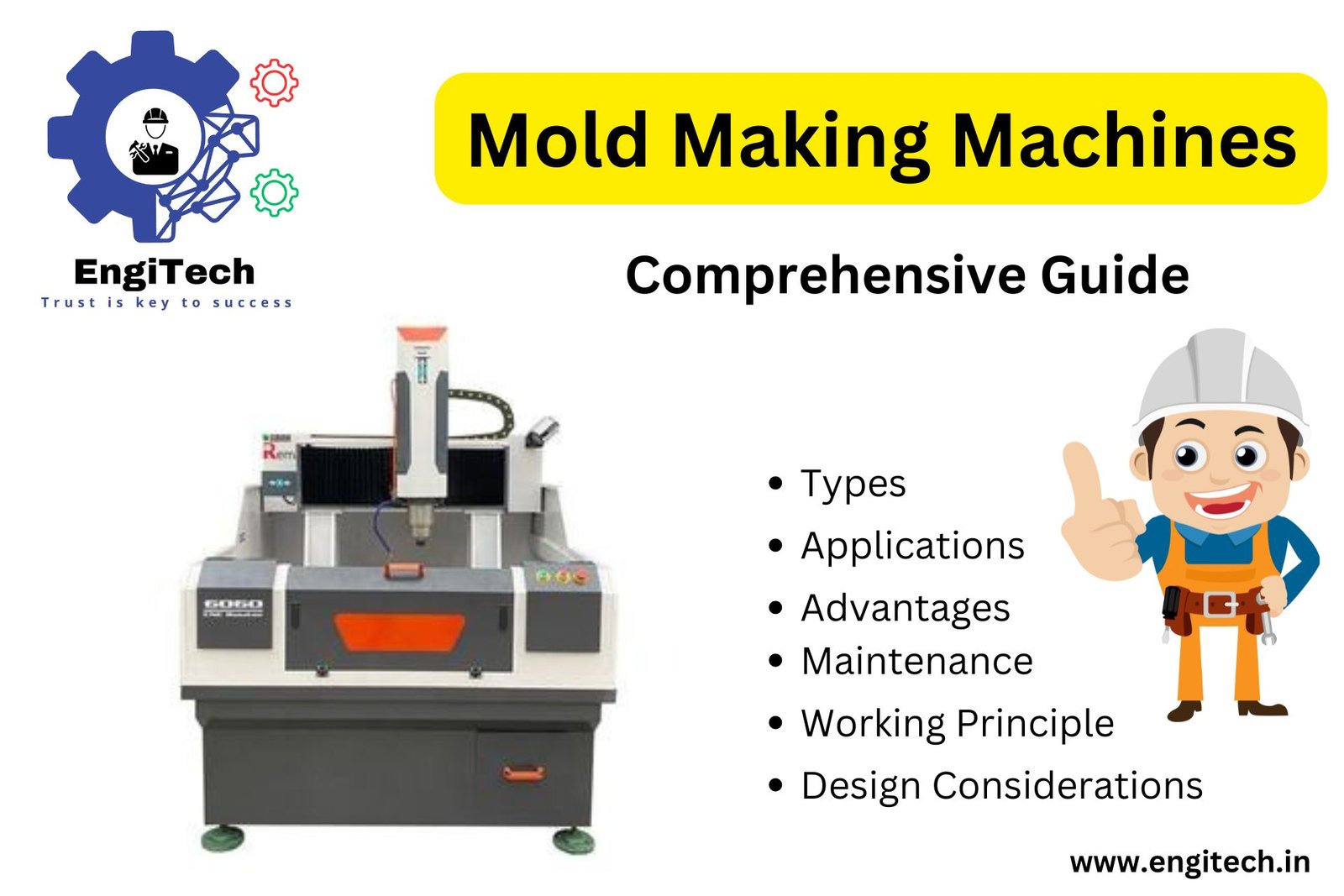
Mold making machines are vital in the manufacturing industry, shaping the components and products we use daily. These machines enable the creation of molds that produce intricate designs, precise parts, and high-quality finishes. Whether you are a knowledge seeker, student, or working professional, understanding mold making machines is essential for mastering manufacturing processes. This comprehensive guide will delve into the different types of mold making machines, their applications, working principles, and insights from industry experts to enhance your understanding.
What Are Mold Making Machines?
Mold making machines are specialized tools used to create molds from materials like metal, plastic, or ceramics. These molds are then used in various manufacturing processes, such as injection molding, casting, and compression molding, to produce parts and components. The precision and efficiency of these machines are crucial for industries like automotive, aerospace, consumer goods, and electronics, where high-quality parts are required.
Types of Mold Making Machines
Understanding the different types of mold making machines is key to selecting the right equipment for your manufacturing needs. Below are the primary types of mold making machines used in the industry:
- Injection Molding Machines
- Overview: Injection molding machines are widely used to produce plastic parts by injecting molten plastic into a mold. The machine consists of two main parts: the injection unit and the clamping unit.
- Applications: These machines are used in industries such as automotive, medical devices, and consumer electronics. Common products include plastic housings, caps, and connectors.
- Working Principle: The injection molding machine melts plastic pellets and injects the molten material into a mold cavity. After cooling, the mold opens, and the part is ejected.
- Compression Molding Machines
- Overview: Compression molding machines are used to shape thermosetting plastics and composite materials. The process involves placing a pre-measured amount of material into an open mold cavity, which is then compressed by the machine to form the desired shape.
- Applications: These machines are commonly used in the production of large and thick-walled components, such as automotive parts, electrical insulators, and aerospace components.
- Working Principle: The material is placed in the mold cavity, which is then heated and compressed. The heat and pressure cause the material to flow and fill the mold, creating the final part.
- Blow Molding Machines
- Overview: Blow molding machines are used to produce hollow plastic parts, such as bottles and containers. The process involves inflating a heated plastic tube inside a mold until it takes the shape of the mold cavity.
- Applications: These machines are primarily used in the packaging industry for producing bottles, containers, and other hollow products.
- Working Principle: A plastic tube (parison) is heated and placed inside a mold. Air is blown into the tube, inflating it to conform to the shape of the mold. Once the part cools, it is ejected from the mold.
- Die Casting Machines
- Overview: Die casting machines are used to produce metal parts by forcing molten metal into a mold cavity under high pressure. The molds, known as dies, are usually made of high-quality steel to withstand the extreme conditions of the process.
- Applications: These machines are commonly used in the automotive and electronics industries to produce components such as engine blocks, transmission cases, and housings.
- Working Principle: Molten metal is injected into the mold cavity under high pressure, ensuring the metal fills all the intricate details of the mold. After cooling, the part is ejected.
- Rotational Molding Machines
- Overview: Rotational molding machines are used to create large, hollow plastic parts. The process involves rotating a mold as it is heated, causing the plastic material inside to coat the interior surface evenly.
- Applications: These machines are used to produce items such as storage tanks, playground equipment, and marine buoys.
- Working Principle: The mold is filled with plastic powder and then rotated in multiple axes while being heated. The rotation ensures even distribution of the material, forming the hollow part.
Key Components of Mold Making Machines
Mold making machines are composed of several critical components that work together to create high-quality molds. Understanding these components is essential for anyone looking to operate or maintain these machines:
- Mold Base
- The mold base is the main structure that holds the mold cavities and inserts. It provides support and stability to the mold during the molding process.
- Cavities and Cores
- Cavities and cores are the parts of the mold that form the shape of the final product. The cavity is the hollow portion, while the core is the solid part that defines the interior features.
- Ejection System
- The ejection system is responsible for removing the finished part from the mold. This system typically includes ejector pins, plates, and rods that push the part out once it has cooled.
- Heating and Cooling Channels
- These channels control the temperature of the mold during the molding process. Proper heating and cooling are crucial for achieving the desired part quality and reducing cycle times.
- Clamping Unit
- The clamping unit holds the mold halves together during the injection process. It applies the necessary force to keep the mold closed while the material is injected.
Materials Used in Mold Making
The choice of material for molds depends on the application, production volume, and required part quality. Common materials used in mold making include:
- Tool Steel
- Tool steel is the most common material for molds due to its durability, strength, and resistance to wear and tear. It is suitable for high-volume production and precision parts.
- Aluminum
- Aluminum molds are lightweight and cost-effective, making them ideal for prototyping and low-volume production. However, they are less durable than steel molds.
- Beryllium Copper
- Beryllium copper is used for molds that require excellent thermal conductivity and wear resistance. It is often used in conjunction with steel molds to improve cooling efficiency.
- Epoxy and Urethane
- These materials are used for creating molds for short-run production or prototyping. They are less expensive than metal molds but are not suitable for high-volume production.
Mold Design Considerations
Designing a mold requires careful consideration of several factors to ensure the production of high-quality parts. Below are some key design considerations:
- Parting Line
- The parting line is the line where the two halves of the mold meet. It is essential to design the parting line to minimize flash and ensure a smooth surface finish.
- Draft Angles
- Draft angles are the slight angles applied to the vertical surfaces of the mold to facilitate easy removal of the part. Proper draft angles prevent damage to the part during ejection.
- Gate Location
- The gate is the point where the molten material enters the mold cavity. The location and size of the gate are critical for ensuring even filling of the mold and minimizing defects.
- Venting
- Venting allows air and gases to escape from the mold during the injection process. Proper venting is essential for preventing air traps and voids in the final part.
- Cooling System
- The cooling system is designed to remove heat from the mold quickly and evenly. Efficient cooling reduces cycle times and improves part quality.
Maintenance and Troubleshooting of Mold Making Machines
Proper maintenance and troubleshooting of mold making machines are crucial for ensuring consistent production quality and prolonging the life of the equipment. Below are some essential maintenance tips and common troubleshooting techniques:
- Regular Inspection
- Conduct regular inspections of the mold making machine to identify any signs of wear, damage, or misalignment. Early detection of issues can prevent costly downtime and repairs.
- Lubrication
- Ensure all moving parts are properly lubricated to reduce friction and wear. Use the recommended lubricants and follow the manufacturer’s guidelines for lubrication intervals.
- Cleaning
- Clean the mold cavities and other components regularly to remove any residue or buildup that could affect the quality of the parts. Use appropriate cleaning agents and tools to avoid damaging the mold.
- Alignment Checks
- Regularly check the alignment of the mold halves and the clamping unit to ensure they are correctly aligned. Misalignment can lead to defects in the final part.
- Troubleshooting Common Issues
- Short Shots: If the mold is not filling completely, check for issues such as insufficient injection pressure, incorrect gate size, or improper material temperature.
- Flash: Flash occurs when excess material escapes from the mold cavity. To address this, check the clamping force, mold alignment, and parting line condition.
- Warping: Warping can occur due to uneven cooling or excessive shrinkage. Adjust the cooling system, material temperature, and cycle time to reduce warping.
Future Trends in Mold Making Machines
As technology advances, mold making machines are evolving to meet the demands of modern manufacturing. Below are some emerging trends in the industry:
- Automation and Industry 4.0
- Automation is becoming increasingly prevalent in mold making, with machines equipped with robotic arms and sensors for precision and efficiency. Industry 4.0 technologies, such as IoT and AI, are being integrated into mold making machines for real-time monitoring and predictive maintenance.
- Additive Manufacturing Integration
- Additive manufacturing, or 3D printing, is being integrated into mold making processes to create complex mold geometries and reduce lead times. Hybrid machines that combine traditional mold making with additive manufacturing are gaining popularity.
- Sustainability
- The industry is moving towards more sustainable practices, with a focus on reducing energy consumption, using eco-friendly materials, and recycling mold materials.
- Advanced Materials
- New materials, such as high-performance alloys and composites, are being developed for mold making to enhance durability and reduce maintenance costs.
Expert Insights on Mold Making Machines
To provide valuable insights, we consulted with experienced engineers who shared their expertise on mold making machines:
- On Material Selection: “Choosing the right material for your mold is critical. While tool steel is a reliable choice for most applications, consider aluminum for prototyping to save costs and reduce lead times. Always balance durability with production volume and part complexity.” – John Doe, Senior Mechanical Engineer.
- On Design Optimization: “Designing the mold with proper draft angles, gate locations, and cooling channels can significantly impact the final part quality. It’s essential to work closely with the design team to ensure the mold is optimized for both manufacturability and performance.” – Jane Smith, Mold Design Specialist.
- On Maintenance: “Regular maintenance of mold making machines cannot be overstated. Small issues can quickly escalate into major problems if not addressed promptly. Implementing a preventive maintenance schedule is key to avoiding unexpected downtime.” – Michael Brown, Maintenance Manager.
Conclusion
Mold making machines are indispensable in the manufacturing industry, providing the tools necessary to create precise, high-quality parts. Whether you are a student, professional, or industry expert, understanding the types, components, and maintenance of these machines is crucial for success in the field. By following best practices in mold design, material selection, and machine maintenance, you can ensure optimal performance and longevity of your mold making equipment.
As technology advances, staying informed about the latest trends and innovations in mold making machines will help you remain competitive and efficient in your manufacturing processes. By incorporating insights from industry experts and embracing new technologies, you can enhance your knowledge and skills, positioning yourself for success in the ever-evolving world of manufacturing.
This comprehensive guide provides valuable information to help you understand and master mold making machines, whether you’re just starting or looking to deepen your expertise. With the right knowledge and tools, you can confidently tackle any mold-making challenge and contribute to the production of high-quality, precision parts that drive the modern world.
Here are the top 7 most asked FAQs related to mold making machines:
- What are the different types of mold making machines, and how do they differ?
- This question is commonly asked by beginners and professionals alike, seeking to understand the specific functions and applications of various mold making machines, such as injection molding, compression molding, and blow molding machines.
- How do I choose the right mold making machine for my manufacturing needs?
- This is a frequent inquiry from professionals who need guidance on selecting the most suitable machine based on factors like production volume, material type, and part complexity.
- What materials are best suited for making molds, and how do they impact the final product?
- Students and professionals often ask this question to understand the benefits and drawbacks of different mold materials like tool steel, aluminum, and beryllium copper, especially in terms of durability, cost, and production efficiency.
- What maintenance practices should be followed to ensure the longevity of mold making machines?
- Ensuring the long-term performance of mold making machines is a common concern. People often seek advice on best practices for routine maintenance, including cleaning, lubrication, and alignment checks.
- How does the mold design affect the quality of the final product?
- This question is crucial for professionals involved in mold design and manufacturing, as it explores the importance of elements like draft angles, gate location, and cooling channels in producing high-quality parts.
- What are the latest trends and innovations in mold making machines?
- Industry professionals and students are keen to stay updated on the newest technologies, such as automation, additive manufacturing, and sustainable practices, that are shaping the future of mold making.
- How do I troubleshoot common issues with mold making machines, such as short shots or warping?
- Troubleshooting is a vital skill for those operating or maintaining mold making machines. This question addresses the common problems encountered during production and offers solutions to minimize defects and downtime.
These FAQs address the most common concerns and questions, providing valuable information to enhance understanding and decision-making for those involved in mold making.
Engineering Expertise with EngiTech – Our Team
Unlock the full potential of your manufacturing processes with EngiTech, your ultimate resource for expert insights and cutting-edge knowledge on industrial machinery. Whether you’re a seasoned professional or just starting out, our in-depth guides, industry news, and innovative solutions are designed to elevate your understanding and efficiency. Dive into a wealth of information on mold making machines, CNC lathes, lubrication systems, and more, all curated to help you stay ahead of the curve in the rapidly evolving world of engineering. Join our community of forward-thinking engineers and industry leaders, and transform your expertise into success with EngiTech.in.