
4. Types of Packet Seal Machines
Selecting the right packet seal machine often depends on your production volume, material compatibility, and specific operational needs. Below are some common varieties:
4.1 Impulse Sealers
- Ideal For: Small businesses or low-volume sealing
- How They Work: Heat is generated only when the sealing arm is lowered, making them energy-efficient
- Pros & Cons: Affordable and straightforward, but not ideal for high-speed applications
4.2 Constant Heat Sealers
- Ideal For: Mid-range production volumes
- How They Work: The sealing bar stays hot continuously, ensuring quicker sealing times
- Pros & Cons: Faster throughput than impulse sealers, but can consume more power and require careful temperature control
4.3 Band Sealers
- Ideal For: Medium to high-volume operations
- How They Work: Features a conveyor belt that continuously moves pouches through a heated sealing section
- Pros & Cons: Highly efficient, but typically requires a dedicated production line and higher upfront cost
4.4 Vertical Form Fill Seal (VFFS) Machines
- Ideal For: Large-scale packaging in food and beverage industries
- How They Work: Forms the bag from roll stock, fills it with product, and seals it—often in one continuous process
- Pros & Cons: Extremely fast and automated, but more expensive and requires a skilled workforce for setup and operation
4.5 Rotary Sealers
- Ideal For: Laboratory or specialized medical applications
- How They Work: Use rotating rollers to apply heat and pressure, ideal for sealing medical pouches
- Pros & Cons: Ideal for sterile packaging, but not as versatile for broader consumer goods
In addition to these, new hybrid and specialized sealing machines are constantly emerging, catering to niche demands such as resealable zippers or spout pouches.
5. Key Features to Look For
Choosing a packet seal machine involves more than just grabbing the first model you see on sale. Prioritize the following features to get the best fit for your needs:
- Material Compatibility: Ensure the machine supports the types of film or pouch materials you intend to use (e.g., polyethylene, polypropylene, laminated films, biodegradable materials).
- Speed and Throughput: Consider the machine’s sealing rate (packs per minute) relative to your production goals.
- Sealing Width and Length: Different products require different bag sizes. Make sure the machine can accommodate your widest packages.
- Temperature Control: Precise heat settings can mean the difference between a perfect seal and a disastrous meltdown.
- Maintenance Requirements: Some machines require frequent part replacements; factor in ongoing costs and downtime.
- Automation Level: Fully automated machines can significantly reduce labor but come with a higher price tag.
- Ease of Use: User-friendly interfaces and clear instructions can save you time and training costs.
- Safety Mechanisms: Look for machines with built-in safety features like emergency stops, heat guards, or sensor-based shutoffs.
Pro Tip:
Ask for a demonstration or trial run if possible. Observing how the machine handles your specific packaging materials can provide invaluable insights.
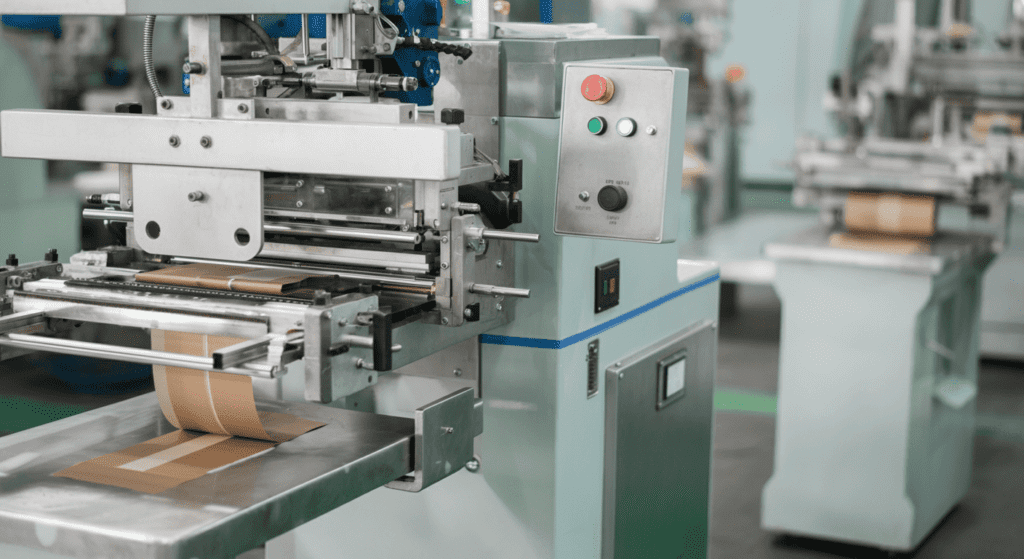
6. How to Choose the Right Packet Seal Machine
Selecting the most suitable packet seal machine boils down to balancing your production requirements, budget, and operational constraints. Here’s a step-by-step process to guide your decision:
Step 1: Define Your Production Needs
- Volume Requirements: Is your output in the hundreds, thousands, or millions of units per day?
- Packaging Sizes: Are you sealing tiny spice sachets or bulky pet food bags?
Step 2: Determine Your Budget
- Initial Cost vs. Long-Term ROI: Some machines have higher upfront costs but lower maintenance fees.
- Funding Options: Investigate leasing or financing if large-scale automation is crucial for your business growth.
Step 3: Assess Space Constraints
- Floor Plan Considerations: Automated lines often need more room for conveyors, feeders, and quality-control stations.
- Future Scalability: Plan for expansion if you anticipate production growth.
Step 4: Evaluate Machine Features
- Automation Level: How many steps in the packaging process need automation?
- Special Functionality: Do you require date coding, nitrogen flushing, or resealable zippers?
Step 5: Check Service and Support Availability
- After-Sales Service: Machines can break down, so confirm the manufacturer’s or distributor’s service responsiveness.
- Training and Manuals: A well-documented user manual and accessible customer support can prevent prolonged downtime.
Step 6: Run a Test or Pilot
- Sample Runs: Whenever possible, run your actual packaging materials through the machine.
- Performance Metrics: Check seal integrity, speed, and overall reliability.
By carefully evaluating these steps, you’ll minimize guesswork, reduce the risk of buyer’s remorse, and set yourself up for a more efficient, profitable packaging operation.
7. Installation, Operation, and Maintenance
A well-chosen packet seal machine will only deliver optimal performance if it’s installed and maintained correctly. Below are some best practices:
7.1 Proper Installation
- Site Preparation: Ensure you have adequate electrical supply, ventilation, and floor space.
- Leveling and Alignment: Improper leveling can cause inconsistent seals and operational hazards.
- Initial Setup: Collaborate with technicians or follow the detailed manual to calibrate sealing temperatures and pressures.
7.2 Daily Operation Checks
- Pre-Operation Warm-Up: Allow the machine to reach the specified operating temperature.
- Visual Inspection: Look for loose components, wear-and-tear on belts, or residual debris.
- Test Seals: Start each shift with a test batch to confirm seal integrity.
7.3 Routine Maintenance
- Cleaning Schedules: Residue or dust accumulation can hamper machine efficiency and contaminate products.
- Part Replacements: Keep critical spare parts on-hand, such as heating elements, conveyor belts, or sensors.
- Lubrication: Periodically lubricate moving parts as recommended by the manufacturer to minimize friction and wear.
7.4 Troubleshooting Common Issues
- Wrinkled Seals: Could indicate incorrect temperature or pressure settings.
- Incomplete Seals: Often a sign that the heat isn’t reaching the required threshold or you’re moving too fast through the machine.
- Burn Marks on Packaging: Temperature may be too high, or the film is incompatible with that sealing method.
Maintenance Tip:
Document every repair, part replacement, or performance anomaly in a logbook. Over time, patterns in this data can help you preemptively address recurring issues.
8. Industry Applications and Real-World Examples
The versatility of packet seal machines spans multiple industries. Let’s explore some notable applications:
- Food & Beverage:
- Example: Snack manufacturers rely on vertical form fill seal machines to package chips, nuts, and dried fruits. A well-sealed bag ensures freshness and crunch.
- Pharmaceuticals & Medical Supplies:
- Example: Sterile environments often use rotary sealers to package surgical tools or diagnostic kits. Proper seals are crucial to maintain sterility and compliance with health regulations.
- Cosmetics & Personal Care:
- Example: Single-use face masks or sample sachets for creams require precise sealing to avoid leakage and oxidation.
- Pet Food & Animal Feed:
- Example: Large, resealable pouches for pet treats are often sealed with band sealers to manage bulk production efficiently.
- Industrial & Automotive Components:
- Example: Small hardware parts like screws, bolts, and O-rings are typically sealed in robust pouches for easy organization and protection against moisture.
Case Study:
A mid-sized coffee producer upgraded from manual sealing to a band sealer. This change boosted throughput by 40%, minimized worker fatigue, and improved overall product consistency. The ROI was realized within six months through increased productivity and fewer packaging errors.
9. Overcoming Common Challenges
Even the most advanced packet seal machines can encounter hurdles. Here are some common challenges and strategies to address them:
9.1 Choosing the Right Film
- Problem: Incompatible packaging materials leading to weak seals or burn marks.
- Solution: Always consult material compatibility charts and run sample tests. Work closely with film suppliers to ensure you’re using the right thickness and material composition.
9.2 Maintaining Consistent Heat
- Problem: Fluctuating temperatures leading to inconsistent seal quality.
- Solution: Invest in models with advanced temperature-control systems. Regularly calibrate sensors and heating elements to avoid drift.
9.3 Managing Downtime
- Problem: Extended periods of inactivity can cause mechanical and electrical issues.
- Solution: Even if you have seasonal production, run the machine periodically to keep parts lubricated and functional.
9.4 Training Operators
- Problem: High turnover or lack of operator expertise causes operational inefficiencies.
- Solution: Provide comprehensive training and reference materials. Consider “train-the-trainer” programs to ensure knowledge continuity.
9.5 Adapting to New Packaging Trends
- Problem: Growing consumer demand for eco-friendly or specialized packaging puts pressure on existing machines.
- Solution: Look for upgrade paths or modular machines that can adapt to new packaging types.
Industry Resource:
The Flexible Packaging Association offers articles on emerging materials and technologies. Consulting such resources can keep you ahead of the curve and aware of the latest sealing innovations.
10. Latest Innovations in Packet Seal Machines
The packaging industry is far from stagnant. Recent technological advancements continue to push the boundaries of efficiency, sustainability, and automation.
10.1 Ultrasonic Sealing
- Overview: Uses high-frequency vibrations to fuse materials, eliminating the need for direct heat.
- Benefits: Reduced energy consumption, quicker sealing, and less risk of packaging damage.
10.2 Smart Sensors and IoT Integration
- Overview: Modern machines can incorporate sensors connected to the Internet of Things (IoT), enabling real-time monitoring of seal quality, temperature, and machine performance.
- Benefits: Predictive maintenance, reduced downtime, and data analytics for continuous improvement.
10.3 Eco-Friendly Packaging Adaptations
- Overview: Manufacturers are developing machines that can handle compostable films or paper-based materials.
- Benefits: Meeting consumer demand for sustainable products without sacrificing packaging integrity.
10.4 Robotic Pick-and-Place Systems
- Overview: Automated arms that place products into bags or pouches before sealing.
- Benefits: Drastically reduces manual labor and increases production speed, ideal for high-volume factories.
10.5 High-Speed Zipper and Reseal Technology
- Overview: Specialized sealing mechanisms allow for the integration of zippers or spouts in pouches.
- Benefits: Enhances convenience for end-users, creating a competitive advantage in the marketplace.
Innovation Highlight:
Research from the World Packaging Organization suggests that advanced sealing methods like ultrasonic could reduce packaging waste by up to 15% in some sectors. This figure underscores the economic and environmental benefits of staying current with technological innovations.
FAQs about Packet Seal Machine
Q1: How do I know if a packet seal machine is right for my small business?
A1: Evaluate your production volume and future growth potential. For smaller batches, an impulse or band sealer can be a cost-effective solution. If you anticipate scaling up, opt for a more versatile machine that offers higher throughput and better automation.
Q2: Can I use eco-friendly materials with a typical packet seal machine?
A2: Many newer models support biodegradable or compostable films. However, always confirm the material compatibility with the machine’s temperature and pressure requirements before making bulk purchases.
Q3: How often should I calibrate my packet seal machine’s heating elements?
A3: Monthly or quarterly calibration is a good rule of thumb, although high-volume operations may need more frequent checks. Always follow the manufacturer’s guidelines.
Q4: Are packet seal machines difficult to operate?
A4: Most modern machines come with user-friendly interfaces and built-in safety features. A brief training session is usually enough for operators to become proficient.
Q5: What’s the average lifespan of a high-quality packet seal machine?
A5: With proper maintenance and routine part replacements, a well-made machine can last anywhere from 5 to 15 years, depending on usage intensity and build quality.
Conclusion
From ensuring product safety to extending shelf life and boosting brand appeal, a packet seal machine plays a pivotal role in today’s packaging landscape. By taking the time to understand how these machines function, what features to look for, and how to maintain them, you’re better positioned to make an informed decision that will elevate your packaging process.
Remember: The choice of machine directly impacts your production efficiency, packaging quality, and overall profitability. Prioritize features that align with your operational goals and invest in reputable brands or suppliers that offer robust support. Your packaging line is a direct reflection of your brand’s quality—make sure it’s a good one.
Looking to dive deeper or ready to invest in a packet seal machine? Explore our full range of packaging solutions here (internal link). If you have questions or want personalized advice, feel free to contact our experts or leave a comment below. We’d love to help you find the best sealing equipment for your unique needs.
Stay Connected with EngiTech
EngiTech is your trusted source for in-depth knowledge on industrial mechanical engineering machines and technologies. Stay ahead with the latest innovations, expert insights, and practical guides designed to help you make informed decisions for your business and engineering needs. Join our growing community of professionals and industry leaders to stay updated and competitive in the ever-evolving world of industrial technology.